目前汽車電子委員會 (AEC ) 發布的 AEC Q101《基于失效機理的汽車用分立器件應力試驗鑒定要求》已得到行業的廣泛認可和應用。通過汽車 AEC Q101 鑒定的分立器件,是目前可靠性最高的民用分立器件,其應用已逐步擴展到醫療、航空、航天等高可靠裝備中。國內對車規級分立器件質量保證要求研究不多,現有研究也主要側重鑒定考核項目。2021 年 3 月 AEC 發 布 了 AEC Q101E 版, 本 文 結 合AEC Q101E 版相對 D 版的修訂情況,從鑒定考核要求、鑒定擴展、關鍵檢驗項目試驗應力的確定原則以及局限性和應對策略 4 個方面對車規級分立器件的質量保證要求進行研究。
鑒定考核要求
汽車是一種預期壽命很長的制品,其工作時要承受高溫,高濕,低溫等嚴酷自然環境的考驗,氣溫變化快,振動劇烈,但是汽車對于關鍵組件(例如安全氣囊控制系統,剎車系統等等)可靠性要求很高,上述因素造成汽車廠商對于車規級分立器件可靠性要求很高,鑒定考核項目多,試驗應力惡劣。AEC Q101D 版將所有的鑒定考核項目都列在一個檢驗表中,缺乏條理性。此次修訂,AECQ101E 版將檢驗項目分為加速環境應力試驗、加速壽命試驗、封裝完整性試驗、芯片制造可靠性試驗和電性能驗證試驗 5 個群組,共包括 57 項檢驗。分立器件的封裝形式分為氣密封裝和非氣密封裝 ( 塑封 ) 兩種,目前民用產品的封裝以非氣密封裝為主,AEC Q101 規定的大部分檢驗也是針對塑封封裝器件制定的。
1.加速環境應力試驗
加速環境應力試驗主要是考核器件對高溫,高濕和溫度變化環境應力的抵抗能力,包括預處理和帶有偏置的強加速穩態濕熱試驗、不帶偏置強加速穩態濕熱試驗,溫度循環試驗以及功率循環試驗等,其具體項目及要求如表1所示。該分組每項試驗的樣品需從3個非連續生產批中抽取,每批抽取77只器件,不允許出現任何失效。
AEC Q101 規定的加速環境應力試驗主要考核器件耐環境應力的能力。
(1) 預處理的對象只是表面裝設的分立器件。表面安裝裝置引出端離本體很近,在焊接過程中會承受很大的熱應力,若裝置的材質吸收了潮氣就會造成爆米花。對模擬器件安裝過程中所受熱應力進行預處理,其主要步驟有電測試,外部目檢,溫度循環測試(5次),烘焙測試,吸潮測試,模擬回流焊測試(3次)以及終點電測試。實施三次回流焊,即模擬器件雙面安裝,一次性返工。
(2) 帶偏置的強加速穩態濕熱試驗是通過施加嚴酷的溫度、濕度和偏置條件加速潮氣穿透外部保護材料 ( 塑封料 )。GB/T 4937.4-2012《半導體器件 機械和氣候試驗方法 第 4 部分 :強加速穩態濕熱試驗 (HAST)》 規 定“130 ℃,96 h 的 HAST 試 驗 產 生的失效機理與相對濕度 85%,85 ℃,1 000 h 的高溫高濕反偏 (H3TRB) 試驗相同”。HAST 試驗使用了超出正常使用條件的環境應力,加速系數較大,可能誘發正常條件下不會發生的失效。AEC Q101 規定HAST 試驗的電壓不超過 42 V,H3TRB 試驗的電壓不超過 100 V,主要原因是試驗時濕度較高,較高的電壓容易導致試驗箱內產生電火花。隨著試驗設備的進步以及碳化硅等高壓器件對施加較高偏置電壓的需求,今后器件承制方需要根據實際情況提高試驗時施加的偏置電壓。
