共讀好書
王子伊 付明浩 張曉宇 王晶 王代興 孫浩洋 何欽江
摘要:
金絲鍵合技術是微電子領域的封裝技術,一般采用金線,利用熱、壓、超聲共同作用,完成微電子器件中電路內部連接,即芯片和電路或者引線框架之間的互連。本文在深入了解鍵合機理后,選用 25μm 金絲,基于正交試驗方法,研究鍵合壓力、超聲功率、鍵合時間等參數對楔焊鍵合及球焊鍵合后金絲拉力及焊點形貌的影響,根據鍵合強度拉力值確定鍵合的最佳工藝參數范圍。
1 引言
金絲鍵合作為集成電路封裝過程中的關鍵工序,用于完成集成電路封裝中芯片與基板、基板與殼體間的電氣互連。引線鍵合技術根據鍵合方法可分為楔形鍵合和球型鍵合。球焊鍵合方向靈活、可靠性高,楔焊鍵合可實現最小拱弧且單個焊點占用面積小,在集成電路封裝過程中均有應用。一個模塊中有大量金絲,一根金絲失效都會影響模塊甚至整機系統的正常運作,因此,控制并提高鍵合金絲質量尤為重要。金絲鍵合失效主要包括:金絲線弧過長引起的金絲塌陷短路、金絲過緊引起的頸縮點斷裂、鍵合參數過大引起的金絲焊點變形量從而引發的斷裂、鍵合參數過小引起的金絲焊點壓焊不牢。在實際生產中,鍵合參數對金絲質量的影響較大,因此,本文在深入了解鍵合機理后,選用 25μm 金絲,研究超聲功率、鍵合壓力、超聲時間對金絲拉力及焊點形貌的影響,確定最佳的工藝參數。
2 試驗方案
2.1 試驗材料的設計和選擇
本文選取純度為 99.99%的 25μm 的金絲作為鍵合引線材料進行金絲鍵合,如圖 1 所示。
本文選擇芯片焊盤尺寸為 100μm×160μm 的鋁焊盤,鋁膜厚為 600nm;鍍金 2μm 的介質基板為鍵合板材,研究不同工藝參數對金絲鍵合質量及一次鍵合成功率的影響,引線鍵合示意圖如圖 2 所示。
2.2 試驗方案
本文采用正交試驗方法研究工藝參數對鍵合金絲質量的影響。選取鍵合壓力、鍵合時間、超聲功率三個工藝參數作為試驗對象,每個參數選取 3 個變量,一共九組試驗。楔焊鍵合超聲功率選取 16~18W,鍵合壓力選取 14~16g,鍵合時間選取 60~100ms;球焊鍵合超聲功率選取 30~35μIn,鍵合時間選取 30~35ms,鍵合壓力選取 25~33g。鍵合金絲后對金絲焊點形態、金絲強度進行分析。應保證實驗前、高溫、低溫以及高低溫沖擊后,金絲抗拉強度均大于 5g。鍵合拉力測試示意圖如圖 3 所示,A 點為第一鍵合點脫落,B 點為第一頸縮點斷裂,C 點為金絲斷裂,D 點為第二頸縮點斷裂,E 點為第二鍵合點脫落,應當根據金絲斷裂位置進行相應的工藝參數調整。
3 金絲鍵合工藝參數研究
