隨著半導體技術的飛速發展,芯片集成度不斷提高,功能日益復雜,這對半導體貼裝工藝和設備提出了更高的要求。半導體貼裝工藝作為半導體封裝過程中的關鍵環節,直接關系到芯片的性能、可靠性和成本。本文將深入分析半導體貼裝工藝及其相關設備,探討其發展趨勢和挑戰。
一、半導體貼裝工藝概述
半導體貼裝工藝是將芯片通過有機膠、金屬焊料或其他連接方式精確地粘貼在基板或引線框架上的過程。這一工藝步驟在半導體封裝流程中占據重要地位,它實現了芯片與外部電路的電氣連接、機械連接和熱連接,確保了芯片的穩定性和可靠性。
半導體貼裝工藝的主要目的是將切割后的裸芯片(晶粒)粘貼到基板上,形成芯片組件。這一過程中,需要確保芯片與基板之間的電氣連接良好,同時提供足夠的機械支撐和熱散失能力。為了實現這一目標,貼裝工藝需要高精度的定位、穩定的貼裝壓力和可靠的連接方式。
二、半導體貼裝工藝步驟
半導體貼裝工藝通常包括以下幾個關鍵步驟:
- 基板準備:在貼裝芯片之前,需要對基板進行清洗、涂膠等預處理工作。清洗基板可以去除表面的污垢和氧化物,提高貼裝質量;涂膠則是為了增強芯片與基板之間的粘接力,防止芯片在使用過程中脫落。
- 芯片定位:使用高精度的貼裝設備將芯片準確地放置在基板上的預定位置。這一過程需要高精度的定位系統和穩定的機械結構,以確保芯片的位置精度和貼裝壓力均勻性。
- 芯片粘貼:將芯片粘貼到基板上的過程可以通過多種方式實現,如銀膠粘貼、共晶粘貼、高分子膠粘貼等。不同的粘貼方式適用于不同的應用場景和需求。
- 固化處理:粘貼完成后,需要對芯片進行固化處理,以提高芯片與基板之間的粘接力。固化處理可以通過加熱、紫外線照射等方式實現,具體方法取決于所使用的粘貼材料。
- 質量檢測:最后,需要對貼裝完成的芯片組件進行質量檢測,包括外觀檢查、電氣性能測試等。這可以確保芯片組件的質量符合設計要求,提高產品的可靠性和穩定性。
三、半導體貼裝設備分析
半導體貼裝設備是實現半導體貼裝工藝的關鍵工具。隨著半導體技術的不斷發展,貼裝設備也在不斷更新換代,以滿足日益提高的貼裝精度和效率要求。
- 貼裝設備類型
半導體貼裝設備主要分為手動貼裝設備和自動貼裝設備兩大類。手動貼裝設備適用于小批量、多品種的生產需求,具有靈活性高、成本低等優點;但貼裝精度和效率相對較低。自動貼裝設備則適用于大批量、單一品種的生產需求,具有貼裝精度高、效率高、穩定性好等優點;但設備成本較高,需要專業的操作和維護人員。
在自動貼裝設備中,又可以根據貼裝方式的不同分為引腳插入式貼裝設備、表面貼裝設備(SMT)和倒裝芯片貼裝設備(FC)等。引腳插入式貼裝設備適用于引腳數量較少的芯片貼裝;表面貼裝設備則適用于引腳數量較多、體積較小的芯片貼裝;倒裝芯片貼裝設備則適用于高端芯片貼裝,如CPU、GPU等。
- 貼裝設備關鍵技術
半導體貼裝設備的關鍵技術包括高精度定位系統、穩定的機械結構、可靠的連接方式、智能控制系統等。
高精度定位系統是實現芯片精確定位的關鍵。現代貼裝設備通常采用光學或激光定位系統,通過攝像頭捕捉芯片和基板的圖像,并通過算法計算出芯片在基板上的精確位置。同時,設備還需要具備高速、高精度的運動控制系統,以確保芯片在移動過程中的穩定性和準確性。
穩定的機械結構是確保貼裝設備長期穩定運行的基礎。貼裝設備需要承受高速、高頻次的運動沖擊和振動,因此機械結構需要具備足夠的剛性和穩定性。此外,設備還需要具備良好的散熱性能,以防止因過熱而導致的設備故障。
可靠的連接方式是確保芯片與基板之間電氣連接良好的關鍵。不同的芯片和基板材料需要采用不同的連接方式,如銀膠粘貼、共晶粘貼、高分子膠粘貼等。貼裝設備需要具備多種連接方式的選擇和切換能力,以滿足不同應用場景的需求。
智能控制系統是實現貼裝設備自動化、智能化的關鍵。現代貼裝設備通常采用先進的控制算法和人工智能技術,實現設備的自動化控制和智能決策。例如,設備可以根據芯片和基板的不同特性自動調整貼裝參數和工藝流程;同時,還可以實時監測設備的運行狀態和貼裝質量,及時發現并處理異常情況。
- 貼裝設備發展趨勢
隨著半導體技術的不斷發展,貼裝設備也在不斷更新換代。未來,貼裝設備將朝著高精度、高效率、智能化、柔性化等方向發展。
高精度是貼裝設備永恒的追求。隨著芯片集成度的不斷提高和尺寸的不斷縮小,對貼裝精度的要求也越來越高。未來,貼裝設備將采用更先進的定位系統和運動控制系統,實現更高的貼裝精度和穩定性。