(3) 溫度循環試驗模擬溫度劇烈變化對器件的影響,考核器件承受由于不同材料熱膨脹系數的差異而產生的內部剪切應力的能力。AEC Q101 規定試驗最低溫度為 -55 ℃,最高溫度為器件的最高結溫,循環次數為 1 000 次,遠遠嚴于普通民用產品。例如,GB/T 12560:1999《半導體器件 分立器件分規范》規定的循環次數為 500 次循環。AEC Q101E 規定試驗后可以選擇 :進行 125 ℃下全部電參數的測試之后進行開封并選取 5 只器件進行鍵合強度測試,或者進行超聲掃描,如果出現分層,則選取分層最嚴重的 5只器件進行開封并進行鍵合強度試驗,如果通過鍵合強度試驗,則器件通過該分組試驗。
(4) 間歇式工作壽命試驗通過間歇式給器件加電/停電來達到改變器件溫度、考核器件結構及材料承受因溫度改變而引起內部剪切應力能力的目的。相對于溫度循環,間歇工作壽命通過設備本身發熱來達到改變溫度的目的,在測試過程中設備內部會出現溫度梯度現象,對于設備的評價更加苛刻。
間歇工作壽命試驗中存在2個關鍵考核條件——加電/停電所達到結溫或殼溫,以及加電/停電周期次數。對于傳統的金屬陶瓷封裝,容易判斷殼溫的變化,因此一般規定殼溫的變化量。對塑封分立器件而言,許多封裝形式都難以監控殼溫變化量,因為塑料是一種不良的熱導體。因此 AEC Q101 規定通過監測結溫的變化控制加電和斷電,并給出了結溫變化 100 ℃和 125 ℃兩個條件。
對于循環次數,AEC Q101D 版和 AEC Q101E 版規定需要進行的循環次數,同時又提供了計算循環次數的公式。以結溫溫升 100 ℃條件下的循環次數為例,循環次數為 15 000 次,計算公式為 60 000/(x+y),x、y 為實現結溫變化所需最短加電和斷電時間。以加電 2 min,斷電 4 min 為例,循環次數為 60 000/(2+4)=10 000 次循環。調查發現,AEC Q101C 版是根據封裝體積確定循環次數要求的 :小體積器件 ( 例如 TO-220 封裝 )加電和斷電時間分別為 2 min,需要 15 000 次循環 ;中等體積器件 ( 例如 TO-3、TO-247 封裝 ) 加電和斷電時間分別為 3.5 min,需要 8 572 次循環 ;大體積器件加電和斷電時間分別為 5 min,需要 6 000 次循環 ;無引線器件需要按照 60 000/(x+y) 進行計算,最多不超過 15 000 次循環。由于封裝形式越來越多,不易區分,因此 AEC Q101D 版和 AEC Q101E 版對以上原則進行了簡化,這也導致部分內容不易理解。
2 加速壽命試驗
加速壽命試驗就是用加電方法來加速器件劣化,以評定器件壽命能否達到規定要求,具體步驟及要求如表2所示。AEC Q101E版本指定加速壽命試驗由高溫反偏與高溫柵偏2組組成,每組試驗時間為1000 h,閘流晶體管的高溫反偏用交流阻斷試驗代替,齊納二極管的高溫反偏用穩態工作試驗代替。高溫柵偏只對場效應晶體管有效。該分組每項試驗的樣品需從3個非連續生產批中抽取,每批抽取77只器件,不允許出現任何失效。
3 封裝完整性試驗
AEC Q101E 版規定的封裝完整性試驗主要考核器件的機械特性,包括對鍵合工藝、芯片粘接工藝、耐受焊接時熱量的能力、耐機械應力的考核,具體項目和要求見表 3。其中,恒定加速度、掃頻振動、機械沖擊和密封試驗僅適用于氣密封裝器件,且需要串序進行。該分組的樣品從 1 個生產批中抽取。
4 芯片制造可靠性試驗
這種分組試驗在MOSFET,IGBT中都有應用,其具體內容就是通過考察柵極上氧化層的絕緣完整性來評價芯片制造過程對器件可靠性產生的影響。在芯片制造工藝改變之前和之后,都要做這個測試。
5 電特性驗證
