制造智能化
生產力的提升是整個人類社會前進的動力。從蒸汽機的發明,到自動生產線的引入,再到數控機床和計算機集成制造的出現,工業革命已經完成了三次生產力躍升,實現了從手工生產到機械化、電氣化、再到數字化的變革。當下隨著無線互聯、大數據和人工智能的發展,我們迎來了工業4.0時代,制造業正在從自動化向智能化全面轉型。
在此背景下,"智能工廠"應運而生,它利用先進的自動化技術、數據分析和機器學習,實現了生產過程的高度優化和靈活性。而"工廠預測性維護"是智能工廠概念的一個關鍵組成部分。
根據IoT Analytics的報告,預測性維護市場規模將從2021年的69億美元增長到2026年的282億美元,年復合增長率將達到31%。對于降低維護成本的需求,以及實時流分析技術的不斷普及,將促進這一市場持續擴大。
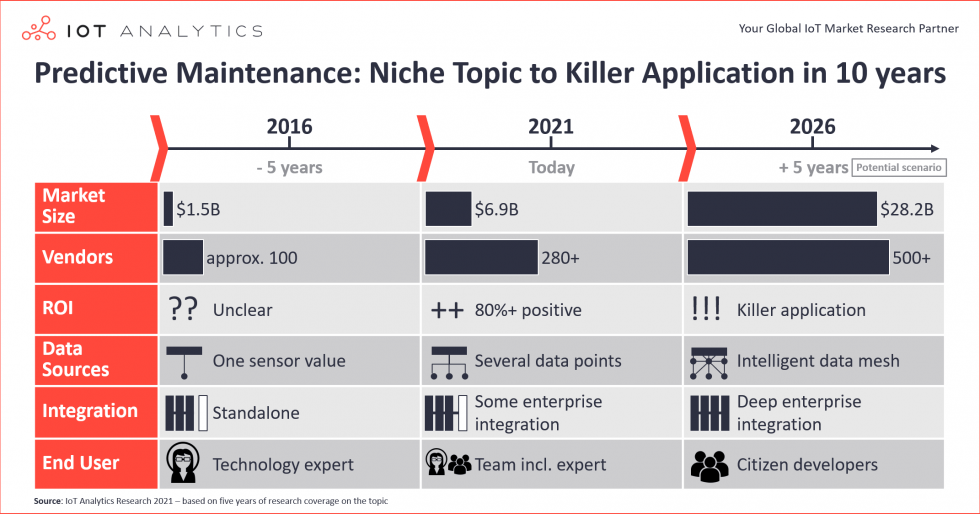
圖1:預測性維護市場發展
(圖源:IoT Analytics)
從預防性維護到預測性維護
提前化解潛在風險
在過程工業領域,確保設備的正常運行是關鍵因素,它不僅影響工廠的高效率運作,同時也是可靠和安全生產的基石。對于工廠而言,如何在提高產能的同時降低維護成本、提升關鍵設備的可用性,并減少非計劃性的停機時間,已成為一個日益重要的議題。
設備維護的兩種主流模式是預防性維護和預測性維護,它們的共同目標是消除非計劃性的生產停機。
1
預防性維護
預防性維護側重于基于時間的策略,為設備設定一個預計的使用“保質期”,然而這種方法并不能準確反映設備的實際運行狀況,例如潛在的故障風險及其發生的時間通常是未知的。“過度維護”往往不能有效地預防“非計劃停機”,有時甚至會意外地引發“維修性故障”。
2
預測性維護
相比之下,預測性維護通過實時監測和分析設備的運行狀態,能夠為用戶提供關于設備故障風險的即時評估,提前發出風險預警,并協助判斷“保質期”的適用性,找到每一臺設備自己專屬的維護平衡點,從而避免非計劃停機的發生。
