實驗名稱:充粘液管道損傷檢測
實驗原理:在管道上的傳感器激發一束超聲能量脈沖,此脈沖沿著管道長度方向向遠處傳播,并充斥整個圓周方向,在導波傳播過程中遇到缺陷時,入射波會在缺陷處發生反射、透射,由同一傳感器接受到入射信號和缺陷回波信號,可得到接受到的入射波和缺陷反射回波的時間差?t。若導波傳播速度C(采用楊氏速度)已知,就可以估算出缺陷的位置。
缺陷的位置可由缺陷反射回波信號所被接受到的時間來確定,而缺陷的大小則有缺陷反射回波信號的強度來確定,當缺陷的裂紋越大,導波的缺陷反射回波就大,由此用反射系數來定量分析缺陷的大小。
圖a實驗裝置示意圖
首先通過計算機編程生成信號數據,通過USB接口發送到信號發生器,生成實驗所需的原始激勵信號。信號發生器通過ch1將原始激勵信號輸入數字示波器,又通過ch2將激勵信號經過功率放大器放大后,驅動與功率放大器連接的壓電陶瓷環,使之產生相應頻率的振動,在管道中激勵出超聲導波并在管道中傳播。最后經壓電陶瓷應變片接收后輸入數字示波器形成端面回波波形。
超聲導波的管道檢測實驗設備主要有信號發生器、功率放大器、傳感器、數字示波器以及計算機組成。實驗對象為一根4米長的鋼管,鋼管外徑為88毫米,壁厚為4毫米。實驗裝置示意圖如圖a所示。
測試設備:信號發生器、ATA-M4功率放大器、壓電陶瓷、示波器、鋼管
圖b實驗被測件
實驗過程:本實驗主要的研究內容為:(1)研究充粘性液體管道中超聲導波的傳播特性,并與充水管道和空管中超聲導波的傳播特性進行比對;(2)研究充粘性液體管道的超聲導波損傷檢測。在同一個一根長為4米,外徑為88毫米,壁厚為4毫米的鋼管上進行充機油、充水和空心鋼管實驗。擬定實驗步驟如下:
1、將壓電傳感器貼在管道上。在管道端部緊貼與管道截面相同的壓電陶瓷環激勵導波,離壓電環10mm處的管道外壁沿周向均布16個相同規格的壓電陶瓷片接受導波:沿管道長度方向,每隔25cm處的管道外壁沿周向均布6個壓電陶瓷片跟蹤記錄導波傳播信號。
2、將所有實驗儀器連接好后,進行完好空管實驗。激勵信號的頻率從100KHz到40KHZ每10KHz為間隔測量一次,周期數為10和20。
3、將管道豎立,向鋼管里注滿水,然后再平放管道進行完好的充水管道實驗。如圖3-2-8所示為測量結束后將鋼管中水放出。
4、將管道再次豎立,向鋼管里注滿機油,然后再平放管道進行完好的充機油管道實
