在全球汽車電動化的浪潮下,汽車半導體領域的功率電子器件作為汽車電動化的核心部件,成為了車企和電機控制器Tire 1企業關注的熱點。車用功率模塊已從硅基IGBT為主的時代,開始逐步進入以碳化硅MOSFET為核心的發展階段。
為什么說碳化硅是車用功率模塊的未來?
碳化硅的禁帶寬度約為硅基材料的3倍,臨界擊穿場強約為硅基材料的10倍,熱導率約是硅基材料的3倍,電子飽和漂移速率約是硅基材料的2倍。碳化硅材料的耐高壓、耐高溫、高頻特性相較于硅基器件能應用于更嚴苛的工況,可顯著提高效率和功率密度,降低應用端的成本、體積和重量。
圖1 各類半導體材料性能對比
根據Yole數據,2021-2027年,全球碳化硅功率器件市場規模將由10.9億美元增長到62.97億美元,年復合增長率為34%;其中電動車用碳化硅市場規模將由6.85億美元增長到49.86億美元,年復合增長率更是高達39.2%,而電動車(逆變器+OBC+DC/DC轉換器)是碳化硅最大的下游應用,占比將由62.8%增長到79.2%,市場份額持續攀升。
圖2.Yole的市場分析
碳化硅在汽車行業的應用趨勢
電動汽車行業發展至今,行業最關心的是續航里程。影響續航里程的因素有很多,包括電池容量、車身重量、電力系統的電能轉化效率等。功率半導體是電能轉換的核心,碳化硅功率器件比硅基器件有低導通損耗、高開關頻率和高工作耐壓等優勢,能獲得更高的系統電能轉換效率,且在使得同等電量情況下,比使用硅基功率器件獲得更多的續航里程。因此電動汽車對于碳化硅功率器件的應用需求日益凸顯。
在電動汽車中,碳化硅功率器件的應用主要為兩個方向,一個用于電機驅動逆變器(電機控制器),另一個用于車載電源系統,主要包括:電源轉換系統(車載DC/DC)、車載充電系統(OBC)、車載空調系統(PTC和空壓機)等方面。
圖3.電動汽車中需要使用碳化硅器件的裝置
●電機控制器:影響續航里程
電動汽車整車系統中,動力電池的成本占比最高,約占整車成本的4-5成,在成本一定且電池技術路線確定的情況下,直接通過增加電池容量來提升續航里程的思路難以實現,在保證電池容量及技術路線不變的前提下,如何通過其他方法提升電能的轉化效率,降低電能損耗,實現續航里程的提升,一直是行業在探索的問題。
根據目前已知的行業數據,在電機控制器中用碳化硅MOS替換硅基IGBT后,會獲得電機控制器的效率的提升,NEDC工況下,對電池續航的貢獻提升在3%-8%之間,所以電控應用對碳化硅器件的需求最為迫切。同時,在國內新能源汽車市場大力推進適應高壓快充技術的高壓平臺上,硅基IGBT應對起來就非常吃力,取而代之的是碳化硅MOS。這更加確定了碳化硅功率器件在下一代電控系統中的核心和不可替代性地位。
近年來多家車企已開始全面采用碳化硅功率模塊,特斯拉的Model 3和Model Y、比亞迪的漢、蔚來的ET5和ET7、小鵬的G9和G6等車型相繼量產碳化硅電機控制器,整車的續航里程與加速性能都得到了顯著的提升。
圖4.特斯拉的逆變器
●車載輔助系統的碳化硅應用
