一.印制基板的基本功能
1.足夠的機械強度;
2.能夠承受組裝工藝中的熱處理和沖擊;
3.具有足夠的平整度以適應自動化的組裝工藝;
4.能承受 6 次以上的焊接和返修工作;
5.良好的電氣性能和耐潮濕性能;
6.良好的尺寸穩定性。
二.印制電路板性能等級
軍用印制電路板性能等級分為如下三級:
1級:普通軍用電子設備,主要用于地面和一般軍用設備。要求印制電路板組裝后有完整的功能,一定的工作壽命和可靠性,允許有一些不影響電氣和機械性能的外觀缺陷;
2級:專用軍用電子設備,主要用于軍用通信設備、復雜的軍用電子設備等。要求印制電路板組裝后有完整的功能,較長的工作壽命及較高的可靠性,允許有不影響使用性能的輕微外觀缺陷;
3級:高可靠軍用電子設備,主要用于車載、機載、艦載、航天等軍用電子設備。要求印制電路板組裝后有完整的功能、長的工作壽命、連續工作和高的可靠性,在使用中不允許發生任何故障。
三.印制電路板基本要求
1.印制電路板應符合設計文件和工藝文件要求,根據印制板結構確定基材的覆銅箔面數(單面、雙面或多層板),并與組裝過程中選用的元器件、工藝材料的特性相兼容。
2.印制電路板外觀要求
1)基板面應平整、邊緣整齊、圖形不失真;不應有碎裂、毛刺、起泡和分層 ;
2)印制導線表面應光潔,色澤應均勻,無翹箔、鼓脹和明顯的劃痕;
3)表面鍍層應光亮均勻,不起皮鼓泡;
4)阻焊膜厚度應不大于焊盤的厚度;
5)焊盤上應無字符、阻焊膜和其它污物沾污;
6)其它性能應符合GJB362B中的有關要求。
3.印制電路板應適用于波峰焊和再流焊。
4.平整度(弓曲和扭曲)
焊接前通孔插裝PCB的弓曲和扭曲應不大于1%,表面安裝用PCB的弓曲和翹曲一般應不大于 0.75%,窄間距應不大于 0.5%。
5.工藝基準孔、識別標志及焊區的安裝位置精度應符合組裝工藝要求,標志表面平整、無沾污、亮度均勻,相對背景有較高的反差。
6.印制電路板表面涂(鍍)覆層的選擇
1)軍用PCB 表面涂(鍍)覆層應采用熱風整平工藝或電鍍鎳金工藝,不應使用化學鍍鎳金工藝;PCB 表面涂(鍍)覆層應在PCB 裝配圖上注明。
2)PCB 焊盤及金屬化通孔可焊性保護層應采用含鉛量≥3%的鉛錫合金焊料;表面安裝焊盤采用錫鉛合金為可焊性保護層,錫鉛合金層厚度應不小于 2.8μm~8μm。對于 3 級印制電路板和高密度PCB 建議使用電鍍鎳金(Ni/Au)為可焊性保護層。Ni層為 5μm~7μm,Au層為 0.05μm~0.15μm。
3)阻焊膜的涂覆按 GJB362B的 3.5.1.8執行。固化的阻焊膜的最小厚度按GJB4057的規定,2級板為 10μm,3級板為 18μm;
4)需要安裝(螺裝或焊接)屏蔽盒的印制表面涂覆鉛錫焊料時,應盡量減少鉛錫焊料涂覆面積,或按進行阻焊膜與鍍錫層交叉的網格方式設計大面積接地面。
7.印制電路板的可焊性
1)印制電路板金屬化孔的可焊性
按QJ832A 規定的試驗后,焊料應潤濕到孔頂部周圍的焊盤(連接盤) 上。在焊接溫度為 232℃~237℃,焊接時間為 3s 的條件下,金屬鍍層應對焊料呈濕潤狀態,必須完全潤濕孔壁,不應有不潤濕或露基底金屬的現象。 可不完全填滿孔,但焊料相對于孔壁的接觸角應小于90o。
2)印制電路板表面可焊性
根據規定的焊接溫度、焊接時間和附著在導體上焊料層的外觀,表面可焊性要求按表 4 規定。
8.印制電路板的耐熱性(熱應力)
