制造任何數(shù)量的印制電路板而不碰到一些問題是不可能的,其中有部份質(zhì)量原因要?dú)w咎于覆銅層壓板的材料。在實(shí)際制造過程中出現(xiàn)質(zhì)量問題時(shí),常常是因?yàn)榛宀牧铣蔀閱栴}的原因。甚至是一份經(jīng)仔細(xì)寫成并已切實(shí)執(zhí)行的層壓板技術(shù)規(guī)范中,也沒有規(guī)定出為確定層壓板是導(dǎo)致生產(chǎn)工藝出問題的原因所必須進(jìn)行的測(cè)試項(xiàng)目。
在這里列出一些最常遇到的層壓板問題和如何確認(rèn)它們的方法。一旦遇到層壓板問題,就應(yīng)當(dāng)考慮增訂到層壓材料規(guī)范中去。通常如果不進(jìn)行這種技術(shù)規(guī)范的充實(shí)工作,那就會(huì)造成不斷地產(chǎn)生質(zhì)量變化,并隨之導(dǎo)致產(chǎn)品報(bào)廢。通常,出于層壓板質(zhì)量變化而產(chǎn)生的材料問題,是發(fā)生在制造商所用不同批的原料或采用不同的壓制負(fù)荷所制造的產(chǎn)品之中。
很少有用戶能持有大量足夠的記錄,使之能夠在PCB加工場(chǎng)所區(qū)分出特定的壓制負(fù)荷或材料批次。于是就常常發(fā)生這樣的情況:印制電路板在不斷地生產(chǎn)出來并裝上元件,而且在焊料槽中連續(xù)產(chǎn)生翹曲,從而浪費(fèi)了大量勞動(dòng)和昂貴的元件。如果裝料批號(hào)立即可查知、層壓板制造者即能核對(duì)出樹脂的批號(hào)、銅箔的批號(hào)、固化周期等。也就是說,如果用戶不能提供與層壓板制造者的質(zhì)量控制系統(tǒng)保持連續(xù)性,這樣就會(huì)使用戶本身長(zhǎng)期蒙受損失。
下面介紹在印制電路板制造過程中,與基板材料有關(guān)的一般問題。
一.表面問題
現(xiàn)象征兆:印料粘附性差、鍍層粘附性差、某些部分不能蝕刻掉,以及某些部分不能錫焊。
可采用的檢查方法:通常用水在板表面形成可看見的水紋進(jìn)行目視檢查,或用紫外線燈照射檢查,用紫外燈照射銅箔可發(fā)現(xiàn)在銅箔上是否有樹脂。
可能的原因:
1.因?yàn)槊撃1∧ぴ斐傻姆浅V旅芎凸饣谋砻妗⒅率刮锤层~表面過份光亮。
2.通常在層壓板的未覆銅的一面,層壓板制造者沒有除去脫模劑。
3.銅箔上的針孔,造成樹脂流出,并積存在銅箔表面上,這通常出現(xiàn)在比3/4盎司重量規(guī)格更薄的銅箔上,或環(huán)境問題造成有樹脂粉末在銅箔表面經(jīng)過層壓。
4.銅箔制造者把過量的抗氧化劑涂在銅箔表面上。
5.層壓板制造者改換了樹脂系統(tǒng)、脫模薄,或刷洗方法。
6.由于操作不當(dāng),有很多指紋或油垢。
7.在沖制、下料或鉆孔操作時(shí)沾上機(jī)油或其它途徑遭到有機(jī)物的污染。
解決辦法:
1.建議層壓板制造商使用織物狀薄膜或其它脫模材料。
2.和層壓板制造商聯(lián)系,使用機(jī)械或化學(xué)的消除方法。
3.和層壓板制造商聯(lián)系,檢驗(yàn)不合格的每批銅箔;索取除去樹脂所扒薦的解決辦法,改善制造環(huán)境。
