一、解決方案概述
本解決方案旨在利用深控技術研發的 “不需要點表的工業網關”,實現對 PLC(可編程邏輯控制器)、CNC(計算機數字控制機床)和 SCADA(數據采集與監視控制系統)設備的數據采集,為工業生產過程中的監控、管理和優化提供有力支持。該工業網關具有獨特的優勢,能夠自動識別設備的通信協議和數據格式,無需繁瑣的點表配置,大大簡化了數據采集的過程,提高了系統的部署效率和穩定性。
二、實現方式
(一)PLC 數據采集
連接方式
通過以太網、串口等常見的通信接口將 “不需要點表的工業網關” 與 PLC 設備進行物理連接。確保連接穩定可靠,通信線路符合工業標準要求,以防止數據傳輸過程中的干擾和丟失。
自動識別與適配
工業網關啟動后,會自動掃描并識別所連接的 PLC 型號及其通信協議。利用其內置的智能算法,無需人工設置點表,即可快速適配 PLC 的數據結構,實現對 PLC 內部各種數據寄存器(如輸入寄存器、輸出寄存器、中間繼電器、數據寄存器等)的自動識別和數據采集。
數據傳輸
采集到的 PLC 數據經過加密處理后,通過網絡(有線或無線)傳輸到指定的上位機系統或數據中心。支持實時傳輸和定時批量傳輸兩種模式,可根據實際需求進行靈活配置,以滿足不同應用場景對數據及時性和帶寬資源的要求。
(二)CNC 數據采集
接口對接
對于具備以太網接口的 CNC 設備,直接使用網線將工業網關與 CNC 設備相連。對于一些老舊型號僅支持串口通信的 CNC 設備,可通過串口轉以太網模塊將其轉換為以太網接口后再與工業網關連接。
協議解析
工業網關針對常見的 CNC 通信協議,如 Fanuc FOCAS、Siemens Sinumerik 840D 等,進行內置協議解析。能夠自動識別 CNC 設備的運行狀態、加工參數(如切削速度、進給量、主軸轉速等)、刀具信息、工件坐標等關鍵數據,無需人工干預點表配置,實現高效準確的數據采集。
數據整合與傳輸
將采集到的來自不同 CNC 設備的多源數據進行整合和標準化處理,使其符合統一的數據格式。然后通過可靠的網絡傳輸通道,將處理后的數據發送到上層的生產管理系統或數據分析平臺,以便進行進一步的加工分析和決策支持。
(三)SCADA 數據采集
系統集成
將 “不需要點表的工業網關” 作為 SCADA 系統與底層設備(包括 PLC、CNC 等)之間的中間橋梁進行集成。工業網關通過與 SCADA 系統的通信接口(如 OPC UA、Modbus TCP 等)進行連接,實現數據的雙向傳輸。
數據匯聚與轉發
工業網關從底層設備采集到的數據,按照 SCADA 系統要求的格式和協議進行重新封裝后,實時轉發給 SCADA 服務器。同時,也能夠接收 SCADA 服務器下發的控制指令,并將其準確無誤地傳送到相應的設備,實現對設備的遠程控制和監控。
數據緩存與斷點續傳
考慮到網絡穩定性可能對數據傳輸造成的影響,工業網關具備數據緩存功能。在網絡中斷時,將采集到的數據臨時存儲在本地緩存中,待網絡恢復后,自動進行斷點續傳,確保數據的完整性和連續性,不丟失任何重要的生產數據。
深控技術——不需要點表的工業網關
三、應用案例
案例一:機械加工車間智能化升級
項目背景
某機械加工車間擁有多臺不同品牌和型號的 CNC 機床,以及用于車間設備控制和管理的 PLC 系統。過去,車間對設備運行數據的采集和管理主要依靠人工記錄和定期巡檢,存在數據不準確、不及時以及無法實時監控設備狀態等問題。為了提高生產效率、降低設備故障率、優化生產工藝,車間決定進行智能化升級,引入數據采集與分析系統。
解決方案實施
在每臺 CNC 機床和 PLC 設備處安裝深控的 “不需要點表的工業網關”。網關通過自動識別和適配設備的通信協議,成功采集了 CNC 機床的加工參數、運行狀態、刀具壽命等數據,以及 PLC 系統控制的設備開關量、模擬量等信息。
將采集到的數據傳輸到車間的本地服務器上,搭建了一套基于大數據分析的生產管理系統。該系統對數據進行實時分析和可視化展示,生產管理人員可以通過電腦或移動終端隨時查看設備的運行情況、生產進度、加工質量等關鍵指標。
當設備出現異常時,系統會自動發出報警通知,并通過短信或郵件的方式推送給相關維修人員。同時,系統根據歷史數據和實時數據分析,為設備維護提供預測性建議,提前安排設備維護計劃,減少設備突發故障對生產的影響。
應用效果
