共讀好書
首先,我們先了解一下,什么是功率半導體?
功率半導體包括兩個部分:功率器件和功率IC。功率器件是功率半導體分立器件的分支,而功率IC則是將功率半導體分立器件與各種功能的外圍電路集成而得來。功率半導體的功能主要是對電能進行轉換,對電路進行控制,改變電子裝置中的電壓和頻率,直流或交流等,均具有處理高電壓、大電流的能力。
目前主流、使用較多的半導體器件,一是晶閘管,它可以輸出較大功率,但頻率相對較低,主要用于直流輸電和大功率低頻電源等;二是IGCT,它是將GTO與門極驅動電路以低感方式集成在一起,這樣可以改善關斷性能,此器件目前主要用于大功率電機傳動,包括船舶驅動、海上風電等;三是IGBT,自上世紀90年代突破技術瓶頸以后,已經實現產業化和大規模應用,當前大功率IGBT最高可實現6500V,其應用方式較廣,包括軌道交通、光伏發電、汽車電子等,是當前主流開關器件。
IGBT模塊具有節能、安裝維修方便、散熱穩定等特點,它的作用是交流電和直流電的轉換,同時還承擔電壓高低轉換的功能,可以說是電動車的核心技術之一。IGBT的好壞直接影響電動車功率的釋放速度。
IGBT約占電機驅動系統成本的一半,而電機驅動系統占整車成本的15-20%,也就是說IGBT占整車成本的7-10%,是除電池之外成本第二高的元件,也決定了整車的能源效率。
新能源汽車對IGBT提出非常高的要求,要求其擁有更強大、更高效的功率處理能力,同時也要降低本身過多的電力消耗和不必要的熱量產生,以提高整車的性能。主要在溫度沖擊、功率循環、溫度循環、結溫等與全生命周期可靠性相關的一些方面提出了更高的標準。
作為新型功率半導體器件的主流器件,IGBT應用非常廣泛,如家用電器、電動汽車、鐵路、充電基礎設施、充電樁,光伏、風能,工業制造、電機驅動,以及儲能等領域。
IGBT模塊是新一代的功率半導體電子元件模塊,誕生于20世紀80年代,并在90年代進行新一輪的改革升級,通過新技術的發展,現在的IGBT模塊已經成為集通態壓降低、開關速度快、高電壓低損耗、大電流熱穩定性好等等眾多特點于一身,而這些技術特點正式IGBT模塊取代舊式雙極管成為電路制造中的重要電子器件的主要原因。
近些年,電動汽車的蓬勃發展帶動了功率模塊封裝技術的更新迭代。目前電動汽車主逆變器功率半導體技術,代表著中等功率模塊技術的先進水平,高可靠性、高功率密度并且要求成本競爭力是其首先需要滿足的要求。
功率器件模塊封裝結構演進趨勢
IGBT作為重要的電力電子的核心器件,其可靠性是決定整個裝置安全運行的最重要因素。由于IGBT采取了疊層封裝技術,該技術不但提高了封裝密度,同時也縮短了芯片之間導線的互連長度,從而提高了器件的運行速率。
按照封裝形式和復雜程度,IGBT產品可以分為裸片DIE、IGBT單管、IGBT模塊和IPM模塊。
1、裸片DIE:由一片晶圓切割而成的多顆裸片DIE;
2、IGBT單管:由單顆DIE封裝而成的IGBT分立器件,電流能力小,適用于家電等領域;
3、IGBT模塊:由多顆DIE并聯封裝而成,功率更大、散熱能力更強,適用于新能源汽車、高鐵、光伏發電等大功率領域;
4、IPM模塊:在IGBT模塊外圍增加其他功能的智能功率模塊(IPM);
IGBT被稱成為“功率半導體皇冠上的明珠”,廣泛應用于光伏電力發電、新能源汽車、軌道交通、配網建設、直流輸電、工業控制等行業,下游需求市場巨大。IGBT的核心應用產品類型為IGBT模塊。IGBT模塊的市占率能夠達到50%以上,而IPM模塊和IGBT單管分別只有28%左右和20%左右。從產品的投資價值來看,由于IGBT模塊的價值量最大,有利于企業快速提升產品規模,其投資價值最大。
IGBT 應用領域
實現IGBT國產化,不僅需要研發出一套集芯片設計、晶圓制造、封裝測試、可靠性試驗、系統應用等于一體的成熟工藝技術,更需要先進的工藝設備。
隨著芯片減薄工藝的發展,對封裝提出了更高的要求。封裝環節關系到IGBT是否能形成更高的功率密度,能否適用于更高的溫度、擁有更高的可用性、可靠性,更好地適應惡劣環境。
IGBT模塊封裝是將多個IGBT集成封裝在一起,以提高IGBT模塊的使用壽命和可靠性,體積更小、效率更高、可靠性更高是市場對IGBT模塊的需求趨勢。常見的模塊封裝技術有很多,各生產商的命名也不一樣,如英飛凌的62mm封裝、TP34、DP70等等。一個IGBT模塊的封裝需經歷貼片、真空焊接、等離子清洗、X-RAY照線光檢測、鍵合、灌膠及固化、成型、測試、打標等等的生產工序。
IGBT封裝工藝流程
IGBT模塊封裝流程簡介
1、絲網印刷:將錫膏按設定圖形印刷于散熱底板和DBC銅板表面,為自動貼片做好前期準備 印刷效果;
2、自動貼片:將IGBT芯片與FRED芯片貼裝于DBC印刷錫膏表面;
