隨著汽車電動化及智能化的發展,以及這幾年特斯拉、比亞迪及國內造車新勢力的強勢崛起,自動駕駛技術的發展,同時隨著國產化替代的推進,“車規級”這個詞也越來越多的出現在了大家的視野中。
但是 “車規級”到底意味著什么?為什么需要 “車規級”?相關的很多問題想必大家都比較懵懂,筆者就根據個人對AEC標準的理解,結合最近查閱的大量相關資料,給出了一些分析,算是拋磚引玉。
本文將以“車規級”激光雷達為切入點,從針對激光器件的AEC-Q102標準開始解讀,逐步回答“什么是車規級?”這個問題。然后從自動駕駛技術對車規級標準的推動開始,看車規級標準為適應新技術和應用的需求是如何一步步發展的。
因AEC標準文檔數量很多,信息量極大,筆者的解讀難免有所偏頗及遺漏,所以歡迎業內專家一起交流討論,共同推進國產汽車電子元器件及零部件的發展。
什么是“車規級”?
但凡是汽車行業的,大都聽說過一個詞,叫“車規級”或“汽車級”。就像蘋果推出“視網膜屏”后,大家都說自己是“視網膜屏”,否則都不好意思和別人打招呼。車企喜歡說自己車上用的是 “車規級”零部件,Tier 1喜歡說自己用的是“車規級”芯片,仿佛誰用了非“車規級”的就落了下乘。
已經有越來越多的國產器件供應商真正開始著手對器件進行AEC-Q認證,并自建試驗室了。然而,目前國產“車規級”元器件種類及數量都還比較少,某些聲稱的所謂“車規級”器件,實際上根本沒有通過AEC-Q認證。此外,雖然通過了就是“車規級”,但“車規級”確遠遠不止于AEC-Q。
以激光雷達為例,車企宣稱某款車是全球首款搭載“車規級”激光雷達的車,激光雷達供應商也在宣傳自家的產品是率先實現量產的 “車規級”產品。外行看個熱鬧,內行卻會覺得“車規級”這個詞被“濫用”了。下面,我們結合激光雷達的例子來看看“車規級”這個概念是如何被“濫用”的。
第一項關于激光雷達器件的車規標準
我們先不談什么是“車規級”,先普及一個常識:行業標準通常是落后于行業技術發展的。就像法律的制定,也一定是滯后于社會發展的。那么我問你,激光雷達作為新生事物,其使用的激光器件現在有行業標準了嗎?
答案是:已經有了。
AEC-Q102 REV A中加入了激光器件(來源:aecouncil.com)
AEC-Q102“Optoelectronic
Semiconductors 光電子半導體”在2020年4月份發布的A版本中加入了Laser激光器件,并在4.5章節中專門規定了針對Laser的測試注意事項和要求。
AEC-Q102 REV A中對激光器件的規定(來源:aecouncil.com)
并且,AEC-Q102還專門規定了針對激光器件的以下部分:
4.5章測試注意事項(Notes for Testing Laser Components);
流程變更指南(Process Change Guideline for Laser Components);
最小參數測試要求和失效標準(Minimum Parametric Test Requirements and Failure Criteria);
Table 3認證測試方法(Qualification Test Methods);
Table3某些專門針對Laser的測試要求(Required only for laser components.)
通過以上信息可以得到哪些結論呢?
(1) AEC-Q102正式發布時間是2020年4月6日;
(2)在此之前沒有針對Laser器件的AEC標準。
那么問題來了,在此之前發布的宣稱達到了“車規級”的激光器件還是“車規級”嗎?
雖然AEC-Q102草案早就出來了(2017年已經是ready to be published狀態了),在最理想的情況下,假如標準從草案到正式發布期間并無任何更新,而某款立項于2018年的激光雷達是參照草案的標準找的零部件,那么,這款激光雷達就算是達到了車規標準。
然而,在通常情況下,上述假設并不成立。如果你聲稱通過了AEC—Q認證,客戶問你要AEC—Q報告,你總不能說是依據草稿出的報告吧?此外,AEC-Q測試周期很長,成本也很高,一般也不會用草稿去作測試,因為標準正式實施后,如果有更新,有些測試項目你還得再做一遍。
全球首款“車規級”
激光器件的發布及量產“上車”
我們再換個角度看一下。熟悉AEC—Q標準的小伙伴們應該了解,耐久類測試要求起步通常是1000小時,但在AEC-Q102中,除常規測試項目外還專門規定了一個可靠性驗證Reliability Validation,時間從最低1000小時到最高10000小時。
大家估計對10000小時沒有直觀概念,這么說吧,一年只有8760小時,而AEC-Q102要求超長壽命的Laser器件HTOL(High Temperature Operating Life高溫使用壽命)測試時間要達到10000小時。
AEC-Q102 REV A中對可靠性驗證的規定(來源:aecouncil.com)
好,現在結論來了:AEC-Q102正式發布時間是2020年4月,可靠性測試起步1000小時,一般不會做這么短,長壽命至少4000小時,就是5.5個月,那么符合標準的激光器件量產你猜會在什么時間?