電特性驗證主要是為了檢驗器件電特性能否達到規定要求,其具體條目及要求如表4所示。普通民用器件只需檢定常溫電參數指標,AEC Q101中規定需檢定器件高溫,常溫及低溫電參數指標全部合格。非嵌位感性負載開關試驗評估了MOS與IGBT在系統應用過程中遇到極端電熱應力時的容量,通過該試驗,可以獲得MOS器件對能量的耐受容量。
6 銅絲鍵合器件的鑒定
隨著銅絲鍵合生產工藝的不斷進步,銅絲鍵合器件市場占有率越來越大,但銅絲鍵合可靠性水平和金絲鍵合器件仍有一定差距。銅絲鍵合也有如下2個方面:第一,銅絲易氧化,影響鍵合質量;二是銅絲的硬度和屈服強度比金絲的高,鍵合時需要更高的超聲功率與鍵合壓力,容易損傷芯片。此次修訂,AEC Q101E 版增加了對采用銅鍵合絲的器件的考核要求,檢驗項目為溫度循環、HAST、間歇工作壽命試驗和高溫反偏,提高了試驗的應力,并增加了試驗強度和試驗前、后的檢驗和分析項目。
7 失效判定
電子元器件在進行各項試驗 ( 特別是壽命試驗 )后,電參數一般會出現一定的漂移。電參數變化率的多少反映了產品一致性的好壞,可以從一定程度上反映產品長期可靠性。汽車的最低設計壽命為 15年,因此,對電子元器件可靠性有較高的要求,不允許產品試驗后電參數出現較大變化。AEC Q101 規定試驗后電參數 ( 漏電流除外 ) 除應符合產品規范要求外,其變化量不得超過 ±20%。
AEC Q101E 版新增以下規定 :
● 對于導通電阻 (RDS(on)) 小于等于 2.5 mΩ 的器件,間歇工作壽命、功率溫度循環和溫度循環試驗后允許導通電阻變化量不超過 0.5 mΩ ;
● 潮濕相關試驗后漏電流的測量值不得超過初始值的 10 倍,其他試驗后的測量值不得超過初始值的 5 倍。
8 其他說明事項
分立器件廠商的產品要進入車輛領域,打入一級汽車電子大廠的供應鏈,必須符合兩個條件,一是產品通過 AEC-Q101 要求的鑒定考核,二是質量管理體系通過 IATF16949《汽車質量管理體系標準》認證。AEC Q101 規定,器件成功通過本標準所規定的所有測試,即可以聲明本產品已通過AEC Q101認證。由于汽車電子委員會沒有對產品進行認證服務,所以目前市面上還沒有通過鑒定的車規級元器件。
鑒定擴展
AEC Q101 規定的鑒定考核項目多、應力高,因此試驗費用高、周期長。對每種型號的器件都進行鑒定考核既耗時又費力,會極大地增加最終產品的成本。為了降低產品鑒定考核的成本,AEC Q101 規定可以將結構相似的產品列入同一族系,利用族系中已鑒定合格產品的鑒定考核數據,將鑒定合格資質擴展到族系中其他器件。
1 鑒定擴展原則
實施鑒定擴展應符合以下原則 :
(1) 對于沒有相似產品的試驗數據的新器件,按檢驗表的項目和抽樣方案進行檢驗 ;
(2) 對族系內現有代表性產品經鑒定考核合格的其他設備,若設備復雜程度比通過鑒定合格的產品低,則該類設備只需做靜電放電敏感度試驗及電參數驗證即可;
(3) 對于有部分試驗數據的器件,根據具體情況確定需要進行的檢驗項目 ;
(4) 對于工藝過程進行變更的器件,按規范的要求補充相應的檢驗。
2 列入同一族系的原則
AEC Q101 從晶圓制造和組裝工藝兩個方面給出了列入統一族系的標準。
