?
圓柱電池一般為全極耳電池(大圓柱),相對方形電池制造工藝,全極耳圓柱電池前段工序取消了模切制片工序,其余和方形電池制造流程基本一致。裝配段典型工序為揉平、包膠。鋰電池極耳揉平方式在電池制程過程中占據(jù)重要的地位;對于全極耳電池,正/負極片空白區(qū)位于電池兩端,一般需要先對空白區(qū)揉平,使其端面致密,再對其進行極耳焊接;為了防止電池的極耳短路,在極耳焊接之前,會對極耳要外露的部分提前進行包膠。中段/后段與方形電池測試流程也基本一致。下圖為全極耳圓柱電池制造流程。
全極耳圓柱電池制造流程
設備主要功能及描述
1.1 圓柱鋰電池發(fā)展現(xiàn)狀
圓柱鋰電池也稱為圓形鋰電池,最早是由日本SONY公司于1992年發(fā)明的18650鋰電池,其歷史相當悠久,采用較為成熟的卷繞工藝,自動化程度高,產(chǎn)品質(zhì)量穩(wěn)定,成本相對較低,目前已大面積普及與廣泛應用。
圓柱18650電池是被研究得最多、技術討論最充分的電池品種。單體主要由正極、負極、隔膜、正極負極集電極、安全閥、過流保護裝置、絕緣件和殼體共同組成。殼體,早期鋼殼較多,當前以鋁殼為主。其內(nèi)部結構如圖1所示。
圖1 圓柱電芯內(nèi)部結構
1.2 圓柱鋰電池裝配設備
近幾年,隨著新能源汽車市場的再一步擴大,以及消費者對續(xù)航里程要求的不斷提高,車企對動力電池在容量、生產(chǎn)成本、儲能壽命和產(chǎn)品附加屬性等方面都提出了更高的要求。在原材料領域尚未獲得巨大突破的前提下,適當增大圓柱鋰電池的尺寸以獲得更高能量密度便成為一種生產(chǎn)的主要方向。
如今鋰電池正在往安全性以及標準化的方向發(fā)展,設備的高精度、高效率、系列化以及高自動化生產(chǎn)線將成為行業(yè)發(fā)展的大方向。本節(jié)提供一種鋰電圓柱電池自動化生產(chǎn)線,實現(xiàn)高效自動化生產(chǎn),大大節(jié)省人力成本,極大提高產(chǎn)能和產(chǎn)品質(zhì)量及成品率,為客戶實現(xiàn)利益最大化。全自動化和智能化的鋰電池生產(chǎn)設備將在保證鋰電池生產(chǎn)工藝的基礎上,使生產(chǎn)出的鋰電池具有較好的一致性,高的安全性能和直通良率,從而降低生產(chǎn)成本。
圖2為圓柱電池的裝配工藝流程圖,實現(xiàn)了從卷芯到電芯焊接封口整個流程的自動化生產(chǎn)。圓柱電池裝配線用于實現(xiàn)圓柱鋰離子電池的電芯輸送、電芯與鋼殼的裝入、(-)Tab與鋼殼底部焊接、鋼殼滾槽、Hi-pot、X射線檢測、蓋帽焊接、注液、封口、清洗、套膜裝盒。所以整個圓柱電池裝配線設備包括以下設備:卷芯上料機構、J/R與B/I插入機、Tab焊接與縮口機、T/I插入機、輥槽機、短路檢測、注液機、(+)Tab焊接機、封口機等,后面一一重點介紹這些設備。
圖2 圓柱電池裝配工藝流程
1.3 圓柱電池裝配產(chǎn)線未來的發(fā)展趨勢
圓柱電池生產(chǎn)線使用時間比較長,相應的技術已經(jīng)非常成熟,現(xiàn)有的裝配線設備也大同小異。未來的發(fā)展趨勢,除了從材料方面繼續(xù)改善,找到高性能的電芯材料外,對于電池裝配生產(chǎn)線而言,效率、成本等依然是動力鋰電池未來發(fā)展的方向,對現(xiàn)有市場發(fā)展概況總結后有以下幾點值得關注:
①電池本體的性能方面,比如電池尺寸、能量密度等越來越大。
②裝配生產(chǎn)效率,在保證設備成本改動不大的情況下,不斷改善生產(chǎn)效率;現(xiàn)有的圓柱鋰電池裝配效率可達到120PPM,甚至更高。
③電池裝配線的自動化程度,顯而易見自動化程度高,人工成本減少了很多,同時生產(chǎn)的良率更容易控制。合理控制每個工序的制作時間,從而有效縮短鋰電池的生產(chǎn)時間,而且極大改善了工人的勞動強度大和生產(chǎn)成本高的問題。
④人機工程方向,設備易操作、易維修更是要關注的一點,保證設備操作的靈活性。
⑤縮短生產(chǎn)周期,提高產(chǎn)品質(zhì)量,降低生產(chǎn)成本是未來整體發(fā)展方向,模塊化技術的應用是自動化設備深度優(yōu)化的目標。
1.4 圓柱鋰電池生產(chǎn)裝配線的設計
對于圓柱電池產(chǎn)線的設計,針對客戶提出的要求會有不同的設計,根據(jù)在生產(chǎn)過程中遇到的問題及相應的實踐,主要要從以下幾個方面去考慮:
①產(chǎn)品的工藝:包括電池的大小、極耳的大小、焊接的厚度等。
②廠房空間大小:據(jù)此安排生產(chǎn)線設備的具體位置,以及要優(yōu)化的機構等,還要考慮人機工程,人工操作的方便性,以及后期維護的可操作性。
③設備的設計:結構越簡單越好,這樣更容易操作。
④生產(chǎn)線中節(jié)拍的分配:重點考慮瓶頸工位的效率,如果效率達不到,考慮將單工位改為雙工位甚至多工位,同時高的安全性能和直通良率也是重點關注的點。
⑤產(chǎn)品定位方式:對于客戶不同的需求,采用不同的產(chǎn)品定位方式,比如側邊定位、以兩邊為基準定位、夾具定位等。
⑥粉塵防止裝置:圓柱電池裝配線設備中基本都是每個需要除塵的設備中都有相應的除塵設施,比如集塵器、毛刷等。
⑦質(zhì)量檢測:整套裝配線中會涉及CCD檢測、電芯測厚檢測、絕緣檢測、短路檢測等。
⑧生產(chǎn)線的外觀的一致性:保持整套設備的美觀。
設備組成及關鍵結構
2.1 卷芯上料機
圓柱鋰電池的關鍵來料就是卷芯(極組),它是電池性能的重要保障之一,其制作工藝技術已經(jīng)研究成熟,因此不再繼續(xù)闡述。著重關注從卷芯(極組)開始裝配的設備流程,圓柱鋰電池的裝配線從卷芯上料開始,包括卷芯(極組)托盤投入、輸送線運輸、卷芯(極組)供應、空托盤堆疊、排出、卷芯(極組)裝入托杯、托杯輸送等工序環(huán)節(jié),整個過程對卷芯(極組)的定位要求準確,以及卷芯(極組)裝入托杯的高精確度,卷芯(極組)上料的效率也是設備重點考慮的地方,提高自動化程度與生產(chǎn)效率是市場、企業(yè)對未來設備的要求方向。
