共讀好書
陳婷 周偉潔 王濤
摘要:
研究了微波等離子工藝影響導電膠形貌的機理,進一步分析了等離子清洗次數對電路可靠性的影響。結果表明,對裝片后的電路進行 1 次等離子清洗可以有效清除鍵合指表面的有機沾污。而多次等離子清洗會改變導電膠的成分從而嚴重破壞導電膠形貌,容易造成塊狀的導電膠脫落,影響封裝的可靠性。研究多次等離子清洗對導電膠表面形貌、芯片粘接強度等的影響,為采用合理的等離子處理參數提供了一定的理論參考。
1 引言
陶瓷封裝作為一種高可靠的芯片封裝形式,在高可靠應用領域中具有不可替代的獨特優勢。封裝質量會直接影響元器件的可靠性和使用壽命 [1-2] 。在集成電路的裝片工藝過程中,對于采用合金焊料熔封的器件,需要采用耐受溫度超過 300 ℃的高溫導電膠將芯片和外殼底座粘接在一起。高溫導電膠主要由銀顆粒、氰酸脂樹脂、固化劑等物質組成 [3] 。在高溫固化過程中,液態的氰酸酯樹脂的黏度陡然下降,導電膠中的氰酸酯樹脂可能會擴散至鍵合指,造成電路外殼的鍵合指沾污。該沾污現象會影響鍵合可靠性,因此需要去除鍵合指上的有機沾污組分,防止對鍵合工藝造成不良影響 [4] 。
微波等離子清洗技術作為一種精密干法清洗技術,利用高能量的粒子與有機物之間的反應生成易揮發的小分子氣體產物,從而有效去除鍵合指表面的有機污染物,改善鍵合指表面性能,增加材料的表面能量 [5-6] 。與傳統溶劑清洗方式相比,等離子清洗有許多優點,如不污染環境、不需要清洗液體,能增加表面潤濕性能,改善黏著力 [7] 。因此,微波等離子清洗在電子封裝領域中具有重要作用。
目前,關于微波等離子清洗工藝對導電膠可靠性影響的研究還不充分。本文探究了在 1 次等離子清洗過程各階段導電膠結構的變化,對比了微波等離子清洗次數對導電膠微觀結構及電路可靠性的影響,并分析了多次清洗造成的電路失效的相應機理,為采用合理的等離子清洗參數提供了一定的理論參考。
2 試驗方案
微波等離子體是由工作頻率為 2.45 GHz 的微波激發工藝氣體放電,在正負極磁場作用下的諧振腔體內產生的等離子體。選用不同的工藝氣體可產生不同的活性等離子體,如 O 等離子體、H 等離子體。這些活性等離子體對被清洗物進行表面物理轟擊與化學反應雙重作用,使被清洗物表面生成粒子和氣態物質。將這些物質經過抽真空排出,從而達到清洗物質表面的目的。由于整個放電過程不需要正負電極,產生的自偏壓極小,從根本上避免了靜電損傷,因此微波等離子清洗技術適合于在半導體芯片封裝中應用 [8] 。本試驗中的微波等離子清洗過程包括氧化處理和還原處理 2 個步驟。經過試驗設計,確定了試驗的具體工藝參數:
1)氧化過程采用的工藝氣體為 O 2 ,設置微波等離子清洗功率為 800 W,清洗時間為 20 min,氣體流量為300 mL/min;
2)還原過程采用的工藝氣體為 H 2 ,設置微波等離子清洗功率為 800 W,清洗時間為 30 min,氣體流量為300 mL/min。
完成 1 次氧化過程和 1 次還原過程為 1 次微波等離子清洗循環。試驗人員分別對裝片后的電路進行 1次、2 次和 3 次微波等離子清洗循環處理,觀察芯片四周溢出的導電膠形貌變化,并與導電膠初始形態做對比。
3 試驗結果
3.1 微波等離子清洗過程對導電膠形貌的影響
