作者:泛林集團 Semiverse Solutions 部門半導體工藝與整合高級工程師王青鵬博士
持續的器件微縮導致特征尺寸變小,工藝步驟差異變大,工藝窗口也變得越來越窄[1]。半導體研發階段的關鍵任務之一就是尋找工藝窗口較大的優秀集成方案。如果晶圓測試數據不足,評估不同集成方案的工藝窗口會變得困難。為克服這一不足,我們將舉例說明如何借助虛擬制造評估 DRAM 電容器圖形化工藝的工藝窗口。
在 DRAM 器件開發中,必須在硅晶圓上刻蝕用于存儲電荷的電容孔陣列??捎脕碇圃?40nm 孔陣列的圖形化方案包括極紫外光刻刻蝕、四重光刻刻蝕、雙自對準雙重圖形化技術 (SADP)(80nm芯軸間距)和雙自對準四重圖形化技術 (SAQP)(160nm芯軸間距)。在這項研究中,我們選擇了浸潤式雙 SADP 和 SAQP 圖形化方案,并對其工藝靈敏性和工藝窗口進行了比較。我們為每個圖形化方案 (SADP和SAQP) 建立了虛擬工藝流程(如圖1),并將電容器孔面積作為電容及其均勻性分析的衡量標準。為了算出孔面積的變化范圍,我們在 SEMulator3D 中使用結構搜索,尋找 4×4 孔陣列中電容器孔面積的最小值和最大值,并計算出平均面積和面積差值。圖2顯示了一次輸出結構的測量結果,其中確定了結構中孔面積的最小值和最大值。
圖1:SADP和SAQP的主要工藝步驟
圖2:最小面積與最大面積的虛擬測量結果
基于以上的虛擬流程和測量,我們使用 SEMulator3D 分析模塊,進行了3000次蒙特卡羅實驗。我們將芯軸關鍵尺寸和間隔層厚度設置為實驗設計的輸入參數,將平均面積和面積變化范圍設置為輸出參數。表1列出了 SADP 和 SAQP 工藝的輸入參數值范圍。虛擬實驗設計結果幫助我們研究每項輸入對平均面積和面積變化范圍的影響。在表1中,MX 表示 X 方向芯軸關鍵尺寸;MY 表示 Y 方向芯軸關鍵尺寸;SPX1 表示 X 方向第一個間隔層厚度;SPX2 表示 X 方向第二個間隔層厚度;SPY1 表示 Y 方向第一個間隔層厚度;SPY2 表示 Y 方向第二個間隔層厚度。
表1:實驗設計變量及輸入范圍
平均面積越大、面積變化范圍越小,電容分布就越密集且均勻。通常認為,平均面積在900nm2至1100nm2之間,面積變化范圍小于200nm2被定義為實驗成功。在特定條件下,可以為工藝窗口算出成功模擬實驗在總體實驗所占比率(稱為規格內比率),從而生成平均值和3-sigma(±3*標準差)分布。這個比率表示產生成功標準范圍內平均面積和面積變化范圍需要的輸入組合比例。
為了最大化平均±3 sigma窗口中的實驗成功次數,可以通過調整輸入工藝參數平均值的方法,優化規格內比率[2]。如果優化后的規格內比率仍然不夠高,還可以通過提高規格 (3 sigma) 要求,進一步對其進行優化。我們計算了不同條件下 SADP 和 SAQP 工藝的規格內比率。在 3 sigma 分布相同的情況下,SADP 工藝的規格內比率比 SAQP 工藝高約10%。調整芯軸關鍵尺寸的 3-sigma 規格后,SADP 工藝的規格內比率接近100%。當芯軸關鍵尺寸相同時,SAQP 工藝的規格內比率較低,表明 SAQP 工藝窗口需要進一步緊縮。
結論
在這項研究中,我們使用虛擬制造為先進 DRAM 結構中的電容器形成工藝進行了工藝窗口評估和優化。虛擬評估提供了明確且可量化的指導,幫助我們判斷在先進 DRAM 結構中使用不同圖形化方案的工藝難題。最重要的是,我們能在晶圓實驗前確定每個圖形化方案的最佳工藝目標組合和條件允許的最大工藝窗口。
-
電容器
+關注
關注
64文章
6217瀏覽量
99540 -
DRAM
+關注
關注
40文章
2311瀏覽量
183447 -
虛擬制造
+關注
關注
0文章
11瀏覽量
9429 -
泛林集團
+關注
關注
0文章
58瀏覽量
11801
發布評論請先 登錄
相關推薦
電力電容器的防火防爆
三星宣布:DRAM工藝可達10nm
電容器的入門學習教程
薄膜電容器生產工藝
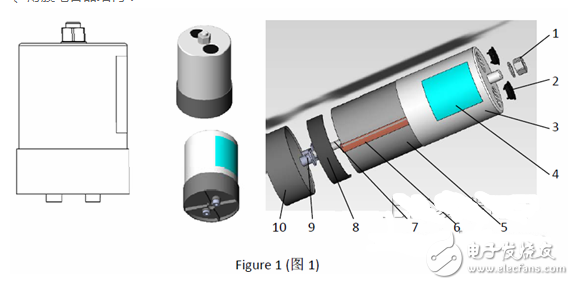
評論