0 引言
燃煤電廠發(fā)電過(guò)程中會(huì)產(chǎn)生大量的煙塵顆粒物,經(jīng)過(guò)濾除塵后煙塵顆粒物的濃度低、粒徑小,在空氣中漂浮的時(shí)間長(zhǎng)[1],通過(guò)呼吸進(jìn)入人體內(nèi),會(huì)對(duì)人的健康造成很大傷害,也會(huì)對(duì)無(wú)塵度要求較高的工業(yè)生產(chǎn)造成不良影響[2]。因此,設(shè)計(jì)一款性能穩(wěn)定、能夠?qū)崟r(shí)監(jiān)測(cè)低濃度煙塵的系統(tǒng)具有重要意義。
系統(tǒng)以Mie散射為理論基礎(chǔ),它表述了光在微小顆粒物表面發(fā)生散射的規(guī)律[3]。相比較其他原理的測(cè)量方法,基于光散射法的檢測(cè)設(shè)備具有自動(dòng)化程度高、儀器體積小、可以直接獲得測(cè)量結(jié)果等優(yōu)點(diǎn)[4],本文結(jié)合激光調(diào)制、微弱信號(hào)處理以及嵌入式等技術(shù),設(shè)計(jì)了一款能夠在線測(cè)量的低濃度煙塵檢測(cè)系統(tǒng)。
1 Mie散射檢測(cè)原理
經(jīng)過(guò)濾除塵后,煙塵粒徑多數(shù)集中在0.2~10 μm之間,形狀多為球體[5]。此時(shí)粒子粒徑遠(yuǎn)遠(yuǎn)小于粒子間的距離,這樣就可以忽略粒子間的散射,把待測(cè)區(qū)的散射光強(qiáng)看成一個(gè)整體[6],符合Rosin-Rammler分布,其分布函數(shù)為:
式中x和N是描述煙塵粒子分布的特征參數(shù),x表示為粒徑大于x的粒子數(shù)占粒子體積的36.8%,N大小反映了粒子粒徑的分布程度;N越大表示粒子粒徑越集中[7];d為粒子直徑,T是分布函數(shù),其導(dǎo)數(shù)的意義表示粒徑為d的煙塵顆粒在整個(gè)煙塵顆粒群中的比例,公式為:
若待測(cè)區(qū)的體積為V,煙塵質(zhì)量濃度為A mg/m3,密度為ρ,煙塵顆粒總體積為V煙塵,則關(guān)系式如下:
對(duì)于確定的煙塵排放源,σ中的各參數(shù)為已知量,則可由式(6)得出總散射光強(qiáng)I總與煙塵濃度A為一次線性關(guān)系,這也是本檢測(cè)系統(tǒng)的理論依據(jù)。
2 系統(tǒng)設(shè)計(jì)方案