5、進行有缺陷的充機油管道實驗。利用鋸弓在距離鋼管端部2m處加工三種缺陷,缺陷分別為環向1/8圓弧、環向3/16圓弧和環向1/4圓弧。對這三種缺陷分別進行超聲導波檢測。然后再將管中機油放出。
6、進行有缺陷的空心管道實驗。
7、進行有缺陷的充水管道實驗
實驗結果:通過對4米長無損傷充機油管道的超聲導波檢測,研究中心頻率與周期數對導波衰減程度、信號波峰值和單一模態激發的影響,來確定用來檢測有缺陷的充粘性液體的管道的超聲導波導波的最佳中心頻率。
在10周期不變的情況下,分別激發頻率40kHz、50kHz、60kHz、70kHz、80kHz、90kHz、100kHz的導波信號,如圖c至圖i所示。
圖c充油管道在10周期40kHz頻率下時程曲線圖
圖d充油管道在10周期50kHz頻率下時程曲線圖
圖e充油管道在10周期60kHz頻率下時程曲線圖
圖f充油管道在10周期70kHz頻率下時程曲線圖
圖g充油管道在10周期80kHz頻率下時程曲線圖
圖h充油管道在10周期90kHz頻率下時程曲線圖
圖i充油管道在10周期100kHz頻率下時程曲線圖
由圖c至圖i所示的導波的時程曲線圖可得到,10周期70kHz頻率導波的端面回波次數最多為六次,測其傳播距離最遠,并且激發出的模態數最少,適合在充粘性液體管道中超聲導波檢測。如圖d所示在10周期50kHz下導波的端面波次數為六次傳播距離也較遠,但其激發出的模態數較多,故不適合在充粘性液體管道中超聲導波檢測,當周期數為20時,其在時域信號的持續時間長,波形易疊加,折中取舍,選取10周期的信號進行實驗。
ATA-M4功率放大器是一款理想的單通道放大器。最大輸出345Vrms電壓,400VA功率,可驅動0~100%的阻性或非阻性負載。輸出阻抗匹配多個檔位可選,客戶可根據測試需求調節。
審核編輯 黃宇
-
功率放大器
+關注
關注
103文章
3993瀏覽量
135098 -
檢測
+關注
關注
5文章
4649瀏覽量
92948
發布評論請先 登錄
安泰電子ATA-105功率放大器的電子實驗案例(案例合集)
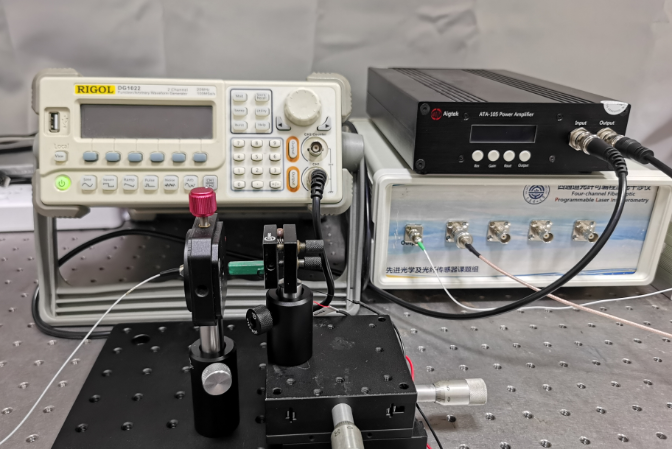
安泰電子ATA-3040功率放大器的電子實驗案例(案例合集)
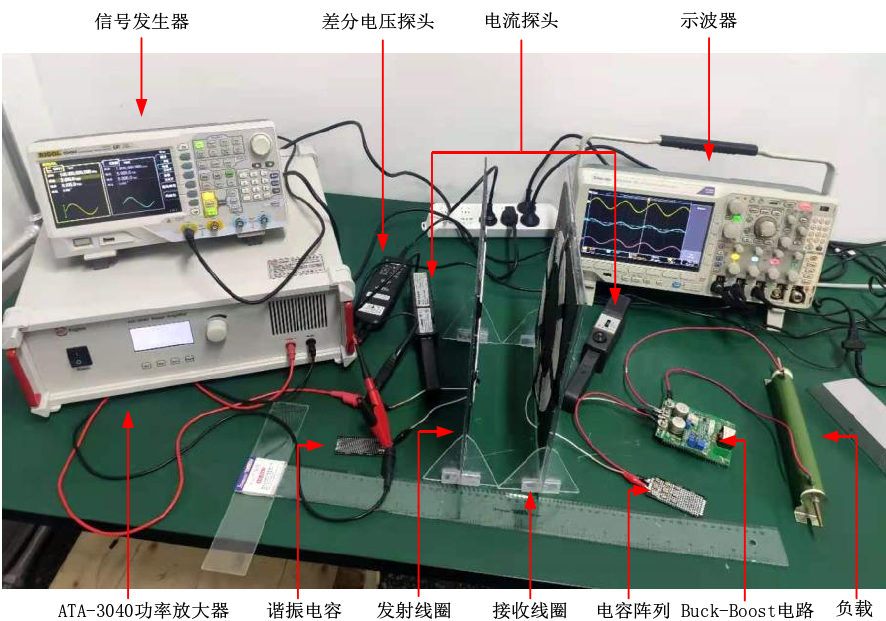
安泰電子ATA-3080功率放大器的電子實驗案例(案例合集)
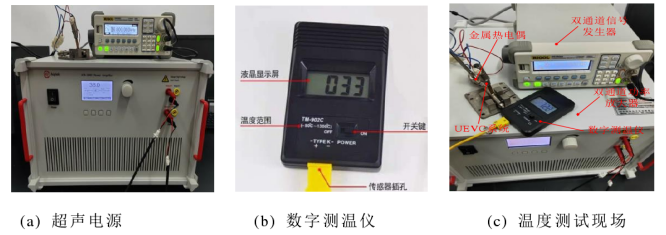
評論