具體的工序流程在后面會配合相應的設備詳細介紹。
圖3是利用16×16的極組(卷芯)專用托盤進行極組供給,具體流程如下:人工通過小車(或者托盤輸送線)的方式將托盤投入到設備入口處,設備自動將托盤進行輸送、分盤、定位,使用機械手將托盤中的極組取放到極組專用托杯中,為極組入殼設備進行供料,具體的工藝流程如圖4所示。
圖4 卷芯(極組)設備工藝流程
設備每個工位完成的具體動作包括如下步驟:①卷芯托盤供給;②托盤升降機;③托盤移送;④卷芯移送;⑤卷芯移送傳送帶;⑥卷芯直徑檢查。
卷芯上料設備布局如圖5所示。
圖5 卷芯上料設備布局
1—極組托盤小車;2—極組托盤供料;3—極組托盤傳送;4—取出托盤內(nèi)極組;5—極組放入進料工裝內(nèi);6—空托盤疊放(5層);7—空托盤疊放(10層);8—空托盤小車排出
從上面的工藝流程中可以得知,卷芯上料機重點是把卷芯(極組)從托盤中取出并放在相應的托杯上,而準確性和工作效率是其重要的衡量標準。所以設備中的取料機械手的作用顯得尤為重要,選取該結構作為關鍵結構詳細說明,如圖6所示。
圖6 取料機械手
取料機械手在工作中,采用的16個夾子(手指)從極組托盤中取料,在氣動裝置的控制下可以高效完成相應動作。工作過程中的注意事項如下:
①卷芯夾取手指下降時有上下浮動功能。
②卷芯移送時一列的標準是16個。
③夾取手指的內(nèi)部及角保證光滑,卷芯不會有損傷。
④卷芯內(nèi)部不會因為夾取手指及套座移送而導致?lián)p傷。
2.2 J/R與B/I插入機
J/R即卷芯(極組),B/I即底部絕緣片。該工序的目的是將底部絕緣片(B/I)插入在極組(J/R)上,然后裝入鋼殼(或鋁殼)中,這是圓柱鋰電池裝配線的關鍵流程。結構相對較復雜,設備所完成的動作較多。
J/R與B/I插入機用于實現(xiàn)電芯的(-)端部整理、(-)端部外徑檢測、NG出料、自動上料、(-)Tab定位、下絕緣片裝入、折(-)內(nèi)極耳、折(-)外極耳、鋼殼自動供料、吸取粉塵、CCD檢查絕緣片與極耳是否蓋住中心孔、電芯入殼、NG排出、良品下料等功能。
其中極組由專用托杯通過輸送鏈板進行供給進入設備入口,分別對極組的終端Tab、先端Tab進行定位整理,插入B/I并隨即彎折Tab,通過視頻(CCD)對Tab彎折狀態(tài)與B/I狀態(tài)進行實時檢查;對鋼殼內(nèi)部進行除粉塵作業(yè),鋼殼插入極組。具體工藝流程如圖8所示。
圖8 工藝流程圖
1)設備的組成及工位劃分
①卷芯供料;
②B/I沖裁和插入;
③負極耳定位與折彎;
④CCD檢查;
⑤鋼殼供給及插入;
⑥鋼殼插入卷芯單元;
⑦良品與NG品排出。
2)關鍵結構
J/R與B/I插入機設備布局如圖9所示。
圖9 J/R與B/I插入機設備布局
1—料機械手;2—先端Tab定位與終端Tab定位;3—底部絕緣片插入;4—底部絕緣片沖裁;5—先端Tab彎折&終端Tab彎折;6—極組插入鋼殼(入殼);7—鋼殼供料;8—NG排出
從圖9中可知,底部絕緣片(B/I)插入、底部絕緣片(B/I)沖裁、先端Tab彎折與終端Tab彎折、極組插入鋼殼(入殼)、鋼殼供料等比較關鍵,對整個裝配出來的半成品有至關重要的作用,選取其中幾個機構做詳細的介紹說明。
①底部絕緣片(B/I)沖裁機構如圖10所示。
圖10 B/I(底部絕緣片)沖裁機構
1—伺服電機;2—上下導向;3—沖裁模具;4—B/I吸取機構;5—B/I卷料供給方向;6—B/I卷料回收裝置
底部絕緣片(B/I)的沖裁機構工作時重要注意事項如下:
a.B/I沖裁和供給時不會因靜電(有去靜電離子發(fā)生器)導致供給錯誤發(fā)生;
b.B/I插入使用負壓吸取方式;
c.B/I插入裝置設計為可上下浮動的構造,插入時卷芯上部不會有損傷;
d.B/I片材質(zhì):PP/PET建議厚度為0.3mm;
e.B/I顏色:藍色(顏色不允許白色和黑色);
f.B/I供給確認,使用真空壓力進行檢查;
g.B/I沖裁不會出現(xiàn)中心口偏移的現(xiàn)象;
h.底部絕緣片的沖裁模具材質(zhì)為SKD11。
②(-)2Tab(負極)折彎。如圖11所示,負極的兩個Tab折彎工藝以及其先后折彎順序可以清晰看出來,在工作過程中,Tab的折彎和視頻檢查先后進行,做到加工的精確性和完整度,保證加工質(zhì)量。
圖11 Tab折彎機構
③鋼殼供給機構。鋼殼供給機構如圖12所示,該機構的鋼殼供給方式為包裝箱供給鋼殼,磁石吸附供給方式供給數(shù)量為10層。卷芯插入前在鋼殼內(nèi)部進行正壓吹,采用負壓吸的方式對鋼殼進行清潔處理。
圖12 鋼殼供給機構
1—供料緩存Ⅰ;2—鋼殼吸取裝置Ⅰ;3—提升機構Ⅰ;4—換盤橫移;5—鋼殼輸出;6—供料緩存Ⅱ;7—鋼殼吸取裝置Ⅱ;8—提升機構Ⅱ
2.3 Tab焊接與縮口機及T/I插入機
如圖13所示,底部焊接機完成Tab焊接、縮口、插Pin、T/I插入等工藝,入殼后的極組投入設備,將(-)Tab與鋼殼底部進行電阻焊接、鋼殼口部縮頸、插入中心Pin、裝入T/I。過程中會分別對焊接強度、縮口外徑、中心Pin、T/I進行實時有效的檢查判斷。整體工藝流程如圖14所示。
圖13 底部焊接機
圖14 整體工藝流程圖
1)設備組成及工位劃分
①電芯供料;
②卷芯中心孔整形;
③負極耳焊接部分;
④正極耳整形;
⑤整形后位置精度保證在±3?以內(nèi);
⑥電池翻轉180°;
⑦鋼殼縮口;
⑧極耳定位與整形;
⑨T/I沖裁與插入;
⑩T/I檢查;
?極耳整理。
2)關鍵結構
如圖15所示的設備布局圖中可知,Tab焊接與縮口機設備中(-)Tab焊接與拉力檢查、縮口、中心Pin插入、T/I沖裁、T/I插入等比較關鍵,對整個裝配出來的產(chǎn)品有至關重要的作用,選取其中幾個機構做詳細的介紹說明。
圖15 關鍵結構設備布局
1—極組中心孔整理;2—視覺檢測(CCD);3—(-)Tab焊接與拉力檢查(焊接設定值:電流、電壓、壓力);4—縮口;5—中心Pin供應;6—中心Pin插入;7—(+)Tab定位;8—T/I沖裁;9—T/I插入
①負極Tab焊接機構。負極Tab焊接機構構成如圖16所示,該機構主要完成負極處Tab與鋼殼的焊接工序,完成之后同時進行拉伸檢測,確定焊接后的強度能夠滿足要求。