歐司朗宣布世界上首款符合AEC-Q102的四通道激光器(來源:osram.com)
歐司朗作為全球光電器件的巨頭,在2019年9月宣布了其符合AEC-Q102的四通道激光器。注意,這只是宣布,離實際量產能用,還有很長的時間。
這一點沒做過工程設計的小伙伴們可能不太有感覺,就比如新聞上發布了某項新技術,大家可能就認為馬上就能用上了,其實上還差得遠呢。這中間大概的關系是這樣的:實驗室àTier 2企業à Tier 1企業àOEMà用戶,大家可以看到,從實驗室到用戶,中間還隔著很多道,其中還有Tier n企業,產業鏈很長且很復雜。
回到歐司朗這顆激光器件SPL S1L90A_3,我們看下它的datasheet信息。
歐司朗SPL S1L90A_3激光器手冊(來源:osram.com)
其中有幾個關鍵信息:
(1)此激光器可以用于激光雷達;
(2)通過了AEC-Q102認證;
(3) SPL S1L90A_3器件手冊初版發布時間是2022年2月。
做過汽車電子產品設計的小伙伴們應該都了解上面的信息意味著什么,但我在這里還是科普一下:汽車電子產品的設計,是極少在量產項目中直接采用全新器件的。
一是為了保證產品的可靠性,畢竟從來沒用過,技術實力不夠;二是為了降低BOM成本,畢竟新東西剛量產都貴,因為還沒上量呢;三是降低技術風險,新技術誰家都沒摸索過,出點問題項目可能就得延期,用之前大家都得“掂量掂量”。
接下來我就從一顆芯片開始,講一下一個新技術從發布到量產的流程:
芯片供應商Tier 2制定芯片規劃(Roadmap),各Tier 1及OEM調研;
芯片供應商確定芯片開發時間;
Tier 2提供免費工程樣片,Tier 1預研(advance)項目設計導入;
Tier 2提供量產芯片,Tier 1采用量產芯片進行DV(Design validation設計驗證);
采用新器件的Tier 1的項目SOP,產品量產;
OEM采用此Tier 1產品的車型量產。
新器件導入項目流程(來源:左成鋼)
從上面的新器件導入流程我們可以看到,一款新器件從設計到量產需要1年以上時間,Tier 1設計好還需要1年時間,這差不多就需要2年或3年時間。這已經算是比較快的了,要知道一般的汽車電子零部件,一個項目從立項到SOP就是3年左右。如果從芯片供應商做推廣開始算,期間少說也得3年時間了。
從歐司朗的那顆激光器的量產時間我們也能看出來,器件從發布到量產,期間經過了2年零5個月的時間,并且器件發布時間還稍早于AEC-Q102標準發布時間。
那么能不能再快一點呢?可以!
芯片在工程樣片階段就導入量產項目,如圖中紅色虛線箭頭所示,跳過驗證階段。待芯片一量產,馬上進入DV,少則三個月,多則半年就可以達到臨近SOP狀態(指產品硬件凍結,軟件大概率還在更新)。
那么這樣能有多快呢?這就取決于芯片供應商和項目本身了,順利的話,說不定1年就SOP了,但還真沒怎么見過這么玩的,尤其是涉及到安全功能的零部件,OEM敢,Tier 1估計也不敢,因為出問題是要負責的。
AEC-Q強制性標準碼?
理論上,AEC-Q只是一個汽車行業標準,并不是法律,也沒有強制性的認證制度,做與不做,“各憑心意”。但實踐中,汽車行業對電子零部件中采用的元器件的基本要求就是“車規級”,而AEC-Q已成為汽車行業事實上的電子零部件通用測試標準,只有通過了AEC-Q認證,大家才認為是車規級元器件。
即使OEM不去審核,Tier 1也不會偷偷地用“非車規”的器件,原因大概有以下幾點:
(1)無“非車規”器件可用。一般大的Tier 1都很規范,物料庫是全球共用的,有專門的團隊維護,物料庫中基本不會存在“非車規”物料;
(2)新器件導入、器件變更、老器件廢止等有專門團隊負責,研發工程師一般沒有權限進行操作,只能“有什么用什么”,基本不可能用到“非車規”器件;
(3) Tier 1和OEM差不多,為保證可靠性和項目進度,也喜歡沿用老設計,專業名詞叫“carry over”,也就是一般量產項目很少采用新器件做全新設計,這個前面也講過。
那有沒有可能存在一種情況,非得用“非車規”器件呢?基本沒有。Tier 1沒有理由去使用“非車規”的器件,除非這個器件不在AECQ范圍內,如開關、電機、繼電器等機電器件,還有連接器、電線、PCB等,但這些物料都有其相應的行業標準。
因此,對想要進入汽車行業的Tier 2來說,AEC-Q標準就是個門檻。
激光雷達器件過“車規”,
不等于激光雷達也過了“車規”
講了半天,小伙伴發現一個問題沒有,我最初提的問題是“激光器件Laser Components”有“車規級”標準嗎?而不是問“激光雷達”,為什么?