4.向?qū)訅喊逯圃焐趟魅〕サ姆椒ā3M?a target="_blank">推薦使用鹽酸,接著用機(jī)械方法除去。
5.在層壓板制造進(jìn)行任何改變前,同層壓板制造商配合,并規(guī)定用戶的試驗(yàn)項(xiàng)目。
6.教育所有工序的人員戴手套拿覆銅板。弄清確實(shí)層壓板在運(yùn)輸中是否有合適的墊紙或裝入了袋中,并且墊紙含硫量低,包裝袋沒有臟物,注意保證沒有人正在使用含有硅酮的洗滌劑時(shí)去接觸銅箔,保證設(shè)備狀態(tài)良好。
7.在鍍前或圖形轉(zhuǎn)印工藝前對(duì)所有層壓板去油。
二.外觀問題
現(xiàn)象征兆:層壓板顏色明顯不同、表面顏色不同、表面或內(nèi)層有污斑、層壓板表面上有各種顏色的薄層
可采用的檢查方法:目視。
可能的原因:
1.玻璃布基層壓板在PCB加工前或蝕刻后的表面上有白色布紋或白點(diǎn)。
2.經(jīng)工藝PCB加工后,表面出現(xiàn)白斑或露出玻璃布更多了。
3.經(jīng)工藝PCB加工后,特別是在錫焊后,表面上有一薄層白色膜,這表明是樹脂輕度浸蝕或是有外來的淀積物。
4.基材的顏色變化超出了可能接受的外觀要求。
5.由于層壓板過熱或受某些藥水濃度過高時(shí)間過長(zhǎng)浸泡,基材外觀產(chǎn)生棕色或棕色斑紋。
解決辦法:
1.在極個(gè)別情況下,是因?yàn)楸砻嫒鄙贅渲@露出玻璃布,這在今天是罕見的。更經(jīng)常看到的是表面上的微小起泡或小的白色空穴。這是由于玻璃布表面涂覆層和樹脂系統(tǒng)反應(yīng)所造成的。露出很多玻璃布的板子,在濕度增加時(shí),表面電阻率下降。 然而具有微小起泡或小鼓泡的板子則通常不下降。嚴(yán)格地說,這只是一個(gè)外貌問題同層壓板制造者打交道,避免再發(fā)生這樣的問題;并確定微小起泡可接受的內(nèi)部標(biāo)準(zhǔn)。
2.經(jīng)工藝PCB加工后露出玻璃布的絕大部分情況是由于溶劑浸蝕,去除了一些表面樹脂。與層壓板制造者一起檢驗(yàn)所有的溶劑和鍍液,特別是層壓板在每種溶液中的時(shí)間和溫度保證它們適用于所用的層壓板。在可能情況下按照層壓板制造者推薦的條件PCB加工。
3.與層壓板制造商一起檢驗(yàn),保證所用的助焊劑是適用于所用的板材。驗(yàn)證可能淀積出礦物質(zhì)或無機(jī)物的工藝過程,在可能淀積出礦物質(zhì)或無機(jī)物的工藝過程,在可能情況下,盡可能使用去除了礦物質(zhì)的水。
4.與層壓板制造商聯(lián)系,保證層壓板的任何主要組成或樹脂(它們對(duì)顏色有影響)在作出改變前為用戶所認(rèn)可。有時(shí)過量的銅合金轉(zhuǎn)移會(huì)影顏色。與層壓板制造商打交道,確定可接受的外觀范圍。
5.檢查浸焊操作,焊料溫度和在焊料槽中的停時(shí)間。也檢查在印制板上的發(fā)熱元件或整個(gè)印制板的環(huán)境溫度。假如后者超出了所用層壓板允許溫度的上限,基板會(huì)產(chǎn)生棕色。受某些藥水濃度過高時(shí)間過長(zhǎng)浸泡的板材在后工藝加熱考板時(shí)才表現(xiàn)出來,檢查控制藥水濃度及時(shí)間。