本系統(tǒng)主要由四部分組成:激光發(fā)射單元、信號(hào)接收單元、STM32數(shù)據(jù)處理單元以及上位機(jī)軟件。激光器在調(diào)制信號(hào)驅(qū)動(dòng)下發(fā)出調(diào)制激光,通過(guò)擴(kuò)束鏡照射到待測(cè)煙塵區(qū)發(fā)生散射,散射光通過(guò)聚光鏡匯集到光電探測(cè)器轉(zhuǎn)換為電信號(hào),電信號(hào)經(jīng)過(guò)放大濾波、A/D轉(zhuǎn)換進(jìn)入STM32處理單元進(jìn)行數(shù)據(jù)處理,最后通過(guò)串口送入上位機(jī)進(jìn)行實(shí)時(shí)顯示并存儲(chǔ)。系統(tǒng)設(shè)計(jì)方案如圖1所示。
2.1 激光發(fā)射單元
激光發(fā)射單元主要包括:LD激光器、基準(zhǔn)電壓源電路、信號(hào)調(diào)制電路、激光器電流驅(qū)動(dòng)電路。
系統(tǒng)選用波長(zhǎng)為650 nm的LD激光器作為激光光源,此時(shí)激光波長(zhǎng)和煙塵粒徑大小為同一數(shù)量級(jí),滿足Mie散射的理論要求[8]。基準(zhǔn)源選用LM399高精度基準(zhǔn)電壓源[9],基準(zhǔn)電壓為6.95 V,通過(guò)電位器分壓和低通濾波器消噪,獲得3 V直流偏置電壓。信號(hào)調(diào)制選用高頻精密函數(shù)信號(hào)發(fā)生器MAX038,產(chǎn)生200 Hz頻率的正弦信號(hào)[10],經(jīng)濾波后輸出2 V調(diào)制電壓。電路中的AR1和AR2為L(zhǎng)M393電壓跟隨器,用于提高電路的輸入阻抗以及防止前后級(jí)的互相影響。直流偏置電壓Vb和信號(hào)調(diào)制電壓Vm通過(guò)低噪聲、零漂移的OPA188運(yùn)放芯片疊加,產(chǎn)生5 V激光調(diào)制電壓信號(hào)。恒流源電路是由運(yùn)放AR4和AR5組成的負(fù)反饋電路,電路中利用NPN型三極管的電流放大特性進(jìn)行擴(kuò)流輸出,最終獲得40 mA激光驅(qū)動(dòng)電流。驅(qū)動(dòng)電路如圖2所示。
2.2 信號(hào)接收單元
信號(hào)接收單元主要包括:光電探測(cè)器、I-V轉(zhuǎn)換放大電路、濾波電路。
系統(tǒng)選用型號(hào)為S1787-12高速響應(yīng)硅光電二極管(PIN)作為探測(cè)器,在波長(zhǎng)為650 nm時(shí)感光靈敏度可達(dá)最高值0.4 A/W。經(jīng)過(guò)光電探測(cè)器轉(zhuǎn)換的電信號(hào)十分微弱,對(duì)此信號(hào)的處理不能只是簡(jiǎn)單地放大,而是在放大有用信號(hào)的同時(shí)能夠具備抑制噪聲的能力。前置I-V轉(zhuǎn)換電路的設(shè)計(jì)是為了方便對(duì)檢測(cè)信號(hào)進(jìn)行處理,但轉(zhuǎn)換中會(huì)產(chǎn)生一定的噪聲和偏置電流,可能導(dǎo)致后續(xù)放大電路產(chǎn)生誤差,為了消除這種影響,電路采用T型反饋網(wǎng)絡(luò),轉(zhuǎn)換芯片選用高精度OPA277運(yùn)算放大器。