AEC-Q102 REV A規定的器件范圍
來回顧一下AEC-Q102規定的范圍:應用于車內或車外的光電子半導體optoelectronic semiconductors,如:LED,光電二極管,激光器件,從晶圓Wafer Fab技術講,還有光電晶體管。其中有激光雷達嗎?AEC-Q102標準中還真出現了一次Lidar這個詞,不過是說Laser的應用。
AEC-Q102 REV A4.5章節
另外,我們從標準中AEC下面的一行字“Component Technical Committee”中也能來,他是管器件Component的,不是管零部件的。
AEC器件技術委員會
所以說,AEC-Q102標準不是用于激光雷達的,是用于激光雷達中用到的元器件的。這么說吧,所有的AEC—Q102標準,全部都是規定電子元器件的,而非電子零部件。因此,元器件通過了ACE-Q102標準下的“車規”,不代表激光雷達也通過了。
有“車規級”的激光雷達嗎?
在回答這個問題前,我們先科普一下電子零部件標準。對于業內具體做設計的小伙伴們來講,這些標準可能是耳熟能詳的,但對于Tier 2或者OEM,大多數人還真不一定能講清楚。
下面是筆者總結的汽車行業電子零部件相關標準,有國標也有相應的國際標準,可能不全,但基本上就這么多,基于這些行業標準,電子零部件通過相應測試項目及等級,就可以認為滿足了車載應用標準。
當然了,大多數車企會要求按照自己的標準來,國內的一般都參考國際標準,或其合資伙伴的標準,外資品牌都有其自有標準,某些測試項目是ISO/IEC標準中是沒有的,比如福特、大眾的不少標準都是高于ISO/IEC標準的,各家標準的對比這個事情比較復雜,寫出來估計大家也看不下去,也看不懂,在此略過不談。
但有一點大家要記住,ISO/IEC等國際標準可以看做是所有標準的元標準,無論國標、企標等其他標準,都可以看作其衍生標準。對初入行或想了解汽車行業標準的小伙伴們,建議從ISO/IEC等國際標準入手,建議讀英文原文,并且要多讀,反復讀。不要試圖一次從頭讀到尾,一般人做也不到。可以跳著讀,也可以先挑自己需要的部分讀,或者感興趣的章節去讀。
對汽車電子零部件來講,比如VCU模塊,ECU模塊等,其首先需要選用符合AEC標準的電子元器件,再以電子零部件總成的方式,依據相關行業標準,在合規試驗室,通過OEM規定的相關測試項目及等級,拿到測試報告,然后才可以裝車量產。至于具體測試計劃、測試項目、周期、測試工裝、費用等,掰開講內容非常多。
前面已講過,這里再重申一下:汽車電子零部件的試驗標準,也是非強制性標準。
好,回到小標題,有“車規級”的激光雷達嗎?答案是:有,也沒有。此話怎講?
廣義上來講,“車規級”的激光雷達可以指采用了“車規級”激光器及光電探測器(SiPM)的激光雷達,并且,激光雷達產品本身通過了相應的汽車行業零部件標準測試要求。Tier 1具有IATF 16949等汽車行業認證,這時才可以講這個激光雷達是“車規級”的。
但這并不準確,甚至顯得很業余。在汽車行業內部,大家一般并不這么講,因為聽起來、不專業,大企業根本不屑于講自己的零部件是“車規級”的,你啥時候見過博世宣傳自己的ESP或iBooster是“車規級”的?
“車規級”要點總結
注意,敲黑板了,下面是結論,以后要考的:
(1) AECQ是器件級標準,一般講的“車規級”是指某些種類的電子元器件,而電子零部件沒有特定的“車規級”標準,不存在所謂的“車規級”零部件(嚴格意義上,可以說芯片、激光器或探測器達到了“車規級”,但不能說域控制器或激光雷達達到了“車規級”);
(2)如果只說滿足車規級標準,或者說溫度范圍滿足車載應用,而不說具體通過了哪個AEC-Q標準,都是假的“車規級”;
(3)只有器件手冊datasheet上注明了“AEC-Q*** Qualified”,才表明此器件通過了車規級器件測試標準認證,是“車規級”的,此時器件供應商是能夠提供合規測試報告的。
記住這三點,以后就不會被“無良商家”的廣告忽悠了,或者遇到滿嘴跑火車的人,你也可以把這篇文章甩給他,讓他好好學習學習。
技術的發展與“車規”標準的進化
最近在外網看了一篇關于AEC標準的文章,寫得挺好的,原文較長,我大概給大家翻譯一下,下面是部分原文:
汽車級標準的進化(來源:microcontrollertips.com)
我大概總結一下:
車規級認證意味著元器件的生產制造和性能是符合特定的行業標準的;
車規級認證標準不是一成不變的,它是鮮活的,是不斷進化的;
新標準是為應對新技術而制定的;
現有標準也會因新技術和新的應用而不斷地更新和進化;
車規級測試標準不期望涵蓋電子元件的所有使用場景和所有可能的故障模式。
“進化中”的AEC標準
AEC-Q100、AEC-Q101和AEC-Q200這三個標準是最早制訂的、也最常被引用的AEC-Q標準。在AEC網站上的“文檔”頁面列出了37個標準和子標準,其中七個被列為“新New”或“初始版本Initial release”。所以說AEC-Q標準是在不斷進化的,特別是隨著高級駕駛輔助系統(ADAS)和自動駕駛等新技術的發展,標準還將保持這種持續更新的狀態,以適應新技術和應用的需求。
比如,專門為光電半導體optoelectronics, MEMS傳感器, 以及模組multichip modules制定的標準:
AEC-Q102:汽車應用的光電半導體應力測試標準
AEC-Q103:MEMS壓力傳感器應力測試標準
AEC-Q104:汽車應用的多芯片模塊(MCM)應力測試標準
AEC-Q102標準解讀
AEC-Q102上面我們在前面已經講得比較多了,現在專門講一下這個標準的發展和進化。