1.印制電路板在溫度 287℃±6℃的熔融焊料中浸焊 10s~11s 后,不應出現分層、起泡或破壞,表層印制導線對基板的抗剝強度應符合抗剝強度的要求,阻焊層不出現起皺、脫落等現象。在實際焊接過程中,印制電路板元器件和導線的手工焊接溫度規定為240℃±10℃,波峰焊焊接溫度為250℃±5℃,再流焊焊接溫度為235℃±5℃;按上述規定執行時,如印制電路板出現分層、起泡、或破壞,或阻焊層不出現出現起皺、脫落等現象則是印制電路板的耐熱性(熱應力)不符合要求。
9.阻燃型環氧樹脂紡織玻璃布基材(FR-4)抗剝強度
1.在正常條件下厚度 35μm以上的FR4基板表層印制導線對基板的抗剝強度應不小于 1.4N/mm;厚度為 18μm的FR4基板表層印制導線對基板所承受的最小剝離強度應不小于 1.1N/mm;在經受 2)規定的試驗條件后, FR4 基板多層印制電路板表層印制導線對基板的抗剝強度應不小于1.2N/mm。
2)在下列條件下連續依此放置后,FR4基板表層的印制導線對基板的抗剝強度應不小于 1.2N/mm。溫度-65±2℃下放置 6h;溫度 125±2℃下放置 16h;在交變濕熱條件下放置 48h。10.PCB 基材選用設計時應根據PCB 的使用條件和機械、電氣性能要求選擇基材:
1)根據印制板的尺寸、單位面積承載元器件質量,確定基材板的厚度;
2)選擇時還應考慮到電氣性能要求、Tg和CTE、平整度等因素及孔金屬化的能力;
3)除設計另有規定外,印制板所用的基材為阻燃型環氧樹脂紡織玻璃布基材(FR- 4)
四.混裝印制電路板
1.混裝印制電路板基材要求
有鉛元器件和無鉛元器件混裝PCB 基板材料主要根據電子產品的性能指標、使用環境、焊接溫度來選擇。
1)焊接溫度 240℃以下的產品,采用FR4 環氧玻璃纖維基板;
2)焊接溫度 240℃~250℃的產品,可選擇高 Tg 為 150℃~170℃的FR-4;
3)高可靠及厚板,焊接溫度 250℃以上的產品,采用FR-5;
4)使用環境溫度較高或撓性電路板采用聚酰亞胺玻璃纖維基板;5)對于散熱要求高的高可靠電路板采用金屬基板;
6)對于高頻電路則需要采用聚四氟乙烯玻璃纖維基板。
1.混裝印制電路板焊盤表面鍍(涂)層
應選擇可焊性符合GJB362B 要求的印制電路板表面鍍層,同時應考慮成本、儲存條件等因素。高可靠軍用電子設備推薦采用Pb-Sn 熱風整平(HASL)鍍層。
如果產品對于焊盤的平整度有較高的要求,推薦采用電鍍 Ni/Au 鍍層。高密度組裝建議采用電鍍 Ni/Au 鍍層,備選Pb-Sn 熱風整平(HASL)鍍(涂)層。
有些軍品PCB表面鍍層的設計中為了滿足兩次回流焊的需求,避免二次回流焊時,第一次焊接的元器件掉件,采用“溫度階梯焊”工藝,即 PCB 的A面熱風整平Pb-Sn合金鍍層,而在 B面涂覆無鉛焊料,這是不可取的 ; 掉件問題可以通過PCB布局設計解決,也可以通過其它工藝方法解決。1)設計方法采用雙面再流焊的混裝時,印制電路板設計應將大元器件布放在A面,小元器件在B面。
放置在B面的元器件應遵循以下原則:元器件(Dg)/焊盤面積<30g/in2式中:
Dg—元件質量;
P—該元件焊盤總面積。
雙面再流焊工藝一般先焊B 面,然后再焊 A 面,如果輔 B 面的元器件質量過重,二次回流時可能落在再流焊爐中。
當質量/面積比(Dg/P)小于 30g/in2 時雙面再流焊二次回流,元器件也不會掉下來。
2)工藝方法