微弱信號(hào)放大部分,設(shè)計(jì)二級(jí)放大電路,放大倍數(shù)可達(dá)100×10倍。但實(shí)際上放大器本身也存在一定的噪聲,所以放大電路可通過(guò)可調(diào)電阻R21根據(jù)實(shí)際測(cè)量靈敏度來(lái)確定最合適的放大倍數(shù)。偏置調(diào)節(jié)的作用是通過(guò)減法器給交流信號(hào)疊加直流偏移。電路如圖3所示。
濾波電路對(duì)提高整個(gè)信號(hào)檢測(cè)單元的信噪比起著決定性的作用,設(shè)計(jì)二級(jí)二階無(wú)限增益多路負(fù)反饋帶通濾波電路,第一級(jí)電路中心頻率為202 Hz,第二級(jí)電路通過(guò)R29調(diào)整為200 Hz,運(yùn)算放大器選用噪聲低、穩(wěn)定性好的AD8039芯片,采用反相接法,反相輸入端的開(kāi)環(huán)增益無(wú)限大,可視為虛地,輸出端由電阻和電容構(gòu)成兩條反饋支路,理論上該電路的品質(zhì)因數(shù)Q可以達(dá)到理想值。電路如圖4所示。
2.3 STM32數(shù)據(jù)處理單元
STM32數(shù)據(jù)處理單元主要包括:STM32F103、供電電路、JTAG程序接口、A/D轉(zhuǎn)換輸入接口、串口模塊、數(shù)據(jù)存儲(chǔ)模塊。
處理器選用的是STM32F103ZET6芯片,此芯片具有高速嵌入式存儲(chǔ)器以及先進(jìn)的通信接口[11]。供電電源選用AX1117-3.3 V芯片;JTAG程序下載接口用于系統(tǒng)硬件仿真及在線調(diào)制功能;串口模塊選用RS232芯片實(shí)現(xiàn)單片機(jī)與上位機(jī)的通信;數(shù)據(jù)存儲(chǔ)模塊選用的是電可擦除存儲(chǔ)芯片F(xiàn)M24C02,可以實(shí)現(xiàn)數(shù)據(jù)存儲(chǔ)和壓縮,以便后續(xù)分析及處理。結(jié)構(gòu)框圖如圖5所示。
2.4 上位機(jī)軟件設(shè)計(jì)
本系統(tǒng)上位機(jī)利用LabVIEW軟件開(kāi)發(fā),上位機(jī)界面中設(shè)計(jì)了數(shù)據(jù)波形與數(shù)值顯示窗口、串口調(diào)試窗口以及數(shù)據(jù)存儲(chǔ)控鍵。顯示界面如圖6所示。
圖中曲線表示未加入煙塵的檢測(cè)結(jié)果,為了便于觀察輸入電壓量的變化,縱坐標(biāo)的量程大小設(shè)置為可調(diào),量程范圍0~3.3 V。
