#01適用范圍
本文適用于ASU或CDC的算法開發和驗證,尤其適用于控制器底層軟件也自主開發或可控的用戶,不適用于整套系統完全黑盒的測試用戶。因此,本文HIL的測試對象為控制器本身而非整套懸架系統。
#02
仿真前提
滿足ASU&CDC的MIL/HIL測試須要滿足如下條件
1.建立CDC物理模型,即CDC速度 - 電流 - 力圖譜。通常由第三方激振臺或CDC供應商提供,參考如下。
2.建立空簧本體、管路、閥體以及儲氣罐等物理仿真模型,甲方提供ASU氣路原理圖以及簧體本身的物理參數。提供ASU實物以及可控制各個閥體/電機動作的A2L文件。
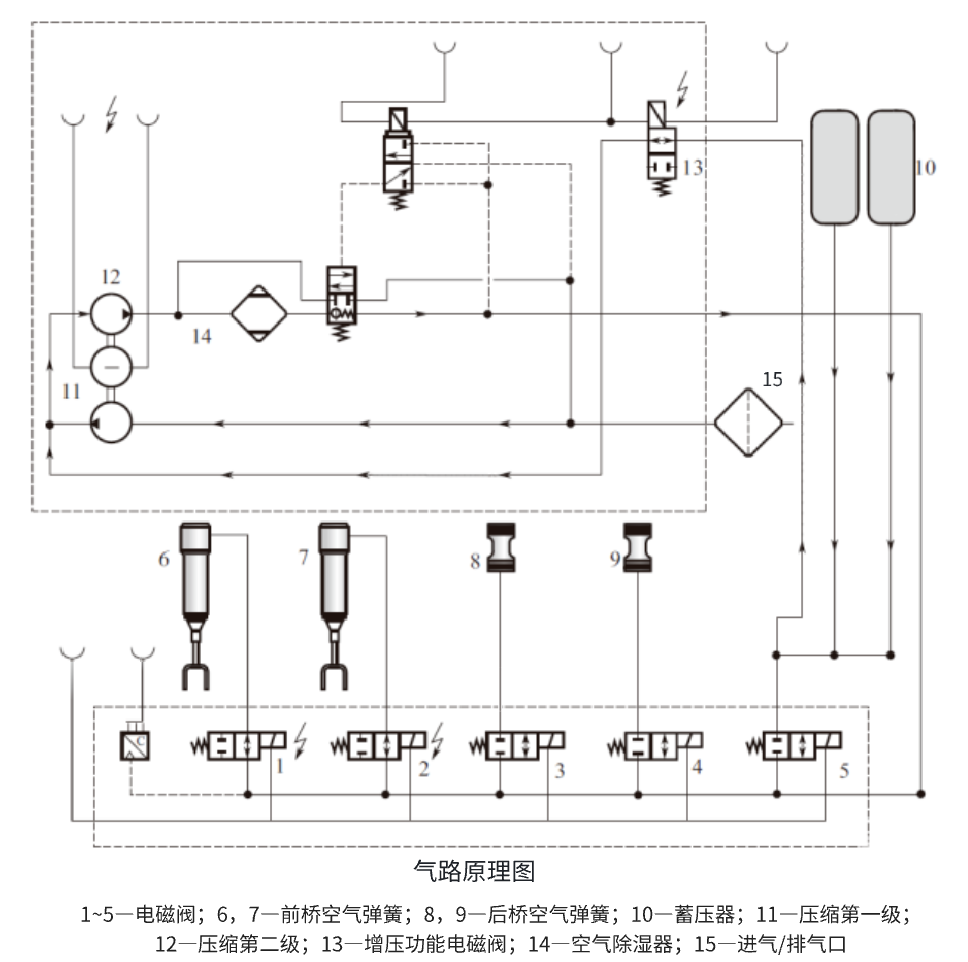
3.匹配控制器的I/O接口。
?供電
?CAN
?速度和加速度傳感器(通常為PSI5或PWM)
?采集ASU&CDC電磁閥電流
5.實時仿真系統。
6.部分底層軟件匹配,例如bypass內部氣壓傳感器。
#03
SIL/HIL仿真實施
基于ASU&CDC的物理模型,匹配CarSim動力學軟件,在Simulink環境中即可完成SIL仿真,此處不作為重點展開。
完成HIL仿真的前提條件是具備一套實時仿真系統。通常一套HIL仿真系統需要由上位機、硬實時下位機、相關機箱和板卡等組成。這套系統往往是復雜的或者說不平易近人的。
TSMaster提供的解決方案是在Windows系統里建立軟實時仿真環境用于運行動力學模型。通過CAN總線接口以及支持CAN接口的I/O板卡(例如通過CAN總線控制的PSI5板卡)完成I/O匹配,并通過內存與動力學軟件實時交互。此外,TSMaster本身已具備測試用例管理,執行以及后處理能力,至于CAN總線仿真,更不用詳述了。
那么參考ASU&CDC的I/O接口須要完成如下準備:
1.筆記本電腦:部署TSMaster和CarSim。
2.CAN工具:可以選擇例如TC1014等工具。
3.電源&線束:電源用于對被測件供電;相關線束連接通常使用BOB。
4.PSI5模擬板卡:通過CAN指令控制。
5.板卡以及線束改造:獲取電磁閥動作狀態(通常通過采集電流)。
針對上述4和5兩條,如果甲方具備底軟能力,就可以通過私有CAN將傳感器信號傳入,將電磁閥電流信號或者驅動狀態位通過CAN傳出,整套測試系統就可以相應變得更為簡潔。那么一套仿真系統也將會變得如下圖一樣簡潔。
#04
案例分享
參考二/三章節,基于甲方提供的必要的信息輸入,進行底層軟件匹配,進而完成測試仿真系統搭建,參見下圖。
基于此可以完成大量的測試仿真驗證,以下是ASU和CDC測試內容的簡要匯總。
以下為典型的測試工況舉例:
1.CDC減速帶工況
HIL測試數據能較好地模擬實車狀態,減振器高度波形和幅值吻合度較高,且能準確識別減速帶的位置。