三.機(jī)械PCB加工問題
現(xiàn)象征兆:沖制、剪切、鉆孔PCB加工質(zhì)量不一致,鍍層結(jié)合力差或在金屬化孔中鍍層參差不齊。
檢查方法:對(duì)來料檢查,試驗(yàn)各種關(guān)鍵的機(jī)械PCB加工操作,并把層壓板來料經(jīng)孔金屬化工藝后,進(jìn)行常規(guī)剖析。
可能的原因:
1.材料固化、樹脂含量、或增塑劑改變,會(huì)影響材料的鉆孔、沖制和剪切質(zhì)量。
2.鉆孔、沖制或剪切工藝差,使得生產(chǎn)質(zhì)量差或不一致。
3.沖制或鉆孔前預(yù)熱周期時(shí)間太長(zhǎng),有時(shí)會(huì)影響層壓板的PCB加工。
4.材料的老化,主要是酚醛材料,有時(shí)導(dǎo)致材料中增塑劑跑掉、使得材料比平常更脆。
解決辦法:
1.與層壓板制造者聯(lián)系,確立模似關(guān)鍵機(jī)械PCB加工性能要求的試驗(yàn)。不應(yīng)使用生產(chǎn)模具作試驗(yàn),否則生產(chǎn)模具的磨損和變化會(huì)影響試驗(yàn)結(jié)果。在任何機(jī)械PCB加工性能變化的問題中,只有問題是同材料批號(hào)變化同時(shí)發(fā)生的時(shí)候,才能懷疑層壓板質(zhì)量有問題。
2.參閱關(guān)于各種類型層壓板的制造推薦說明。與層壓板制造商聯(lián)系,弄清每一種級(jí)別層壓板的特定鉆速、進(jìn)給、鉆頭和沖溫度。要記住:每一個(gè)制造廠家使用不同的樹脂和基材的混合物,其推薦說明會(huì)各不相同。
3.小心地預(yù)熱層壓板,務(wù)必找出任何過熱區(qū),例如在加熱燈下的過熱區(qū)。當(dāng)加熱材料時(shí),應(yīng)遵守先進(jìn)先出的原則。
4.與層壓板制造商者一起檢驗(yàn),取得材料的老化特性數(shù)據(jù)。周轉(zhuǎn)庫(kù)存,使得庫(kù)存通常是新生產(chǎn)的板材。務(wù)必查出在倉(cāng)庫(kù)貯存中可能產(chǎn)生的過熱。
四.翹曲和扭曲問題
現(xiàn)象征兆:無論P(yáng)CB加工前、后或PCB加工過程中,基材翹曲或扭曲。錫焊后孔傾斜也是基材翹曲和扭曲的征兆。
檢查方法:用浮焊試驗(yàn),有可能進(jìn)行來料檢驗(yàn)。用45度傾斜錫焊試驗(yàn)特別有效。
可能的原因:
1.在收貨時(shí)或在鋸料和剪料后,材料翹曲或扭曲,這通常是由于層壓不當(dāng)、切斷不當(dāng)或?qū)訅喊褰Y(jié)構(gòu)不均衡所引起的。
2.翹曲也可以是由于材料貯存不當(dāng)而引起,特別是紙基層壓板,當(dāng)將其豎放時(shí),就會(huì)使其呈弓形或變形。
3.產(chǎn)生翹曲是由于覆的銅墻鐵壁箔不相等,如要一面是1盎司,在另一面是2盎司:電鍍層不相等,或特殊的印制板設(shè)計(jì)引起了銅應(yīng)力或熱應(yīng)力。
4錫焊時(shí)夾具或固不當(dāng),在錫焊操作中重的元件也會(huì)引起翹曲。
5.在工藝PCB加工過程或錫焊過程中,材料上的孔位移或傾斜是由于層壓板固化不當(dāng),或基材玻璃布結(jié)構(gòu)的應(yīng)力而引起的。