3 實(shí)驗(yàn)結(jié)果
為了驗(yàn)證低濃度煙塵檢測(cè)裝置的靈敏度與準(zhǔn)確性,本文進(jìn)行了靈敏度及曲線標(biāo)定實(shí)驗(yàn)。實(shí)驗(yàn)選用鍋爐燃燒產(chǎn)生的粉煤灰顆粒,實(shí)驗(yàn)環(huán)境為自制的圓柱形模擬煙道,煙道的體積為0.785 m3,可以通過(guò)加入不同質(zhì)量的粉煤灰顆粒物求出煙道內(nèi)的粉煤灰濃度,作為標(biāo)準(zhǔn)濃度,利用標(biāo)準(zhǔn)濃度和實(shí)際測(cè)量值進(jìn)行比較計(jì)算誤差。
3.1 靈敏度實(shí)驗(yàn)
安裝實(shí)驗(yàn)裝置,通過(guò)煙道頂端小口向內(nèi)散落少量粉煤灰顆粒物,經(jīng)過(guò)激光光束時(shí)會(huì)產(chǎn)生散射,實(shí)驗(yàn)結(jié)果如圖7所示。
從圖中可以看到,當(dāng)粉煤灰經(jīng)過(guò)激光光束時(shí),探測(cè)器接收電信號(hào)會(huì)有明顯的變大,隨著粉煤灰的下落,電信號(hào)又逐漸恢復(fù)到初始值,說(shuō)明系統(tǒng)對(duì)低濃度粉煤灰顆粒物的后向散射信號(hào)敏感性較好,可以用于低濃度煙塵測(cè)量。
3.2 曲線標(biāo)定實(shí)驗(yàn)
為了檢驗(yàn)系統(tǒng)的準(zhǔn)確性以及驗(yàn)證光散射產(chǎn)生的模擬電壓量與粉煤灰濃度成一次線性關(guān)系,設(shè)計(jì)兩組不同遞增量的測(cè)量實(shí)驗(yàn)。粉煤灰質(zhì)量在0~250 mg范圍內(nèi)遞增量設(shè)定為25 mg,在250~750 mg范圍內(nèi)遞增量設(shè)定為50 mg,每組質(zhì)量測(cè)量時(shí)間為200 s,每秒記錄一個(gè)數(shù)據(jù),計(jì)算200個(gè)數(shù)據(jù)的平均值,每次實(shí)驗(yàn)后要對(duì)模擬煙道進(jìn)行清理再進(jìn)行下次實(shí)驗(yàn)。實(shí)驗(yàn)結(jié)果如表1所示。
對(duì)表1中粉煤灰濃度與輸出電壓平均值進(jìn)行線性擬合,擬合標(biāo)定曲線如圖8所示。從圖中可以看出,粉煤灰濃度與電壓平均值有著明顯的一次線性關(guān)系,設(shè)線性方程為y=kx+b,通過(guò)線性最小二乘法計(jì)算可得曲線標(biāo)定方程為:
式中,y表示煙塵濃度值(mg/m3),x表示輸出電壓值(mV)。
