共讀好書
高曉義 陳益鋼
(上海大學材料科學與工程學院 上海飛凱材料科技股份有限公司)
摘要:
在先進封裝的銅種子層濕法蝕刻工藝中,電鍍銅鍍層的蝕刻存在各向異性的現象。研究結果表明,在磷酸、雙氧水的蝕刻液體系中,因電偶腐蝕造成的凸點電鍍銅蝕刻量約為銅種子層蝕刻量的 4.9 倍。通過分析凸點上錫、鎳鍍層的能譜數據及蝕刻效果,發現該凸點結構中的錫、鎳鍍層表面存在鈍化層,導致錫、鎳鍍層的蝕刻量遠低于銅鍍層。在加入不同添加劑的蝕刻液中,通過絡合銅或破壞錫、鎳鍍層表面鈍化層的方法,均能達到抑制凸點上銅鍍層發生電偶腐蝕的效果。其中,復合型添加劑可以使凸點上銅鍍層的橫向蝕刻量降低約 82%,并且添加劑無殘留風險。
1 引言
隨著半導體產業的發展,先進封裝技術被廣泛應用于高性能消費電子產品。其中,晶圓級芯片尺寸封裝能夠通過制作扇入或扇出型銅再布線層(RDL)在晶圓表面排布更多的 I/O 端子,實現高密度、高集成度的互聯。凸點技術是在 IC 表面制作 I/O 端子的關鍵 [1] 。
在凸點技術工藝中,銅蝕刻液會同時接觸到凸點結構中的銅、鎳、錫、銀等多種金屬鍍層 [2] 。一般情況下,凸點結構中電鍍銅的橫向蝕刻速率要比濺鍍(PVD)銅的縱向蝕刻速率快。針對金屬蝕刻的各向異性問題,業界已經開展了一定的研究。邢攸美等人 [3] 對蝕刻液的化學組分進行了一系列的分析排查,并收集了改善各向異性蝕刻(指被蝕刻材料在橫向與縱向的蝕刻速率之間存在巨大差異的蝕刻)的添加劑種類。劉瑞豐等人 [4] 嘗試通過改變工藝條件來優化各向異性蝕刻的效果,并嘗試通過整合銅、鈦分步蝕刻工藝達到降低銅的橫向蝕刻量的目的。陳波等人 [5] 通過研究蝕刻工藝與蝕刻設備條件,優化了蝕刻工藝過程中銅蝕刻的均勻性,從而減少了蝕刻時間,進而降低銅的橫向蝕刻量。因此,針對電鍍銅蝕刻的研究工作主要是通過改善生產工藝與蝕刻液的蝕刻效果,以降低銅的橫向蝕刻量。
在銅蝕刻過程中,因為存在不同金屬結構的堆疊,且蝕刻過程均裸露在蝕刻液中,所以凸點結構與蝕刻液將形成微型的原電池。這種微型的原電池將造成凸點結構中電鍍銅鍍層的加速蝕刻。電鍍銅鍍層的加速蝕刻將造成凸點結構中電鍍銅鍍層尺寸的急劇收縮,進而降低凸點結構在封裝焊接中的可靠性。在銅蝕刻過程中,由于微型原電池的產生而造成的銅鍍層加速蝕刻的腐蝕現象一般稱為電偶腐蝕。該類研究很少聚焦多層異種金屬堆疊情況下發生的電偶腐蝕。
KEAR 等人 [6] 通過表征銅在電化學腐蝕過程中的陰陽極狀態,分析推導了在氯離子環境下的腐蝕電位特性,為研究多層金屬中的電偶腐蝕提供了一定的借鑒和參考。在電偶腐蝕研究中,大多傾向于研究宏觀結構的金屬部件的接觸腐蝕現象 [7-9] 。在半導體器件微
觀結構的制作過程中也具備了產生電偶腐蝕的條件,但因為微觀結構的尺寸過小,難以在凸點蝕刻研究中表征電偶腐蝕的影響。