(1)第二次再流焊時將再流焊爐上/下溫區設置一定的溫度差,一般爐子底部溫度低于頂部溫度 20℃~30℃。
(2)采用膠粘劑:B面的SMD/SMC經過兩次再流焊。當A面焊接時,B 面向下,已經焊在 B面的元器件在A面再流焊時,其焊料會再熔融,而且較大的元器件在傳送帶輕微振動時回發生偏移,甚至脫落,所以涂覆焊膏前還需用膠粘劑固定。
五.層壓板白斑和微裂紋等質量要求
1.IPC-610E-213
這種固有的層壓板狀況是在印制板制造或組裝過程中造成的。組裝過程中引起的白斑和微裂紋(例如:插針的壓接,再流焊等),通常不會進一步擴展。白斑違反最小電氣間隙的情況下,考慮到產品的運行環境條件,例如潮濕環境、低氣壓等,可能需要進行額外的性能測試和電介質阻抗測量。基板內含埋入式元器件的場合,可能需要規定另外的要求。
1.1白斑
1.1.1定義:一種發生在層壓基材內部,玻璃纖維在編織交叉處與樹脂分離的情形,表現為在基材表面下分散的白色斑點或“十字紋”,通常和熱應力 有關。
1.1.2合格1,2,3級:無白斑跡象。
1.1.3可接受1,2級
1)對白斑的要求是組件功能正常。
制程警示3級:層壓基板內的白斑區域超過內層導體間物理間距的50%。
注:白斑不是缺陷條件。白斑是在熱應力下可能不會蔓延的內部狀況, 且目前尚無定論證明白斑是導電陽極絲CAF生長的催化劑。分層是在熱應力下可能蔓延的內部狀況,且可能是CAF生長的催化劑。IPC-9691耐CAF 測試用戶指南和IPC-TM-650測試方法2.6.25提供了確定與CAF生長有關的層壓版性能的更多信息。
1.1微裂紋
1.1.1定義:一種發生在層壓基材內部,玻璃纖維在編織交叉處與樹脂分離的情形,表現為在基材表面下連續的白色斑點或“十字紋”,通常和機械應 力有關。
1.1.2合格1,2,3級:無微裂紋跡象。
1.1.3可接受
1)1級:對微裂紋的要求是組件功能正常。
2)2,3級
(1)層壓基板內的微裂紋區域不超過非公共導體間物理距離的50%。
(2)微裂紋未使間距減少到最小電氣間隙以下。
1.2.4缺陷- 2,3級
1)層壓基板內的微裂紋區域超過非公共導體間物理距離的50%。
2)間距減到最小電氣間隙以下。
3)板邊緣處的微裂紋使導電圖形到板邊的距離減到最小距離以下,或無具體規定時,減少量大于2.5mm。
1.1起泡和分層
一般情況下,分層和起泡是因材料或工藝存在先天不足造成的。對于發生在功能區與非功能區之間的起泡和分層,只要是絕緣的,并且其它要求都滿足,可以是可接受的。
1.1.1定義
1)起泡:一種表現為層壓基材的任何層與層之間,或基材與導電箔或保護 性涂層之間的局部膨脹與分離的分層形式。
2)分層:印制板內基材的層間、基材與導電箔間或任何其他面間的分離。
1.1.1合格1,2,3級:無起泡或分層。
1.1.2可接受- 1,2,3級:起泡/分層范圍未超過鍍覆孔間或內層導體間距離的25%。
1.3.4缺陷:1,2,3級
1)起泡/分層范圍超過鍍通孔間或內層導體間距離的25%。
2)起泡/分層使導電圖形間距減少至最小電氣間隙以下。
注:起泡或分層范圍可能在組裝或運行期間增加。這時可能需要制定單獨的要求。
1.1顯布紋/露織物
1.1.1定義
1顯布紋定義:基材表面的一種狀況,雖然未斷裂的纖維完全被樹脂覆蓋 , 但顯現出玻璃布的編織花紋。
1)露織物定義:基材表面的一種狀況,未斷裂的編織玻璃布纖維沒有完全被樹脂覆蓋。
