摘要:在當下的實際應用中,特別是電動汽車領域,由于該領域的快速發展導致功率半導體器件需要更高的性能要求。自功率半導體誕生以來,技術人員主要致力于提高元件的耐壓耐溫、開關頻率、通流能力等性能,然而硅元件性能受限于基地材質,該材質存在明顯的上限,目前的硅功率半導體的性能基本接近上限,難以滿足當前及未來電動汽車電機控制器對效率,功率密度,體積,可靠性等方面的需求。這些問題的存在使得行業積極轉向采用前沿技術:采用性能更加優異的碳化硅(SiC)功率半導體器件代替傳統的硅(Si)功率半導體器件進行電機控制器設計。關鍵詞:SiC電動汽車電機控制器結構優化
1行業發展現狀
國內電動汽車產業始于 21 世紀初期,在2006 年開始嘗試實現混合動力汽車產業規模化,并開始逐步拓展至純電動汽車的生產范圍 [1]。當時的專家團隊就電動汽車的車用動力蓄電池、驅動電機、燃料電池、電力電子設備等關鍵零部件的總體集成和技術研發進行了大規模的攻關,促進產學研結合,從而奠定了現今中國在電動汽車領域發展的基礎。隨著產業不斷競爭和整合,電動汽車因其發展迅猛,效果顯著,性能優異,技術可靠等優點,迅速成為了國內最主流的一種電動汽車產品。電動汽車顧名思義—指利用電能驅動車輛運行,首先通過高性能電池儲存并輸出電能,然后由電機驅動裝置將能量精確控制并分配至驅動電機 - 輪轂系統從而實現車輛運行的方式。由于這個方向與傳統汽車行業相比差別較大,國外的領先程度也不高,同時由于行業藍海阻力小,沒有存在明顯的行業專利壁壘和壟斷,國內技術創新發展迅速,使得我國后發優勢得到了充分的體現。2013 年實現了高功率硅 IGBT 器件國產化,2016 年達到世界先進水平,我國電動汽車得以能夠同歐美企業同臺競技。
2電動汽車電機驅動系統的研究
2.1電力驅動裝置應用需求
隨著技術的不斷發展在電力驅動系統中的電動機已經從傳統的直流電機、交流異步電機發展到了同步磁阻電機、永磁電機等效率高、體積小、功率密度大的新型電機產品。相比于傳統驅動電機,新型電機具備體積小,功率大,成本低,控制精度高的優勢。傳統電機控制系統簡單響應性能雖然不錯,但由于體積、成本、效率等因素導致了其無法同新型電動機在電動汽車這個行業上競爭,而新型電機是因為采用了先進的電機驅動裝置才能發揮出新型電機的性能。
電動汽車要走進千家萬戶,首先得能夠保證行業能自行發展,穩定盈利,那么必然會面臨著一個國家政策補貼減少和完全取消這樣一個嚴峻的考驗。當國家的政策扶持逐步取消以后,什么樣的產品才能賣出合適的價格?才能讓市場接受?才能走進千家萬戶?首先是價格,要能夠讓普通消費者買得起,然后是與同競爭對手燃油汽車相比要跑得里程要長續航能力強,再者安全系數一定要高,最后是智能化水平要領先。而電機驅動裝置,作為電動汽車三大核心技術之一,其性能的好壞直接決定了車輛的總體指標。因此對電機驅動裝置的要求就是成本低,效率高,體積要小,環境適應性強,容忍性強。那么就需要具備高功率密度、能耐受高溫、不懼低溫、電氣控制性能好、抗電磁干擾能力強或者容易控制、過載運行能力強、過負荷倍數要突出、控制容易且精確穩定和綜合系統性能強等特點。只有這樣才能在產品端表現出優勢,才能具有較強的行業競爭力。
2.2傳統電機驅動控制器研究
隨著電力電子技術水平迅速發展得到進一步的提升以及各種先進高性能微處理器,其控制和功能日趨豐富而強大,電機驅動的自動控制系統設備已實現完全數字化控制,產業也迅速朝著集成化、模塊化的方向發展。
