高速激光熔覆工藝已經得到了市場的高度認可,高速激光熔覆代替普通激光熔覆將成為行業技術發展的必然趨勢。但激光熔覆是一種較為復雜的工藝過程,為幫助廣大高速激光熔覆用戶較快的掌握工藝,根據多年的經驗,把高速激光熔覆工藝的知識要點和各種工藝問題的原因總結如下,希望對廣大的業內同行能有所幫助。
1.高速激光熔覆的工作原理
高速激光熔覆是利用高能激光束將金屬粉末流在空中熔化,同時也將基體熔化形成熔池,熔化的粉末和熔化的基體結合后,快速冷卻形成冶金結合的涂層。
2.高速激光熔覆工藝關鍵參數及其對熔覆效果的影響
(1)激光功率
功率大小直接影響單位時間內可以熔化的粉末量,影響熔覆效率。在其他工作參數確定時,功率過小,可能會導致粉末熔化不徹底,磨拋后出現麻點,結合力不夠,涂層硬度偏低;功率過大,有可能熔道過熔,導致表面出現斜皺紋。
(2)送粉量
粉流與激光相遇后,吸收激光能量。粉量越大,吸收的激光能量越多。粉量過大時,會導致激光能量不足,出現涂層熔不透,磨拋后出現麻點,還會出現基體不能熔化,涂層和基體不能實現冶金結合,導致涂層脫皮問題。粉量大,粉末利用率低;粉量小,粉末利用率高。
(3)線速度
線速度越大,熔覆越薄,線速度越小,熔覆越厚。線速度過大,會導致基體不能形成熔池,涂層和基體不能很好冶金結合,熔道冷卻慢,紅色尾巴過長,出現脫皮現象。線速度小可提高涂層硬度以及粉末利用率。
(4)步進
步進越小,搭接率越大,涂層表面越細膩;步進越大,搭接率越小,涂層條紋越明顯。步進影響稀釋率,步進小時,照射到基體上的激光能量小,稀釋率低;步進大時,照射到基體上的激光能量多,稀釋率高。
(5)送氣量
氣體有兩個作用,一是輸送粉末,二是保護高溫涂層,防止氧化。送粉氣量過小,容易堵粉;送粉氣量過大,粉末速度過快,彈射大,粉末利用率低。一般情況下,氬氣比氮氣對涂層的保護更好,涂層質量更高。
(6)噴嘴高度
噴嘴過高,粉末發散大,粉末利用率低;過低,熔覆過程噴嘴容易粘粉。
3.高速激光熔覆過程中容易出現的問題及原因分析
(1)脫皮