碳化硅肖特基二極管、SiC MOSFET 器件則主要應用于車載OBC、DC/DC、空調系統,主要影響充電效率和輔助系統用電效率、開關頻率等。◎車載充電機(OBC)為電動汽車的高壓直流電池組提供了從基礎設施電網充電的關鍵功能,并決定了充電功率和效率的關鍵部件。電網中的交流電轉換為直流電對電池進行充電, 碳化硅二極管及MOSFET器件則可用于車載充電機PFC和DC-DC次級整流環節,推動車載充電機向雙向充放電、集成化、智能化、小型化、輕量化、高效率化等方向發展。◎電源轉換系統DC/DC 是轉變輸入電壓并有效輸出固定電壓的電壓轉換器,實現車內高壓電池和低壓電瓶之間的功率轉換,主要給車內低壓用電器供電,如動力轉向、水泵、車燈等。隨著整車智能化、電氣化的發展,對DCDC的供電功率及安全性提出了更高的要求。
◎車載空調系統中,在高壓平臺車型,因為快速充電所帶來的電池包的熱集聚,需要快速釋放。當前的技術是采用車載空調系統為電池包散熱,因此對于空壓機和PTC的頻率以及功率都有大幅提升的要求。而傳統的硅基IGBT和MOS器件已無法滿足,采用碳化硅MOS器件已勢不可擋。
車用碳化硅功率模塊的產業化落地與技術邏輯
當前,全球碳化硅產業格局呈現美、歐、日三足鼎立態勢,碳化硅材料七成以上來自美國公司,歐洲擁有完整的碳化硅襯底、外延、器件以及應用產業鏈,日本則在碳化硅芯片、模塊和應用開發方面占據領先優勢。中國目前已具備完整的碳化硅產業鏈,在材料制備和封測應用等部分環節具有國際競爭力。目前排名在前幾位均為國外公司,國內公司尚未形成一定市占率。
而在新能源汽車領域,由于我國汽車電動化走在全球最前列,本土市場拉動正在成為國產半導體企業崛起的有利因素。
現在,全球碳化硅企業都在積極開拓汽車市場,主要應用落地包括功率分立器件和功率模塊。其中,碳化硅芯片的優良特性,需要通過封裝與電路系統實現功率的高效、高可靠連接,才能得到完美展現。經過專業的設計和先進的封裝工藝制作出來的碳化硅MOSFET功率模塊,是目前電動汽車應用的主流趨勢。
目前新的設計SiC模塊的設計方向是結構緊湊更緊湊,通過采用雙面銀燒結和銅線鍵合技術,以及氮化硅高性能AMB陶瓷板、用于液冷型銅基PinFin板、多信號監控的感應端子(焊接、壓接兼容)設計,努力往低損耗、高阻斷電壓、低導通電阻、高電流密度、高可靠性等方向努力。通過好的設計和先進的工藝技術確保碳化硅MOSFET性能優勢在設備中得到最大程度發揮。
圖5.碳化硅MOSFET封裝要求
更小的元胞尺寸、更低的比導通阻、更低的開關損耗、更好的柵氧保護是碳化硅MOSFET技術的主要發展趨勢,體現在應用端上則是更好的性能和更高的可靠性。加之碳化硅器件的高功率密度、高結溫特性、高頻特性要求,也對現有封裝技術提出更高的要求,目前中國的功率模塊封裝創新主要朝著如下幾個方向在走:
●更先進的連接材料以及連接工藝,以承受更高的溫度變化
功率模塊中主要使用3種陶瓷覆銅板:AI2O3-DBC熱阻最高,但是制造成本最低;AlN-DBC熱阻最低,但韌性不好;Si3N4-AMB陶瓷材料熱阻居中,韌性極好,熱容參數也更出色,可靠性遠超AlN和AI2O3,使得模塊散熱能力、電流能力、功率密度均能大幅提升,非常適合汽車級的碳化硅模塊應用。
●更短的連接路徑以及更先進的連接技術,以降低雜感來適應器件高頻特性
銀燒結是目前碳化硅模塊領域最先進的焊接技術,可充分滿足汽車級功率模塊對高、低溫使用場景的嚴苛要求。相較于傳統錫焊技術,銀燒結可實現零空洞,低溫燒結高溫服役,焊接層厚度減少60-70%,適合高溫器件互連,電性能、熱性能均優于錫焊料,電導率提高5-6倍,熱導率提高3-4倍。很多企業已經嘗試將功率模塊內部中的所有傳統焊料升級迭代為銀燒結工藝,包括芯片,電阻,傳感器等。