3.1 楔焊鍵合關鍵工藝參數研究
影響自動金絲鍵合質量的關鍵因素為:形變量,焊接過程中的超聲功率和鍵合時間。為了得到最佳鍵合工藝參數,本項目采用正交實驗,進行了三因素、三水平設計,鍵合金絲第一焊點參數具體設計方案如表 1 所示。
設置不同鍵合工藝參數,制備 9 組鍵合金絲樣品,并將 9 組樣品送去進行抗拉強度測試。每個樣品對 5根金絲進行測試,金絲抗拉強度及斷裂位置如表 2 所示。
9 種不同樣品測試結果表明,所測試的金絲抗拉強度最低為 8.85gf,最高為 10.41gf,強度均滿足GJB548B—2005 剪切試驗要求(大于 3gf),金絲鍵合質量良好。
金絲斷裂位置均發生在頸縮點處,未出現在第一、第二焊點斷裂的情況,說明金絲與芯片、基板形成了良好的冶金結合,鍵合質量良好。設計的正交試驗如表 3 所示。
通過對比各水平條件下極差數據可知:因素 B 形變量的極差 R 大于因素 C 超聲功率,大于因素 A 鍵合壓力,這說明在自動金絲鍵合過程中,對金絲鍵合第一焊點影響最大的工藝參數是形變量,其次是超聲功率,最后是鍵合時間。最佳的鍵合工藝參數 A1B3C1,即鍵合時間為 60ms,形變量 40%,鍵合壓力為 20g。
鍵合金絲第二焊點參數具體設計方案如表4所示。
設置不同鍵合工藝參數,制備 9 組鍵合金絲樣品,并將 9 組樣品送去進行抗拉強度測試。每個樣品對 5根金絲進行測試,金絲抗拉強度及斷裂位置如表 5 所示。9 種不同樣品測試結果表明,所測試的金絲抗拉強度最 低為 7.98gf , 最 高 為 9.79gf , 強 度 均 滿 足GJB548B—2005 剪切試驗要求(大于 3gf),金絲鍵合質量良好。
金絲斷裂位置均發生在第二焊點頸縮點處,未出現在第一、第二焊點斷裂的情況,說明金絲與芯片、基板形成了良好的冶金結合,鍵合質量良好。
設計的正交試驗如表 6 所示。通過對比各水平條件下極差數據可知:因素 B 形變量的極差 R 大于因素C 超聲功率,大于因素 A 鍵合壓力,這說明在自動金絲鍵合過程中,對金絲鍵合第一焊點影響最大的工藝參數是形變量,其次是超聲功率,最后是鍵合時間。最佳的鍵合工藝參數 A3B3C3,即鍵合時間為 120ms,形變量 40%,鍵合壓力為 22g。
自動金絲楔焊鍵合對金絲抗拉強度影響最大的工藝參數為形變量,當鍵合金絲形變量達到設定值時,繼續增大鍵合時間和超聲功率不會增加金絲與芯片或基板的接觸面積,即不再影響金絲的抗拉強度。綜上,自動金絲楔焊鍵合的最佳工藝參數如表 7 所示,采用最佳工藝參數進行自動金絲鍵合,一次鍵合成功率達到 100%,鍵合金絲形貌如圖 4 所示。
