電動汽車的勃興孕育了一批批選手投身汽車電子賽道,同時還有許多本來屬于汽車領域之外的零部件廠商參與其中。一時間對于汽車零部件認證標準的說法引起廣泛討論,諸如ISO、IATF、AEC-Q100等詞匯充斥著人們的視野。
其中AEC-Q100被廣泛認為是所謂的車規認證,很多廠商認為只要通過AEC-Q100認證就是達到了所謂的“車規級”,但也有些廠商認為僅通過AEC-Q100并不足夠,還需要通過ISO 26262認證,還有部分廠商宣稱通過了相關的認證但遲遲未打入車企的供應鏈之中,甚至在實際測試過程中不達標。
對于“車規級認證”,人們有不同的看法,看似只需經過有關認證便可直接向外界宣布,然而事實果真如此么?
在9月27日第20期的“新能源汽車半導體在線研討會”上,總經理王楊對汽車零部件認證標準和體系進行了詳細的解讀,并對車規認證的真正定義作出了解釋。
以下是王楊的分享內容:
今天,我就汽車電子量產測試與認證體系這一主題與各位同仁進行交流。我們在下面就電子產品可靠性測試涵蓋哪些內容進行探討。縱觀不同電子產品的制造工藝,大體為:晶圓級--裝置--板上裝置封裝--PCBA--系統/模塊--產品。由此可見,可靠性測試貫穿于半導體及電子產品生產的全生命周期流程。
對于可靠性標準來說的話,大家比較熟悉的如JESD47,主要是面向消費、商業和工業類產品。對于汽車類產品來說,主要是AEC-Q100系列,其中101、102是不同細分領域的再劃分。對于軍標來說,主要遵循MIL-STD-883、202、750標準。所以,針對不同等級的電子產品,都有相關的標準來評定整個質量。
在體系認證方面,生產廠商分為ISO9001認證體系和兩大認證體系,它是所有生產廠商或質量管理體系廠商認證體系的核心準則。二是以汽車零部件制造管控體系標準為重點的IATF16949。
AEC-Q100和IATF16949有什么區別?
大家有時候可能會疑惑,AEC-Q100和IATF16949到底有什么區別?這兩個標準所約束的方向是不一樣的。
我們來做個橫向對比,首先AEC-Q100和JEDEC是屬于技術標準,它有嚴格的、具體的、標準化的工作程序。而ISO和IATF只是提出一個要求,實際上并沒有嚴格和具體化的數據性表征。
其次,所有的技術標準都有統一和絕對的判決標準,比如AEC-Q100對汽車電子的溫度要求是有絕對值的。但是,IATF16949沒有統一的判定標準,而是依照各企業自身情況而定,所以它是個體系標準。
第三點,技術標準一般而言以應用為主,而體系標準只是闡述管理思路、邏輯和方法。
最后,一切技術標準均以達到特定目標為目的,體系標準則是規定達到這些目標的具體方法。因此從核心目標上看,技術標準更加注重產品自身,而體系標準則更加注重日常運營和生產活動這一流程。
每個人都應該先清楚自己有什么目標,然后再去思考遵守哪一個標準。若為進行發展、特定數據收集、明確目標等,則應遵循AEC-Q100的準則。若要升級企業的管理,制造手段以保證日常生產經營活動符合標準,那么就必須借助IATF16949。
IATF16949的歷史
為協調國際汽車質量系統規范,世界主要汽車制造商及協會于1996年成立了一個專門機構,稱為國際汽車推動小組,簡稱為IATF。IATF的成員包括5個國家的協會:美國汽車工業行動集團(AIAG);意大利汽車工業協會(ANFIA);德國汽車工業協會(VDA);法國汽車制商委員會(CCFV)和汽車裝備工業聯盟(FIEV);和9大OEM汽車制造商:寶馬、戴姆勒、克萊斯勒、標致-雪鐵龍、菲亞特、福特、通用、雷諾和大眾等。
針對IATF16949標準,有5大工具:產品質量先期策劃和控制計劃、潛在失效模式和后果分析參考手冊、測量系統分析參考手冊、統計過程控制參考手冊、生產件批準程序。
產品質量先期策劃與控制計劃就是每一個企業尤其是生產制造企業對其整體的生產制造進行計劃與規劃安排。潛在失效模式及后果分析參考手冊所謂FMEA,主要是針對拿到失效結果后,如何去分析的參考。測量系統分析參考手冊叫做MSA,這主要是對于產品生產完成之后,我們應該如何對其進行測試,測試的設備是否齊全,能否讓之后的整個產品的質量符合標準呢?統計過程控制保證了制造過程中沒有錯誤。生產件批準程序對全部生產流程進行控制,從開發到小批量出貨,再到批量生產,批準流程均有相應的規定。
所以16949是一個定制得非常仔細的方法論,所有汽車或汽車零部件相關企業都會遵從16949的質量體系過程。
AEC-Q100怎么來的?