為進一步提升模塊電性能及可靠性,嘗試的方向是采用DTS+TCB(Die Top System + Thick Cu Bonding)技術,在常溫條件下通過超聲焊接將粗銅線與AMB基板、及芯片表面的覆銅片進行鍵合連接,實現彼此間的電氣互聯。相較鋁線鍵合,模塊壽命可提升3倍以上,且電流和導熱能力可大幅提升。
●更集成的封裝結構設計以及電路拓撲,以進行更好的系統熱管理
為使模塊產品熱路徑設計更緊湊,促使逆變器系統集成設計更緊湊高效,進一步降低整體系統逆變器成本,通過封裝形式的改變,改善散熱性以及通流能力。采用多芯片并聯的內部結構,各并聯主回路和驅動回路參數基本一致,最大程度保證并聯芯片的均流性。模塊內部封裝有溫度傳感器(PTC),且PTC安裝在靠近芯片的模塊中心位置,得到了一個緊密的熱耦合,可方便精確地對模塊溫度進行測量。
國產車用碳化硅功率模塊的未來走向
當前,新能源汽車產銷兩旺,汽車半導體產業正在成為全球集成電路行業發展的重要動力。功率半導體將成為單車成本最高的半導體,也是國內企業現階段最有可能實現突破的汽車半導體領域,而碳化硅已毋庸置疑地成為了主要突破點。
大部分汽車企業已開始積極布局碳化硅上車應用,碳化硅功率半導體產業在中國乃至全球都處于爆發前夜,國內車用碳化硅功率的發展,需要車企、Tier1和碳化硅器件廠家的共同努力。從長期發展來看:◎建立行業的標準和規范:汽車企業需要聯合起來,探討并發布一些共性的要求來構建需求,形成共同的測試標準和技術規范,減少行業試錯成本; ◎建立健全產業支持政策:從上游到下游,行業應考慮如何建立一整套的支持和互信政策,推動上游材料、芯片到下游應用的打通; ◎加強產業及區域協同創新:從中國發展產業的邏輯來看,區域的集群是很重要的積極影響因素。從區域集群走出來的產業,可以逐步擴展到全國乃至全球范圍。這就需要地方上在區域經濟的規劃層面,進行更細致的政策支持和政企溝通;
◎引入適宜的金融服務:半導體產業周期長、投入重、測試水平嚴苛,需要有相應的金融政策和服務,來支持產業良性循環和發展,例如設立車用***保險項目等。
小結:隨著新能源汽車的發展,以及國內芯片行業的崛起,我國將會在以碳化硅為代表的第三代半導體領域有很大的作為,不管是技術投入還是投資方面都有很大的建樹,期待這個領域的長期發展。
-
新能源汽車
+關注
關注
141文章
10535瀏覽量
99482 -
功率模塊
+關注
關注
10文章
467瀏覽量
45108 -
碳化硅
+關注
關注
25文章
2762瀏覽量
49053
原文標題:中國車用碳化硅功率模塊的成長之路
文章出處:【微信號:QCDZSJ,微信公眾號:汽車電子設計】歡迎添加關注!文章轉載請注明出處。
發布評論請先 登錄
相關推薦
碳化硅SiC在電動車中的應用
碳化硅功率器件的工作原理和應用
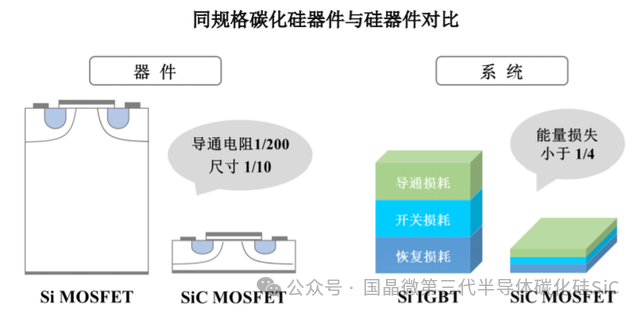
碳化硅功率器件的優勢和應用領域
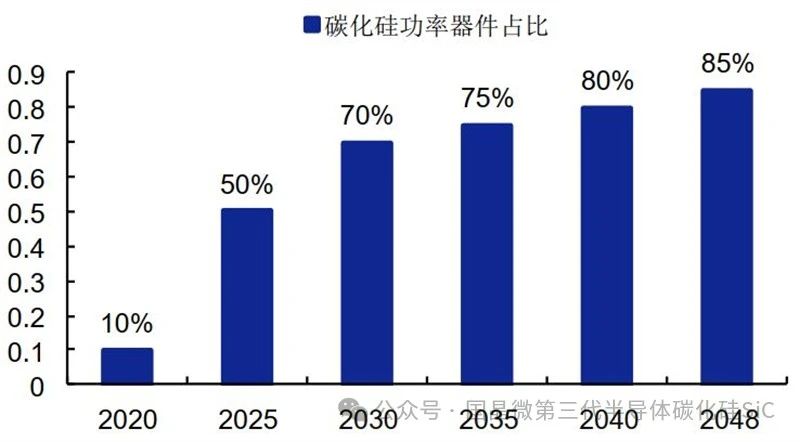
Wolfspeed推出創新碳化硅模塊
碳化硅功率器件的原理簡述
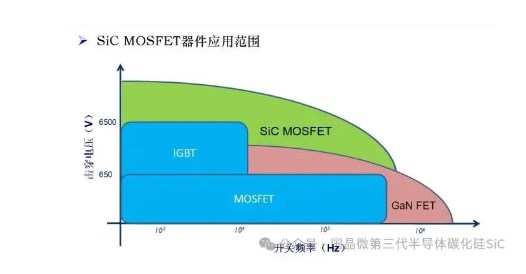
評論