3.2 球焊鍵合關鍵工藝參數研究
金絲球焊鍵合操作方便、靈活,壓點面積大、焊接可靠性高,且無方向性,因此深入探討超聲功率、鍵合時間、鍵合壓力等參數對金絲球焊鍵合質量的影響十分必要。本試驗同樣采用三因素三水平 L 9 (3 3 )的正交試驗表進行試驗。球焊鍵合金絲第一焊點參數具體設計方案如表 8 所示。
設置不同鍵合工藝參數,制備 9 組球焊鍵合金絲樣品,并將 9 組樣品送去進行抗拉強度測試。每個樣品對 5 根金絲進行測試,金絲抗拉強度及斷裂位置如表 9 所示。
9 種不同樣品測試結果表明,所測試的金絲抗拉強度 最低 為 5.47gf , 最 高 為 6.81gf ,強 度均 滿足GJB548B—2005 剪切試驗要求(大于 3gf),金絲鍵合質量良好。金絲斷裂位置發生在第二焊點頸縮點,部分金絲第二焊點發生脫焊,這說明雖然金絲與芯片、基板形成了良好的冶金結合,但是第二焊點為薄弱環節,鍵合強度偏低。
設計的正交試驗如表 10 所示。
通過對比各水平條件下極差數據可知:因素 B 鍵合壓力的極差 R 大于因素 A 超聲功率,大于因素 C 鍵合時間,這說明在自動金絲球焊鍵合過程中,對金絲鍵合第一焊點影響最大的工藝參數是鍵合壓力,其次是超聲功率,最后是鍵合時間。最佳的鍵合工藝參數A1B1C3,即超聲功率為 31μIn,鍵合壓力為 32g,鍵合時間為 39ms。
從表 9 可以看出,金絲鍵合抗拉強度雖然滿足GJB548B—2005 剪切試驗要求,但是整體抗拉水平偏低,且第二焊點存在脫焊現象,說明第二焊點為薄弱環節,故需要對第二焊點進行補球加固,提高鍵合金絲可靠性。
球焊鍵合金絲補球參數具體設計方案如表 11 所示。
9 組球焊加固后鍵合金絲抗拉強度。每個樣品對 5根金絲進行測試,金絲抗拉強度及斷裂位置如表 12 所示。
9 種不同樣品測試結果表明,所測試的金絲抗拉強度最低為 11.11gf,最高為 12.28gf,強度均滿足GJB548B—2005 剪切試驗要求(大于 3gf),金絲鍵合質量較高。
金絲斷裂位置發生在第一焊點頸縮點、第二焊點頸縮點,未發生第一焊點脫焊以及補球脫焊等情況,這說明補金球參數適當,可將金絲第二頸縮點覆蓋住,起到了補球加固的效果。
設計的正交試驗如表 13 所示。
通過對比各水平條件下極差數據可知:因素 C 鍵合時間的極差 R 大于因素 A 超聲功率,大于因素 B 鍵合壓力,這說明在自動金絲球焊鍵合過程中,對金絲鍵合補球影響最大的工藝參數是鍵合時間,其次是超聲功率,最后是鍵合壓力。最佳的鍵合工藝參數A1B1C1,即超聲功率為 34μIn,鍵合壓力為 38g,鍵合時間為 29ms。