AEC-Q102最初專注于光電二極管photodiodes,于2016年修訂后增加了LED,適用于所有汽車內外部照明應用。隨著新技術和應用的發展,標準也在不斷發展。
AEC-Q102于2020年4月再次修訂,為激光雷達系統應用添加了激光器。標準定義了光電子半導體認證的最低應力測試要求和參考測試條件,同時它結合了各種測試標準,如JEDEC,IEC,MIL-STD,及各種制造商資格標準,對器件提出了最高水準的測試要求。
比如,對于光電半導體而言,使用壽命在很大程度上取決于應用。內部照明的要求就不那么嚴格,而用于車輛外部(比如前大燈和激光雷達)時,對可靠性的要求就要大幅度提高。另外,與乘用車相比,在卡車上的應用對長壽命的要求可能就要更高一些,這些在新標準中均有體現,而這些內容在之前的標準中是沒有的。
AEC-Q102 REV A中對LED可靠性驗證的規定
另外,對比AEC-Q101的新舊版本,也能更明顯地看出來這種變化。光電半導體原來是涵蓋在《AEC-Q101分立半導體元件的應力測試標準》中的,在版本從D更新到E后,光電半導體相關內容全部轉到了新的AEC-Q102標準中去。
另外,標準的誕生離不開眾多相關領域的專家和公司,他們做出了極其重要的貢獻。這從另一方面也能看出,AEC始終與業內專家和公司保持著緊密聯系,AEC也會周期地的召開會議討論標準問題,這個后面單獨講。
AEC-Q102標準制定的參與者(來源:Hella)
QEC-Q102標準能帶來哪些好處?這個Hella總結了一下,我們直接搬過來,最后一條算是Hella加的吧,畢竟主業是做車燈的:
有法可依;
標準匯集了超過60家公司的知識經驗;
專注汽車級行業需求,并覆蓋了所有汽車級應用范圍;
對所有電子元器件的平等性要求;
推動新的車輛照明技術的應用。AEC-Q102標準的優點(來源:Hella)
AEC-Q103標準解讀
AEC-Q103是專門為MEMS壓力傳感器測試制定的標準。
對自動駕駛技術來講,車輛定位(GPS)、車輛的加減速(多軸加速度傳感器)、車輛的姿態(陀螺儀)等應用,包括未來的飛行汽車,基于對安全的自動駕駛的需求,MEMS器件都是必不可少的。
MEMS器件對自動駕駛技術的重要性
其實在AEC-Q100里面是涵蓋了MEMS傳感器的,但是沒用細分到壓力傳感器。在MEMS家族中,壓力傳感器是個特例。這也很好理解,你想一下,要想測氣體壓力,你就得開個孔,讓需要測量的氣體進來,這樣才能進行測量,而其他用途,比如溫度、磁場、加速度等就可以間接進行測量。
在標準的Scope中也明確了,這個標準要和AEC-100結合使用,也就是說,AEC-Q103是專門針對壓力傳感器制定了一些額外的測試要求。
除了大家熟知的胎壓監測應用外,發動機管理系統、車輛穩定性、乘客安全系統和排放控制等方面的都有壓力傳感器的應用,這個我們后面再講。
AEC-Q103對壓力傳感器的應用并沒有給出很詳細的說明,僅從機械等級角度進行了兩類區分,M1是通用傳感器,M2是用于TPMS的。
AEC-Q104標準解讀
AEC-Q104是專門為Multichip Modules (MCM)多芯片模組制定的標準,這個標準很特殊。
前面我們講過,AEC-Q全是規定電子元器件的,而MCM是由多個元器件組成的一個模組,從某種意義上來講,它算是一個小型零部件了(其實MEMS也算是MCM,實際上AEC-Q104也包含了),只不過MCM是把一些芯片加器件做成了一個獨立封裝Package的形式,對外連接可以是焊盤,或者是連接器。
目前標準僅適用于那些設計出來是可以直接焊接在PCB (Printed Circuit Board) 印刷電路板上的MCM的,這一點大家注意。
AEC-Q104是2017年initial release的,目前還沒有版本號,和AEC-Q103一樣,還沒有定稿。AEC-Q104標準本身的范圍并沒有規定得很寬,明確的范圍包括LED模組、MEMs、SSD(Solid State Drives)以及帶連接器的MCMs。因為可能需要一些專門的規定和測試程序,AECQ-104明確了不包括大家熟知的IGBT和Power MOSFET模組。
MCM模組外觀
比如英飛凌的IGBT模組芯片手冊,AEC-Q104就僅寫了汽車應用, 沒有給出測試標準。
另外,還有一個比較特別的地方,AEC-Q103和AEC-Q104在參考標準里面分別引入了ISO 16750-4(氣候負荷)及ISO 16750-5(化學負荷),在這其他的AEC標準里是沒有過的。前面我們講過,ISO 16750是汽車行業電子零部件標準,這就有意思了,所以說從某種意義上來講,MCM算是一個小型零部件了。
除MCM外,AEC-Q104對SIP(System in Package,系統級封裝)也有指導意義。
SIP跟我們經常談到的SOC(System on chip)類似,SOC是在一個chip上做了個系統,而SIP是一個Package。當然了,SOC是芯片供應商直接做好了,以一個芯片的形式提供給Tier 1使用,而SIP既可以是芯片供應商來做,也可以是和Tier 1或OEM基于具體應用來定制開發的產品。
這個AEC-104中已清晰地規定了哪些產品可以做成SIP形式,以在做成SIP時,哪些由芯片廠商做、哪些由Tier 1做、哪些由Tier 1.5做。(關于這個,我們后面會再單獨發文章解析)
AEC-Q104是AEC與Intel、Infineon、Microchip, NXP, OnSemi、TI等公司一起制定的,是行業首個適用于MCM和SIP、定義了BLR(Board Level Reliability板級可靠性)測試的標準。這解決了什么問題呢?