微波等離子清洗過程中各階段導電膠的形貌如圖 1 所示。固化后的導電膠呈現典型的銀白色,表面較為致密且無明顯的孔洞,如圖 1(a)(d)所示。在氧化過程中,高能量的 O 等離子體一方面會與導電膠中的樹脂反應生成小分子易揮發物質,導致材料中的 C、O含量減少。導電膠中的高分子樹脂結構遭到破壞,導致導電膠表面出現少量的孔隙,如圖 1(e)所示。另一方面,有機物的消耗使得導電膠表層的銀顆粒裸露出來,會繼續和 O 等離子體反應生成黑色氧化銀,如圖 1(b)所示。氧化銀的電阻較大,因此需將銀的氧化物還原。在等離子的還原過程中,高能量的 H 等離子體與氧化銀中的 O 粒子結合,將黑色的氧化銀還原為銀白色的銀單質,如圖 1(c)所示。但導電膠還原后因體積膨脹造成的空洞無法復原,故在圖 1(f)中仍可看到明顯凹坑。
利用能量色散 X 射線光譜儀(EDX)分析導電膠在等離子清洗過程中各主要元素的含量,結果如表 1所示。在經過 1 次循環的微波等離子清洗后,導電膠中有機物中的 C 含量略有減少。這主要是因為在氧化過程中導電膠表層有機物中的 C、O 等與高能量的 O等離子體反應生成 CO、CO 2 等小分子物質 [9] ,這些氣態物質在清洗過程中采用抽真空方式排出。
綜上可知,導電膠經過 1 次等離子清洗處理后,膠體表面經歷了由淺變深再變淺的顏色變化。其表面形貌雖無明顯變化,但是由于表層少量有機物的損失,使得其致密的微觀結構出現少量孔隙。
3.2 微波等離子清洗次數對導電膠形貌的影響
經過不同循環次數的等離子清洗處理后的導電膠宏觀形貌如圖 2 所示。經過 2 次微波等離子循環清洗后的導電膠表面已經出現明顯的脫落區域。利用EDX 分析確認脫落物為導電膠。由于脫落的導電膠較少,在后續的吹掃過程中已經被完全去除,故未在電路內部發現剝落的導電膠。經過 3 次微波等離子循環清洗后的電路,其內部導電膠剝落區域顯著擴大,且有明顯脫落的塊狀導電膠。
除宏觀形貌的差異外,經過不同循環次數的等離子清洗處理后導電膠的微觀形貌差異也較大,如圖 3所示。經過多次等離子清洗處理后,導電膠表面逐漸由較為平整的狀態變為凹凸不平的狀態。進一步采用聚焦離子束設備(FIB)分析導電膠內部的結構,經過不同循環次數的等離子清洗處理后導電膠內部微觀形貌如圖 4 所示。導電膠的初始結構中含有大量的銀顆粒,這些銀顆粒之間通過具有高強度粘接性能的樹脂基體連接在一起,導電膠各區域的縱向界面都是致密的結構,因而可以保持結構穩定和較高的粘接強度 [10] 。經過 1 次微波等離子清洗處理后,導電膠的內部結構遭到破壞,被破壞的導電膠的厚度約為 1.5 μm,并且與下部的導電膠主體之間出現了界面區域。但是該界面區域不明顯,表層導電膠與未遭到破壞的導電膠之間仍然存在較多起到粘接作用的樹脂,因而也不容易脫落。通過圖 4(c)(d)可以看出,結構遭到破壞的導電膠厚度有顯著增加(從 1.5 μm增加至 10 μm 和15 μm),其結構也呈現出明顯的疏松多孔狀態。