本文旨在探討在先進封裝的銅蝕刻工藝中凸點結構的電鍍銅鍍層的電偶腐蝕過程,并分析其產生的原因,嘗試通過遴選合適的蝕刻液添加劑,抑制電鍍銅鍍層的電偶腐蝕,以達到提升封裝時凸點結構可靠性的目的。
2 實驗材料與方法
2.1 實驗材料
封裝工藝結構假片包含:PVD 鈦(厚度為 1000魡)、PVD 銅(厚度為 3 000 魡),以及圖形化的銅線與凸點結構。圖 1 為封裝工藝結構假片示意圖。
凸點結構的制作工藝流程:1)使用磁控濺射的方法在晶圓表面依次沉積金屬鈦、銅,為后續電鍍線路與結構凸點提供導電的種子層;2)使用光刻膠對需要電鍍沉積金屬的位置進行圖像化開口;3)依次進行銅、鎳、錫 / 銀合金等金屬層的電鍍(在進行錫 / 銀合金的電鍍時,銀的質量分數一般控制在 2%左右);4)去除光刻膠,得到實驗所需的晶圓。裁剪后,實驗晶圓的尺寸為 2 cm×2 cm。
蝕刻液的基本成分如下:質量分數為 8.5%的H 3 PO 4 ,質量分數為 4.5%的 H 2 O 2 ,其余成分為水。在此基礎上,添加一定量的鹽酸、苯并三氮唑、復合型添加劑來降低電偶腐蝕效應。
2.2 主要儀器與設備
實驗使用的主要儀器與設備如表 1 所示。
2.3 實驗方法
在燒杯中配置實驗所需的蝕刻液 100 g,加入襯四氟磁力攪拌子后,將燒杯放入水浴鍋進行控溫;將磁力攪拌子的轉速調節為 50~60 r/min,將水浴鍋的溫度控制在(23±0.5)℃進行樣片的浸泡實驗,使用塑料鑷子來固定裁剪好的晶圓(2 cm×2 cm)。該晶圓的蝕刻實驗使用秒表作為計時工具。圖 2 為浸泡實驗的裝置示意圖。
使用結構晶圓進行蝕刻實驗,設蝕刻結構假片時通過秒表記錄的蝕刻時長為 t 0 。結合實際生產中的工藝窗口需求,在蝕刻 2 倍的 t 0 時長后取出樣品。
使用掃描電子顯微鏡(SEM)拍照并測量樣品中的 RDL、凸點上電鍍銅鍍層的尺寸,分別用 D R 、D 表示蝕刻后的 RDL 中電鍍銅鍍層(RDL 銅)在水平方向的單側損失量和凸點上電鍍銅鍍層(凸點銅)在水平方向的單側損失量。PVD 銅鍍層(PVD 銅)的厚度 D 0 =
3 000 魡。
PVD 銅的平均蝕刻速率 v 0 為
RDL 銅與凸點銅的蝕刻速率分別為 v R 、v P ,v R 與 v P的計算式為
2.4 測量方法
用秒表測量蝕刻過程的時間,使用 SEM 測量蝕刻前后不同結構上金屬的尺寸變化和蝕刻后凸點結構的表面形貌,使用能譜儀(EDS)測量凸點結構表面的金屬元素組成。
3 實驗結果與討論
3.1 銅蝕刻中的電偶腐蝕實驗