解決辦法:
1.矯直材料或在烘箱中釋放應(yīng)力,按照層壓板制造者推薦的傾斜角和板材加熱溫度進(jìn)行切斷操作。同層壓板制造商聯(lián)系,保證不用結(jié)構(gòu)不均衡的基材。
2.把材料平放貯存在裝貨紙板箱中或者把材料斜放平躺在貨架上。通常材料放置時(shí)應(yīng)和地面成60度角或更小。
3.和層壓板制造商聯(lián)系,避免兩面覆的銅箔不相等。分析電鍍層和應(yīng)力,或者裝有重的元件或大的銅箔面積引起的局部應(yīng)力。把印制板重新設(shè)計(jì),使元件和銅面積平衡。有時(shí)把印制板一面的大部分導(dǎo)線和另一面的導(dǎo)線垂直布設(shè),使兩面的熱膨脹不相等而引起扭曲,只要可能,應(yīng)避免這種布線。
4.在錫焊操作中,印制板,特別是紙基印制板必須用夾具夾住。在某些情況中,重的元件必須用特殊的夾具或用固定物均衡。
5.與層壓板制造者聯(lián)系,采用任何所推薦的后固化措施。在某些情況下,層壓板制造商會(huì)推薦另一種層壓板用在更為嚴(yán)格或特殊的用途中。
五. 層壓板起白點(diǎn)或分層
現(xiàn)象征兆:白點(diǎn)或布紋出現(xiàn)在表面上或材料里;既可在局部出現(xiàn),也會(huì)在大面積上出現(xiàn)。
檢查方法:恰當(dāng)?shù)母『冈囼?yàn)。
可能的原因:
1.在錫焊時(shí),大面積起泡是由于壓進(jìn)材料中的濕氣和揮發(fā)物引起的。機(jī)械PCB加工不良也是個(gè)原因,因?yàn)闀?huì)使層壓板分層、使得層壓板在濕法工藝PCB加工中吸收水份。
2.在錫焊時(shí)產(chǎn)生白色布紋或白點(diǎn),這是由于層壓板結(jié)構(gòu)不均衡、層壓板固化不當(dāng)、層壓板應(yīng)力釋放不良或者電鍍銅延展性差。
3.在錫焊操作中露出纖維或嚴(yán)重起白點(diǎn)。這是由于過度地與溶劑接觸的緣故,特別是含氯的溶劑,可使樹脂軟化所致。
4.基材受熱時(shí),固定得很緊的大元牛或連接終端會(huì)使板材產(chǎn)生很大的應(yīng)力。結(jié)果在此密集區(qū)域的周圍起白點(diǎn)。板材在浸焊過程中或在浸焊后隨即受應(yīng)力,撓曲或彎曲也會(huì)起白點(diǎn),
解決辦法:
1.通知層壓板制造商,查出了有這樣問題的一批層壓板。對(duì)于所有板材使用所推薦的機(jī)械PCB加工方法。
2.與層壓板制造商聯(lián)系,以取得關(guān)于在浸焊前印制板如何釋放應(yīng)力的說明。在高濕下將印制析板貯存一段時(shí)間后會(huì)吸收過量的濕氣,這會(huì)影響印制板的可焊性。在浸焊操作前將印制板預(yù)烘和預(yù)熱,以減少熱沖擊,會(huì)有助于解決這兩個(gè)問題(參閱關(guān)于多層材料,貯存的印制電路板的吸濕數(shù)據(jù))。
3.與層壓板制造商聯(lián)系,以獲得最適宜溶劑和應(yīng)用時(shí)間的長(zhǎng)短。當(dāng)基材改變時(shí),要驗(yàn)證所有的濕法PCB加工工藝,特別是溶劑。