隨著車輛電動化智能化及輔助駕駛技術的發展,原來元器件級采用AEC標準,零部件級采用ISO/IEC標準(前文分析過零部件標準,ctimes.com只寫了ISO16750),而對MCM和SIP,沒有適用標準。怎么進行可靠性測試,這是長期以來困擾芯片供應商及Tier 1的一個問題。
MCM/SIP是由多個芯片及器件組成的一個封裝,那這其中用到的芯片和器件還需要相應的AEC-Q測試嗎?這是個很好的問題,所以標準中也給出了建議——可以使用MCM中相應器件的AEC-Q100, AEC-Q101,或AEC-Q200認證原始數據去簡化AEC-Q104認證。
ctimes.com對這個問題解釋得比較清楚,我們可以參考一下。就是說不管你用到了哪些器件,在你把這些器件封裝起來之前,最好已經過了相應的AEC-Q100, AEC-Q101,或AEC-Q200認證測試。
上述內容是強烈建議你去使用全部符合AEC-Q認證的器件去做MCM,但是如果你真的要說我就是任性,我就“偏不用”,行不行?答案是“也可以”。標準原文是這么寫的:考慮到成本及客戶可能同意你這么干,AEC不要求每個sub-component(子器件)必須通過認證,但是鼓勵MCM制造商采用AEC標準去認證子器件,從而使MCM達到最高的質量水平(promote best MCM quality)。
這里面的用詞非常講究,大家細品一下,包括括“address”、“encouraged”、“available”、“promote”等。所以我前面說過,推薦大家一定要去看標準原文,而不是翻譯過來的,原文才能咂摸出來那個欲說還羞、欲言又止,但又心有不甘的那種感覺,你品,你細品。
老外說話比較繞,不直來直去,我用漢語再給大家翻譯一下,可以指導大家未來的工作,大家記住了:
(1) MCM要全部采用AEC認證的器件;
(2)然后只用進行Group H測試即可;
(3)否則的話你就得把所有測試項全來一遍;
關于(1),對那些聲稱達到“車規級”的LTE模組、5G模組、WiFi-BLE模組等,我們要區分一下看它們有沒有通過AEC-Q測試。如果僅僅只是核心芯片有AEC-Q,或聲稱溫度范圍達到了車載應用的最低85度要求,有個IATF16949或PPAP,然后就敢說自己是 “車規級”的,大家就要擦亮眼睛。
某通信模組的 “車規級”
關于(3),如果你說全做太花錢了,客戶同意你“可以不做”,那也行;但你拿標準原文去給客戶看看,我就不信哪個客戶會說“不用做”。
下面這個測試流程很清楚地寫明了認證測試怎么做,大家可以細看一下,很有意思。
“新四化”相關技術對元器件車規標準的推動
除原來就有的三個AEC標準外(Q100,Q101和Q200),我們已經把最新的三個標準都分析了一遍,現在我們再看一下主動及被動安全、電動化、智能化與網聯化對車規級標準的推動。
前面我們講過,AEC標準是一個鮮活的,一直在進化的標準。
AEC-Q102標準在汽車
“新四化”中的應用
隨著技術的發展,車輛用LED做照明的越來越多,大家買車也要看前大燈是不是LED的,有沒有AFS自動轉向功能,最后要這個配置還得加錢,就是因為照明作為一種主動安全及被動安全(比如日間行車燈DRL daytime running lamps)措施,大家都意識到了它的重要性。
BMW已經量產了激光大燈,從最早的鹵素燈,氙氣大燈,LED大燈,進化到現在的激光大燈,能耗比LED降低了30%,反正就是很亮、很貴,具體有多貴,咱也不知道,咱也不敢問。
LED用于屏幕背光,質量的可靠性靠什么來保證?只能靠器件的行業標準。
還有就是現在火熱的激光雷達,其核心就是激光器,前面我們講過了,但有一點大家注意到沒有,激光發射出去了,反射回來誰來接收?這就要用到光電探測器Photomultipliers(SiPM)了。
激光器和探測器都過了AEC-102認證,這個激光雷達才有了車載應用的基礎,用起來質量才有保證,自動駕駛車輛的安全才有保障。
AEC-Q103標準在汽車