電偶腐蝕產生有三個必要條件:1)材料具有不同的腐蝕電位,電偶腐蝕的驅動力是被腐蝕金屬與跟其產生電連接的高電位金屬或非金屬之間產生的電位差;2)存在離子導電支路,電解質必須連續地存在于接觸金屬之間,構成電偶腐蝕電池的離子導電支路;3)存在電子導電支路,即被腐蝕金屬與電位高的金屬或非金屬之間要么直接接觸,要么通過其他電子導體實現電連接,構成腐蝕電池的電子導電支路 [10] 。因此,凸點結構具備產生電偶腐蝕的基本條件。
使用銅蝕刻液進行銅蝕刻實驗,實驗數據以及通過式(1)(2)(3)計算所得的數據如表 2 所示。蝕刻前后凸點銅、RDL 銅與 PVD 銅的 SEM 形貌如圖 3 所示。從表 2 可以看出,凸點銅與 RDL 銅的蝕刻速率 v P 與v R 均高于 PVD 銅的蝕刻速率 v 0 。
從圖 3(b)(d) 可以看出,對比蝕刻后凸點銅與RDL 銅的表面形貌,RDL 銅有明顯的晶格感。從圖 3(f)可以看出,蝕刻后的 PVD 銅表面呈現類圓形微顆粒。由此可知,蝕刻后的凸點銅與 RDL 銅產生了更明顯的粗糙狀態,這將有利于在銅蝕刻過程中增大銅與蝕刻液的接觸面積,進而加快蝕刻速率。
基于表 2 數據,同為電鍍銅的情況下,凸點銅的蝕刻速率明顯高于 RDL 銅的蝕刻速率。對比凸點銅與RDL 銅的結構可知,凸點銅的上層接觸多種金屬結構。通過觀察蝕刻后的凸點銅形貌可以發現,越靠近上層金屬鎳時,凸點銅的尺寸收縮越大,即蝕刻速率越快,凸點銅的損失量為 3.68 μm。
根據凸點結構的制作過程可知,裸露在蝕刻液中的金屬元素分別為銀、錫、鎳和銅,通過電鍍的方式將錫、銀沉積在晶圓上,形成的是錫、銀混合金屬層,而非共晶的合金。在未經過熱回流時,錫、銀僅以物理堆疊的方式沉積在一起。在這種多層金屬結構的蝕刻作業中,非常容易產生電偶腐蝕,即鎳、錫、銀中的一種或幾種元素與凸點銅形成電偶腐蝕。
金屬按照電勢自低到高排序為鎳、錫、銅、銀。在電偶腐蝕過程中,高電勢金屬為陰極,且僅作為電極導通電子的傳遞,并不參與得失電子的反應 [10] 。
使用 SEM 對蝕刻后的晶圓進行定位,用 EDS 進行元素掃描,圖 4(a)為凸點上錫 / 銀元素的 EDS 譜圖,圖 4(b)為凸點上鎳元素的 EDS 譜圖。使用 EDS 掃描到錫 / 銀元素的位置(位置 1)和鎳元素的位置(位置2)如圖 4(c)所示。
根據 Apreo 2S 的技術參數,當電壓為 10 kV 時,SEM 在金屬表面的理論掃描深度為 100~500 nm。從圖 4(a)可以看出,錫元素的質量分數約為 98.6%,氧元素的質量分數約為 1.4%,未發現銀元素。從圖 4(b)可以看出,鎳元素的質量分數約為 99.7%,氧元素的質量分數約為 0.3%。