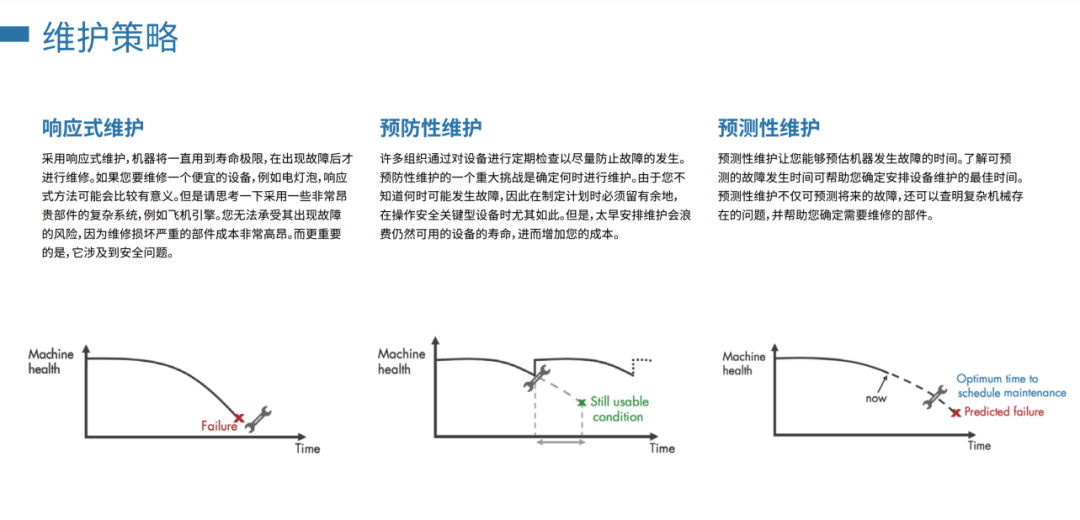
圖2:三種維護策略比較
(圖源:Mathworks)
預測性維護的概念起源于20世紀70年代,簡稱PdM(Predictive Maintenance)。當時隨著計算機技術和數據分析方法的發展,人們開始探索如何通過數據分析來優化設備的維護和運營。開始時,預測性維護主要應用于航空和軍事領域,用于提高關鍵設備的可靠性和安全性。
隨著時間的推移,這一概念逐漸被應用到各種工業領域,特別是在工業4.0和智能制造的背景下,預測性維護結合了先進的物聯網(IoT)技術、大數據分析和人工智能(AI),成為現代工業維護的重要組成部分。
盡管大多數企業仍依賴歷史經驗來診斷設備故障,這些經驗通常是這些領域的專家多年積累的結果,但它們的共享和傳承對許多企業管理者來說是一個挑戰。若能利用基于歷史故障記錄的大數據分析,并結合自然語言處理算法,構建一個企業診斷系統來固化這些經驗,并充分利用工廠的故障記錄數據,就能實現對故障的快速匹配診斷,并及時進行有效的修復和維護。這不僅能大幅提高故障處理效率,還能顯著降低誤判風險。對于工廠而言,預測性維護不僅提高了制造業的生產效率和質量,還改變了傳統工業生產的方式,使得生產過程更加智能、高效和可持續。
Tenaris是一家全球無縫鋼管制造商,該公司從2018年底引入了ABB Ability的高低壓電機狀態監測系統,在電機上部署傳感器來監測其日常工作狀態,然后通過無線網關將數據傳輸到專門的云端進行存儲和分析。通過對于電機狀態數據的實時監測分析,該系統可以提前預測出電機的故障類型和停機時間,從而做到更合理的計劃性維修。通過預測性維護系統的引入,Tenaris實現了460臺電機的24小時全天候無休運轉,每年生產量提高至約800,000噸。
圖3:ZDT系統
(圖源:FANUC)