“新四化”中的應用
前面講過,除了大家熟知的胎壓監測應用外,MEMS壓力傳感器廣泛應用于傳動系統和安全系統。乘客安全系統一個典型的安全相關的應用估計一般人不是很了解,比如側面碰撞和行人保護應用。
還有就是用于電動車鋰電池的壓力檢測,這也是一個安全需求。研究表明,測量電池組內部的壓力能夠很好地提前對電池熱失控進行預警。如果電池漏氣,加上溫度的突然上升,就會增加電池組內部的壓力,從而產生壓力脈沖。MEMS壓力傳感器會持續地監測電池包內部的壓力,并實時發給BMS。即使在停車狀態,電池包的任何壓力異常都可以通過MEMS壓力傳感器進行監測。
基于這些和車輛安全相關的應用需求,AEC-Q100已經無法滿足,于是AEC-Q103應運而生。另外,這個標準是2019年才發布的,目前還是initial release初版狀態,還沒有版本號,所以現在看的壓力傳感器芯片手冊上面寫的還是依據AEC-100,這也是正常的。
AEC-Q104標準在汽車
“新四化”中的應用
目前能看到的直接采用AEC-Q104認證的MCM較少,不過我還是找到了一個,剛好是和自動駕駛技術相關的。
MCM可以用于802.11p DSRC、C-V2X應用,里面集成了一個5 GHz單刀雙擲收發開關,一個5 GHz高增益LNA(low-noise amplifier低噪放),一個5 GHz的PA(power amplifier功放)。
技術的發展及標準的進化
基于目前汽車行業的技術發展趨勢,AEC-Q標準并未包含某些器件及技術應用的認證測試,包括我們前面提到的Power MCM。
還有,目前攝像頭的圖像傳感器(image sensor)和圖像信號處理器(ISP)適用的是AEC-Q100集成電路認證,而攝像頭模組是按照零部件來算的。但從某種意義上講,攝像頭模組也許可以參考AEC-Q104的MCM測試要求,然后攝像頭總成按零部件?這個筆者并沒有找到相關參考資料。
另外就是車載觸摸屏及顯示器,目前也沒有相應的AEC-Q標準,但是據說啟動會議在2017年已經開過了。
車載觸摸屏及顯示器的車規級標準
其實顯示器和攝像頭很接近,結構上都是玻璃加一部分集成電路,對外接口也都是一樣的FPC連接器,但這目前是不符合AEC-Q104中對MCM范圍及接口部分描述的。
在此順便提一下另外一個標準。為了解決基于人類和計算機視覺的汽車成像系統在圖像質量測量方面存在的相當大的模糊性,IEEE‐SA(IEEE標準協會)專門成立了IEEE-SA P2020汽車成像標準工作組,并已開始著手開發新標準,目標是指定用于測量和測試汽車系統中圖像質量的方法和指標(不同于AEC-Q專注于器件級別)。
IEEE-SA P2020于2016年7月召開了初次電話會議,并且每年都會有幾次會議,最近的一次是2022年2月,類似于AEC的周期性會議模式。
HMI和計算機視覺系統是智能座艙、ADAS和自動駕駛功能不可或缺的一部分,而IEEE的這個標準未來將對這些領域的技術應用產生重要的指導作用。
最后,我們引用microcontrollertips.com的一段話作為結束:“車規級”認證是一個不斷進化的、涵蓋了多種器件范圍的標準,AEC組織也在一直不斷地根據現有技術發展審視現有標準,并不斷地開發新的標準,以滿足如ADAS、自動駕駛、計算機視覺和激光雷達等新應用的需求。符合AEC-Q認證(AEC-Q qualified)是產品系統設計及硬件選型中的重要因素。”
AEC的歷史及基本概念
前面我們著重介紹了AEC的最新標準,以及順帶介紹了已有標準,但并沒有直接從AEC的前世今生來介紹,這多少有點不太符合我們一貫的風格。沒關系,接下來我們就開始正式介紹,大家搬好小板凳,泡上茶,我要開課了。
AEC歷史及簡介
AEC的全稱是Automotive Electronics Council Component Technical Committee,汽車電子委員會元器件技術委員會,不過大家一般都簡稱AEC汽車電子委員會,從其后面的“Component”能看出來,AEC是專注于元器件級別的,這個我們前面講過。