高效率是貼裝設備發展的重要趨勢。隨著市場競爭的加劇和生產成本的不斷上升,提高貼裝效率成為降低生產成本、提高競爭力的關鍵。未來,貼裝設備將采用更先進的生產流程和技術手段,實現更高的生產效率和產能。
智能化是貼裝設備發展的重要方向。隨著人工智能技術的不斷發展和應用,貼裝設備將具備更強的智能控制和決策能力。例如,設備可以根據生產需求自動調整工藝流程和參數設置;同時,還可以實時監測設備的運行狀態和貼裝質量,及時發現并處理異常情況。
柔性化是貼裝設備適應多品種、小批量生產需求的關鍵。未來,貼裝設備將具備更強的柔性化生產能力,可以根據不同的生產需求快速切換工藝流程和參數設置。這將有助于降低生產成本、提高生產效率和靈活性。
四、半導體貼裝工藝與設備的挑戰與解決方案
盡管半導體貼裝工藝和設備取得了顯著的進展和成就,但仍面臨一些挑戰和問題。以下是一些主要的挑戰及其解決方案:
- 挑戰一:貼裝精度要求高
隨著芯片集成度的不斷提高和尺寸的不斷縮小,對貼裝精度的要求也越來越高。微小的偏差都可能導致芯片與基板之間的電氣連接不良或機械支撐不足等問題。
解決方案:采用更先進的定位系統和運動控制系統,提高貼裝精度和穩定性。同時,加強對設備的維護和保養工作,確保設備的長期穩定運行。
- 挑戰二:貼裝材料選擇困難
不同的芯片和基板材料需要采用不同的連接方式,如銀膠粘貼、共晶粘貼、高分子膠粘貼等。不同的連接方式具有不同的優缺點和適用范圍,選擇不當可能導致貼裝質量下降或成本上升等問題。
解決方案:根據芯片和基板的不同特性選擇合適的連接方式。同時,加強對新材料和新工藝的研究和開發工作,以提供更多選擇和可能性。
- 挑戰三:生產成本高
半導體貼裝設備和工藝的成本相對較高,這對企業的生產成本和競爭力產生了一定影響。同時,隨著市場競爭的加劇和生產成本的不斷上升,降低生產成本成為提高企業競爭力的關鍵。
解決方案:通過技術創新和工藝優化降低生產成本。例如,采用更先進的生產流程和技術手段提高生產效率;同時,加強設備的維護和保養工作延長設備使用壽命降低維修成本等。
- 挑戰四:環境要求嚴格
半導體貼裝工藝和設備對生產環境的要求非常嚴格,如溫度、濕度、潔凈度等都需要控制在一定范圍內。否則可能導致芯片受潮、氧化或污染等問題影響貼裝質量和可靠性。
解決方案:加強對生產環境的控制和管理工作。例如,采用先進的溫濕度控制系統和潔凈室技術確保生產環境的穩定性和可靠性;同時加強對員工的培訓和管理提高員工的環境意識和操作技能等。
五、結論
半導體貼裝工藝與設備是半導體封裝過程中的關鍵環節之一,對芯片的性能、可靠性和成本具有重要影響。隨著半導體技術的不斷發展,貼裝工藝和設備也在不斷更新換代以滿足日益提高的貼裝精度和效率要求。然而,在發展過程中仍面臨一些挑戰和問題如貼裝精度要求高、貼裝材料選擇困難、生產成本高以及環境要求嚴格等。通過技術創新和工藝優化等措施可以有效解決這些問題推動半導體貼裝工藝與設備的進一步發展。
未來,隨著人工智能、物聯網等新興技術的快速發展和應用場景的不斷拓展半導體貼裝工藝與設備將迎來更廣闊的發展前景和機遇。企業需要密切關注市場動態和技術發展趨勢加強技術創新和研發投入提高產品質量和競爭力以應對日益激烈的市場競爭和挑戰。同時,政府和社會各界也應加強對半導體產業的支持和引導推動半導體產業的持續健康發展。
-
芯片
+關注
關注
459文章
51600瀏覽量
429879 -
半導體
+關注
關注
335文章
28032瀏覽量
225557 -
貼裝
+關注
關注
0文章
92瀏覽量
16972
發布評論請先 登錄
相關推薦
半導體工藝講座
招聘半導體封裝工程師
半導體生產封裝工藝簡介
半導體封裝工藝之模塑工藝類型
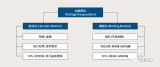
半導體封裝工藝的四個等級
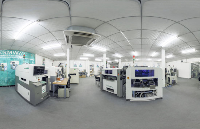
半導體封裝工藝面臨的挑戰
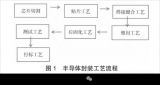
半導體溫控新突破:精度與效率的雙重提升
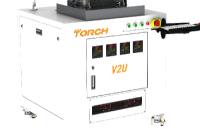
評論