根據以上分析數據基本可以判斷,在錫 / 銀混合金屬層中未發現銀元素,這說明銀元素的分布與含量不足以響應 EDS 的掃描分析。由于 EDS 的分析結果只能定性判斷金屬表層的元素組成,并不能作為準確定量分析的依據。基于此分析數據,并以氧化錫、氧化鎳的元素組成作為表層氧化物質進行估算,錫、鎳元素在凸點結構表面的氧化深度應為 1~30 nm。結合蝕刻后的凸點形貌可以觀察到,凸點上存在錫元素與鎳元素的位置未有明顯的蝕刻反應。綜合分析以上數據及蝕刻現象,凸點上的錫、鎳元素在蝕刻過程中,符合張寶宏等人研究的金屬鈍化理論 [10] ,即凸點結構中的錫、鎳元素因在磷酸、雙氧水的蝕刻環境中產生了鈍化膜而未被腐蝕,所以在凸點結構的電偶腐蝕中未能參與陽極反應。
據此可以判斷,凸點結構中錫、鎳元素因鈍化作用,很難參與電偶腐蝕的陽極反應,主要是電鍍銅作為電偶腐蝕的陽極參與電偶腐蝕反應。所以此結構中,銀與銅分別作為陰極與陽極形成電偶腐蝕。凸點結構的電偶腐蝕機理如圖 5 所示。
3.2 蝕刻液中的添加劑對電偶腐蝕的影響
凸點結構中的電偶腐蝕是凸點銅產生加速蝕刻的主要原因。抑制凸點中電鍍銅的收縮,需要抑制電偶腐蝕的產生或改變電偶腐蝕的電流方向。
緩蝕劑對銅腐蝕的影響研究結果表明,苯并三氮唑(BTA)類含有 N、S、P 等極性基團或不飽和鍵的有機化合物可以與銅發生配位,從而形成[Cu(I)BTA]類的絡合膜層,該膜層可阻斷銅的腐蝕反應 [11-13] 。據此,可以通過添加對銅有絡合作用的物質,如 BTA 類物質,以減緩或阻礙電偶腐蝕過程中外部離子電路的導通,從而達到抑制電偶腐蝕的目的。
針對電偶腐蝕防護的方法,張文毓提出了陽極犧牲層的保護概念 [14] 。一些研究提出了改變陰陽極面積比例的概念 [15-16] 。改變電偶腐蝕的陽極種類或者減小陰陽極的面積比,可以分攤電偶腐蝕過程中銅的損傷或者降低陰陽極之間的電勢差。根據實驗結果,可以添加鹽酸等對錫、鎳氧化膜有破壞作用的物質,以達到破壞陰極或者轉移陽極的目的 [17-18] 。
此外,根據材料廠商提供的性能參數,復合型添加劑兼具以上兩種功能:一方面通過絡合吸附作用阻斷銅在電偶腐蝕中的離子傳導;另一方面減緩錫、鎳元素表面形成鈍化膜的速度,防止錫、鎳元素表面形成陰極,以達到抑制電偶腐蝕的目的。
選用苯并三氮唑、鹽酸以及飛凱材料提供的復合型添加劑進行蝕刻液配制,并進行蝕刻實驗。在遴選添加劑比例的實驗中發現,苯并三氮唑的添加量過高會導致蝕刻速率過低,無法完成對比實驗;添加量過低則起不到保護作用。鹽酸的添加量過高則會嚴重腐蝕錫、鎳層,破壞凸點的基本結構;添加量過低則達不到轉移陽極的目的。復合型添加劑的添加比例為材料商推薦的比例。據此,遴選合適的添加比例后,對蝕刻效果進行評估。此實驗所用的配方如表 3 所示。
根據第 2 節提出的實驗方法與計算方法進行數據收集,在進行蝕刻實驗后,使用 SEM 對蝕刻后的凸點進行拍照,實驗數據以及通過式(1)(2)(3)計算所得的數據如表 4 所示。使用不同配方的蝕刻液進行蝕刻后凸點的 SEM 形貌如圖 6 所示。