發那科(FANUC)是一家數控系統生產商,與思科共同開發了“Zero Down Time”零停機功能,并將這一系統部署到了通用汽車的生產線中。該系統實時收集機器人數據并進行分析,可在機器人發生故障之前檢測到機器人機構、控制裝置等方面的異常,并提醒用戶在停機發生前進行有針對的維護維修,從而避免突然停機帶來的損失。通過此預測維護系統,成功地為通用汽車縮短了生產停機時間并有效地提高了設備綜合效率(OEE)。
其實遠不止以上列舉的兩個領域,預測性維護系統已經在汽車制造業、能源產業、化工業和食品加工等多個工業生產環節中發揮了巨大的作用,在提高了生產率的同時,還進一步實現了更高的安全性。
在預測性維護系統中
構筑高速可靠的連接
要實現一個完整的設備預測性維護系統,可以分為三個層面:感知+執行層、連接和云平臺。在設備端,需要通過傳感器來采集各種模擬數據,然后轉換成數字信號發送至云端,云端的大數據平臺進行數據的分析和處理,然后將分析結果分享給運維人員,同時將指令反饋回端側做出相應的持續監測或提醒。
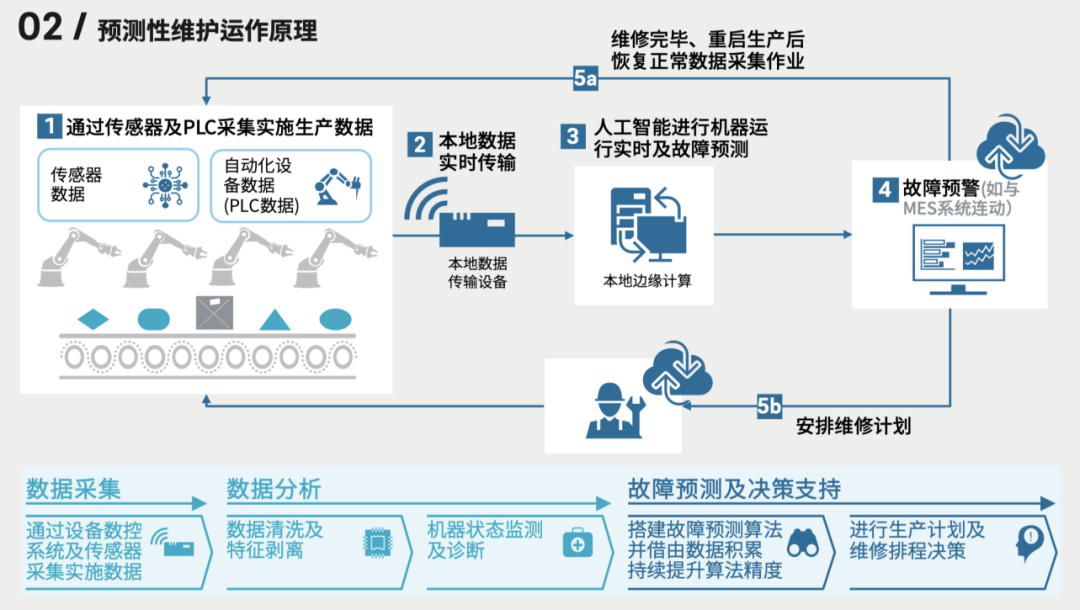
圖4:預測性維護原理
(圖源:羅蘭貝格)
顯而易見,在工廠預測性維護系統中,充斥著大量的連接場景,連接器在其中扮演著重要的紐帶角色。具體體現在以下幾個關鍵部分:
傳感器連接
連接器用于將傳感器物理連接到工廠中的機器和設備上。這些傳感器監測如溫度、振動、壓力等關鍵參數,用于檢測設備可能出現的問題。連接器確保這些傳感器可靠地附著在目標設備上,并穩定傳輸數據。
數據采集單元
在數據采集單元,連接器用于將各種傳感器和測量設備連接到數據采集系統。這樣一來,就可以從多個源收集數據,并將其傳輸到中央處理單元以進行進一步分析。
工廠的預測性維護系統依賴于內部通信網絡來共享和傳輸數據。連接器在這里用于連接不同的網絡組件,如路由器、交換機和數據處理單元,保證信息流動的穩定性和高效性。
