壓力與溫度
和在刻蝕工藝中一樣,半導體制造商在沉積過程中也會通過控制溫度、壓力等不同條件來把控膜層沉積的質量。例如,降低壓強,沉積速率就會放慢,但可以提高垂直方向的沉積質量。因為,壓強低表明設備內反應氣體粒子的數量少,粒子之間發生沖撞的概率就少,不會妨礙粒子的直線運動。施加高溫則可以提高膜層的純度。當然,這樣一來就無法使用鋁(其熔點為550度)等熔點低的金屬材料。
▲ 圖7:壓強對沉積工藝的影響
因此,在不同需求下,沉積相同材料也可采用完全不同的沉積方式。例如,同樣是沉積二氧化硅(SiO2),柵極絕緣層與STI所需特性就不同,其沉積的方式也不同。柵極絕緣層是核心元件區域,要求較高的沉積質量,應采用高溫低壓的方式;STI則不然,它只要起到兩個元件間的絕緣作用即可,通過低溫高壓的方式加快沉積速率才是關鍵。
材料選擇上的難題
您或許常會在新聞中看到這樣的報道:“發現了性能高出XX倍的新材料”。只看新聞內容,會感覺一場翻天覆地的半導體革命似乎即將來臨。但在所謂的“新材料”中,真的能派上用場的卻寥寥無幾。因為,材料本身的特性好,并不代表它一定能制成高性能的半導體。對沉積材料的要求可不比沉積設備低。下面,我們來看一看材料的特性會對半導體制程產生什么樣的影響。
▲ 圖8:加熱導致圖形損壞
物體遇熱體積會變大,這種現象被稱作熱膨脹。鐵軌之間留有縫隙就是為了防止鐵軌在炎熱的夏天因膨脹變形。半導體制程中也會出現這種熱膨脹現象。問題在于,每一種材料的熱膨脹程度不同,例如鋁的熱膨脹系數是氧化硅的40倍之多。舉個比較極端的例子:如果在氧化硅上沉積了鋁薄膜,即便鋁薄膜沉積很成功,一旦進入后續的高溫工藝,其內部結構就會完全被破損。換句話說,如果采用膨脹系數完全不同的材料替代之前的沉積材料,會嚴重影響高溫條件下的產品良率。
▲ 圖9:電遷移現象
除此之外,還要考慮材料的電遷移(EM,Electromigration)現象。電遷移是指在金屬布線上施加電流時,移動的電荷撞擊金屬原子,使其發生遷移的現象。鋁等輕金屬很容易發生這種電遷移現象。為防止鋁的電遷移現象,半導體制造商們開始用銅布線替代鋁,結果是又多了一道防止銅擴散的阻擋層沉積工藝。隨著半導體不斷微細化發展,銅布線也開始出現電遷移現象。為攻克這一難關,英特爾又用鈷布線取代了銅。而既然核心金屬布線層的材料發生了變化,上下層的工藝也肯定要跟著變。可見,想解決材料的電遷移現象,前后方的工藝也要隨之發生很大變化。
要始終銘記:半導體制程是數百個工藝錯綜復雜緊密連接而成的,牽一發而動全身。新材料是好是壞,不能單看材料本身的特性,還要看能不能與前后方工藝相連,畢竟沉積材料不能獨立存在。