AEC成立的目的就是為了器件通用化。最早的時候行業是這樣的,比如福特要用一家芯片/器件供應商的A芯片/器件,供應商就要按照福特的要求進行測試,通過后福特才會采用;但是如果克萊斯勒也要用,他是不是不認可福特的測試的,供應商就要再按克萊斯勒的要求再測一遍,才能用于克萊斯勒。福特和克萊斯勒提議建立AEC就是為了通用化,大家可以一起用,降低測試成本。
創建AEC的想法發生在1992年夏天的JEDEC會議上。GM (通用汽車)的德科電子(Delco Electronics)的Servais會見了Chrysler(克萊斯勒)的Jennings,隨后他們倆聊了在電子零件資格認證領域遇到的一些共同困難,隨后提到了“通用資格規范”的想法,這是改善這種情況的一種可能的方法。
在1993 德科電子的一次會議上,討論了每家公司使用的各種資格認證方法。會議決定,“通用認證規范”的想法是可行的,此后不久就開始了Q100(集成電路應力測試認證)的工作,主要IC供應商都參與了標準的制定。AEC-Q100的初始版本(最初叫CDF-AEC Q100)在 1994 年 6 月提交給了所有的 IC 供應商,這個文件代表了克萊斯勒,德爾科電子和福特的首選資格證書。
這個文件鼓勵交換資格數據,并指出,如果一個部件符合該文件,則該部件對所有三家公司都具有資格。該文件不涉及定價問題,也不阻止三家公司使用其他資格要求作為特殊條件。
此后AEC又陸續制定了其他零件類別的認證規范:如用于分立半導體器件的AEC-Q101和用于被動器件的AEC-Q200。
AEC每年舉辦一次可靠性研討會。在1995年印第安納波利斯的研討會上,拍攝了以下AEC創始人的照片,來,我們膜拜一下大神:
AEC會員
汽車電子委員會(AEC)最初由克萊斯勒,福特和通用汽車成立,最初AEC由質量體系委員會和組件技術委員會兩個委員會組成,現在的委員是由一些企業的固定會員(Sustaining Members)及其他技術會員(Technical members)、準會員(Associate members)及特邀會員(Guest members)的代表組成。
固定會員主要來自Tier 1供應商及器件制造商,包括:Aptiv安波福、Bosch博世, Bose博士、Continental大陸、Cummins康明斯、Denso電裝、Gentex、Harman哈曼、Hella海拉、John Deere、Kostal科世達、Lear李爾、Magna麥格納、Sirius XM,、Valeo法雷奧、Veoneer、Visteon偉世通、ZF采埃孚。
怎么樣,業內小伙伴們對這些公司是不是都很熟?他們如今在汽車行業依然是大名鼎鼎,如雷貫耳。
有一點大家發現沒有,就是這里面幾乎沒有國內公司,收購而來的Nexperia和ISSI勉強算兩個。所以國內的Tier 1及國產汽車電子器件/芯片供應商還需要繼續努力。
AEC-Q標準是免費的
官網有段話挺有意思的:AEC組件技術委員會是為可靠、高質量的電子元器件建立標準的標準化機構。符合這些規范的組件適用于惡劣的汽車環境,無需額外的元器件級認證測試。本網站提供AEC組件技術委員會制定的技術文件。這些文檔可以直接下載。
行業小伙伴們發現什么問題沒有?AECQ標準竟然是免費的,還是可以直接下載來使用的,驚不驚喜,意不意外?AEC是不是很良心?是不是打破了我們的認知?
可能會有小伙伴們說,我就從來沒買過標準啊?那我只能呵呵了。拋開盜版的標準不談,很少有標準是免費的,包括大家常見的ISO、SAE等國際標準,GB國標也是要購買的,就是要便宜的多。筆者曾經購買過一個SAE標準,花了700多。大家在公司用的標準,其實是公司買的,都不是免費得來的。
制定標準需要組織,需要人,就一定需要資金。雖然這些組織基本都是非營利性組織,但組織運轉也是需要資金支持的。另外,工業標準本身就是市場的產物,本身就是商品,制定標準的成本實際上就是分攤給那些從標準中獲益的機構。比如DIN(德國工業標準)的60%的工作是通過標準的收費來支撐的。