電力驅動裝置這種集成系統由多個模塊組合而成,傳統的電力驅動裝置采用硅 IGBT作為電流的控制元件,普通硅器件結溫目前已達到 150℃,接近硅材質的上限,并且元件在工作溫度大于 80℃后就會出現顯著的性能降低、芯片載流能力下降、開關波形不穩定、毛刺增加等問題,這要求提供更大的驅動電流,同時增加了對控制電路的壓力。為滿足車輛控制的可靠性要求,往往需要散熱系統和驅動控制系統,形成較大的系統冗余,且硅 IGBT 本身也存在一定程度的模塊冗余。這導致集成系統體積碩大、成本高昂且性能一般,主要用于對設備體積不敏感的場所例如高鐵、電動公交等。
從占用體積角度分析,為保證散熱,集成系統采用循環水冷系統直接接觸芯片的方式帶走熱量,但因為水冷液正常工作溫度在50-90 攝氏度范圍,硅 IGBT 元件的可靠工作溫度與冷卻介質溫差較小,需要極高的傳
熱能力才能保證熱量的快速轉移。但為了保證系統安全可靠,在高頻振動下穩定、不老化,電子元器件必須與冷卻介質完全隔離,不能采用常規民用產品,直接接觸冷卻和液體表面沖擊冷卻。因此,中間層的傳熱介質只能是銅制熱管或純銅均熱板,其成本相對高昂而且需要較大的接觸表面積來保證熱量的快速轉移,這導致水冷系統水道復雜、成本高、體積大近乎占據整個模塊約 40%。為保證開關波形的穩定,必須保證在最惡劣工況下 IGBT 驅動元件電磁干擾要盡量小,不會因為大電流導致紋波異常,引起錯誤的開關動作。通常采用三相橋式逆變電路的 IGBT系統,為保證最終輸出波形能接近正弦波需要采用 PWM 高頻開關,配合續流元件和平波電容從而實現波形整理。而傳統硅 IGBT模塊因工作溫度導致的性能劣化且由雜波引起的穩定時間延遲導致系統開關頻率較低,僅有 30kHz 左右,這導致在輸出正弦波驅動電流時 PWM 波形頻率太低需要很大的平波電容才能實現設計目標。這些電容組統稱為母排電容,集成后也占用了較大體積,且因為電容數量眾多,導致工作電壓也較高而能采用的 PP 膜電容僅具有較好的低頻性能。雜波的尖銳波形形成的高次諧波會導致母排電容組的損耗增加,發熱量很大。傳統的集成系統工程設計是采用定制電容器,封裝外殼直接與散熱模組連接,通過循環水冷系統帶走熱量。因此母排電容及其附屬配件占用了整個模塊約 45%,成本是難以降低。
去除以上兩部分組件,真正用于電機驅動的核心部件 IGBT 模組和控制電路的體積只占整個模塊的 15%,雖然這部分占成本比例高,但由于國產化元器件進度很大,更新換代速度較快。因此成本下降速度很快,屬于創新競爭的關鍵環節。可以根據市場定位選擇合適價格的元器件。而其余的散熱系統和母排電容系統的成本和占用體積幾乎無法減少。這嚴重影響產品的競爭力。
2.3SiCMOSFET 驅動元件替代硅 IGBT元件設計
硅 IGBT 與 SiCMOSFET 驅動芯片兩者電氣參數特性差別較大,對驅動的要求也不同,主要體現在以下幾個方面,見表 1。
表1
從開通、關斷控制電壓來看,相比于傳統硅 IGBT,采用 SiC 器件需要更高的開通電壓,但關斷電壓可采用 0V,這極大簡化了控制電路的設計,不需要額外的負壓電路。對比電磁干擾的耐受性能 CMTI,碳化硅MOSRET 也顯著強于傳統硅 IGBT,能實現更高的可靠性同時簡化驅動電路設計。
從開關時間來看,開關時間的成倍縮短能大大減少系統在導通與關斷之間切換過程的時間,過程時間越短,則過程狀態下的開關損耗就越小,顯著降低的開關損耗極大降低高頻運行下的發熱。同時導通電阻的降低也能減少通流損耗,低頻、大電流下的發熱也能顯著減少。綜合各種運行工況來看,作為電流控制的關鍵環節,任意一種損耗的減小均能大幅提高系統運行效率。
從開關頻率方面來看,通常硅 IGBT 的應用開關頻率不大于 40kHz,而 SiC 而開關頻率通常在 100-200kHz,相對來說得到大幅提升,在用于 PWM 驅動產生正弦波輸出的過程中能夠有效優化波形,能降低對母排電容的容量要求,大幅降低輸出毛刺和抖動,可以減少母排電容的發熱損耗。
