線束作為汽車的“神經系統”,負責汽車各部分之間電壓和信號等數據的傳遞。同樣,線束也如“神經系統”般復雜和脆弱,在整車制造過程中容易出現大量問題。如何采取適當的措施減少或者避免缺陷的產生成為保障汽車安全的重要一環。特別是在如今汽車電子系統不斷向集成化、功能化、智能化發展的今天,線束故障的發生將直接導致整車“癱瘓”。不僅如此,如果線束產品在開發及生產過程中的故障發現得太晚,或者是到產品投入市場時才發現,返工及糾正措施在成本及時間上都耗費巨大。為了避免這種情況,如何在早期階段就發現問題并有效減少或者避免故障發生便成為了重中之重。FMEA就是有效的解決方法。那么什么是FMEA呢?
FMEA,即Failure Mode and Effects Analysis,是在產品設計階段和過程設計階段,對構成產品、設備的子系統、零件,以及構成過程的各個工序逐一進行分析,找出所有潛在的失效模式,并分析其可能的后果,從而預先采取必要的措施,以提高產品或設備的質量和可靠性的一種系統化的活動。最開始是美國在上世紀50年代,在軍事領域進行信息系統的設計分析中應用,后面擴展到航天工業,到70年代,FMEA開始用于民營企業,到70年代末期,FMEA開始被美國汽車工業所采納。福特是最早實施FMEA的公司之一,將FMEA技術操作標準寫入其操作手冊標準中,這不僅僅是用于福特內部,福特公司還規定其所有供應商都必須對其供應給福特公司的零部件進行 FMEA分析。1993年, 福特、 通用和克萊斯勒三大汽車巨頭制定了一套針對汽車產業中的所有零件的" 潛在失效模式與影響分析參考手冊", 至此, FMEA作為一種標準化的技術在美國汽車行業中得到了極大的應用。1994年, 作為QS-9000 的核心方法之一,為了提高產品的質量,ISO推薦將FMEA方法用于產品的設計階段, 以確保產品生產過程的穩定性。到目前,世界許多汽車生產商和電子制造服務商(EMS)都已經采用這種模式進行設計和生產過程的管理和監控。
FMEA目前主要分為設計FMEA(DFMEA)、過程FMEA(PFMEA)。其中DFMEA指設計失效模式和后果分析,關注的是產品設計產生的潛在失效。PFMEA指過程失效模式和后果分析,關注的是產品制造過程中產生的潛在失效。
DFMEA和PFMEA的區別
應用階段:DFMEA應用于產品設計階段,而PFMEA應用于產品制造階段。
分析對象:DFMEA主要針對產品設計,包括各個零部件和子系統,而PFMEA則主要針對生產過程中的各個步驟,包括工藝、設備、材料和人員等。
分析方法:DFMEA的分析方法側重于預防潛在的失效,通常包括對設計進行檢查、試驗和驗證。而PFMEA則側重于找出生產過程中的問題,并采取措施進行糾正和預防。
在實踐中,企業需要根據具體情況和需求選擇使用DFMEA還是PFMEA。例如,對于一個新產品的設計,企業可能會選擇使用DFMEA來評估潛在的設計問題,以提高產品質量和可靠性。而在產品制造過程中,企業可能會選擇使用PFMEA來識別和解決生產過程中的問題,以優化生產流程并提高效率。值得注意的是DFMEA和PFMEA并不是完全獨立的。它們可以相互補充,提供更全面的質量保證。例如,在設計階段,DFMEA可以識別潛在的設計問題,然后在生產階段,PFMEA可以進一步評估這些問題的實際影響,并采取相應的糾正措施。
雖然DFMEA和PFMEA在應用對象、方法和結果上有明顯的區別,但它們都是為了預防和減少產品或過程中的潛在失效。為了讓大家更好的學習并深入了解DFMEA和PFMEA,ATC汽車技術平臺特邀請國內頭部線束總成企業質量總監開展《線束DFMEA/PFMEA專題培訓》內容涵蓋線束D/PFMEA分析邏輯、線束D/PFMEA常見失效模式和優化措施,更有結合企業實際制造過程的案例演練與答疑,在設計中引入DFMEA預防潛在的失效,生產中引入PFMEA對過程風險進行識別,大大提升線束產品過程生產的良品率,降低產品生產成本,提升顧客滿意度。
編輯:黃飛
-
神經系統
+關注
關注
0文章
84瀏覽量
12988 -
汽車安全
+關注
關注
4文章
269瀏覽量
34575 -
線束
+關注
關注
7文章
973瀏覽量
25976
原文標題:yyds,線束專家總結的設計經驗都在這里...
文章出處:【微信號:線束專家,微信公眾號:線束專家】歡迎添加關注!文章轉載請注明出處。
發布評論請先 登錄
相關推薦
車規MCU之設計失效模式和影響分析(DFMEA)詳解
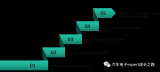
電子封裝失效分析培訓IPC610技能培訓耀谷owen技能培訓基地
dfmea
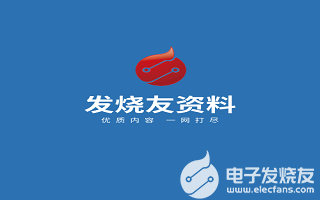
dfmea分析
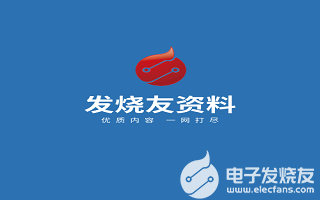
dfmea里的過濾嗎
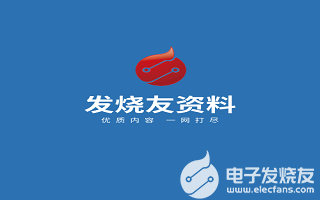
pcb行業dfmea
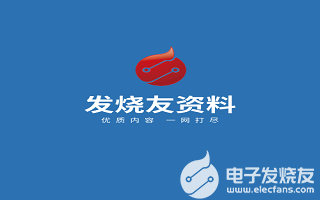
dfmea怎么念
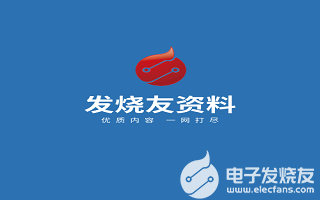
dfmea和pfmea的區別
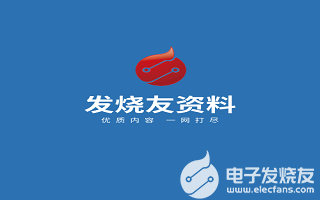
評論