豪華車型峰值功率在300KW以上,百公里加速5S左右,最高車速180Km/h左右;主流經濟車型峰值功率在100KW左右,百公里加速10S左右,最高車速150Km/h左右。
1、高功率密度
高功率密度可提高整車續航里程,需減小電驅傳動系統空間尺寸和重量;
反拖充電時反齒面載荷增加;高速旋轉下發生齒輪膠合失效的風險增加;
高轉速下,由于動態效應(共振)導致載荷增加的風險;
軸承和齒輪都很有可能需要更高的精度等級,但對應的就是更高的成本。
2、高轉速
新能源汽車驅動電機高速化,可以在保持體積重量不變時提高功率,進而提升汽車動力性;或者保持同樣功率和動力性,同時可以縮小電機體積,降低成本。
以BYD秦EV/120kW電機為例,轉速由14000rpm提升到20000rpm:體積減小24%、重量減小26.5%、成本降低26%。
高速電機存在的幾個問題:
(1)高速帶來的轉子離心力大,需要更高的轉子強度,可以通過低鐵損硅鋼片(降低厚度)和高強度硅鋼材料解決;
(2)高速軸承和高轉速油封的選擇、對動平衡要求更高,工藝裝配要求更高;
(3)高速帶來的鐵損增加和繞組渦流損耗、電頻率增大,電流位移和趨膚效應;
(4)激振頻率高,NVH惡化,需要在電磁設計、結構設計、電機控制等方面綜合考慮。
(5)控制方面,開關頻率增加,IGBT損耗增加,可以通過應用SiC、DSP升級和更新算法等方法解決;
(6)高轉速的標定測試臺架資源受限。
3、高效率
(1)提高電機效率:硅鋼片選型、繞線方法、永磁體布置方式;
(2)提高電控效率:IGBT選型、載波頻率;
(3)提高減速器效率:速比選擇、潤滑油選型及油量、軸承選型。
以速比匹配為例,需考慮多個工況進行選擇:
4、NVH性能
沒有內燃機噪聲掩蓋齒輪噪音,電動車對齒輪噪音容忍度更低;
電機本身會產生激勵導致噪音;
在反拖充電過程中,反齒面會完全受載;
潛在的齒輪嘯叫風險,這是在高轉速以及對應的頻率范圍內,輪齒嚙合頻率激勵所導致的;
高轉速導致高頻嘯叫,人耳朵對2-5kHz的聲音很敏感;
需對系統模態響應進行精細控制以避免共振。
5、EV兩擋優勢
以BYD秦EV為例,在原車120kW電機基礎上,匹配兩檔進行計算:
NEDC工況下,整車能耗可降低2.5%:
EUDC工況下,整車能耗可降低3.5%:
調節電機工作點,提高電驅動系統總效率。
6、EV兩擋技術方案
AMT構型:結構緊湊、性價比高:
AT構型:換擋品質高、無動力中斷:
無離合器、無同步器的電驅動機械變速器(EMT)構型——成本低、結構緊湊、維護方便
EMT系統的“無沖擊換檔”控制性能——消除“打齒”,延長使用壽命;消除換檔噪聲,改善舒適性;極短動力中斷時間,提升整車加速能力
責任編輯:彭菁
-
新能源汽車
+關注
關注
141文章
10530瀏覽量
99456 -
軸承
+關注
關注
4文章
2111瀏覽量
31162 -
驅動系統
+關注
關注
3文章
371瀏覽量
26935 -
系統技術
+關注
關注
0文章
6瀏覽量
6199
原文標題:電驅動系統技術發展趨勢和挑戰
文章出處:【微信號:EDC電驅未來,微信公眾號:EDC電驅未來】歡迎添加關注!文章轉載請注明出處。
發布評論請先 登錄
相關推薦
汽車電驅動系統技術未來發展趨勢及關鍵技術分析
電力驅動測試系統的技術原理和應用
電源管理技術的三大創新發展趨勢
軟件無線電關鍵技術有哪些發展新趨勢?
大功率IGBT驅動的技術特點及發展趨勢分析
新能源汽車電驅動系統關鍵技術創新發展趨勢
軟件無線電的歷史和發展趨勢講解
汽車電驅動系統技術未來發展趨勢及關鍵技術分析
新能源電驅動技術發展趨勢總結
電驅動系統集成包括哪些
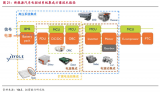
評論