初始狀態和經 3 次微波等離子清洗處理后的表層導電膠的熱失重曲線如圖 5 所示。初始狀態的導電膠在 200 ℃下的失重僅有 0.03%,在 350 ℃下的失重不超過 1%,表現出優異的耐高溫性。但是當溫度超過400 ℃后,材料的失重速率陡然上升。這是因為在該溫度下樹脂中的三嗪結構發生分解,破壞了導電膠交聯結構的完整性和穩定性 [11] 。經過 3 次微波等離子清洗處理后的導電膠在 500 ℃下僅有不到 1%的質量損失。這說明結構中已經基本不存在起到粘接作用的樹脂,導致表面結構脫落風險增加,從而出現圖 2(d)中導電膠脫落的現象。
3.3 多次等離子清洗處理后導電膠剝落的機理
在對導電膠表面進行多次 O 等離子體處理的過程中,由于在 1 次等離子清洗過程中導電膠表層的有機樹脂已經大部分被去除,形成了多孔結構——— 如圖4(b)所示—— — 再次進行等離子處理時,O 等離子體穿過多孔結構的空隙繼續與下層的導電膠進行反應,使得有機樹脂繼續消耗,導致多孔結構的厚度增加超過10 μm。導電膠經過多次的氧化還原后,起到粘接作用的樹脂基體已經基本上被全部氧化去除。銀顆粒與下層導電膠主體的結合強度降低,導致導電膠多孔結構在后續可靠性篩選過程中受到熱應力或機械應力的作用時可能發生脫落,形成片狀多余物,導電膠剝落的過程如圖 6 所示。
4 可靠性分析
對器件進行微波等離子清洗時,等離子體的氧化、還原作用區域主要集中于暴露在芯片周圍的區域。芯片的尺寸越大,暴露區域面積的占比越小 [11] 。而未暴露的導電膠被芯片遮擋,等離子清洗幾乎不會破壞芯片底部的導電膠,因此芯片的粘接強度并未下降。完成電路封裝后,針對經過不同次數等離子清洗處理的電路進行剪切力測試,發現芯片粘接強度無明顯變化。
由于經過多次微波等離子清洗后的導電膠表層結構疏松,在經歷溫度沖擊及機械應力時表層的導電膠將發生脫落,形成可移動的導電多余物。這種多余物會直接導致顆粒碰撞噪聲檢測試驗失效,并且帶來器件內部的互連短路風險。對于大尺寸芯片的貼裝工藝,裝片膠的使用量更多,鍵合引線更加密集,膠皮脫落會帶來更高的短路風險 [12] 。
5 結論
在微波等離子清洗過程中使用的高能量的 O 等離子體會與導電膠中的有機物反應,導致導電膠結構出現變化。導電膠經過 1 次微波等離子清洗后,雖然其成分和結構發生了輕微變化,但是未出現明顯的脫落現象,因此 1 次微波等離子清洗不會對電路的可靠性造成影響。在經過多次微波等離子清洗后,導電膠表層中起粘接作用的有機物會發生反應至完全消耗,
導致塊狀的導電膠脫落。脫落后的導電膠如果搭在鍵合絲上,會引起電路短路。隨著微波等離子清洗次數的增加,導電膠的粘接結構將發生更大改變,有可能影響器件在溫度循環、熱沖擊以及機械沖擊、振動等試驗后的可靠性,包括引起粘接強度、水汽等方面的惡化。此外,微波等離子清洗工藝參數(如氧化、還原時間及功率)對清洗后表面結構的影響還有待進一步的研究。
審核編輯 黃宇
-
等離子
+關注
關注
2文章
236瀏覽量
29927 -
微波
+關注
關注
16文章
1043瀏覽量
83682 -
導電膠
+關注
關注
0文章
100瀏覽量
11637
發布評論請先 登錄
相關推薦
[分享]LED導電膠、石英晶體導電膠、集成電路導電銀膠
有哪些因素會對導電膠的導電性能造成影響
關于導電膠點膠加工的應用和區別分析
導電膠和導電銀漿
RFID各向異性導電膠類型和可靠性
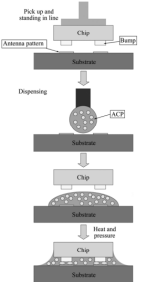
評論