AEC是由Chrysler-Ford-GM于1994年聯合發起組成,目前會員已遍及全球各大車廠、Tier 1和集成電路廠家。AEC技術委員會負責制定車規級器件可靠度標準AEC-Q系。汽車電子的Fab./OSAT都要遵從車用器件供貨商質量系統(IATF16949),但Design House只需要遵從ISO9001。
AEC-Q系列根據產品分類不同,認證標準也不同。其中AEC-Q100主要針對IC產品,Q101主要針對分立器件,Q102主要針對光電器件,Q103主要針對MEMS,Q104主要針對MCM,Q105主要針對觸摸屏系統,Q200主要針對被動型器件。所以大多數IC設計公司,大家都非常關注AEC-Q100。
那么AEC-Q100的認證技術來源是哪里?有10%-20%來自各大車廠自己的規范,80%是來自國際規范,比如ISO 16750、SAE (美國自動車工程師協會)等。
1.5%的失效率在汽車上后果不堪設想
接下來講一下為什么要做零缺陷,特別是在芯片級。對于汽車而言,使用的電子零部件數量相當大。以傳統車為例,基本以300個IC組成一個ECU單元,50個ECU組成一輛車。假設300個IC有1 PPM(每百萬個零件中的失效個數),那么一整臺車就有15000 PPM,即100臺車中就有1.5臺失效。
即使供應鏈上下游制造商合作,1.5%失效率都將給安全性要求很高的車輛帶來非常恐怖的后果。因此對汽車制造行業而言,僅有一項指標即零缺陷。如今各零部件廠商或終端廠商均付之以巨大的努力與勞動,設計端與制造端均做著各種改良,以保證零缺陷為終極。正因為如此,如今汽車電子的門檻如此之高,常常因一次錯誤,而導致人員傷亡。
還有一點,為什么說汽車電子的測試環境或質量要求那么高?由于汽車整體應用環境較為嚴酷,如溫度、車外環境溫度都將面臨著急冷急熱等問題,車內溫度將表現出不同分布規律,離引擎較近的地方溫度會比較高,剎車片部位可能瞬間上百度溫度。也有震動,碰撞和濕度等因素,要求產品能夠經受住惡劣環境拷打。盡管在設計階段對上述條件作了布置與排列,但是在最后的測試階段上述指標仍是適用的。只有實操之下對有問題的器件進行測試,才能不把問題留在下一關。
AEC-Q100就是車規認證嗎?