4.在波峰焊或手工焊操作中,松開緊固的接線終端,并在浸焊前去除任何散熱器或重的元件。核查機(jī)械PCB加工操作正確性,特別是沖制操作,以保證起白點(diǎn)并是由于操作不當(dāng)而引起的輕度分層。保證板材用夾具適當(dāng)夾住并在受熱時(shí)不受應(yīng)力。不要趁熱或在應(yīng)力下就把印制板放入較冷的焊劑清除劑中驟冷。
六. 粘合強(qiáng)度問題
現(xiàn)象征兆:在浸焊操作工序中,焊盤和導(dǎo)線脫離。
檢查方法:在進(jìn)料檢驗(yàn)時(shí),進(jìn)行充分地測(cè)試,并仔細(xì)地控制所有的濕法PCB加工工藝過程。
可能的原因:
1.在PCB加工過程中焊盤或?qū)Ь€脫離可能是由于電鍍?nèi)芤骸⑷軇┙g或在電鍍操作過程中銅的應(yīng)力引起的。
2.沖孔、鉆孔或穿孔會(huì)使焊盤部分脫離,這將在孔金屬化操作中變得明顯起來。
3.在波峰焊或手工錫焊操作過程中,焊盤或?qū)Ь€脫離通常是由于錫焊技術(shù)不當(dāng)或溫度過高引起的。有時(shí)也因?yàn)閷訅喊逶瓉碚澈喜缓没驘峥箘儚?qiáng)度不高,造成焊盤或?qū)Ь€脫離。
4.有時(shí)印制板的設(shè)計(jì)布線會(huì)引起焊盤或?qū)Ь€在相同的地方脫離。
5.在錫焊操作過程中,元件的滯留的吸收熱會(huì)引起焊盤脫離。
解決辦法:
1.交給層壓板制造商一張所用溶劑和溶液的完整清單,包括每一步的處理時(shí)間和溫度。分析電鍍工序是否發(fā)生了銅應(yīng)力和過度的熱沖擊。
2.切實(shí)遵守推存的機(jī)械PCB加工方法。對(duì)金屬化孔經(jīng)常剖析,能控制這個(gè)問題。
3.大多數(shù)焊盤或?qū)Ь€脫離是由于對(duì)全體操作人員要求不嚴(yán)所致。焊料槽的溫度檢驗(yàn)失效或延長(zhǎng)了在焊料槽中的停留時(shí)間也會(huì)發(fā)生脫離。在手工錫焊修整操作中,焊盤脫離大概是由于使用瓦數(shù)不當(dāng)?shù)碾娿t鐵,以及未能進(jìn)行專業(yè)的工藝培訓(xùn)所致。現(xiàn)在有些層壓板制造商,為嚴(yán)格的錫焊使用,制造了在高溫下具有高抗剝強(qiáng)度級(jí)別的層壓板。
4.如果印制板的設(shè)計(jì)布線引起的脫離,發(fā)生在每一塊板上相同的地方;那么這種印制板必須重新設(shè)計(jì)。通常,這的確發(fā)生在厚銅箔或?qū)Ь€拐直角的地方。有時(shí),長(zhǎng)導(dǎo)線也會(huì)發(fā)生這樣的現(xiàn)象;這是因?yàn)闊崤蛎浵禂?shù)不同的緣故。
5.在可能條件下,從整個(gè)印制板上取走重的元件,或在浸焊操作后裝上。通常用一把低瓦數(shù)的電烙鐵仔細(xì)錫焊,這與元件浸焊相比,基板材料受熱的持續(xù)時(shí)間要短。
七. 各種錫焊問題
現(xiàn)象征兆:冷焊點(diǎn)或錫焊點(diǎn)有爆破孔。
檢查方法:浸焊前和浸焊后對(duì)孔進(jìn)行經(jīng)常剖析,以發(fā)現(xiàn)銅受應(yīng)力的地方,此外,對(duì)原材料實(shí)行進(jìn)料檢驗(yàn)。