這是由于基體沒有形成熔池,粉末與基體沒有冶金結合,可能的原因有:功率過低;粉量過大;線速度過快;工件表面有油污或電鍍層等。
(2)裂紋
涂層出現裂紋的原因有:基體硬度過高(淬火、滲碳/氮);基體有疲勞層;粉末硬度過高等。鎳基粉末容易出現裂紋;硬度高的粉末多層熔覆時,也會出現裂紋。
(3)氣孔
涂層出現氣孔的原因有:基體有銹跡油污;粉末有雜質;粉流不穩;粉量過大;功率不夠;或線速度過大等。
(4)浮粉多,涂層無金屬光澤
可能的原因有:粉量過大;功率過小;線速度過快;噴嘴高度過高;激光光斑過小;鏡片污染等。
(5)磨拋后出現麻點
可能的原因有:功率不夠;粉量過大;線速度過快等。
(6)涂層出現斜皺紋
可能的原因有:功率過大;熔池溫度過高;粉末過度液化。
(7)噴嘴粘粉
可能的原因有:粉末彈射太高;銅頭溫度過高;噴嘴工作距離過低,噴嘴表面太粗糙或污染(建議拋光處理)。熔覆頭偏離中心放置,有利于減少粘粉現象。
(8)堵粉
可能的原因有:粘粉沒有及時清除;粉末流動性不好;粉末有雜質或粉末受潮(要烤干)等。在多路送粉時,各路送粉不均等是堵粉的重要原因。
(9)熔覆時有滋滋聲
可能的原因有:粉末受污染;粉末受潮;基體不干凈等。功率密度過大也會導致熔池金屬氣化,產生熔覆噪聲。這些問題會影響涂層防腐性。
(10)熔覆火花飛濺
可能的原因有:線速度過大;功率密度過大;功率和粉量不匹配;氣流量過大等。
(11)粉流不穩,進而導致涂層不平整
粉流不穩的原因有:刮板磨損大;送粉通道堵塞;氣流過小;送粉器密封圈處密封不好或送粉管破損等導致漏氣等。
(12)熔覆效率下降(涂層厚度變薄)
可能的原因:保護鏡污染;刮板磨損;工作距離不合適;出粉孔被磨大,粉流變粗;激光功率下降等。
-
激光
+關注
關注
19文章
3182瀏覽量
64449 -
高速
+關注
關注
0文章
115瀏覽量
23162 -
激光熔覆
+關注
關注
0文章
135瀏覽量
7075
發布評論請先 登錄
相關推薦
前段體高速激光熔覆修復加工
內孔激光熔覆修復原理及應用
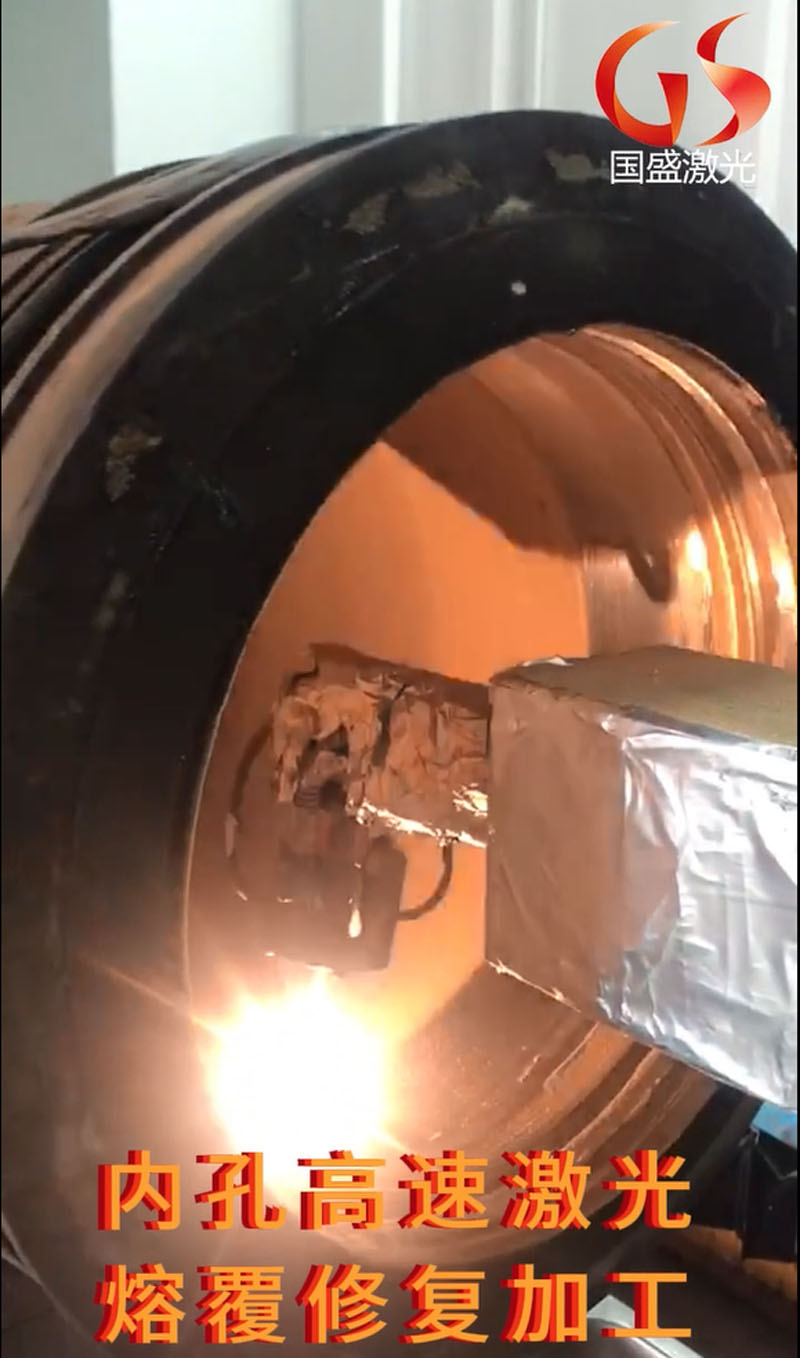
評論