大家一直認為AEC-Q是不是有所謂的車規認證環節,這里要打消一個誤解。
首先,實際上AEC是一個聯盟組織,并不是委員會。AEC未設立認證委員會, 因此沒有“AEC Certification”。它不像ISO或者IATF在全球有標準化委員會。
其次,產品公司只要根據AEC標準,通過完整AEC驗證后,就可自行對外宣告獲得AEC Qualified(資格驗證)或經由中立第三方實驗室出具AEC Qualified報告,但是通過ISO或IATF不能自行對外宣告。
所以獲得資格驗證并沒有那么難,那么如何獲得呢?有以下幾個標準:
產品根據AEC標準要求,完整并成功地通過每項試驗
樣品必須由3個不連續生產的晶圓批次和封裝批次組成
樣品必須將每一根PIN腳通過的ESD電壓紀錄于產品數據表內
在核查期間發生的任何故障都必須完整地記錄在案—分析真因和執行糾正措施以及證實能有效地防止在發
第三方閉環實驗室也要符合以下要求:
須符合ISO/IECQ 17025認證
須具備完整AEC可靠性、電性與物性故障分析和性能讀點能力
1.所有數據可追溯性
2.避免錫須斷裂
3.預防樣品于運送途中損壞
4.確保數據讀點于要求時間內完成
車企可依需要進行實驗室和生產制造供應鏈現場稽核或進行抽驗。因此,拿到AEC-Q100認證只是剛入門,并不能稱為真正的汽車電子,必須充分滿足IATF16949體系,才能真正獲得汽車電子供應準入證。這我們需要弄清楚的是,曾經有一個人說過他的產品為什么AEC-Q100都沒有辦法進車廠而無法前裝的原因。
如何啟動AEC-Q100認證?
第一步,確定溫度等級。AEC-Q100有四個溫度等級:0,1,2,3。其中0為最高級別,相應的溫度區間為-40°C-150°C。若能達到0級要求則代表您的產品可以用于汽車的各個部件。
第二步,跑Test Flow。不同制造環節將進行不同試驗,產品在送樣過程中需要對這些過程進行完整體驗,目前第三方實驗室條件齊全,在全部試驗合格之后即可通過驗證。
我們來對比下面向汽車電子的AEC-Q100與面向消費電子的JEDEC 47有哪些不同。首先,樣品數量上,汽車電子是消費類的三倍,比如JEDEC對消費類樣品數量規定在225顆以上,但AEC-Q100就需要715顆以上。其次,AEC-Q100要求對所有產品進行可靠性測試,以保證在批量生產中實現零缺陷而消費類則無此條款,可進行抽檢。對功能性測試而言,各汽車零部件廠商監測數據均需要給出,即使是準確到個別零件。所以大家想做汽車類產品,一定要重視質量測試。
最后和大家分享下,從AEC-Q100到IATF16949整個流程。
第一步,或者決定產品用于汽車的哪一部分并決定溫度等級,這都是各廠家所規定的。
第二步,提供 IC POD.(Package Outline Drawing,封裝規范標準),POD確定了整個產品的外觀尺寸,以及引腳的數量和間距。
第三部分它是為產品設計自身提供數據,如特定參數,功能和測試電路。
上述三步可以交給專業的測試機構來完成測試。
最后一步是面向最終大規模量產的一套測試流程,有以下幾個測試:
Input QC
Tri-temperature ATE testing
Outlier screening
Production Burn-In
Sensor Preaging Calibration
Package
Output QC
-
電動汽車
+關注
關注
156文章
12069瀏覽量
231123 -
芯片
+關注
關注
455文章
50730瀏覽量
423192 -
車規級芯片
+關注
關注
2文章
241瀏覽量
12168
發布評論請先 登錄
相關推薦
基本半導體碳化硅MOSFET通過AEC-Q101車規級認證
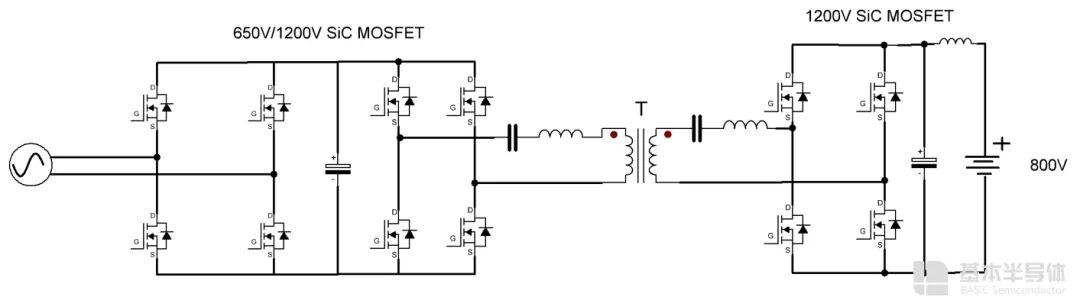
如何辨別符合車規級標準的電子元器件?
