引線鍵合檢測
引線鍵合完成后的檢測是確保產品可靠性和后續功能測試順利進行的關鍵環節。檢測項目全面且細致,涵蓋了從外觀到內部結構的多個方面。
以下是對各項檢測項目的詳細分述:
目檢
球的推力測試
拉線測試
鍵合的失效可靠性
1
目檢
目檢是在顯微鏡下對完成品進行的檢查,主要關注以下幾個方面:
焊球短路:確保金球與相鄰的金球或金屬引線之間無短路觸碰,避免電流異常流通。
焊點的位置偏移:檢查金球是否在焊墊有效面積的75%以內,且金球與相鄰金球或金屬引線之間無觸碰,確保鍵合位置準確。
焊球大小:最小球徑不得小于2倍線徑,最大球徑不得大于5倍線徑,避免過大或過小影響鍵合強度。
第二焊點的魚尾大小:第二焊點(魚尾)的寬度和長度需符合規定范圍,寬度不得小于1.2倍線徑或大于5倍線徑,長度不得小于0.5倍線徑或大于3倍線徑,確保焊點形狀符合標準。
錯焊:核對實際焊線位置與鍵合裝配圖的要求是否一致,避免誤焊導致功能異常。
線尾殘留:檢查線尾是否殘留并黏著在鋁墊上或手指區、銅板區、連接帶上,殘留長度需符合規定范圍,避免影響后續工藝。
引線受損:檢查金屬引線本身和球頸部分是否存在受損、刮傷等,受損程度不得超過25%線徑,確保引線完整性。
碰線、線距不足、塌線:檢查金屬引線之間或金屬引線與芯片之間是否存在短路,線弧與線弧、線弧與芯片邊緣、線弧與其他引腳之間的間距需符合規定,避免短路和塌線現象。
鍵合線的弧度不良:檢查線弧的弧度是否在規格范圍內,避免弧度過大或過小影響鍵合效果和美觀。
漏焊線:核對鍵合裝配圖,確保規定應該焊線的位置已正確焊線,避免漏焊導致功能缺失。
鍵合造成晶粒崩角、隱裂:檢查作業中是否因外力傷及晶粒實體,導致部分晶粒缺失損壞,影響芯片性能和可靠性。
第二焊點頸部斷裂:檢查第二焊點的頸部是否存在拉折、撕裂、裂痕等現象,確保焊點強度符合要求。
通過目檢,可以及時發現并排除潛在的缺陷和問題,確保引線鍵合的質量和可靠性。同時,目檢也是后續檢測項目的基礎和前提,為后續檢測提供了重要的參考和依據。
2
球的推力測試
球的推力測試,也被稱作鍵合點強度測試,是評估引線鍵合質量的重要手段。該測試旨在通過精確的推刀夾具和測試平臺,模擬實際使用中可能遇到的剪切力,從而檢測焊球與芯片或基板之間的結合強度。
測試準備與設備
推刀夾具:選用剛硬且精密的推刀夾具,確保測試的準確性和可靠性。
三軸測試平臺:通過三軸測試平臺,可以精確控制測試頭的移動,確保測試位置準確無誤。
測試角度:剪切工具與芯片表面應呈90°±5°的夾角,以確保測試力的均勻分布。
傳感器:定期校準的傳感器用于測量推力大小,其負載能力應超過焊球最大剪切力的1.1倍,以確保測試的準確性。
光學芯片與顯微鏡:高功率光學芯片和穩定的雙臂顯微鏡用于輔助觀察測試過程,確保測試操作的精確性。
攝像系統:配置攝像系統進行加載工具與焊接對準、測試后檢查、故障分析和視頻捕獲,便于后續分析和記錄。
失效模式與判定
焊球在推力作用下的失效模式多種多樣,主要包括以下幾種:
球脫模式:焊球整體脫離,可能包含或不包含形成的金屬間化合物(如銅鋁材料的殘留)
焊接面殘留:經推力作用后,焊球的焊接面會殘留銅鋁材料或僅殘留引線本身材料(如銅材料)