從 SiC 材料本身的材料性能方面來看,其器件結構具有天生的耐高溫能力,本身熱導率性能優越,是硅材料的三倍,在真空條件下甚至可耐受高達 400-600℃的高溫,在實際工業應用中,為了防止接觸空氣氧化、保證系統可靠性穩定性,SiC 器件必須有車規級封裝,當前耐高溫封裝中,150℃結溫是業界目前的最高執行標準,而 200℃乃至更高耐溫的封裝還在定制化設計之中,潛力深厚具有非常廣闊的發展前景。
從 SiC 材料本身的物理性能方面來看,SiC 半導體器件具有很寬的禁帶寬度,屬于第三代半導體材料,臨界擊穿電場強度是硅材料的近十倍,這使得更高元器件工作電壓成為了可能。目前的產品中傳統硅 IGBT 產
品工作電壓約 450V-800V,而已投產的車用SiC 器件工作電壓可達 1200V-3300V 且仍具備較大提高的空間。這樣可使得同等功率下高電壓小電流驅動成為了可能,電流的減小能顯著降低雜散電感和電磁干擾的影響,且能大幅降低線路損耗與發熱。
為更好的發揮 SiC 器件的特點和優勢,
需要對現有電機控制器進行大量優化和改進。首先控制主系統必須具備更小的延遲、更高的開關頻率和更短的保護動作時間。這需要采用更先進更高頻率的 SOC 片上系統,才能發揮 SiC 器件高開關頻率、低損耗的優勢。其次 SiC 器件損耗低、發熱量小且耐溫高,這些優越的性能組合起來使得 SiC 熱傳導速度極大提高、熱密度提高、冷卻系統大幅減小。采用單獨的耐高溫開關板設計,將所有 SiC器件集成到一起,采用光觸發技術同控制板完全隔離,工作溫度為 150-200℃。這既保證常規控制板工作溫度穩定,又能發揮出 SiC器件板耐高溫的優勢,同時有效降低電磁干擾水平,提高系統可靠性。最后應當采用新型主控算法充分發揮在控制器中移相,適當抵消電機載波的紋波,同時將工作電壓提高一到兩倍,更好的發揮 SiC 器件高電壓的優勢,在維持原波形雜波和諧波占比的條件下,極大地減少平波母排電容的大小和損耗甚至可以在優化控制器的情況下完全消除。通過以上幾種方式可使得電機驅動裝置的功率密度從 8kW/L 提高至 30kW/L 且仍具備很大的發展潛力。
3結語
綜上所述,當前新型車用 SiC 材料控制器在極端環境下的可靠性還在進一步的驗證。SiCMOSFET 與硅 IGBT 材料相比,具有更寬的禁帶寬度、數倍的臨界擊穿場強、兩倍的電子飽和漂移速率和三倍的熱導率這樣的性能優勢,在電氣上具有更高頻、高效、耐高壓、耐高溫等特點取代傳統器件勢不可擋。以當前已經投入使用的 SiC 電機控制模塊同傳統硅 IGBT 模塊系統相比,電機驅動裝置整體系統的體積可減少至 25%,系統重量減少至 30%,電能損耗從 20% 降低至 5%,效率達到 99% 以上,盡管電力元件價格更昂貴,但電機驅動裝置系統的成本還是顯著降低至 65%。從市場上看,SiC 電機控制模塊的使用使得整車續航里程提升 5% 以上,配合更好的能量回收制動,數字控制技術極大提高車輛綜合續航水平且遠未達到理論性能極限,具有很大的發展前景
來源:新能源汽車
作者:陳志飛
廈門市福工動力技術有限公司
~~~~~~~~~~~~~~~~~~~~~~~~~~~~~~~~~~~~~~~~~~
-
控制器
+關注
關注
112文章
16376瀏覽量
178200 -
電機
+關注
關注
142文章
9023瀏覽量
145556
發布評論請先 登錄
相關推薦
Tips:大功率電源PCB繪制注意事項
浮思特|如何通過設計SiC功率模塊優化電動汽車電機驅動熱管理效率?
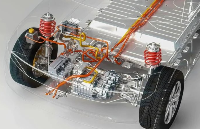
評論