我們來看一下這個SAEJ3018和自動駕駛道路測試相關的標準,價格是87美金。
AEC 年度研討會Annual Workshops
前面講AEC歷史時提過,AEC組織每年都有固定的可靠性研討會,2019年因為還沒有疫情,研討會是正常舉辦了的。
關于2019年的會議,官網信息如下:2019歐洲AEC年度可靠性研討會,暨第二屆歐洲汽車電子可靠性研討會于10月15日至16日在德國慕尼黑喜來登酒店舉行,參加會議的有:汽車電子Tier 1用戶,Tier 2供應商以及歐洲OEM公司的與會代表。會議討論了影響汽車電子元件的18個各種主題的報告。歐洲研討會的會議形式與美國類似,包括了7個開放論壇小組討論,各種AEC文件的討論,以及對未來AEC-Q規范的開發和改進的建議。
原定于2020年舉行的年度會議,因疫情改期到了2021年春,結果最后還是取消了。
2022年的AEC可靠性研討會的計劃目前還沒有定下來。關于2022年研討會活動的更多細節,包括演講議題和主要研討會日期,屆時會在AEC官網公布。
我放幾個AEC研討會的議題小伙伴們感受下:
一個人體靜電放電的調查
電熱導致的寄生柵極泄漏
邦線工藝的評估和改進
CMOS器件不同ESD模型失效特征的比較
制定一個IC因瞬態傳導干擾導致閂鎖的標準
另外,除了年度的可靠性研討會外,還有定期的技術委員會會議(Technical Committee Meetings),比如每周、每月及年度。另外,年度的技術委員會會議是和年度可靠性研討會同時間舉行的。
AEC章程
2. Functional Safety Quality-Managed:Ti提供一系列文檔來幫助Tier 1設計人員進行功能安全設計,降低產品認證的工作量及認證難度,提供的文檔包括器件的功能安全FIT值計算,FMEDA及功能安全手冊等。器件不是根據功能安全標準要求的流程開發的,而是根據Ti通用質量管理流程。
3. Functional Safety-Compliant:有證書,采用了功能安全開發流程,文檔多了FTA(故障樹分析),有功能安全證書。
我們解釋一下:
第一類產品:不屬于功能安全器件產品類別。此類器件通常沒有集成安全相關功能,但是開發功能安全系統時又離不開此類器件的參與。Ti 提供的FIT和FMD將有助于進行安全分析。其實這已經很好了,因為很多器件,比如被動器件和分立半導體器件(因為Ti不怎么做這類器件,就沒涉及),設計時又離不開,用的又多(比起芯片數量要多得多,不是一個數量級的),供應商一般也不提供FIT和FMD,你需要自己找數據。
第二類產品:屬于功能安全器件產品類別。此類器件通常已集成了復雜的內部監控及診斷功能,同時TI又提供了相當多的支持文檔,用于功能安全產品設計時,可以大幅降低產品認證的工作量及認證難度。
第三類產品:功能安全合規產品。此類器件通常是集成了安全特性的復雜器件,如MCU、處理器、電機驅動芯片、電源管理芯片等。此類產品是在Ti通用質量管理流程的基礎上,采用Ti的功能安全流程開發的。可以提供FTA(故障樹分析),有功能安全認證證書。采用此類器件可大幅降低功能安全產品的設計難度及認證難度,或者說,是設計功能安全產品的唯一高效途徑。
-
汽車電子
+關注
關注
3026文章
7941瀏覽量
166910 -
汽車
+關注
關注
13文章
3493瀏覽量
37252
發布評論請先 登錄
相關推薦
深入剖析車規級IGBT模組的成本要素
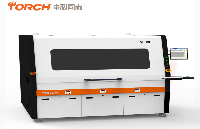
車規級IGBT模組:成本背后的復雜系統解析
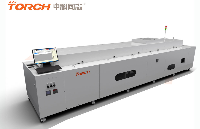
江蘇潤石最新發布7顆車規級型號
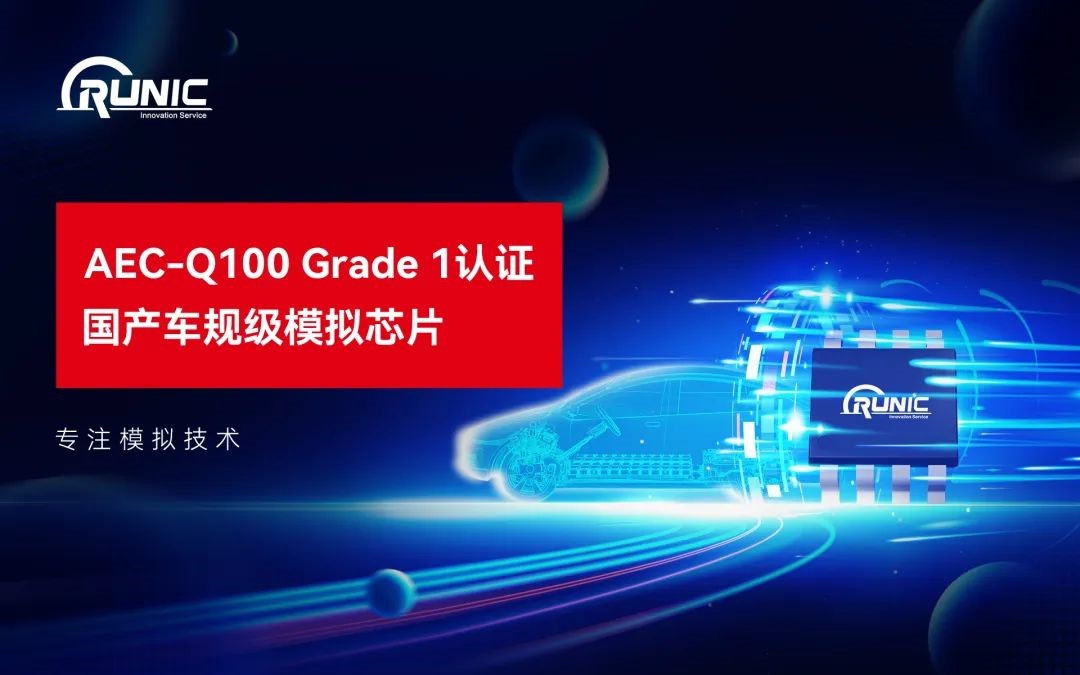
評論