焊墊金屬脫離:焊墊金屬從焊墊上脫離,嚴重時甚至會將芯片的基底材料帶出
推刀位置錯誤:推刀位置設置過高可能推斷引線頸部,設置過低則可能將整個焊墊層推走
通過球的推力測試,可以及時發現并評估引線鍵合的強度和質量問題,為產品的可靠性和后續功能測試提供有力保障。同時,該測試也是質量控制和工藝改進的重要依據。
3
拉線測試
拉線測試(Wire Pull)是一種用于監控鍵合線弧質量和工藝可靠性的重要測試方法。該測試通過施加拉力來評估鍵合線的強度,并確定其最弱位置。
測試位置與設備
測試位置:拉線測試通常選擇在距離第一焊點或第二焊點1/3的位置進行,以模擬實際使用中可能受到的拉力。測試位置的選擇應確保能夠準確反映鍵合線的強度。
測試設備:拉線測試需要使用專門的拉線鉤和測試設備,如拉力計或拉力測試機。這些設備能夠精確控制拉力的施加,并記錄測試過程中的數據。
測試方法
將拉線鉤移動到焊線下方,并沿Z軸方向(即垂直于芯片表面的方向)向上拉扯。測試可以是破壞性的,即直到焊接被破壞;也可以是非破壞性的,即達到預先定義的力度后停止。
拉力范圍與評判標準
拉力范圍:拉力的測試范圍通常根據具體需求而定,常見的范圍包括0~100g、0~1kg和0~10kg等。
質量評判:拉線測試后,需要對鍵合引線的各個部分進行質量評判。評判內容包括第一焊點的焊墊和焊球、球頸、鍵合引線、焊接位置以及第二焊點的線尾等。根據評判結果,可以確定鍵合線的強度和質量是否符合要求。
第二焊點拉線力測試
測試目的:第二焊點拉線力測試是評估第二焊點鍵合強度的一種方法。它通過觀察拉線后殘留金屬的狀況,為工藝分析提供重要信息。
測試方法:進行第二焊點拉線力測試時,拉線鉤應盡量靠近第二焊點,以確保線弧在第二焊點處斷裂。該測試是破壞性的,通常不作為標準測試項,但在特定情況下可用于分析工藝問題。
4
鍵合的失效可靠性
在超聲波焊鍵合過程中,焊盤產生彈坑是一種常見的缺陷現象,它指的是焊盤金屬層下方的二氧化硅層或其他層次受到破壞。彈坑通常肉眼難以察覺,但其對電性能的影響卻不容忽視。
彈坑產生的原因
彈坑的產生源于多種因素,主要包括以下幾個方面:
超聲波能量過高:當超聲波能量超過一定閾值時,會導致硅晶格點陣的破壞,進而形成彈坑。過高的能量輸入使得焊盤下方的材料無法承受,從而產生損傷。
鍵合壓力過大:在楔焊鍵合過程中,如果鍵合力過高,同樣會對焊盤下方的材料造成壓迫,導致彈坑的產生。
焊球尺寸不合適:如果焊球太小,堅硬的鍵合工具在鍵合過程中可能會直接接觸到焊盤金屬層,而非通過焊球進行緩沖,從而增加焊盤受損的風險。
焊盤厚度不足:焊盤的厚度是影響其抗損傷能力的重要因素。當焊盤厚度小于一定值時(如0.6微米以下),其抵抗外力破壞的能力會顯著降低,更容易產生彈坑。
材料硬度不匹配:焊盤金屬和金屬引線的硬度如果匹配不當,也可能導致彈坑的產生。硬度差異過大時,較軟的材料更容易受到損傷。
鋁絲超聲波焊鍵合的特殊性:在鋁絲超聲波焊鍵合中,由于鋁絲的硬度相對較高,如果工藝參數控制不當,也容易導致晶圓焊盤產生彈坑。
芯片本身的問題:芯片本身的質量問題,如材料缺陷、加工精度不足等,也可能導致彈坑的產生。
晶圓測試時的損傷:在晶圓測試過程中,如果探針操作不當,也可能刺傷焊墊,進而引發彈坑問題。