圖16 負極Tab焊接機構構成
②縮口機構。縮口機構構成如圖17所示,該機構主要完成對卷芯的外殼即鋼殼的縮口工序,縮小卷芯上部的鋼殼外徑,這對于電池的封裝是個初步過程,為后續(xù)圓柱電池的封口做好鋪墊。
圖17 縮口機構構成
③Pin插入機構。Pin插入機構構成如圖18所示,該機構主要完成將中心銷(Pin)插入收口成型的卷芯內(nèi)徑中,包括Pin的供料、Pin的插入以及Pin高度檢查等,工序完成的同時也完成了對Pin插入的檢測,保證了工序的準確性以及完整度。
圖18 Pin插入機構構成
1—升降機械手;2—氣動手指與夾具;3—高度檢測;4—載具與輸送;5—二次定位
④T/I插入機構。T/I插入機構構成如圖19所示,該機構主要完成對正極Tab的定位、頂部絕緣片(T/I)插入電池內(nèi)部等工序,同時在動作完成以后對T/I插入進行檢測,保障工序完成的準確性和完整度。
圖19 T/I插入機構構成
1—升降機構;2—90°旋轉;3—真空吸頭;4—載具與輸送
2.4 輥槽機及短路測試機
輥槽機及短路測試機(圖20)是對前面加工好的半成品電池進行加工,即對電池的鋼殼實施槽口加工進而滾壓,并對電池內(nèi)部進行短路測試。輥槽機由上料輸送帶、上料分料盤、輥槽機構、下料分料盤、下料傳送帶等部件和除塵機構與Hi-pot檢測裝置共同組成。輥槽通過采用橫向進刀、上下同時壓縮補給、背輪支撐的結構方式來實現(xiàn)鋼殼槽口的成型。
圖20 輥槽及短路測試設備
具體工藝流程如下:電池投入后將托杯與電池分離,通過上下部的凸輪曲線運動,分別在電池長度方向進行機械壓縮,利用滾刀在鋼殼口部實施槽口的加工;對已完成輥槽工藝的電池進行尺寸檢查(輥槽部位的外徑、高度)與短路測試等。
關鍵結構:輥槽機及短路測試機設備布局如圖21所示;其工藝流程如圖22所示。
圖21 輥槽機及短路測試機設備布局
1—電池投入;2—電池與托杯分離;3—輥槽(6個沖裁頭);4—電池與托杯結合;5—T/I檢查;6—外徑檢測及高度檢測;7—短路檢測;8—X射線(電池排出);9—NG排出
圖22 輥槽機及短路測試設備的工藝流程
從圖20的設備布局圖中可知,輥槽、短路測試設備中輥槽機構、T/I檢查機構、短路檢測機構等是關鍵機構,對整個裝配出來的產(chǎn)品有至關重要的作用,選取其中幾個機構做詳細的介紹說明。
①輥槽機構。輥槽機構如圖23所示,該機構主要完成在電池的鋼殼上進行輥槽,中間會完成電池和托杯的分離與結合動作,鋼殼上部輥槽成型,目的是為了確保蓋帽放置位置。
圖23 輥槽機構
②短路測試機構。短路測試機構如圖24所示,該機構主要完成在(+)Tab定位后,檢測鋼殼與卷芯(+)Tab間的電阻,保證電池內(nèi)部的絕緣性,是電池裝配完成前的檢測工作。
圖24 短路測試機構
2.5 (+)Tab激光焊接機
(+)Tab激光焊接機(圖25)是圓柱電池裝配的后環(huán)節(jié),主要功能是將正極處的Tab與電池的蓋帽進行激光焊接,并做進一步檢測工序,后面詳細介紹各個機構的工作過程。
圖25 (+)Tab激光焊接機
將注液后的電池(+)Tab與蓋帽進行激光焊接的工序包括:(+)Tab清潔、定位、CCD檢測、激光焊接、焊接拉力測試、Tab彎折、蓋帽壓入等。
焊接設備結構布局如圖26所示,可以看出(+)Tab焊接機每個工位的具體工作內(nèi)容。其工藝流程如圖27所示。
圖26 焊接設備結構布局
1—電池供給;2—高度調(diào)整;3—Tab定位;4—DMC清洗(濕擦);5—擦洗(干擦);6—Tab定位(CCD);7—蓋帽供料;8—激光焊接;9—拉力檢測;10—焊接位置檢測(CCD);11—極耳彎折;12—頂蓋壓入;13—高度檢測;14—NG排出;15—隨行治具
圖27 激光焊接機工藝流程
從圖26的設備結構布局圖中可知,(+)Tab焊接機設備中激光焊接機構、拉力檢測機構、極耳彎折機構、頂蓋壓入機構等是關鍵機構,對整個裝配出來的產(chǎn)品有至關重要的作用,選取其中幾個機構做詳細的介紹說明。
①蓋帽激光焊接機構。蓋帽激光焊接機構如圖28所示,該機構主要完成(+)Tab的定位、激光焊接Tab和蓋帽、焊接強度檢測、將蓋帽插入中鋼殼中等工序,每個工序都很關鍵,為后續(xù)的封口環(huán)節(jié)打好基礎。
圖28 蓋帽激光焊接機構
②拉力測試機構。拉力測試機構如圖29所示,它由壓緊板、蓋帽夾持機構、上下運動機構、拉力傳感器、放大器等組成,用于檢查焊接拉力是否滿足強度要求。可根據(jù)要求自動設定檢測的頻次及拉力的大小,具有焊接拉力檢測范圍設置以及拉力異常報警停線功能。
圖29 拉力測試機構
2.6 封口機
封口機(圖30)是圓柱電池裝配的后環(huán)節(jié),是對成型電池外表面鋼殼進行包裝封口,對電池外觀的保護,使得電池內(nèi)部的氣密性更好,是圓柱電池裝配的重要環(huán)節(jié)。封口機用于蓋帽焊接后電池的口部密封。鋼殼經(jīng)封口1次或2次彎折整形作業(yè)后,蹲壓電池上部端面,使電池內(nèi)部保持密閉。
圖30 封口機
封口機設備主要工藝包括:DMC清洗、卷邊1、DMC清洗、卷邊2、蹲封等。其詳細的工藝流程如圖31所示。
圖31 封口機設備工藝流程
封口機設備的整體布局如圖32所示,可以清晰看到設備從電池供給到封口、檢測完排出的加工整個過程。
圖32 封口機設備的整體布局
1—托杯與電池供給;2—DMC涂抹;3—卷邊;4—DMC涂抹;5—卷邊;6—排出;7—托杯與電池供給;8—托杯與電池分離;9—空托杯回流;10—DMC涂抹;11—蹲封;12—高度檢查;13—外形檢查;14—NG排出;15—電池排出
從圖32中可知,封口機設備中的卷邊機構、蹲封機構、外形檢測機構等是關鍵機構,對整個裝配出來的產(chǎn)品有至關重要的作用,選取其中卷邊蹲封機構做詳細的介紹說明。其結構示意圖以及工藝流程如圖33與圖34所示。
圖33 卷邊、蹲封結構示意圖
圖34 卷邊、蹲封工藝流程
封口機通過3爪與封口模具對電池進行1次、2次的卷邊封口,然后利用上模具對電池表面進行蹲封工藝,目的是為了電池高度保持一致。
?