從圖 6 可見,相較于采用無添加劑的 1# 蝕刻液蝕刻后的凸點形貌,分別添加了三種添加劑的蝕刻液對凸點的電偶腐蝕均有抑制作用。復合型添加劑對電鍍銅的保護效果非常明顯。
根據 2# 蝕刻液的 v P 、v R 、v 0 可以看出,BTA 對抑制RDL 銅蝕刻與凸點銅蝕刻均有一定作用。使用 2# 蝕刻液蝕刻后的凸點形貌如圖 6(b)所示,通過添加銅絡合劑有利于保護電鍍銅,對抑制電鍍銅的電偶腐蝕有正向作用。
對比 2#、3# 蝕刻液的 D 發現,對錫、鎳鈍化膜有破壞作用的鹽酸,其抑制電偶腐蝕的作用比 BTA 更明顯。使用 3# 蝕刻液蝕刻后的凸點形貌如圖 6(c)所示,3# 蝕刻液抑制電鍍銅電偶腐蝕的效果比 2# 蝕刻液更明顯,但3#蝕刻液對錫、鎳表層有明顯腐蝕作用。
從 4# 蝕刻液的 v P 、v R 、v 0 可以看出,添加了復合型添加劑的蝕刻液在進行 RDL 銅蝕刻時,其 v R 低于v 0 ,這說明復合型添加劑對 v R 的抑制作用大于對 v 0 的抑制作用。使用 4# 蝕刻液時 v P 大于 v R ,說明復合型添加劑不能完全阻斷凸點銅的電偶腐蝕反應。使用4# 蝕刻液蝕刻后的凸點形貌如圖 6(d)所示,可以看出,復合型添加劑對電偶腐蝕的抑制效果最明顯。據此,為驗證復合型添加劑對電鍍銅的吸附效果以及對凸點結構表面的影響,對蝕刻后的晶圓進行 SEM 定位后使用 EDS 進行元素掃描。圖 7(a) 為回流前凸點銅的EDS 譜圖,回流前 EDS 掃描到凸點銅的位置(紅框位置)如圖 7(b)所示。
從圖 7(a)可知,凸點銅表面有碳、氮、氧、銅四種元素,碳元素的質量分數為 1.3%,氮元素的質量分數為 0.1%,氧元素的質量分數 0.3%,銅元素的質量分數為 98.3%,這說明 4# 蝕刻液中的添加劑在凸點銅表面可以吸附微量有機物。
為保證有機物不影響凸點與基板的后續焊接工藝,需保證凸點結構在金屬回流后,金屬表面吸附的添加劑可揮發或者升華。對使用 4# 蝕刻液蝕刻后的晶圓進行高溫回流處理,高溫回流溫度曲線如圖 7(c)所示,對回流后的凸點銅表面進行 EDS 掃描,EDS 掃描到凸點銅的位置(紅框位置)如圖 7(d)所示。根據圖7(c)的分析結果可以看出,在凸點銅表面不存在有機物殘留峰,即按照凸點工藝的常規條件處理后,可阻斷添加劑的有機物對凸點的污染。
4 結論
本文合理解釋了凸點銅在磷酸、雙氧水蝕刻液中存在的電偶腐蝕現象。凸點銅在此條件下的橫向蝕刻量可達 3.68 μm。相同條件下對比 RDL 銅的蝕刻量,因電偶腐蝕造成的橫向蝕刻量應為 2.94 μm。據此計算,電偶腐蝕造成的凸點銅蝕刻厚度約為 PVD 銅蝕刻厚度(0.3 μm)的 4.9 倍。