彈坑對可靠性的影響
彈坑的存在會嚴重影響鍵合的可靠性。首先,彈坑會破壞焊盤與金屬引線之間的電氣連接,導致電路性能下降或失效。其次,彈坑還可能成為潛在的裂紋源,隨著時間和環境的變化,裂紋可能逐漸擴展,最終導致整個鍵合結構的失效。
因此,在超聲波焊鍵合過程中,必須嚴格控制工藝參數,確保焊盤、焊球、金屬引線等材料的匹配性,以及芯片本身的質量。同時,在晶圓測試和后續處理過程中,也需要采取適當的措施,避免對焊墊造成損傷。通過這些措施,可以有效降低彈坑產生的風險,提高鍵合的可靠性和穩定性。
彈坑缺陷與化學腐蝕分析
彈坑是超聲波焊鍵合中常見的一種缺陷,它指的是焊盤金屬層下方的二氧化硅層或其他層次受到破壞。為了深入分析彈坑缺陷,通常需要進行化學腐蝕分析。
這一分析過程涉及將焊區的金屬鋁腐蝕掉,以觀察金屬間化合物的覆蓋率和焊區金屬層下方電路是否有損傷。
鍵合點的質量與可靠性問題
在實際生產過程中,鍵合點可能會遇到多種問題,如開裂、翹起、尾部不一致以及剝離等。這些問題可能由多種因素導致,包括引線通道不干凈、進料角度不對、劈刀堵塞、引線夾污染、夾力或距離不正確、張力不正確等。此外,金屬間化合物的形成、引線彎曲疲勞、腐蝕、金屬遷移以及振動疲勞等也是影響鍵合可靠性的主要原因。
影響鍵合可靠性的主要因素
焊接面絕緣層未去除干凈:如芯片鍵合區的光刻膠或窗口鈍化膜殘留,會導致金屬間鍵合不良,形成絕緣夾層,增加接觸電阻,降低鍵合可靠性。
金屬層缺陷:如芯片金屬層過薄、有合金點或黏附不牢固,會導致鍵合時無緩沖作用,形成缺陷,或壓焊點容易脫落。
表面沾污:各部件在各個環節均可能產生沾污,如灰塵、有機物、鈉等,會導致原子不能互相擴散,影響鍵合質量。
材料間接觸應力不當:鍵合應力過小會導致鍵合不牢,過大則會影響鍵合點的機械性能,甚至損傷芯片材料。
引線框架腐蝕:鍍層污染過多及較高的殘余應力會導致引線框架腐蝕,影響鍵合可靠性。
-
檢測
+關注
關注
5文章
4492瀏覽量
91525 -
引線鍵合
+關注
關注
2文章
20瀏覽量
8210
原文標題:一文了解引線鍵合檢測
文章出處:【微信號:芯長征科技,微信公眾號:芯長征科技】歡迎添加關注!文章轉載請注明出處。
發布評論請先 登錄
相關推薦
有償求助本科畢業設計指導|引線鍵合|封裝工藝
集成電路封裝中的引線鍵合技術

LED引線鍵合的檢測內容與工藝評價
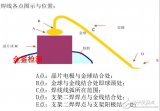
LED引線鍵合工藝評價
引線鍵合是什么?引線鍵合的具體方法
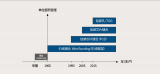
什么是引線鍵合?引線鍵合的演變
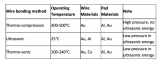
3D 結構和引線鍵合檢測對比
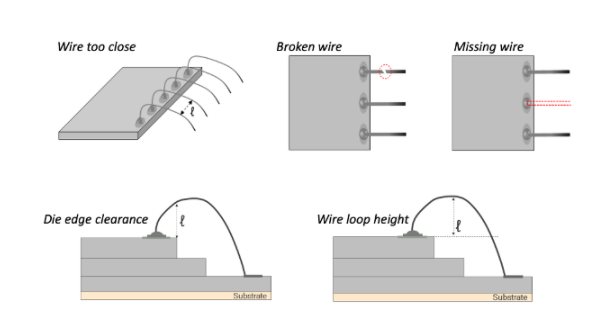
優化關鍵工藝參數提升功率器件引線鍵合的可靠性
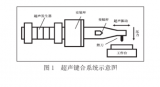
帶你一文了解什么是引線鍵合(WireBonding)技術?
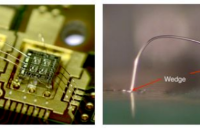
評論