圓柱型電芯Pack系統(tǒng)智能制造
Pack的意思就是包裝,電池pack指的就是組合電池,也就是動力電池的包裝、封裝或者裝配過程。我們都知道動力電池內(nèi)部包括電解液、隔膜、正/負極材料等,這些東西組合在一起成了電芯;而多個單獨的電芯通過特定的方式進行包裝成組最后就形成了我們的動力電池,動力電池加上電池管理系統(tǒng)、電氣和機械系統(tǒng)等就能夠變成電動汽車的能量來源,而這整個過程所用到的就是電池pack。
電池包(pack):一般是由多個電池組集合而成的,同時,還加入了電池管理系統(tǒng)(BMS)等,也就是電池廠最后提供給用戶的產(chǎn)品。
今天以某產(chǎn)品為例講講電池pack系統(tǒng),該產(chǎn)品主要應用于物流車和乘用車。
Pack產(chǎn)品信息
圖1 產(chǎn)品裝配圖
使用18650或21700電芯計算,模塊長度最大為360mm×430mm×75.5mm。
工藝方案選擇
根據(jù)對產(chǎn)品市場導向及市場需求的分析,該項目目標產(chǎn)品LR2170型電芯電池包生產(chǎn)擬采用插接式工藝路線,產(chǎn)品主要應用于物流車和乘用車。
電芯單層陣列組成的模塊,層層疊加組成模組,幾個模組安裝在電池箱里并進行連接,增加管理系統(tǒng),最終形成電池包。可以根據(jù)客戶的需求,變更陣列樣式、層數(shù)、模組串聯(lián)數(shù)量等設計,以便生產(chǎn)出各種形狀和性能參數(shù)的電池包產(chǎn)品。
目前主流的工藝為插接式、電阻焊和鋁絲焊,詳細對比見表1。插接式結構簡單,成本低,安全性能好。
表1 三種工藝方案優(yōu)缺點比較
該項目采用高自動化插接式生產(chǎn)技術,與行業(yè)內(nèi)成熟自動化設備供應商共同優(yōu)化設計,形成了目前的高自動化生產(chǎn)技術。采用插接式模組工藝,可根據(jù)客戶要求,組裝成各種形狀的電池包,型號開發(fā)難度小。采用插接式模組工藝,激光焊無耗材,易維護,成本低。
Pack工藝流程
該項目的汽車動力電池包生產(chǎn)工藝主要由模組生產(chǎn)、電池包生產(chǎn)和容量檢驗三個工段組成。項目針對裝配工藝特點,采用全自動和半自動結合的工藝流程,提高生產(chǎn)效率,降低人力成本。采用自動化插接式模組工藝和半自動電池包工藝,此工藝路線在電池包產(chǎn)品性能和可制造性方面均進行了全面的考慮。
該項目工藝流程以智能制造為設計原則,采用MES管理生產(chǎn)計劃;對班組信息、設備信息、原材料批次信息、生產(chǎn)過程數(shù)據(jù)和質(zhì)量檢測數(shù)據(jù)進行全面的自動采集和匯總分析,實時監(jiān)控生產(chǎn)狀態(tài)和質(zhì)量狀態(tài);可根據(jù)原材料批次信息追溯產(chǎn)品信息,以及通過產(chǎn)品批次信息追溯原材料信息和生產(chǎn)過程信息。
3.1 全自動模組裝配
電芯車間生產(chǎn)電芯分檔后存放于定制料盒中,然后按檔次和批次存放在電芯成品倉庫里,AGV系統(tǒng)根據(jù)MES中生產(chǎn)計劃自動轉運電芯至全自動模組上料區(qū)。
上料區(qū)電芯由工業(yè)機器人上料至自動流水線。電芯經(jīng)過掃碼分選單元,記錄電芯批次、復測電壓和內(nèi)阻;合格電芯經(jīng)過PET膜去除單元,去除負極底部PET膜;經(jīng)等離子體清洗單元,去除電池蓋和電池殼底部表面污漬;進入支架單元,電芯按照一定陣列形式插入支架;經(jīng)激光打碼單元,根據(jù)MES設定在支架上標記打碼,并與電芯信息進行綁定;經(jīng)彈片激光焊接單元,將支架中的彈片與電芯正極進行焊接;經(jīng)并連片上料安裝單元,將并連片安裝在支架上;經(jīng)并連片激光焊接單元,將并連片與彈片進行焊接。至此,模組的子單元模塊全部完成,插接式最上層模塊與中間層模塊的支架和焊接參數(shù)略有區(qū)別,通過設定自動線參數(shù),可實現(xiàn)兩種模塊按照設定比例交替生產(chǎn)。