IGBT封裝環節包括:絲網印、貼片、鍵合、功能測試等環節。這其中任何一個看似簡單的環節,都需要高水準的封裝技術和設備配合完成。
例如貼片環節,將IGBT芯片與FRED芯片貼裝于DBC印刷錫膏表面。這個過程需要對IGBT芯片進行取放,要確保貼片良率和效率,就要求以電機為核心的貼片機具有高速、高頻、高精力控等特點。隨著新能源汽車行業的高速發展,對高功率、高密度的IGBT模塊的需求急速增加,很多汽車廠商都已走上了IGBT自研道路,以滿足整車生產需求,不再被上游產業鏈“卡脖子”。
要生產具有高可靠性的IGBT模塊,高精度芯片貼裝設備必不可少。
3、真空回流焊接:將完成貼片的DBC半成品置于真空爐內,進行回流焊接;
高質量的焊接技術,才能生產出高可靠性的產品。一般回流焊爐在焊接過程中會殘留氣體,并在焊點內部形成氣泡和空洞。超標的焊接氣泡會對焊點可靠性產生負面的影響,包括:
(1) 焊點機械強度下降;
(3)高頻器件的阻抗增加明顯;
4. 導熱性降低導致元器件過度升溫。
真空回流焊接工藝是在回流焊接過程中引入真空環境的一種回流焊接技術,相對于傳統的回流焊,真空回流焊在產品進入回流區的后段,制造一個真空環境,大氣壓力可以降到 5mbar(500pa)以下,并保持一定的時間,從而實現真空與回流焊接的結合,此時焊點仍處于熔融狀態,而焊點外部環境則接近真空,由于焊點內外壓力差的作用,使得焊點內的氣泡很容易從中溢出,焊點空洞率大幅降低。低的空洞率對存在大面積焊盤的功率器件尤其重要,由于高功率器件需要通過這些大面積焊盤來傳導電流和熱能,所以減少焊點中的空洞,可以從根本上提高器件的導電導熱性能。
4、超聲波清洗:通過清洗劑對焊接完成后的DBC半成品進行清洗,以保證IGBT芯片表面潔凈度滿足鍵合打線要求求。
5、X-RAY缺陷檢測:通過X光檢測篩選出空洞大小符合標準的半成品,防止不良品流入下一道工序;
6、自動鍵合:通過鍵合打線,IGBT芯片打線將各個IGBT芯片或DBC間連結起來,形成完整的電路結構。
半導體鍵合AOI主要應用于WB段后的檢測,可為IGBT生產提供焊料、焊線、焊點、DBC表面、芯片表面、插針等全面的檢測。
▲高精度還原線弧
7、激光打標:對IGBT模塊殼體表面進行激光打標,標明產品型號、日期等信息;
8、殼體塑封:對殼體進行點膠并加裝底板,起到粘合底板的作用;
9、功率端子鍵合
10、殼體灌膠與固化:對殼體內部進行加注A、B膠并抽真空,高溫固化 ,達到絕緣保護作用;
11、封裝、端子成形:對產品進行加裝頂蓋并對端子進行折彎成形;
12、功能測試:對成形后產品進行高低溫沖擊檢驗、老化檢驗后,測試IGBT靜態參數、動態參數以符合出廠標準 IGBT 模塊成品。
功率半導體模塊封裝是其加工過程中一個非常關鍵的環節,它關系到功率半導體器件是否能形成更高的功率密度,能否適用于更高的溫度、擁有更高的可用性、可靠性,更好地適應惡劣環境。功率半導體器件的封裝技術特點為:設計緊湊可靠、輸出功率大。其中的關鍵是使硅片與散熱器之間的熱阻達到最小,同樣使模塊輸人輸出接線端子之間的接觸阻抗最低。
IGBT模塊的封裝技術難度高,高可靠性設計和封裝工藝控制是其技術難點。IGBT模塊具有使用時間長的特點,汽車級模塊的使用時間可達15年。因此在封裝過程中,模塊對產品的可靠性和質量穩定性要求非常高。高可靠性設計需要考慮材料匹配、高效散熱、低寄生參數、高集成度。封裝工藝控制包括低空洞率焊接/燒結、高可靠互連、ESD防護、老化篩選等,生產中一個看似簡單的環節往往需要長時間摸索才能熟練掌握,如鋁線鍵合,表面看只需把電路用鋁線連接起來,但鍵合點的選擇、鍵合的力度、時間及鍵合機的參數設置、鍵合過程中應用的夾具設計、員工操作方式等等都會影響到產品的質量和成品率。
來源:芯片半導體實驗室
審核編輯 黃宇
-
封裝
+關注
關注
126文章
7894瀏覽量
142942 -
IGBT
+關注
關注
1267文章
3792瀏覽量
248994
發布評論請先 登錄
相關推薦
芯片封裝工藝集成工程師的必修課程指南
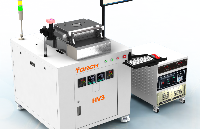
功率模塊封裝全攻略:從基本流程到關鍵工藝
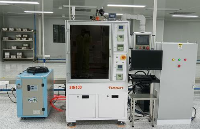
mos封裝工藝是什么,MOS管封裝類型
閑談半導體封裝工藝工程師
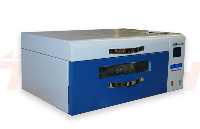
半導體封裝工藝面臨的挑戰
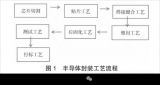
半導體封裝工藝的研究分析
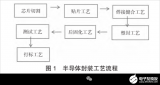
IGBT模塊的12道封裝制程工藝
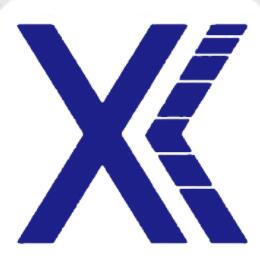
評論