首先對(duì)表中每組200個(gè)測(cè)量值計(jì)算平均誤差,可得誤差范圍為0.31%~1.26%,變化范圍較小,則系統(tǒng)重復(fù)性良好;再通過(guò)標(biāo)定曲線計(jì)算測(cè)量濃度與標(biāo)準(zhǔn)濃度之間的誤差為4.42%。產(chǎn)生誤差的主要原因有:(1)人為因素造成,每次測(cè)量結(jié)束后清洗過(guò)程不仔細(xì)造成顆粒物殘留;(2)每次加入的粉煤灰質(zhì)量一定,但顆粒物粒徑大小是在一定范圍內(nèi)變化的,這樣也會(huì)影響輸出的電壓值。
4 結(jié)論
本文以Mie散射理論為基礎(chǔ),設(shè)計(jì)一款可以用于低濃度煙塵檢測(cè)的系統(tǒng)。通過(guò)實(shí)驗(yàn)驗(yàn)證了此系統(tǒng)在低濃度情況下有良好的靈敏度和重復(fù)性,利用虛擬儀器技術(shù)設(shè)計(jì)了上位機(jī)顯示界面,能夠?qū)崟r(shí)監(jiān)測(cè)煙塵濃度變化。實(shí)驗(yàn)結(jié)果表明:煙塵濃度與輸出電壓量呈明顯的線性關(guān)系,測(cè)量濃度與標(biāo)準(zhǔn)濃度的偏差為4.42%,在國(guó)際標(biāo)準(zhǔn)誤差規(guī)定的范圍內(nèi),可以應(yīng)用于燃煤電廠低濃度煙塵排放的測(cè)量。
-
檢測(cè)系統(tǒng)
+關(guān)注
關(guān)注
3文章
967瀏覽量
43613
發(fā)布評(píng)論請(qǐng)先 登錄
相關(guān)推薦
基于單片機(jī)的酒精濃度檢測(cè)系統(tǒng)
關(guān)于AD5410芯片的保護(hù)程序
【STM32F411 Nucleo申請(qǐng)】在線煙塵檢測(cè)
雍利安GJC4(B)煤礦用低濃度甲烷傳感器
【MAX40056申請(qǐng)】智能煙塵檢測(cè)儀
基于室內(nèi)甲醛濃度檢測(cè)系統(tǒng)設(shè)計(jì)
實(shí)時(shí)對(duì)超低煙塵濃度的自動(dòng)檢測(cè)系統(tǒng)
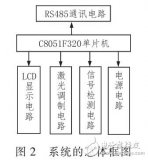
最小二乘多元線性回歸及Mie光散射便攜式揚(yáng)塵粒子監(jiān)測(cè)系統(tǒng)的資料概述
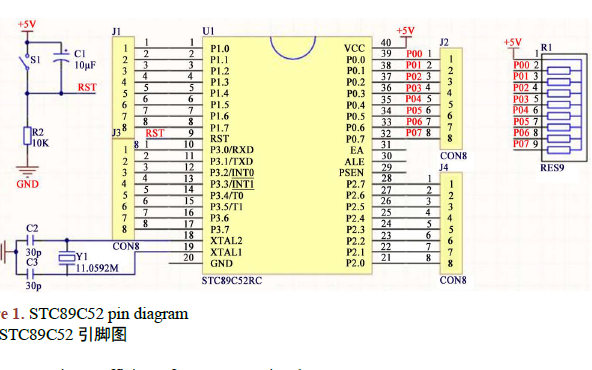
低濃度恒溫恒濕稱(chēng)重系統(tǒng)的技術(shù)要求
硫化氫傳感器有效檢測(cè)化工廠硫化氫氣體的濃度
工地?fù)P塵在線監(jiān)測(cè)系統(tǒng)是如何測(cè)量顆粒物濃度的
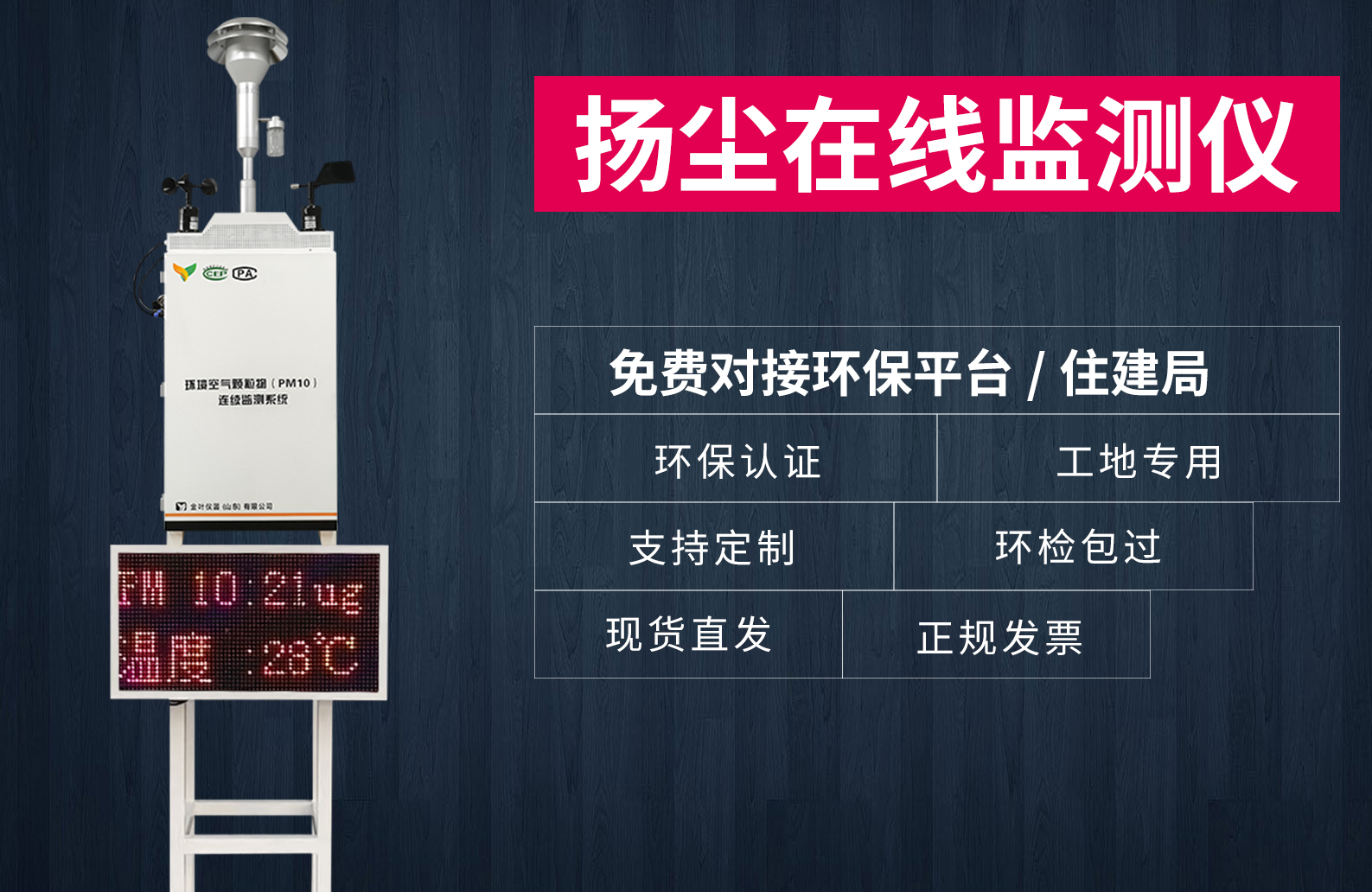
XKCON祥控粉塵濃度檢測(cè)儀高精度檢測(cè)
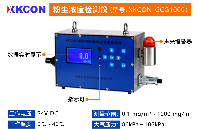
評(píng)論