可能的原因:
1.爆破孔或冷焊點(diǎn)是在錫焊操作后看到的。在許多情況中,鍍得不良,接著在錫焊操作過程中發(fā)生膨脹,使得金屬化孔壁上產(chǎn)生空穴或爆破孔。如果這是在濕法PCB加工工藝過程中產(chǎn)生的,吸收的揮發(fā)物被鍍層遮蓋起來,然后在浸焊的加熱作用下被驅(qū)趕出來,這就會(huì)產(chǎn)生噴口或爆破孔。
解決辦法:
1.盡力消除銅應(yīng)力。層壓板在z軸或厚度方向的膨脹通常和材料有關(guān)。它能促使金屬化孔斷裂。與層壓板制造商打交道,以獲得z軸膨脹較小的材料的建議。
八.尺寸過度變化問題
現(xiàn)象征兆:在PCB加工或錫焊后基材尺寸超出公差或不能對(duì)準(zhǔn)。
檢查方法:在PCB加工過程中充分進(jìn)行質(zhì)量控制。
可能的原因:
1.對(duì)紙基材料的構(gòu)造紋理方向未予注意,順向膨脹大約是橫向的一半。而且基材冷卻后不能恢復(fù)到它原來的尺寸。
2.層壓板中的局部應(yīng)力如果沒釋放出來,在PCB加工過程中,有時(shí)會(huì)引起不規(guī)則的尺寸變化。
解決辦法:
1.囑咐全體生產(chǎn)人員經(jīng)常依相同的構(gòu)造紋理方向?qū)Π宀南铝稀H绻叽缱兓鋈菰S范圍,可考慮改用基材。
2.與層壓板制造商 者聯(lián)系,以獲得關(guān)于在PCB加工前如何釋放材料應(yīng)力的建議。
-
印制電路板
+關(guān)注
關(guān)注
14文章
954瀏覽量
40760
原文標(biāo)題:PCB加工基材及層壓板可產(chǎn)生的質(zhì)量問題
文章出處:【微信號(hào):circuit-ele,微信公眾號(hào):PCB工藝技術(shù)】歡迎添加關(guān)注!文章轉(zhuǎn)載請(qǐng)注明出處。
發(fā)布評(píng)論請(qǐng)先 登錄
相關(guān)推薦
印制電路板蝕刻過程中的問題
印制電路板自動(dòng)功能測(cè)試介紹
印制電路板自動(dòng)功能測(cè)試介紹
常用印制電路板標(biāo)準(zhǔn)匯總
印制電路板設(shè)計(jì)規(guī)范
印制電路板蝕刻過程中的問題
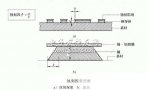
印制電路板的質(zhì)量要求_印制電路板的原理
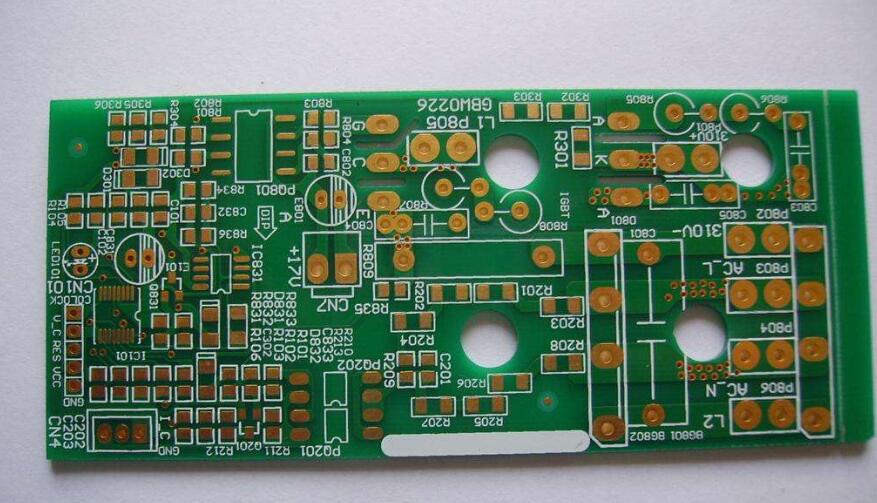
為什么叫印制電路板?印制電路板來由介紹
印制電路板設(shè)計(jì)心得體會(huì)_設(shè)計(jì)印制電路板的五個(gè)技巧
簡(jiǎn)單DIY印制電路板設(shè)計(jì)制作過程
印制電路板的一般布局原則_印制電路板前景
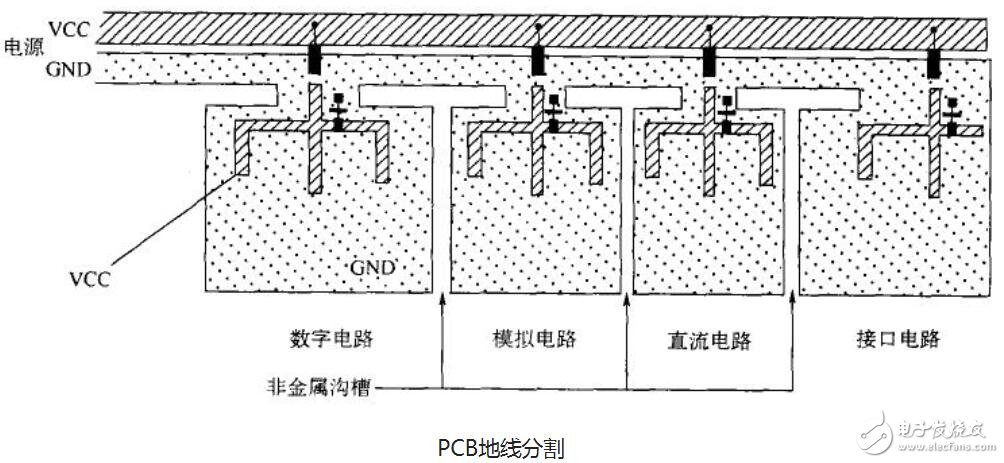
印制電路板翹曲的原因及預(yù)防方法
如何解決印制電路板在加工過程中產(chǎn)生翹曲的問題
柔性印制電路板的生產(chǎn)過程解析
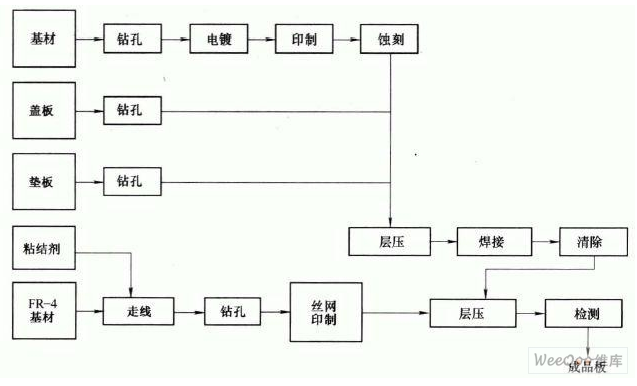
評(píng)論