針對傳統機械潤滑設備存在的高能耗、勞動強度大、結構復雜及智能化程度低等問題,本文設計了一款基于STM32F407控制核心、esp8266無線Wi-Fi通信模塊和KQ330電力載波模塊的集中潤滑系統。
該系統集成了潤滑供電電路、人機交互界面、無線通信電路、通信協議及手機APP等設計。實驗結果表明,該潤滑系統具備移動端APP監控、潤滑可靠性高、潤滑精確度高及操作簡便等優點,能夠有效滿足現代機械的潤滑需求。
引言
機械設備的潤滑是一項重要工作,合理地應用潤滑技術,保障設備正常運行,是鋼鐵冶金、大型礦山、電力等大型工業設備正常運行的基礎。
目前國內使用的集中干油潤滑系統多采用雙線式集中澗滑系統和單線遞進式集中潤滑系統。雙線式潤滑系統結構復雜,系統一旦出現故障,故障點不易判斷,維修較困難;而單線潤滑系統供油量有限,只適用于小型的潤滑系統,不能滿足結構復雜、潤滑精度要求高、潤滑點較多、通信要求高的大型機械設備的潤滑要求。
隨著電子、微機技術以及物聯網技術的飛速發展,不僅為集中潤滑系統提供了新的思路,同時也對集中潤滑系統提出了新的要求。本文采用電力線作為現場通信介質,結合嵌入式和物聯網技術,設計了一套智能集中潤滑系統。
系統總體設計
本系統總體框架結構如圖1所示,主要包括四大部分,分別是底層、中間層、網絡層、云端應用層。
底層
該層為潤滑系統的最底層,主要由供油終端控制器STM32F407和執行機構及各種傳感器組成。供油終端控制器通過電力載波模塊接收并處理主控制器發送的命令,控制執行機構的動作,并將運行狀態反饋到主控制器。
由于終端控制器的存在,使得每個潤滑節點都具有獨立運算、控制的能力,減輕了主控制器的負擔,提高了系統的可靠性。同時供油終端控制器能夠通過各種傳感器監測節點的運行狀態,當出現某種故障的情況下,能夠發出聲光警報,并向主控器發送故障信息。
圖1 控制系統總體框架結構圖
中間層
主要由STM32F407和ESP8266 WiFi模塊組成,STM32F407作為控制核心,通過ESP8266WiFi模塊進行聯網。主控制器接受上層和底層潤滑節點的數據,主控制器通過WiFi模塊與智能手機通信,通過電力載波模塊與終端控制器通信,主控制器的主要作用是:給各個帶有載波通信芯片的終端控制器發出控制指令,查詢檢測數據,按照要求生成各種數據報表,通過觸摸屏監控潤滑系統運行狀態,將潤滑系統中的信息上傳到上位機,并能通過觸摸屏調整工作參數、切換工作模式等。
網絡層
通過WiFi把數據上傳到機智云平臺。
云端應用層。
云平臺采用免費的機智云平臺,使用機智云平臺能夠大大縮短開發周期。使用前WiFi模組需燒寫GAgent固件(機智云為硬件接入提供的運行于通信模組等環境的嵌入式固件系統),使得WiFi模塊主動連接機智云服務器,實現與云端的TCP/UDP通信。同時通過GAgent還能實現設備與手機APP進行通信,可以實時監測整個系統的運行狀況。
硬件設計
硬件系統主要包括電源電路、中央處理器電路、電力載波控制電路、無線控制電路、數據存儲電路和終端顯控電路等。電路控制系統采用模塊化設計,便于設計和檢測各個模塊的功能。系統硬件結構框圖如圖2所示。
STM32F407ZGT6控制模塊
本文采用基于ARM-Cortex-M4的STM32F407Z GT6微控器作為主控芯片設計開發集中潤滑系統,其中主控制器和供油終端控制器均采用STM32F407ZGT6。
該控制器是意法半導體公司(STMicroelectronics)開發的一款高性能微控制器,具有功耗低、存儲空間內存大、處理速度快等優點。STM32F407微控器支持FPU(Floating Point Unit)和DSP(Digital Signal Processing)指令,極大地提高了浮點數運行能力,可以較為輕松地處理復雜的大型控制算法。
供電模塊
穩定的電源輸入是系統正常工作的基本保障。尤其是在工業現場干擾因素較多,對供電模塊的可靠性和穩定性要求更為嚴格。對整個系統而言,由于各個模塊所需的電壓不盡相同,STM32控制器供電電壓為3.3 V,通信模塊需要的供電電壓為5 V,繼電器需要24 V的電壓,因此需要供電模塊能同時提供這3種電壓。
本系統的電力載波通信介質為220 V電力線,為了得到24 V電壓,這里我們選用市場上較為成熟的開關電源來實現220 V到24 V電壓的轉換,然后利用LM2596V-5.0 V得到穩定的5 V電壓。使用AMS1117-3.3穩壓芯片為STM32F407提供穩定的3.3V電壓,該芯片內部集成過熱保護電路和限流電路確保電壓的穩定性。供電電路設計如圖3和圖4所示。
圖2 系統硬件結構框圖
圖3 24V-5V電壓電路