連接器還被用于將預測性維護系統與工廠的控制系統相連接。這種連接可以讓預測性維護系統將其發現的情況和推薦的維護措施傳遞給控制系統,以便操作人員采取必要的行動。
在電源管理方面,連接器用于確保所有的傳感器、數據采集設備和通信設備都能獲得必要的電源供應。這包括將這些設備連接到電源線或電池。
維護和故障診斷
在預測性維護系統的維護和故障診斷階段,連接器可以用于快速連接或斷開設備,以便進行維修或更換。這種快速連接/斷開功能減少了停機時間并提高了維護效率。
通過這些不同的應用,連接器在工廠預測性維護系統中起著至關重要的作用,確保了系統組件之間的穩定連接和高效通信,從而使整個預測性維護過程更加可靠和高效。
工業連接器:助力高效可靠的連接
既然是工業場景中的連接器,自然要能夠抵抗工業環境中的極端條件,在耐用性、魯棒性、電氣性能和防水防塵等方面,都要符合比常規連接器更高的標準。同時,還要滿足某些特殊工業場景中的反復插拔要求、EMI/RFI屏蔽能力、承重能力、更高的機械強度等。此外,連接器還應符合特定行業的安全和質量標準,例如UL、CE、RoHS等認證。這些要求可確保連接器在工業環境中的穩定性和性能,對于維護生產線的高效和可靠運行至關重要。
那么什么樣的連接器能夠滿足以上的種種要求,助力工廠預測性維護系統的穩定高效運行呢?在這里我們為大家挑選了兩款來自TE Connectivity的產品。一款是“盲插移動充電連接器”,在貿澤電子官網上的產品料號為“2400405-1”。
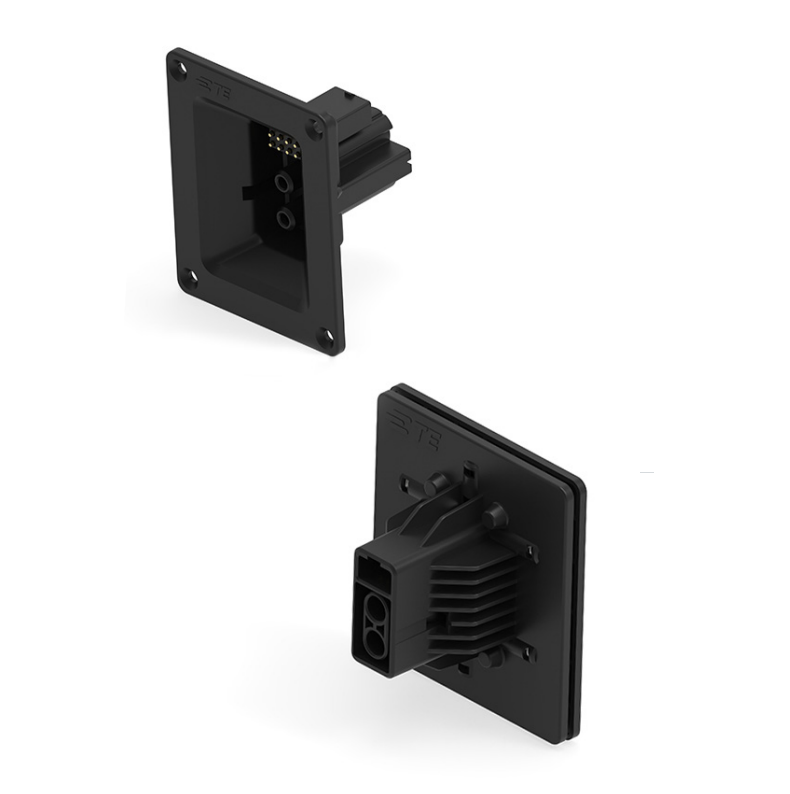
圖5:盲插移動充電連接器
(圖源:貿澤電子)
該連接器具備四大優勢:一是超長壽命周期,達到了至少12,000次的設計插配周期;二是更好的連接靈活性,提供2和3電源觸點選項;三是提供多達8個信號觸點,每條線路高達0.5A;四是提供了盲插便利性,允許一定程度的錯位插入。