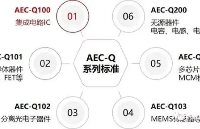
江蘇潤石最新發布12顆車規級模擬芯片
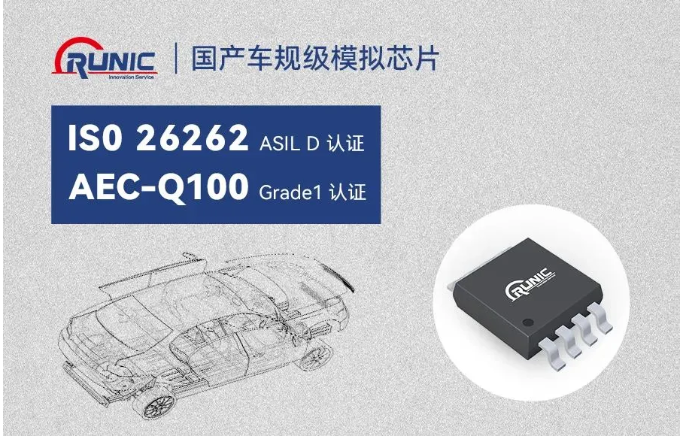
艾為電子獲證車規級芯片,助車企提升智能駕乘體驗
芯弦半導體高性能車規MCU系列獲AEC-Q100車規級認證證書
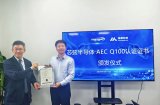
江蘇潤石新增16顆車規級芯片
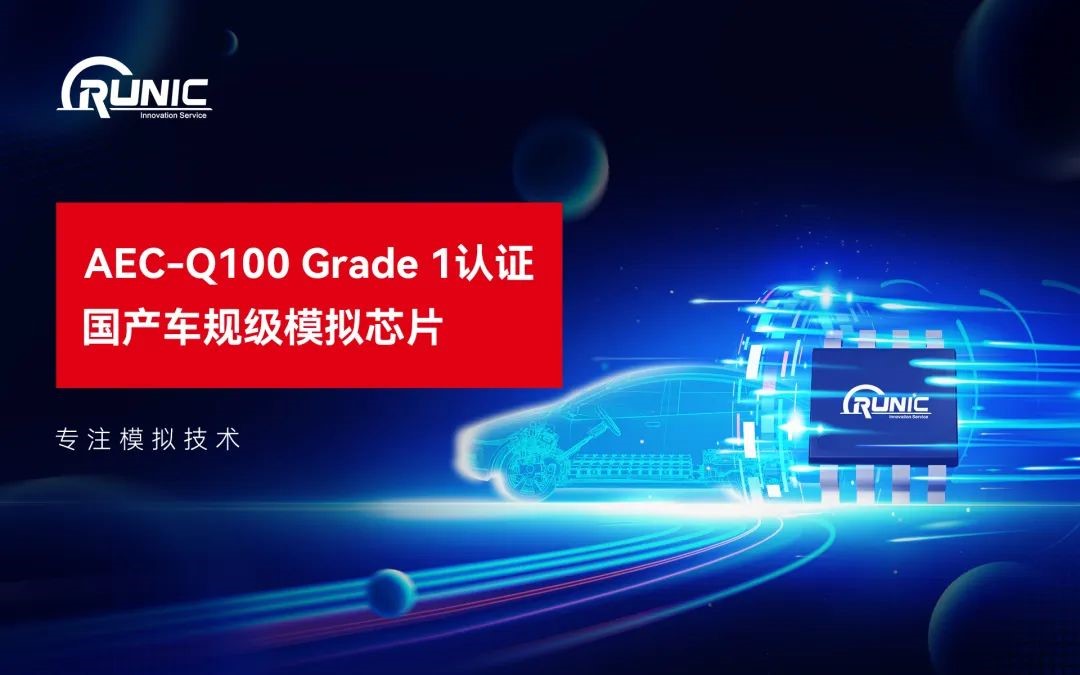
評論