圖4 5 V-3.3V電壓電路
串口WiFi模塊
ESP8266串口WiFi模塊具有體積小、功耗低、使用靈活等特點。內置的TCP/IP協議棧能把串口信號通過WiFi無線發射。ESP8266無線串口模塊通過燒寫GAgent固件可以實現與手機APP的通信。串口WiFi與主控芯片接口電路如圖5所示。
0R20、R21可以避免誤觸發,減小高頻干擾信號。RT9193-33可以接收2.5~5.5 V寬電壓輸入,通過該穩壓芯片可以為ESP8266模塊提供穩定的電壓。
電力載波模塊
電力載波模塊電路主要包括:電力載波核心處理器KQ300、過零檢測電路、功率放大電路、濾波電路和載波耦合電路等。KQ330F模塊的供電電壓為5 V,與單片機連接比較簡單,只需將RX、TX腳與單片機TX、RX腳相連。工作時RX接收單片機串口發送過來的數據經過內部調制AC腳發出,加載到電力線上。從電力線上傳過來的載波信號經過解調從TX發送到單片機上,從而實現了信號在電力線上的傳送。KQ330**電路圖如圖6所示。
軟件設計
手機APP的設計主要利用機智云提供的較為完善的APP框架,通過Android Studio平臺運用Java語言進行開發整合,添加和修改所需的功能。而主控模塊和終端控制器程序的編寫主要用Keil5軟件完成。
通信協議設計
采用電力載波模塊KQ130F進行工業現場潤滑節點的組網。根據載波模塊用戶手冊可知,KQ130F模塊的主要功能是實現數據轉發,沒有自己的通信協議,為了實現各模塊間數據的交互,要對通信協議進行設計。
本系統設計通信協議包括起始標記、目的地址、源地址、命令、數據、校驗碼、結束標志7個部分,幀信息為14個字節,其通信協議格式如表1所示。為了實現網絡通信,每一個供油終端控制器都被分配了唯一8位地址,同時供油終端下的每一個潤滑點也分配了唯一8位地址,主控器地址被分配為0地址。
本系統設計的通信協議能夠實現潤滑系統的單播、組播和廣播。當主機向從機發送命令時,把字節2的最高位設為單/廣標志和單/組播標志,1為廣播或組播,0位單播。
0+目標潤滑點所在供油終端控制器地址+供油終端控制器下潤滑點的地址,從而實現目標節點的單播。
1+000000+00000000,實現所有潤滑點的廣播。
1+供油終端控制器地址+00000000,實現某一供油終端控制器下所有潤滑點的組播。
實驗及分析
本實驗主要測定當潤滑系統在手動模式下,觀察設定潤滑點的潤滑油量是否與實際流出的油量一致,同時也對整個系統進行了測試。測試平臺如圖7所示,現場交互界面如圖8所示,手機監控界面如圖9所示。本實驗測定主管道壓力為12 MPa,通過觸摸屏設置某一潤滑點的油量,實驗結果如表2所示。
從表1可以看出,實際出油的量均比設定值的量要大,平均每次大約多出2 mL左右,觀察給油過程,此種現象的出現是由于電磁閥的延時關閉造成的。經過進一步分析,此值的大小與潤滑點處的壓力也有很大的關系,當潤滑點的壓力接近設定值的上限時,這個值會變大。
當潤滑點的壓力接近 設定值壓力的下限時此值會變小,在實際應用中可以將此影響因素考慮進去。總體來說,本系統達到了預期目標,可以滿足現代設備潤滑的需求。
圖5 串口WiFi接口電路
圖6 電路原理圖
表1 通信協議格式
圖7 測試平臺圖
圖8 現場交互界
圖9 APP監控界面
表2 油量測試
結語
本文研發了一套智能集中潤滑系統,完成了系統硬件和軟件的設計,同時制定了通信協議并實現了系統組網。該系統支持移動端手機APP監控、觸摸操控和精確定量等功能。
友好的移動端和現場交互界面方便了工作人員的操作。隨后,對整個系統及潤滑點的油量進行了測試。實驗結果表明,該系統具有較高的可靠性和潤滑精度,具備良好的實用價值。
-
電力
+關注
關注
7文章
2138瀏覽量
50173 -
STM32
+關注
關注
2270文章
10895瀏覽量
355729 -
潤滑系統
+關注
關注
0文章
10瀏覽量
7019
發布評論請先 登錄
相關推薦
STM32F4內部Flash實驗例程
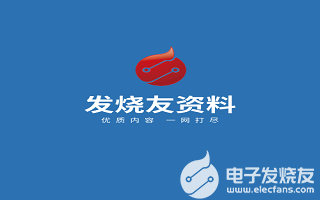
STM32F4 PWM-DAC實驗例程
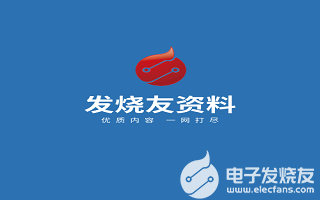
STM32F4 DAC數模轉換實驗例程
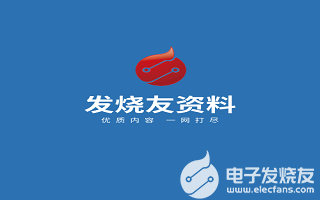
STM32F4開發板硬件平臺簡介
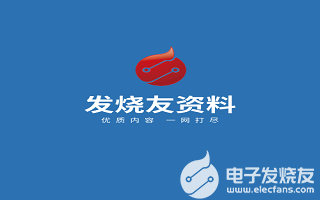
【STM32】STM32F4時鐘系統
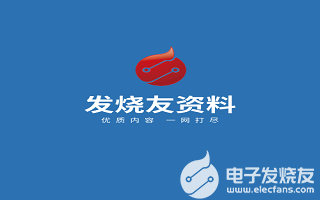
評論