2.CDC短波路面工況
HIL測試數據也較好地體現了整車測試狀態,減振器行程波形和幅值有良好的一致性。
3.ASU蓄壓氣充氣工況
仿真結果為充氣120s,蓄壓器氣壓從7.9bar提高到了11.27bar,比較符合實際情況。
4.ASU壓縮機舉升工況
通過壓縮機舉升20s,前后軸分別舉升23.9mm和21.9mm,也比較符合實際。此外,還準確模擬出了充氣瞬間車輛短時輕微下降的狀態(因為此時管路氣壓較低,且壓縮機充氣相對較慢)。
5.ASU蓄壓氣舉升工況
蓄壓器舉升相對于前述的壓縮機要迅速很多,舉升5s便可使前后軸分別舉升32.6mm和19.6mm,而且充氣瞬間也未出現壓縮機工況中車身下降的情況,所以模擬狀態和實際較為吻合。
#05
后記與個人觀點
根據項目經驗可以得出以下結論:
1.目前基于模型的開發可以在算法開發的中前期提高開發效率。
2.不推薦不具備底層軟件能力的客戶使用該技術路徑。
3.目前可提供章節三中4和5兩條解決方案,但更為推薦使用案例分享中的極簡方案(即通過CAN交互閥體狀態、高度、加速度信息)。
4.能滿足測試需求且高效簡潔的HIL系統將成為仿真的主流。單純堆砌硬件,追求極致物理性能往往會適得其反。因此,針對不同應用場景選擇合適的技術路徑往往更為重要。
-
控制器
+關注
關注
112文章
16332瀏覽量
177806 -
HIL
+關注
關注
2文章
53瀏覽量
17667 -
mil
+關注
關注
0文章
11瀏覽量
8035
發布評論請先 登錄
相關推薦
硬件在環(HIL)仿真應用中的LabVIEW FPGA
永磁同步電機HIL仿真系統
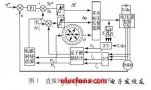
連續阻尼控制電磁概述、功能及特點
技術分享 | 使用TSMaster從零打造車輛控制器HIL實時仿真系列4
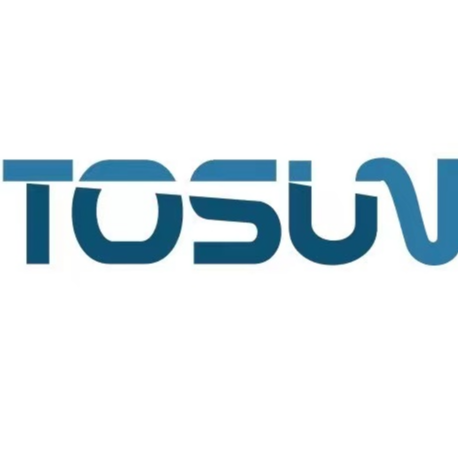
技術分享 | 使用TSMaster從零打造車輛控制器HIL實時仿真系列2-ECU嵌入式代碼生成與TSMaster小程序集成
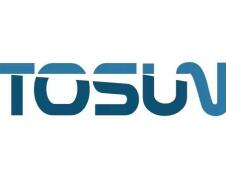
技術分享 | 使用TSMaster從零打造車輛控制器HIL實時仿真系列3-脫離RT的車輛模型的實時仿真
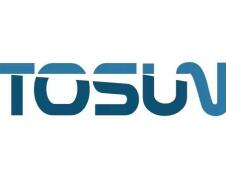
教學驗證篇丨PPEC+HIL BUCK仿真驗證

干貨分享 | TSMaster軟件指南
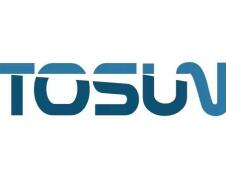
汽車HiL測試:利用TS-GNSS模擬器掌握硬件性能的仿真藝術
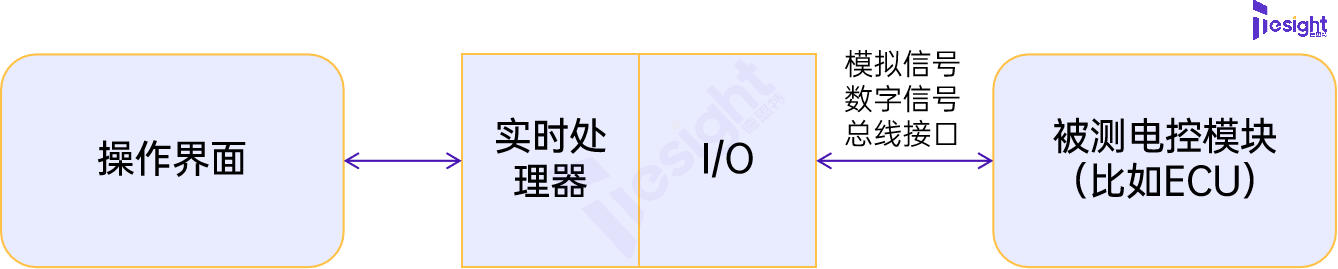
評論