實現了對車間設備的實時監控,設備故障率降低了 [X]%。通過對加工參數的實時優化,產品加工精度提高了 [X]%,廢品率降低了 [X] 個百分點。生產管理人員能夠根據準確的生產數據及時調整生產計劃,車間整體生產效率提高了 [X]%。
案例二:自動化生產線的高效運維
項目背景
一家電子制造企業的自動化生產線由多個環節組成,每個環節都配備了 PLC 控制器來實現設備的自動化運行,同時生產線還配備了 SCADA 系統用于對整個生產過程進行監控和管理。然而,由于生產線中設備種類繁多,通信協議不一致,導致數據采集和系統集成難度大,SCADA 系統無法實時準確地獲取設備的運行數據,影響了生產效率和質量的提升。
解決方案實施
在生產線的各個關鍵節點部署深控的 “不需要點表的工業網關”。網關自動識別并連接了不同品牌和型號的 PLC 設備,實現了對設備數據的快速采集和整合。同時,網關與現有的 SCADA 系統進行無縫對接,通過標準化的數據接口將采集到的數據實時傳輸給 SCADA 服務器。
在 SCADA 系統中,對數據進行了進一步的分析和處理,開發了一系列的監控界面和報表功能。生產管理人員可以直觀地了解生產線的運行狀態、設備性能指標、生產產量等信息,并能夠根據數據分析結果及時調整生產參數和優化生產流程。
通過工業網關的遠程管理功能,技術人員可以在遠程對設備進行監控和維護。當設備出現故障時,能夠快速定位故障原因并進行遠程診斷和修復,大大縮短了設備停機時間,提高了生產線的整體運維效率。
應用效果
解決了生產線數據采集和系統集成的難題,SCADA 系統的數據準確性和實時性得到了顯著提高。設備停機時間減少了 [X] 小時 / 月,生產線的生產效率提高了 [X]%。通過對生產數據的深度分析,優化了生產工藝,產品質量合格率提升了 [X] 個百分點,為企業帶來了顯著的經濟效益。
案例三:能源管理與優化的工業應用
項目背景
某工業園區內有多家企業,涉及多種工業生產領域,包括機械制造、化工、食品加工等。園區內的企業普遍存在能源消耗大、能源管理粗放的問題,缺乏對能源數據的實時監測和分析,難以實現能源的優化利用和成本控制。為了提高園區的能源管理水平,降低能源消耗成本,決定建立一套能源管理系統。
解決方案實施
在園區內各企業的主要能源消耗設備(如電機、變壓器、鍋爐等)上安裝 PLC 控制器,并通過 “不需要點表的工業網關” 將其接入能源管理系統。網關自動采集 PLC 控制器中的能源數據,包括電能消耗、用水量、燃氣用量、蒸汽壓力和溫度等參數。
對于一些具有智能通信接口的能源計量儀表(如智能電表、水表等),工業網關也能夠直接與之通信,獲取更加準確和詳細的能源數據。同時,網關將采集到的能源數據上傳到園區的能源管理中心服務器,搭建了基于云計算和大數據分析的能源管理平臺。
在能源管理平臺上,對園區內各企業的能源數據進行實時監測、分析和統計。通過數據分析,發現能源消耗的高峰時段和低谷時段,以及能源浪費的環節和原因。根據分析結果,為企業制定了個性化的能源優化策略,如調整設備運行時間、優化生產工藝、加強能源設備的維護管理等。
應用效果
實現了園區內能源數據的實時采集和集中管理,企業對能源消耗情況有了更加清晰的認識。通過能源優化策略的實施,園區整體能源消耗降低了 [X]%,能源成本節約了 [X] 萬元 / 年。同時,企業的環保意識和能源管理水平得到了顯著提高,為可持續發展奠定了堅實的基礎。
通過以上三個應用案例可以看出,深控技術研發的 “不需要點表的工業網關” 在 PLC、CNC、SCADA 數據采集中具有顯著的優勢和廣泛的應用前景,能夠為不同行業的工業企業提供高效、可靠的數據采集解決方案,助力企業實現數字化轉型和智能化發展。
審核編輯 黃宇
-
plc
+關注
關注
5032文章
13872瀏覽量
473668 -
數據采集
+關注
關注
40文章
7116瀏覽量
116239 -
SCADA
+關注
關注
6文章
280瀏覽量
37638 -
CNC
+關注
關注
8文章
371瀏覽量
36908 -
工業網關
+關注
關注
0文章
474瀏覽量
12178
發布評論請先 登錄
深控技術不需要點表的工業網關物聯網數據采集解決方案“遠程管理+智能預警”,重塑設備運維模式
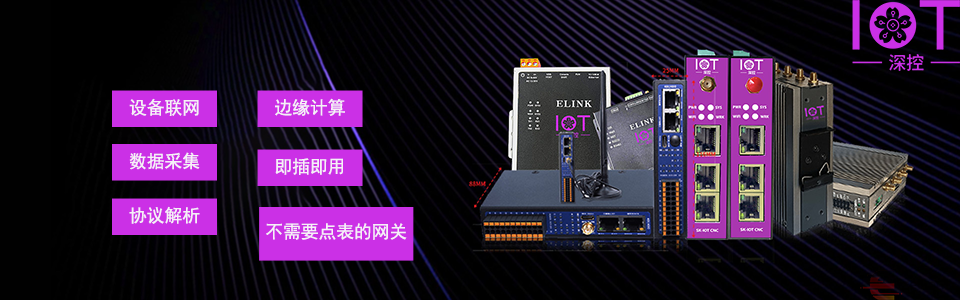
“不需要點表的工業網關” 在工業數據采集的成功應用
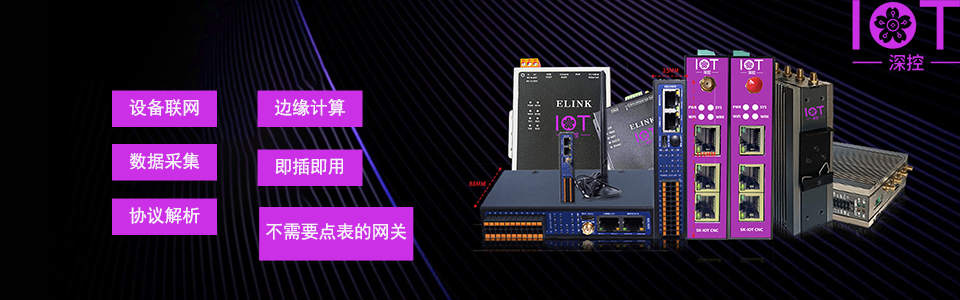
評論