晶圓制造中,被納入同一族系中的產品應是同一家晶圓制造廠所制造的與晶圓制造工藝一致的設備門類。AEC Q101把器件分為功率場效應晶體管、小信號場效應晶體管、功率雙極型晶體管、小信號雙極型晶體管、IGBT、整流二極管和其他器件類型、同族系器件須屬一類。AEC Q101對晶圓制造工藝進行了分解,包括制造流程,芯片版圖設計說明,單元密度,掩膜個數,光刻工藝,摻雜工藝等、鈍化/玻璃化材料與厚度,氧化工藝與氧化層厚度,芯片前金屬化與后金屬化材料,厚度與層數等等10個方面,同一種族系的設備其晶圓制造工藝也必須是一樣的。在組裝工藝上,納入同一支族的產品應是在同一家組裝廠制造出封裝形式接近、組裝工藝類似的設備。
由于分立器件封裝形式眾多,AEC Q101 未能給出屬于同一門類器件的具體封裝形式。AEC Q101 將組裝工藝細分為引線框架材料、引線框架鍍覆、芯片安裝材料和安裝方式、鍵合絲材料、直徑和鍵合方式、塑封料等 6 個方面,同一族系的器件其組裝工藝必須相同。
關鍵檢驗項目試驗應力的確定原則
AEC Q101 規定的溫度循環試驗、間歇工作壽命試驗、高溫高濕反偏試驗等關鍵檢驗的試驗應力是依據汽車電子的典型任務剖面確定的。
AEC Q101D 給出了汽車電子需要滿足的典型的任務剖面 :
● 15 年的使用壽命 ;
● 發動機工作時間 12 000 h ;
● 發動機待機時間 3 000 h ;
● 不工作時間 116 400 h ;
● 600 000 km 里程 ;
● 發動機啟動次數 54 750 次。
AEC Q101E 版省略了以上具體信息,而是規定需要根據任務剖面 ( 使用壽命、發動機工作時間、發動機待機時間、不工作時間和發動機啟動次數 )確定具體的試驗條件。這是由于新能源汽車的工作模式和燃油車有很大不同,因此需要根據具體情況確定試驗條件。但是,省略典型任務剖面信息會對理解 AEC Q101E 版給出的關鍵考核應力的計算過程帶來困惑。
伴隨著自動駕駛,新能源汽車等技術的進步,整機廠商對于汽車電子提出了越來越高的需求。在汽車電子應用中,任務剖面會對環境適應性,服役時間較長和失效率等提出更為苛刻的需求。新技術、新材料(例如銅絲鍵合技術和碳化硅材料等)的使用可能會引起器件失效機理的變化,用戶需根據特定任務剖面來決定檢驗項目試驗應力。
為此,AEC Q101E版附錄7提供了以器件應用任務剖面為依據來判定檢驗項目的測試應力,以及高溫柵偏或者高溫反偏測試指導、在溫度循環試驗和間歇工作壽命試驗這兩個重點檢查項目中試驗應力測定過程可引導裝置研制單位測定新型裝置考核應力,也可引導裝置使用者評價已有認證裝置是否適應應用。
4.2 關鍵檢驗項目試驗應力的確定過程
2.1 高溫柵偏或高溫反偏試驗
根據汽車電子典型應用的任務剖面,15 年內器件的工作時間 tu 為 12 000 h,假設器件在使用環境中的平均結溫 Tu 為 100 ℃,高溫柵偏或高溫反偏試驗時器件的結溫 Tj 為 150 ℃。AEC Q101 版采用阿倫尼烏斯模型對高溫柵偏或高溫反偏試驗引發失效的機理進行建模,見公式 1。
AEC Q101 采用 0.7eV 作為激活能的典型值,玻爾茲曼常數 kB 取 8.61733×10-5eV/K。根據公式tt=tu/Af 計算出時間時間為 916 h,AECQ101 取 1 000 h 作為規范中規定的高溫柵偏或高溫反偏試驗時間。
研制單位或用戶可以根據具體的使用條件計算出具體應用條件下所需的試驗時間。
2.2 溫度循環試驗
根據汽車電子典型應用的任務剖面,15 年內器件要承受 54 750 次開關循環,假設器件在使用環境中受外部因素影響而引發的溫度的變化平均值 ΔTu為 70 ℃,溫度循環試驗時器件的溫度變化 ΔTt 為205 ℃ ( 低溫 -55 ℃,高溫 125 ℃ )。AEC Q101 采用Coffin-Manson 模型對溫度循環引發的失效的機理進行建模,見公式 2。