結論:一種材料,多種方法
讀到這兒,估計讀者們已經發現了幾點有趣之處了:首先,同樣的材料可以通過不同的方法制成。例如,二氧化硅(SiO2)可以通過氧化工藝,也可以通過沉積工藝形成。即便是相同的材料,如果通過不同工藝涂敷到半導體上,其物理特性也會截然不同。
其次,氧化、刻蝕、沉積等看似完全不同的工藝其實有很多共同之處。比如,物理刻蝕中采用的濺射方法,在沉積工藝中同樣也會使用,區別在于“是濺射要刻蝕的晶圓本身”,還是“把濺射出來的粒子沉積到晶圓上”。化學刻蝕中最重要的一點就是刻蝕氣體與反應源生成的廢氣是否易于排放,化學氣相沉積也同樣如此。CVD過程中生成的副產物也要易于揮發、易于排放,這樣后續工藝才會變得更容易。
可見,受半導體制造商青睞的新材料,并不是其本身特性有多優秀的材料,而是其沉積速率、純度等特性易于控制的材料。而且,沉積材料還要易于通過刻蝕或CMP7等工藝去除。如果采用需要過高溫度的材料,可能會因高溫改變已沉積的其他材料。而若采用對溫度非常敏感的材料,又會出現在下一道工藝中無法加熱的問題。
化學機械拋光(CMP,Chemical Mechanical Polishing):通過物理、化學反應研磨, 去除非所需物質,使半導體晶圓表面變得平坦。
如上文所述,“半導體制程由數百個制造工藝緊密連接而成”。想做好每一道工藝,對其他相關部門的業務也要有很好的把握。要擅于與同事溝通,更要懂得準確無誤地傳達自己的想法。一個半導體產品需要多人合作才可以完成,雖然過程有些辛苦,但也很值得。(回顧上一期)
審核編輯:湯梓紅
-
半導體
+關注
關注
334文章
27290瀏覽量
218084 -
制造工藝
+關注
關注
2文章
179瀏覽量
19751 -
刻蝕工藝
+關注
關注
2文章
37瀏覽量
8415
原文標題:半導體前端工藝:沉積——“更小、更多”,微細化的關鍵(下)
文章出處:【微信號:閃德半導體,微信公眾號:閃德半導體】歡迎添加關注!文章轉載請注明出處。
發布評論請先 登錄
相關推薦
半導體前端工藝之刻蝕工藝
半導體工藝講座
《炬豐科技-半導體工藝》IC制造工藝
半導體設備行業跟蹤報告:ALD技術進行薄膜沉積工藝優勢
半導體前端工藝:沉積——“更小、更多”,微細化的關鍵(上)
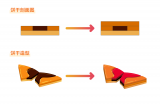
半導體前端工藝之沉積工藝
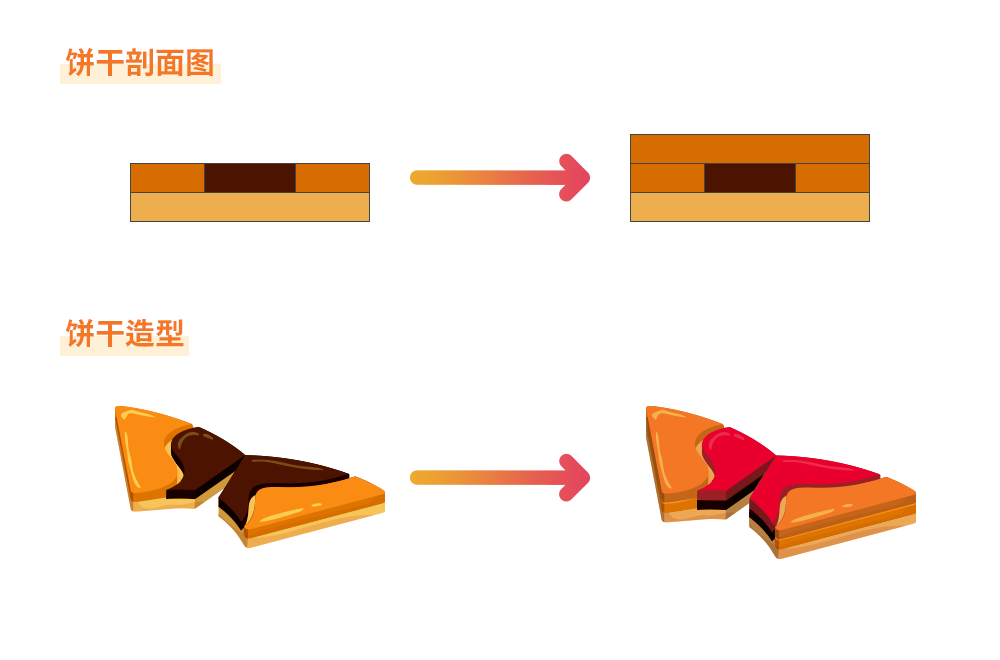
一文詳解半導體薄膜沉積工藝
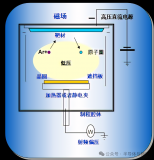
評論