1個負極支架,若干個中間模塊,1個正極模塊在插接組裝單元層層摞起來并擠壓,串聯(lián)為一個初步的模組;經(jīng)極柱安裝工位,分別在模組正負極匯流板安裝極柱;經(jīng)固定板安裝工位,在匯流板上安裝固定板;經(jīng)加熱帶安裝工位,在模組電芯間隙插入加熱帶;在PCB板安裝工位,安裝PCB板和溫度電壓采集線束;在模組打包工位,對模組進行固定;在EOL檢測工序,檢測成品模組的電阻和電壓等參數(shù)。具體工藝流程如圖2所示。
圖2 全自動模組裝配工藝流程
3.2 半自動電池包的裝配
AGV系統(tǒng)根據(jù)MES中生產(chǎn)計劃將原材料自動轉運至上料區(qū),在上料單元,線體定制AGV將電池箱托起,依次經(jīng)過各道工序;在清潔工位,采用吸塵器對電池箱進行異物清潔;在高壓線纜和組件安裝工位,將高壓線纜和組件安裝到電池箱相應位置;在BMC和LMC組裝工序,將BMC和LMC安裝到電池箱相應位置;在入箱和固定工位,工人在自動提升系統(tǒng)協(xié)助下將模組安裝到合適位置;在線束安裝與整理工位,安裝相應線束并整理,在半成品檢測工序,進行Pulse充放電等檢查項目,檢驗裝備的正確性;在封箱工序,涂膠并安裝上蓋板;在成品檢驗工序,檢驗絕緣性和氣密性。
本線體中所有螺釘?shù)难b配力矩都有明確的規(guī)定,通過自動或半自動擰緊裝置進行轉配。半自動電池包裝配工藝流程如圖3所示。
圖3 半自動電池包裝配工藝流程
3.3 容量檢測
AGV系統(tǒng)根據(jù)MES中生產(chǎn)計劃將半成品區(qū)的待測電池包轉運至測試區(qū),人工接線后,測試系統(tǒng)自動檢測電池包容量并上傳數(shù)據(jù)至MES,測試完成后打包入庫。容量檢測工藝流程如圖4所示。
圖4 容量檢測工藝流程
Pack生產(chǎn)制造
Pack生產(chǎn)制造流程:中間支架組裝→電芯上料→電芯篩選(OCV/IR測試)→PET膜去除→等離子清洗→電芯檢驗→電芯入中間支架→焊接→匯流排組裝焊接(正/負極支架組合焊接)→焊點檢查→模組及端板綁定→模組轉接端子組裝→PCB板采集線束和加熱片安裝→模塊檢驗→模組下線流轉。
Pack線從電芯上料至模組裝配的工序流程如圖5所示。
圖5 Pack線從電芯上料至模組裝配的工序流程
4.1 產(chǎn)線布局
Pack產(chǎn)線設備布局如圖6所示。
圖6 Pack產(chǎn)線設備布局
4.2 電芯上料
1)功能:電芯上料的主要功能為從紙盒或標準托盤中取出電芯到自動線。
2)工藝技術:
①托盤用標準出貨紙盒取出,設備自動將電芯從紙盒中取出上線。
②掃描電芯上的條形碼(條形碼位于電芯的側面),和電芯來料數(shù)據(jù)比對。
3)電芯上料設備:電芯上料設備如圖7所示。AGV小車將滿電池盒的托盤運送至上料位,CCD相機拍照定位,距離傳感器檢測高度,夾爪進行抓取操作并將托盤放置在倍速鏈輸送線上。料盒抓取完后,AGV小車將空托盤運送至電芯堆放區(qū)。
圖7 電芯上料設備
電芯上料設備的特點如下:
①AGV小車整托盤上料,節(jié)約上料時間。
②相機定位,四軸調(diào)整,保證抓取動作既準確又穩(wěn)定。
③夾爪具有防撞功能,保證電芯、料盒的安全。
4)上料過程:電芯上料如圖8所示,料盒通過上層輸送線運送至電芯抓取工位進行定位,夾爪將料盒抓取至線體兩側,對料盒進行90°翻轉,電芯抓取機構將電芯抽取至電芯輸送線上,導向機構下降并對電芯進行輸送。空箱通過升降機運送至下層倍速鏈,運送至堆疊工位,可堆疊4跺,滿料后將提示人工取走。
圖8 電芯上料
電芯上料過程的特點如下:
1)空箱回流后進行堆疊,滿料后將產(chǎn)生報警提示,減少人工的操作時間。
2)抓取料采用雙工位,做到故障不停機。
3)抓取后輸送導向機構保證了電芯搬運的穩(wěn)定高效。
4.3 電芯檢測
電芯檢測如圖9所示。上料夾爪從輸送線上一次抓取12只電芯,變間距后放置在步進托板上,并由其將電芯運送至掃碼工位,滾輪帶動電芯旋轉,CCD相機自動抓取電芯上的條碼信息,并上傳至MES。在OCV/IR測試工位,壓板將電芯壓緊,探針同時對12顆電芯進行測試,并將測試信息上傳至MES。下料機械手根據(jù)掃碼及測試情況將電芯放置到OK輸送線或NG工位。
圖9 電芯檢測
電芯檢測的特點如下:
1)采用專利技術,對多組電芯條碼進行滾動掃描,高效且穩(wěn)定。
2)采用專用同軸高頻探針,保證電芯測量的精度和分選的準確率,且更換也比較方便。
3)將NG電芯按照掃碼不良、測試不良、壓降過大及批次不符等情況,進行分類存儲,以便于質(zhì)量追溯。
4.4 電芯篩選(OCV/IR測試)
1)功能:
①測試每只電芯的OCV和ACIR,并將測試數(shù)據(jù)和電芯數(shù)據(jù)綁定后上傳至MES。在聯(lián)機狀態(tài)下,由MES判斷電芯是否合格;在單機狀態(tài)下,數(shù)據(jù)存取在本地;聯(lián)機時,自動上傳至MES。
②將測試合格的電芯流入下一道工序,不合格的電芯單獨流出,并及時提醒員工取出。
2)工藝技術:
①電芯電壓為0~5000mV,分辨率為0.01mV,精度為±0.3mV,整體測試精度為±0.3mV。
②電芯內(nèi)阻為0~2mΩ,分辨率為0.01mΩ,精度為±0.02mΩ,整體測試精度為±0.04mΩ。
電芯內(nèi)阻為2~5mΩ,分辨率為0.01mΩ,儀表精度為±0.02mΩ,整體測試精度為±0.04mΩ。
③測試OCV和IR的標準使用MES中的數(shù)值,技術人員可以根據(jù)需要進行更改。
④針對給出的電芯型號與外形,電壓內(nèi)阻測試儀的測試夾具具有高精度、耐用(接觸探針的使用壽命不小于3000000次)、易于維護和易于換型等特點;由于電芯殼為鋁殼,表面可能會有氧化層,探針端面開齒槽能夠刺破電芯表面氧化層,防止誤判。
⑤軟件功能:具備權限管理功能、記錄功能、查詢功能、修改刪除功能、報表輸出功能、Excel導入與導出及提供數(shù)據(jù)庫外接口。
⑥在測試、分選過程中,電芯表面不得出現(xiàn)任何劃傷和磕碰等。
(5)電芯剝皮
1)功能:
①將電芯外表面的PET膜去除。
②去除電芯正極的絕緣片。
③檢測電芯外觀。
④檢測電芯入裝極性位置。
2)工藝技術:
①不能破壞電芯的涂層。
②電芯內(nèi)表面瞬間溫度不能超過80℃。
③對于外觀及極性位置不良的自動剔除,并提醒工作人員取走。
3)電芯剝皮操作:如圖10所示,步進線將12只電芯同時送到第一次激光切割位,上滾輪壓住電芯,下滾輪轉動,激光器進行環(huán)形切割;步進至第二次激光切割位,激光從環(huán)形至底部進行切割;電芯至剝皮工位用壓板壓住正極側,夾爪將電芯外皮剝離,并由壓縮空氣吹出料倉。
圖10 電芯剝皮
電芯剝皮的特點如下:
①可同時對多只電芯進行處理,生產(chǎn)效率比較高。
②用伺服系統(tǒng)控制電芯旋轉,可保證電芯外皮切割的完整性。
③分次對電芯表皮進行切割,保證了剝皮的可靠性。
4.6 電芯入工裝
如圖11所示,夾爪從輸送線上抓取電芯,分間距后放置在導向槽上。推板將電芯推入旋轉導向,旋轉導向翻轉90°并移動至入殼工位。電芯工裝通過機械手從倍速鏈輸送線上抓取至入殼工位,入殼氣缸將電芯壓入電芯工裝內(nèi)。裝滿電芯的工裝通過機械手抓取至倍速鏈輸送線上。
圖11 電芯入工裝
電芯入工裝的特點如下:
①進入工裝時有精確導向,保證電芯不會傾斜劃傷。
②多只電芯同時進氣入工裝,生產(chǎn)效率比較高。
4.7 等離子清洗
1)功能:對電芯表面進行等離子清洗。
2)工藝技術:清洗完成后,電芯表面去塵,無污物和雜質(zhì)。
3)等離子清洗的操作:如圖12所示,裝滿電芯的工裝通過倍速鏈輸送線運送至等離子清洗工位后進行定位,XY二軸機械手帶動等離子清洗頭對電芯正極表面進行清洗。
圖12 等離子清洗
等離子清洗的特點如下:
①等離子清洗路徑及時間可自由設定,保證清洗效果。
②電芯清洗完成后立即會將支架蓋上,避免再次污染。
4.8 電芯入中間塑料支架
1)功能:
①將中間塑料支架組合體(中間塑料支架、彈片和電壓采集彈片)上料。
②焊接彈片依次裝入到上支架內(nèi)。
③電芯按照模塊要求依次插入裝有彈片的上支架內(nèi),并擠壓保證電芯正極極柱和彈片接觸。
2)工藝技術:
①電芯插接到位,保證正極極柱和彈片完全接觸。
②若電芯位置和極性與要求不符,必須立刻報警提醒操作人員進行處理。