AEC Q101 取 m=4 計算溫度循環試驗的加速系數,并根據公式nt=nu/nt計算出的需要進行的溫度循環的次數為 744 次循環,通過取整,AEC Q101 規定鑒定時需進行 1 000 次溫度循環試驗。
研制單位或用戶可以根據具體的使用條件計算出具體應用條件下所需的溫度循環次數。
2.3 功率循環
根據汽車電子典型應用的任務剖面,15 年內器件要承受 54 750 次開關循環,假設器件在使用環境中的由于自身發熱而引發的溫度的變化的平均值ΔTu 為 55 ℃,功率循環試驗時器件的溫度變化 ΔTt為 100 ℃ ( 常 溫 25 ℃, 加 電 后 結 溫 達 到 125 ℃ )。AEC Q101 采用 Coffin-Manson 模型對功率循環引發的失效的機理進行建模,見公式 2。
AEC Q101 取 m=2.5 計算功率循環試驗的加速系數,并根據公式nt=nu/nt計算出的需要進行的功率循環的次數為 12 283 次循環,通過取整,AEC Q101 規定鑒定時需進行 15 000 次功率循環試驗。
研制單位或用戶可以根據具體的使用條件計算出具體應用條件下所需的功率循環次數。
局限性及應對策略
車規級分立器件屬于民用產品,對航空、航天等應用領域有一定的局限性,具體體現在以下 2 個方面。
(1) 設計及材料頻繁改變,如鍵合絲從金絲,鋁絲改為銅絲等,各批產品的可靠性差別很大,使用者所購產品不一定是當初評估過的。盡管更改后器件可靠性能達到規范要求,但是可靠性的確發生了改變,是否能達到特定應用需求還需再次驗證。
(2) 車規級分立器件評估以汽車壽命周期任務剖面為研究對象,沒有考慮航空,航天等應用任務要求,評估項目存在局限性。
針對車規級分立器件在高可靠應用中的局限性,筆者提出相應的應對策略 :
(1) 考慮到車規級分立器件的設計及材質頻繁變化,提出了用戶應分批購買同一批產品以避免因不同批產品設計及材質不統一而造成的損失;
(2) 考慮到車規級分立器件評價項的限制,推薦用戶對特定任務剖面推薦需補充評價項,如鹽氣試驗,低氣壓試驗和耐輻照試驗。
結語
車規級分立器件鑒定評價項目及應力是以汽車壽命周期內任務剖面為對象而擬定的,其評價項目綜合,測試應力惡劣,被廣泛應用于航空,航天及其他高可靠領域。提出了用戶對車規級分立器件適用性評價應結合應用任務需求,明確評價測試項目及測試應
-
半導體
+關注
關注
334文章
27290瀏覽量
218095 -
分立器件
+關注
關注
5文章
213瀏覽量
21220 -
器件
+關注
關注
4文章
310瀏覽量
27824 -
汽車
+關注
關注
13文章
3493瀏覽量
37253
發布評論請先 登錄
相關推薦
基本半導體碳化硅MOSFET通過AEC-Q101車規級認證
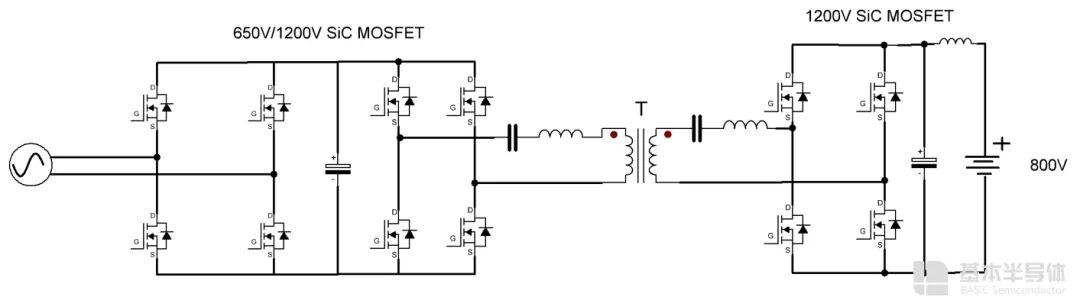
基本半導體碳化硅MOSFET通過車規級認證,為汽車電子注入新動力
芯弦半導體高性能車規MCU系列獲AEC-Q100車規級認證證書
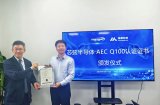
安徽爍軒半導體開展車規級Micro LED驅動及3D封裝技術研究
貝思科爾邀您參加ASPC2024亞太車規級功率半導體器件及應用發展大會
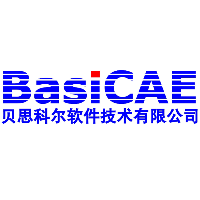
評論