通過分析 EDS 數據、蝕刻后形貌可知,在磷酸、雙氧水的蝕刻環境中,凸點結構中的錫、鎳兩種金屬在蝕刻液中形成了具有保護作用的鈍化膜,致使錫、鎳元素在凸點的電偶腐蝕過程中得到保護。
使用具有絡合功能的苯并三氮唑作為添加劑,在添加質量分數為 0.1%的苯并三氮唑時,其對改善電偶腐蝕有明顯效果,相較于不含添加劑的蝕刻液,可降低凸點銅的橫向蝕刻量約 13%;使用對錫、鎳鈍化膜有破壞作用的鹽酸作為添加劑,在添加質量分數為0.2%的鹽酸時,經蝕刻后鎳、錫表層有明顯腐蝕跡象,降低凸點銅的橫向蝕刻量約 38%;添加質量分數為1%的復合型添加劑,蝕刻后凸點的錫、鎳表層結構完好,降低凸點銅的橫向蝕刻量約 82%,該蝕刻液表現最為優良。
對使用復合型添加劑蝕刻液蝕刻后的凸點進行回流工藝的可靠性驗證。使用 EDS 對凸點表面進行元素分析,并未發現其他元素的殘留。
近期成為熱點的芯粒(Chiplet)技術,是將多個具有特定功能的芯粒,通過先進封裝的形式組合在一起,最終形成一個系統芯片的過程。Chiplet 技術對先進封裝的工藝技術提出了新的挑戰。多芯片組合互聯過程所需的 RDL 銅線,在尺寸上會更小(線寬線距為1~2 μm),工藝過程所允許的 RDL 銅尺寸也將更小(0.2 μm 左右)。新技術的應用對蝕刻液提出了更高的要求。后續將針對復合型添加劑在銅表面吸附保護以及減緩錫、鎳元素形成鈍化膜的作用機理展開深入研究,可以為 Chiplet 技術的應用提供有效的蝕刻技術方案。
審核編輯 黃宇
-
半導體
+關注
關注
335文章
28970瀏覽量
239007 -
封裝
+關注
關注
128文章
8717瀏覽量
145631 -
電鍍
+關注
關注
16文章
469瀏覽量
24886 -
電偶
+關注
關注
0文章
50瀏覽量
15210 -
蝕刻
+關注
關注
10文章
424瀏覽量
16121
發布評論請先 登錄
用于 ARRAY 制程工藝的低銅腐蝕光刻膠剝離液及白光干涉儀在光刻圖形的測量
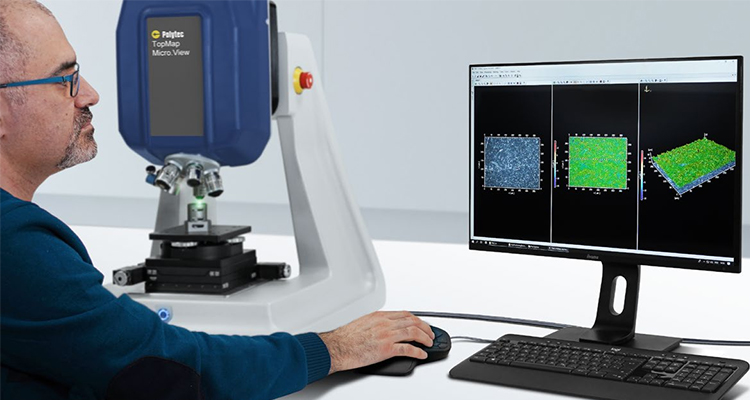
光刻工藝中的顯影技術
晶圓高溫清洗蝕刻工藝介紹
【「芯片通識課:一本書讀懂芯片技術」閱讀體驗】了解芯片怎樣制造
光刻工藝的主要流程和關鍵指標
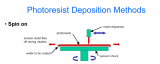
想做好 PCB 板蝕刻?先搞懂這些影響因素
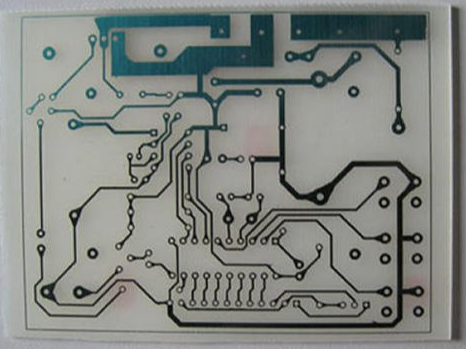
深入探討 PCB 制造技術:化學蝕刻
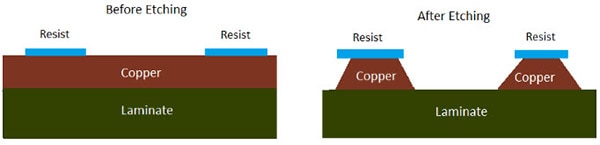
芯片濕法蝕刻工藝
光刻工藝的基本知識
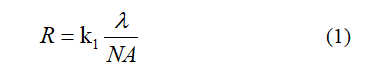
評論