3)電芯安裝支架:如圖13所示,電池支架放置在料架里,人工將料架推入料倉。提升裝置將料倉一層層托起,搬運機構將電池支架推送至搬運位并加以定位。四軸機器人抓取電池支架,通過CCD相機定位后放置在裝滿電芯的工裝板上。電芯支架運送至激光打碼工位打碼,數(shù)據(jù)綁定并上傳至MES。
圖13 電芯安裝支架
電芯安裝支架的特點如下:
①支架料車每側兩臺,其中一臺備用,不影響生產(chǎn)。
②緩存槽可加以調(diào)節(jié),以適應不同規(guī)格的模塊。
③可緩存15min用量,料槽有缺料提前預警功能。
4.9 激光焊接
1)功能:
①使匯流排(中間塑料支架)完整地焊接到電芯的正極端(彈片與電芯焊接,彈片與連片焊接),并將數(shù)據(jù)上傳至MES。
②使匯流排(正極塑料支架)完整地焊接到電芯的正極端(彈片與電芯焊接,彈片與連片焊接),并將數(shù)據(jù)上傳至MES。
③使匯流排(負極塑料支架)組合與彈片激光焊接,并將數(shù)據(jù)上傳至MES。
④焊接后自動檢測焊點質(zhì)量是否合格。合格產(chǎn)品流入下一道工序,不合格產(chǎn)品單獨流出,并及時提醒工作人員取出。
2)工藝技術:
①不能焊穿匯流排及電芯的正極端。
②焊點強度(剝離力)應大于100N。
③能夠焊接鎳片、鋼片等。
④一個產(chǎn)品的焊接參數(shù)放在一個文件里(一個產(chǎn)品一個文件)包含設置參數(shù)、運動參數(shù)和坐標、原點或零點坐標、測距Spec、偏差Spec及焊點檢測對比參數(shù)等。切換產(chǎn)品時只需要選擇這個產(chǎn)品文件,不需要額外動作。
⑥產(chǎn)品信息上的輸入與輸出功能。
⑦界面有焊點布局圖,對Pass和Fail不同焊點有顏色顯示。
⑧可設置產(chǎn)品文件數(shù)據(jù)來源于本地還是服務器,服務器可設置和導入焊接參數(shù)。
⑨焊接工裝便于及時換型使用。
⑩對中途發(fā)生的異常作業(yè),操作人員可通過調(diào)整,繼續(xù)后續(xù)焊接。
? 配備自動焊點檢查功能。
3)激光焊接操作:如圖14所示,支架運送至第一焊接位置定位后進行彈片與電芯正極的焊接。人工將并連片放置在料盒里,規(guī)整氣缸進行規(guī)整,測距傳感器測量并連片厚度,上料機械手根據(jù)測量的厚度抓取并連片將其放置在支架上。支架在第二焊接工位定位后進行并連片與彈片的焊接,每顆電芯的焊接數(shù)據(jù)都會上傳至MES。
圖14 激光焊接
激光焊接的特點如下:
①料盒分別位于左右兩側,更換料時不需要停機。
②規(guī)整定位,測量厚度,抓取安全可靠。
③采用振鏡焊接方式,生產(chǎn)效率非常高。
4.10 模塊堆疊
如圖15所示,六軸機器人將負極支架、焊接模塊和正極支架依次堆疊至模塊堆疊位。電缸使用力矩模式將模塊壓緊,并記錄、判斷高度是否在允許范圍內(nèi),然后移動至人工工位進行焊點檢查。待往復運動至模組拼接完成后,六軸機器人將模組放置在出料工位上。
圖15 模塊堆疊
模塊堆疊的特點是:每層模塊都要壓緊并記錄高度數(shù)據(jù),以保證拼接的可靠性。
4.11 模組組裝及下線
如圖16所示,在模組加壓工位,人工裝上兩側的端板,設備自動將模組加壓至設定長度,自動記錄壓力值并判斷是否在安全值范圍內(nèi)。梯形絲杠有自鎖功能保證模組長度,人工在下一工位進行打包并安裝線束。對模塊進行絕緣測試及DCIR測試,人工進行附件的安裝。完成后由六軸機器人自動將模組搬運至AGV小車上,運送至指定地點。
圖16 模組組裝及下線
1)模組插接組裝
①功能:
a.在焊接好的Cellblock上安裝并聯(lián)匯流排。
b.按照7層模塊進行堆疊。
②工藝技術:每層模塊插接堆疊都必須擠壓到位,并記錄高度值。
2)采集線束安裝:
①功能:人工安裝PCB板采集線束和加熱帶。
②工藝技術:需要掃描檢測是否安裝零部件,若無自動報警提醒操作人員。
3)DCIR測試:
①功能:
a.按照測試流程進行測試,通過探針記錄每一串電芯的電壓。
b.記錄每一串電芯的直流阻抗。
c.測試完直流內(nèi)阻后需要將電芯SOC調(diào)成初始值或設定值。
計算的內(nèi)阻是SOC的函數(shù)來自脈沖功率測試數(shù)據(jù):脈沖放電10s后的放電內(nèi)阻;反饋脈沖10s后的反饋內(nèi)阻。
②工藝技術:
a.記錄每一串電芯的電壓,記錄間隔為0.1s。
b.對于不同模塊的測試工序需要容易更換,探針需定期更換。
c.對于測試意外停止的產(chǎn)品應記錄其充放電容量,并可以依據(jù)此記錄指導返工。
4)下料單元:
①功能:將制作好的模塊按順序下料到模塊流轉車中或AGV小車中。
②工藝技術:運轉模塊的周轉車廠家設計;下料時對物料車和電芯包掃描條碼,并將數(shù)據(jù)上傳到MES。
模組組裝及下線的特點是:模組組裝的同時記錄長度值及壓力值,保證模組組裝的可靠性。
4.12 彈片安裝(單機)
如圖17所示,彈性連接片通過振動盤上料,出料后通過磁性立柱將彈片吸起并插入到治具導向孔內(nèi)。治具移動至下一工位,CCD相機拍照并判斷彈片的角度,旋轉彈片導向孔至正確角度。夾爪將治具抓起并移動至電芯支架上方,壓桿將彈片壓入支架孔內(nèi)。治具通過步進線回流至彈片安裝工位,完成一個循環(huán)。
圖17 彈片安裝(單機)
彈片安裝的特點是:振動盤出料時彈片位置不穩(wěn)定,應先插入導向孔,再判斷角度,保證彈片安裝的準確性。
4.13 正極銅牌焊接(單機)
正極銅牌焊接(單機)如圖18所示。人工將正極銅牌和過渡片放置在料盒里,規(guī)整氣缸進行規(guī)整,測距傳感器測量厚度,上料機械手根據(jù)測量的厚度依次抓取正極銅牌和過渡片放置在工裝上。工裝移動至激光焊接位置后定位進行激光焊接。焊接完成后的銅牌通過機械手抓取至下料位置。
圖18 正極銅牌焊接(單機)
正極銅牌焊接的特點是:一臺正極銅牌焊接機可以同時滿足兩條生產(chǎn)線的生產(chǎn)需求。
4.14 Pack EOL測試
Pack EOL測試的主要功能及檢測基本內(nèi)容有:箱體漏電檢測、絕緣電阻檢測、耐壓檢測、BMS系統(tǒng)功耗、通信端口功能檢測、軟硬件版本確認、LMU數(shù)據(jù)采集功能、數(shù)據(jù)精度檢測、高壓端口電壓和極性檢測、充電功能檢測、其他I/O功能檢測、仿真信號輸入、報警信息確認、Pulse功能測試、國標直流內(nèi)阻測試、采樣數(shù)據(jù)分析、測試報告及數(shù)據(jù)MES存儲。Pack EOL測試工藝流程如圖19所示。
圖19 Pack EOL測試工藝流程
-
制造
+關注
關注
2文章
510瀏覽量
23990 -
電池
+關注
關注
84文章
10564瀏覽量
129515
發(fā)布評論請先 登錄
相關推薦
電池組PACK自動化生產(chǎn)線:新能源行業(yè)的創(chuàng)新力量
電池組PACK自動化生產(chǎn)線:驅動新能源產(chǎn)業(yè)的高效引擎
倍加福IO-Link方案在電池PACK生產(chǎn)線的應用
18650儲能電池組PACK生產(chǎn)線:高效、智能、可靠
革新鋰電池PACK線:重塑生產(chǎn)效能新高度
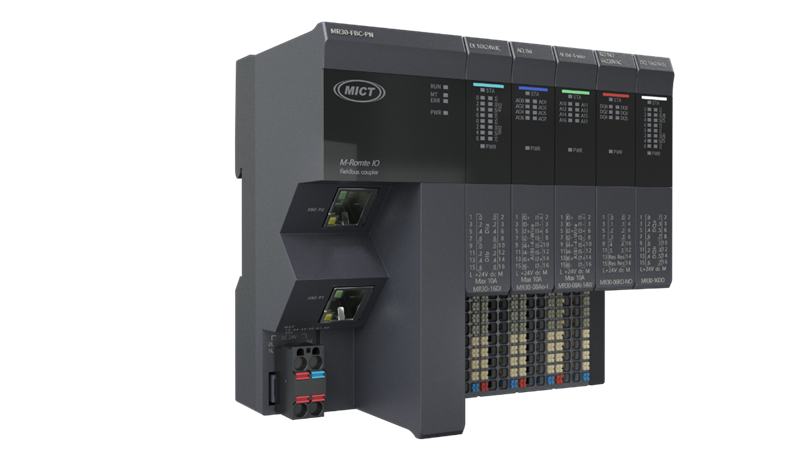
比斯特自動化:引領電池組PACK自動化生產(chǎn)線的創(chuàng)新與發(fā)展
深圳鋰電池Pack自動化生產(chǎn)線:高效、智能的制造新篇章
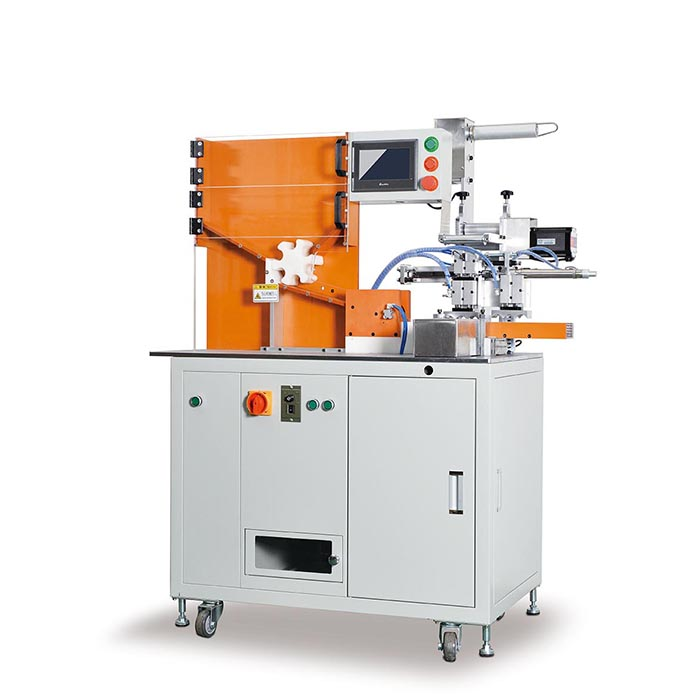
PACK電池包線束工廠|物料、生產(chǎn)、質(zhì)量、測試、設備等管理系統(tǒng)
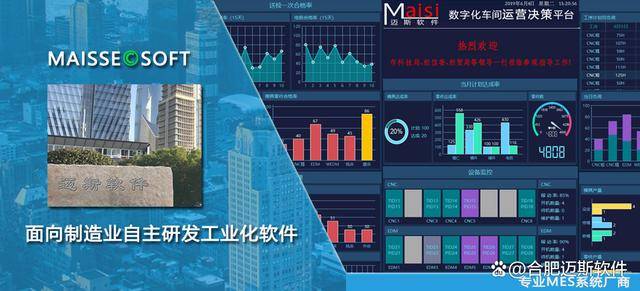
比斯特自動化|電池組PACK自動化生產(chǎn)線:引領能源存儲行業(yè)的新篇章
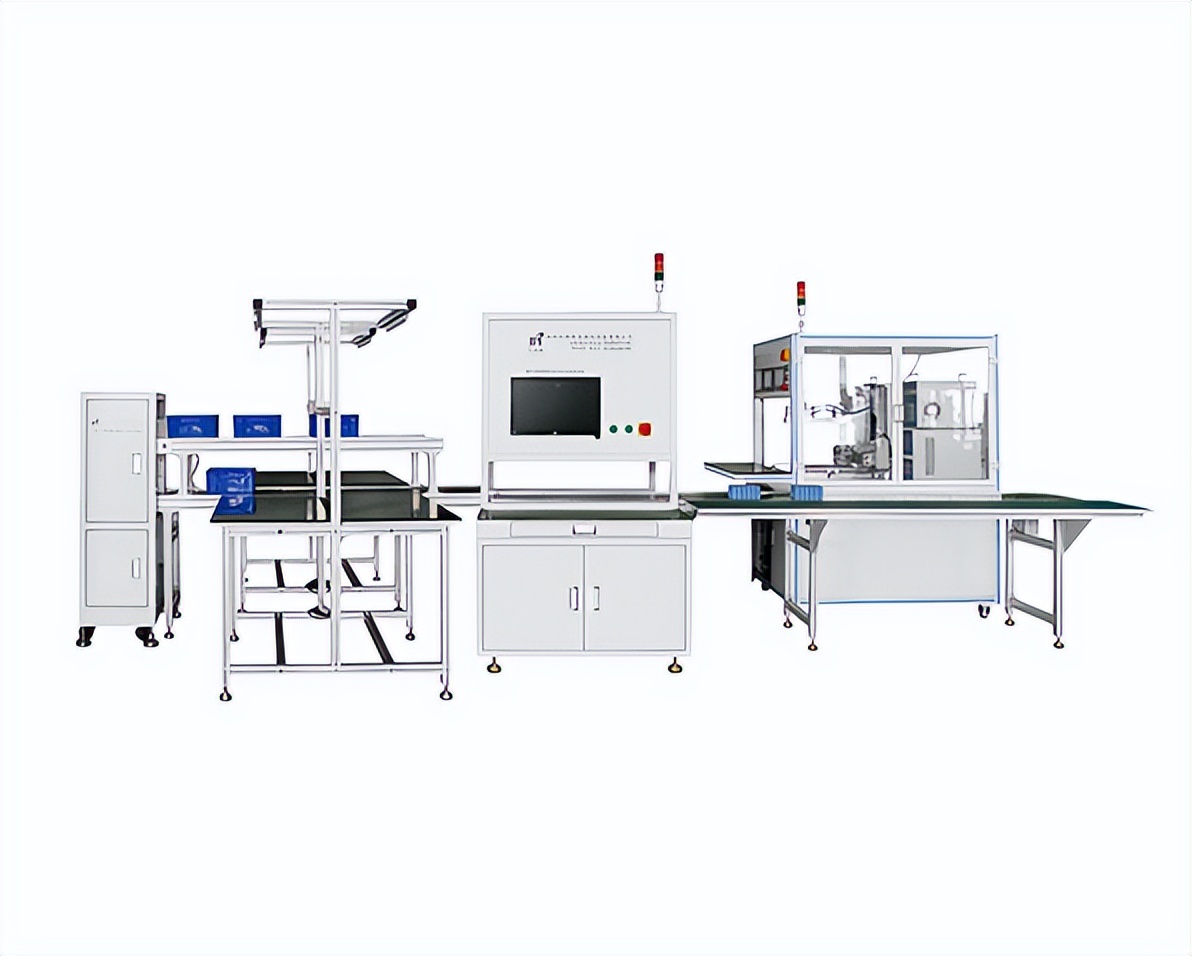
儲能電池組PACK生產(chǎn)線:驅動綠色能源未來的核心
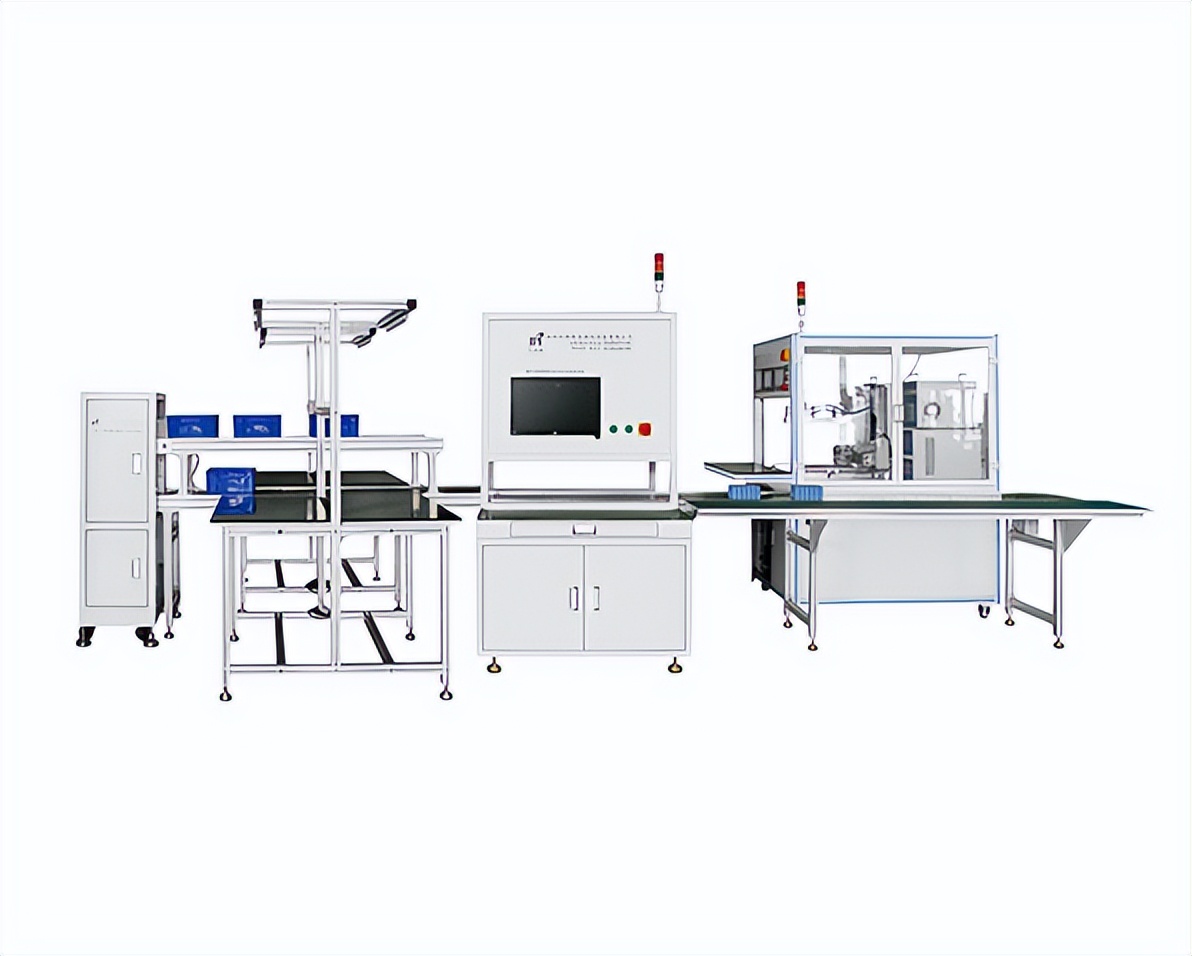
求助,關于cubemx升級和Pack升級問題求解
keil5.23加載pack,啟動軟件后,點擊pack installer會報錯的原因?
keil更改pack后時鐘錯亂的原因?
年產(chǎn)10GWh固態(tài)鋰電池及PACK制造生產(chǎn)項目簽約!
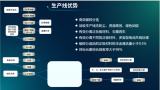
評論