隨著電動汽車行業的迅猛發展,各大廠商紛紛投入巨資進行技術研發和創新。電動汽車的核心之一在于其電池管理系統(Battery Management System, BMS),而BMS的心臟則是其印刷電路板(PCB)。通過這篇文章探討電動汽車BMS PCB的制造過程、技術挑戰以及可制造性(Design for Manufacturability, DFM)設計問題。
電動汽車BMS PCB的重要性
電動汽車的BMS負責監測和管理電池組的狀態,包括電池的充放電、溫度、電壓等,以確保電池的安全、高效運行。BMS的核心部件是其PCB,它不僅承載著各種電子元件,更是整個系統信息處理和傳遞的中樞。
BMS PCB的制造過程
1. 設計階段
設計階段是整個制造過程的基礎。這一階段需要考慮的關鍵因素包括:
電路設計:確保電路設計滿足功能需求,同時考慮信號完整性和電磁兼容性。
布局布線:合理布局可以減少信號干擾,提高PCB的性能和可靠性。
熱管理設計:電動汽車的BMS會產生大量熱量,因此需要考慮良好的散熱設計。
2. 印刷和制造階段
在PCB的印刷和制造階段,需要注意以下幾個關鍵因素:
材料選擇:高質量的基板材料對于確保PCB的長期穩定性至關重要。
精密加工:高精度的制造工藝可以保證電路板的質量和性能。
焊接質量:優良的焊接工藝對于確保電子元件穩定連接至PCB至關重要。
3. 測試與質量控制
制造完成的PCB需要經過嚴格的測試和質量控制,包括:
電氣測試:檢查電路的連通性和功能是否符合設計要求。
環境適應性測試:確保PCB能夠承受極端的溫度、濕度和振動等條件。
PCB可制造性設計問題
1. 尺寸和復雜度
挑戰:隨著電動汽車技術的進步,BMS PCB的功能變得更加復雜,這使得PCB的尺寸和布局設計變得更加困難。
解決方案:通過采用多層PCB設計,以及優化布局布線來解決這一問題。
2. 熱管理
挑戰:BMS PCB在運行過程中會產生大量熱量,不當的熱管理可能導致元件過熱,影響性能和可靠性。
解決方案:設計時應考慮散熱通道,使用高熱導率的材料,以及考慮合適的散熱器件。
3. 電氣安全
挑戰:在高電壓環境下,電氣安全成為一個重要考慮因素。
解決方案:采用足夠的絕緣距離,以及合適的絕緣材料來確保安全。
4. 信號完整性
挑戰:隨著電路的復雜性增加,保持信號的完整性變得更加困難。
解決方案:合理的布線和屏蔽,以及使用差分信號線設計。
5. 電磁兼容性
挑戰:電磁干擾(EMI)可能影響PCB的性能。
解決方案:設計時考慮EMI屏蔽,合理布局元件和布線。
結論
電動汽車BMS PCB的設計和制造是一個高度復雜且技術密集的過程。通過綜合考慮設計、材料選擇、制造工藝、以及測試和質量控制等多個方面,可以實現高性能、高可靠性的BMS PCB。隨著電動汽車技術的不斷進步,BMS PCB的設計和制造也將面臨更多新的挑戰和機遇。
-
電動汽車
+關注
關注
156文章
12067瀏覽量
231110 -
pcb
+關注
關注
4319文章
23080瀏覽量
397515 -
電池管理系統
+關注
關注
41文章
511瀏覽量
33356 -
bms
+關注
關注
107文章
996瀏覽量
65947
原文標題:電動汽車BMS PCB制板的技術分析與可制造性設計
文章出處:【微信號:FANYPCB,微信公眾號:凡億PCB】歡迎添加關注!文章轉載請注明出處。
發布評論請先 登錄
相關推薦
電動汽車BMS PCB設計的要點
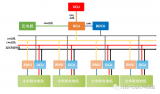
評論