1.1.1顯布紋可接受1,2,3級:顯布紋對于所有級別都可接受,但因其與露 織物相似的表面特征而很容易與之混淆。注:可用顯微剖切圖片作為顯布紋的佐證。
3)缺陷
(1)2,3級:表面損傷切入層壓板纖維。
(2)缺陷1,2,3級:露織物使導電圖形間距減小至最小電氣間隙以下。
2.IPC-6012C-2010
1)白斑
對于 1 級、2 級和 3 級產品,白斑都是可接受的。層壓板板基板中白斑面積大于相鄰導體間距的 50%時,對于 3 級產品是一種制程警示,說明材料、設備操作、工藝或制程出現變異,但不是缺陷。雖然應該將制程警示作為過程控制系統的一部分進行監控,但不要求對個別制程警示進行處置。且受影響產品應照常使用。
注:白斑是層壓板中的一種內部現象,再熱應力作用下它可能不會擴展,同時也無明確結論顯示它是導電陽極絲(CAF)生長的誘因。分層是一種在熱應力作用下可能擴展的內部現象,同時也可能是 CAF 生長的誘因。關于耐CAF 測試,IPC-9691 用戶指南和IPC-TM-650 測試方法 2.6.25 均提供了確定層壓板CAF 生長性能的其他信息。
2)微裂紋
如果微裂紋不會使導體間距減小至低于最小值,且沒有因為模擬組裝過程的熱測試而擴大,則對于所有級別產品均是可接受的。對于 2 級和 3 級產品,微裂紋的跨距不應當超過相鄰導體間距的 50%。
3)分層/起泡
如分層和起泡影響的區域未超過印制板每面面積的 1%,且其未使導電圖形的間距減小至低于最小導體間距,則對于所有級別產品均是可接受的。經過模擬組裝過程的熱測試之后,分層和起泡應當沒有擴大。對于 2 級和 3 級產品,分層/起泡的跨距不應當大于相鄰導電圖形間距的 25%。
3.GJB4896-2003
1)白斑
按下列要求判定:1、2、3級板接收狀況(見圖17):除用于高電壓產品外,白斑均可接收。
(2)1、2、3 級板接收狀況:
①1 、 2 、 3 級 板
a)缺陷未使導電圖形的間距減小低于最小導線間距。
b)經熱應力試驗后缺陷不擴大。
c)板邊緣的微裂紋不使板邊緣與導線的間距減小到低于規定的最小值:若未規定最小值,則間距應大于 2.5mm。
②2、3 級板,見圖 19:微裂紋區域不超過相鄰導線間距的 50%。
③1 級板,見圖 20:微裂紋區域超過相鄰導線間距的 50%,但不使相鄰導線間產生橋接。
(3)1、2、3 級板拒收狀況:缺陷超過上述情況。
3)分層/起泡
按下列要求判定:
(1)1、2、3 級板理想狀況,見圖 21:無分層和起泡。
(2)可接收狀況,見圖 22:
①1 、 2 、 3 級 板
a)每面受缺陷影響的面積不大于板面積的1%;
b)缺陷與最近導體的距離滿足規定的最小間距要求;
c)缺陷經過熱應力、模擬返工或熱沖擊試驗后不擴大;
d)缺陷與板邊的距離大于規定的最小值;若無規定,則大于 2.5mm;
e)由于增強粘接處理面出現的銅箔表面變色或雜斑現象。
②2、3 級板:
a)在相鄰導體或鍍覆孔之間的起泡或分層,不大于其間距的 25%; b)任何孤立缺陷的最大尺寸不大于 0.80mm;在非導電區域,缺陷的最大尺寸不大于 2mm 或印制板面積的 1%。
③1 級板
缺陷在導體之間,并大于其間距的 25%,但未在道題之間產生橋接。
(3)1、2、3 級板拒收狀況缺陷超過上述規定。
注:受影響的面積是由各缺陷面積的總和除以印制板的總面積來確定的。每面應單獨測量。
4.GJB362B-2009對白斑和微裂紋等的質量要求
1)斑點
理想情況下應無斑點。斑點若屬于下列情況可以接收:
(1)斑點是半透明的;
(2)斑點是顯布紋,而不是分層或分離
(3)孤立的斑點離導線的距離不小于 0.25mm。或經過任何焊接操作后不擴大(凝膠顆粒不管在任何位置均可以接收)。
2)白斑和裂紋
理想情況下應無白斑和裂紋。若屬于下列情況可以接收:
(1)若印制板不用于高電場,則白斑可接收;但白斑總面積應不大于印制板總面積的2%(兩面計算),任何方向的尺寸應不大于0.80mm;且不使相鄰導電圖形之間橋接;
(2)裂紋未使導電圖形的間距減小到低于布設總圖中規定的最小值;
(3)熱應力試驗后裂紋不擴大;
(4)板邊緣的裂紋不應使板邊緣與導線的間距減小到低于布設總圖中規定的最小值;若未規定最小值,則間距的減小應不大于 2.5mm;
(5)裂紋不應超過相鄰導線間距的 50%。
5.QJ831B-2011對白斑和微裂紋等的質量要求
1)白斑和裂紋
如果不用于高電場,多層板上的白斑和裂紋應不大于多層板總面積的2%,在內層導線間,應不大于該處間距的 25%,在任何方向上的尺寸應不大于 0.8mm。
2)表面下斑點表面下斑點符合下列條件時,應判為合格:
(1)當表面下斑點是半透明的,或確知為顯露布紋而不是分層和分離;
(2)孤立的斑點距導線的距離至少 0.25mm;
(3)經過任何焊接操作后不擴大
結束語 為提高產品設計和組裝焊接質量,實施可制造性設計和工藝過程控制是必不可少的。《高可靠印制電路板可接受條件》就是高可靠 PCBA 組裝焊接的前提。
我們應立足預防為主,在設計階段就對不同等級 PCB 的可接受條件作出明確規定,其中包括PCB 的驗收要求;例如軍品可以按照GJB362B 的規定進行PCB 的驗收,這樣就可以控制PCB 供貨的質量源頭。
在此基礎上,強化PCBA 組裝焊接工藝控制,就可以避免類似白斑、微裂紋、分層和起泡等質量問題的出現。
業內人士往往注重于各類分析,例如案例分析、質量分析、可靠性分析和缺陷分析等;這是不可少的,但總體上屬于“事后諸葛亮”。
各類分析的最終目的不是就事論事,而是要落實到預防為主的措施上來,這就是前面提到過的可制造性設計和工藝過程控制。
如果我們的印制板是按照GJB362B 驗收的,就可以排除PCB 貨源的問題。在組裝焊接中出現“白斑”的原因基本上是焊接溫度過高,例如軍品焊接無鉛BGA 時峰值溫度要達到 240℃,或手工焊接時實際焊接溫度過高,焊接時間過長,PCB 的玻璃化轉化溫度過低等,需要引起我們的注意 。
審核編輯:湯梓紅
-
pcb
+關注
關注
4319文章
23080瀏覽量
397511 -
半導體
+關注
關注
334文章
27290瀏覽量
218086 -
印制電路板
+關注
關注
14文章
954瀏覽量
40759 -
電路板
+關注
關注
140文章
4951瀏覽量
97689
原文標題:1)
文章出處:【微信號:現代電子裝聯工藝技術交流平臺,微信公眾號:現代電子裝聯工藝技術交流平臺】歡迎添加關注!文章轉載請注明出處。
發布評論請先 登錄
相關推薦
印制電路板PCB工藝設計規范
印制電路板設計規范
印制電路板設計規范-元器件封裝庫基本要求
印制電路板的設計基礎
印制電路板封裝要求
為什么叫印制電路板?印制電路板來由介紹
印制電路板設計心得體會_設計印制電路板的五個技巧
印制電路板的一般布局原則_印制電路板前景
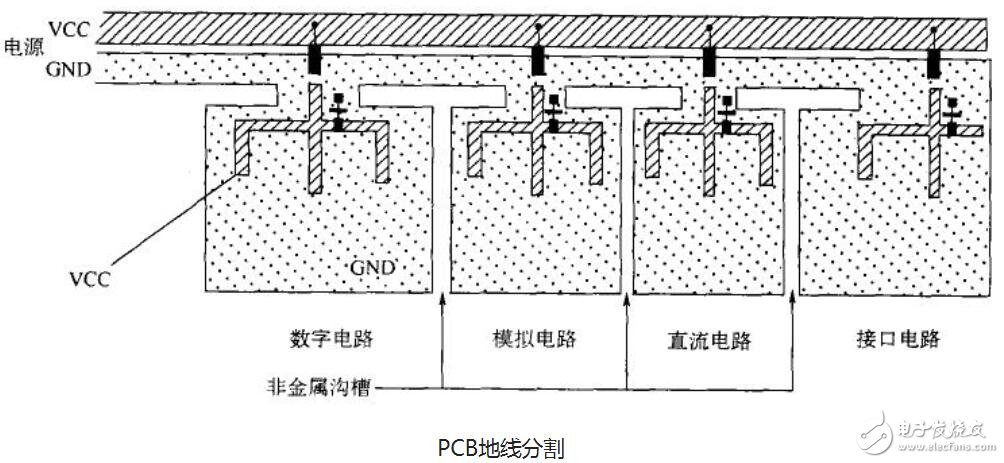
評論