另一款推薦的連接器是TE Connectivity的“AMPMODU 1.0mm中心線互連系統”。
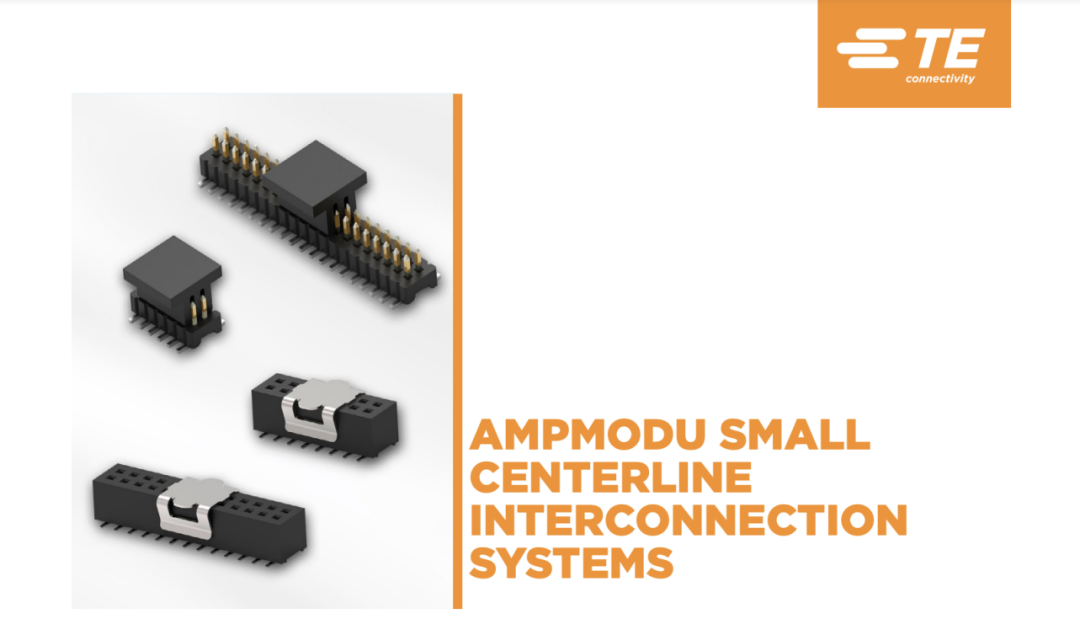
圖6:AMPMODU 1.0mm中心線互連系統
(圖源:貿澤電子)
該系列非常適用于工業I/O連接。與標準2.54mm腳距連接器相比,該系列可節省電路板85%的空間;雙梁觸點設計即使在劇烈沖擊/振動環境中也能提供可靠的電氣連接;鍍金選項提高了耐用性和耐腐蝕性。該系列產品在貿澤官網上的具體產品型號為“1MM-R-D06-VS-00-F-TBP”。
工業預測性維護
AI在工業端側落地的開始
預測性維護,被視為是AI在工業場景中非常容易落地的應用方向之一。這是因為工業領域通常已經擁有大量的歷史運行數據,這些數據可以用于訓練預測性維護模型。這降低了實施AI系統所需的數據收集和準備的成本和復雜性;同時預測性維護具備清晰的業務目標,也更易獲得明顯的投入回報。
此外,預測性維護還具備非常好的“伸縮性”。預測性維護可以逐步實施,從幾臺設備開始,逐漸擴展到整個生產線或工廠。這種漸進的方法有助于企業適應變革,逐步提高維護效率。在AI的能力加持下,智能工廠正在以預測性維護為基礎,向著全面數字化運維場景逐步邁進。
相關技術資源
TE Connectivity的盲插移動充電連接器,了解詳情>>
TE Connectivity的AMPMODU 1.0mm中心線互連系統,了解詳情>>
該發布文章為獨家原創文章,轉載請注明來源。對于未經許可的復制和不符合要求的轉載我們將保留依法追究法律責任的權利。
-
貿澤電子
+關注
關注
16文章
1114瀏覽量
96636
原文標題:隔空把“脈”,料“事”如神,智能工廠中的預測性維護技術
文章出處:【微信號:貿澤電子,微信公眾號:貿澤電子】歡迎添加關注!文章轉載請注明出處。
發布評論請先 登錄
相關推薦
評論