在補球過程中,鍵合時間過長、超聲功率過大、鍵合壓力過大均會導致金絲第二焊點頸縮點受到損傷,反而影響補球加固的效果。綜上,自動金絲球焊鍵合的最佳工藝參數如表 14 所示,采用最佳工藝參數進行自動金絲鍵合,一次鍵合成功率達到 100%,鍵合金絲形貌如圖 5 所示。
為確保最優的鍵合工藝參數能夠滿足產品的批生產要求,在產品裝配合格后隨機抽取 10 根金絲進行抗拉強度檢測,金絲抗拉強度值范圍為 9.07~12.21gf。批產試驗產品最優鍵合工藝參數可以滿足批產質量要求。
4 結束語
通過設計正交試驗,以抗拉強度與斷裂位置作為評價標準,研究了金絲楔焊鍵合及金絲球焊鍵合不同工藝參數對于金絲抗拉強度的影響,從而確定最優工藝參數。在楔焊鍵合中,形變量對鍵合強度影響大于超聲功率大于鍵合時間,最佳工藝參數為鍵合時間為60ms,形變量 40%,鍵合壓力為 20g,最佳工藝參數為鍵合時間為 120ms,形變量 40%,鍵合壓力為 22g;在球焊鍵合中,第一焊點鍵合壓力對鍵合強度的影響大于超聲功率大于鍵合時間,最佳工藝參數為超聲功率為 31μIn,鍵合壓力為 32g,鍵合時間為 39ms,補球過程中鍵合時間對鍵合強度的影響大于超聲功率大于鍵合壓力,最佳工藝參數為超聲功率為 34μIn,鍵合壓力為 38g,鍵合時間為 29ms。
審核編輯 黃宇
-
集成電路
+關注
關注
5420文章
12000瀏覽量
367654 -
封裝
+關注
關注
128文章
8607瀏覽量
145043 -
微電子
+關注
關注
18文章
399瀏覽量
41773 -
鍵合
+關注
關注
0文章
79瀏覽量
8072
發布評論請先 登錄
電機引線螺栓硬釬焊工藝研究
基于推拉力測試機的化學鍍鎳鈀金電路板金絲鍵合可靠性驗證
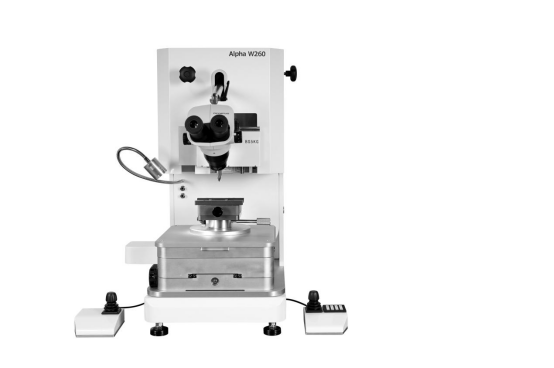
激光錫球焊工藝參數對焊接質量的嚴格把控
激光焊接技術在焊接殷瓦合金的工藝優勢
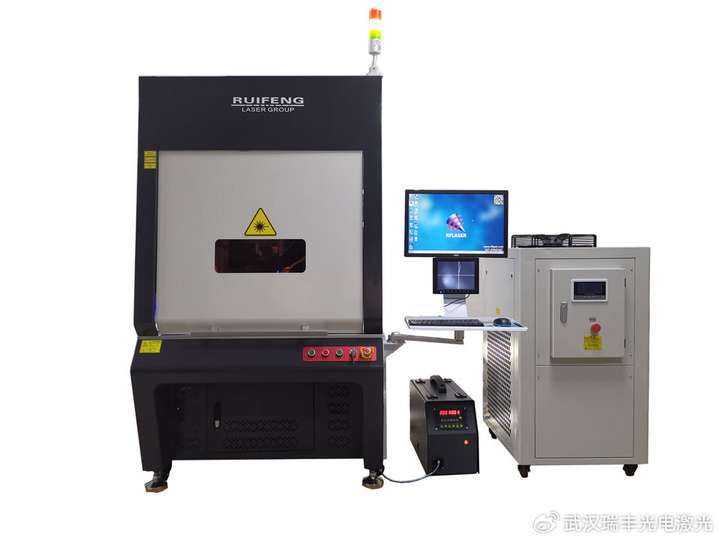
Phase Lab鎳基合金液相粘度數據庫:實現可靠粘度參數預測
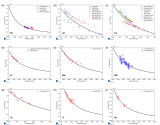
激光焊接技術在焊接鎳合金的工藝應用
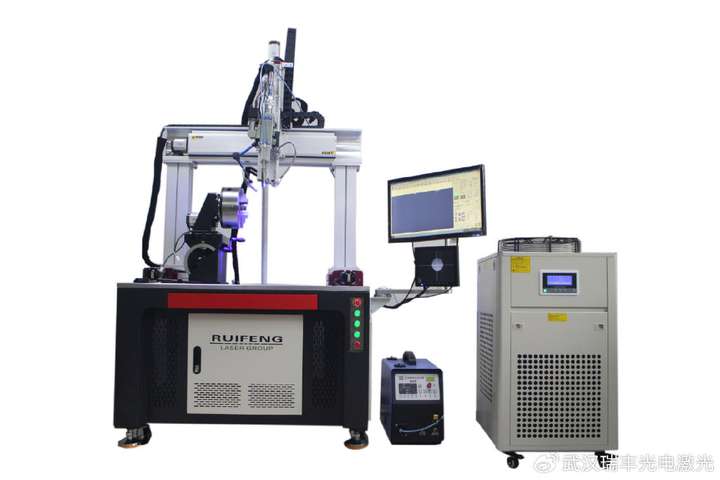
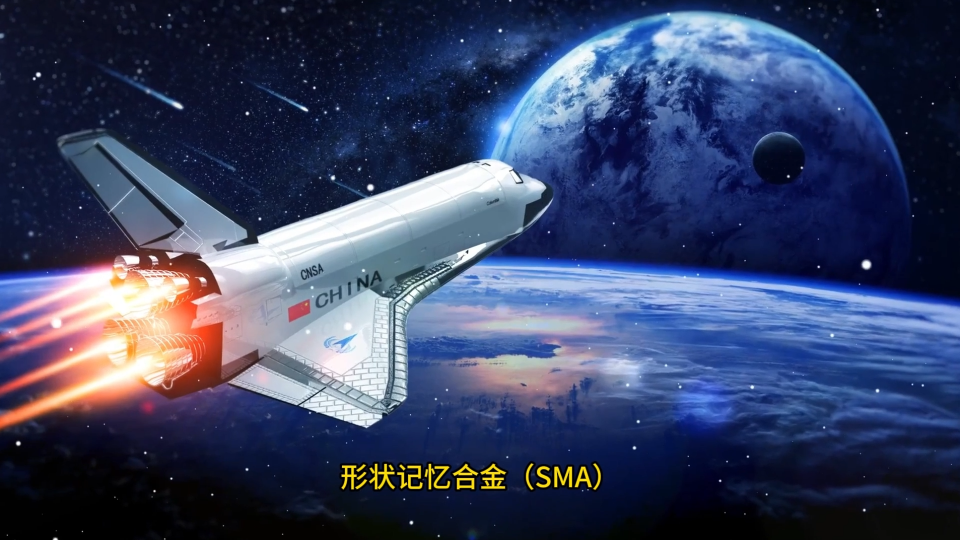
評論