作為輔助駕駛和自動駕駛的關鍵組成部分,新一代汽車芯片正在快速推動異常檢測技術的發展。
據新智駕了解,半導體設備供應商 KLA-Tencor、半導體數據分析服務商Optimal+和EDA巨頭 Mentor (2016年被西門子收購)正在擴大異常檢測領域的相關工作。
異常檢測技術在各行業已經使用多年,是保證芯片生產質量零缺陷的主要技術之一,而零缺陷對汽車行業至關重要。
通常來說,異常檢測是采用硬件和統計篩選算法來定位的。一些芯片可能會通過各種標準測試,但是有時會表現出功能異常。這種芯片可能會影響系統性能或導致系統失效。
異常或缺陷芯片的出現有諸多原因,一些潛在可靠性缺陷在設備發貨時不會出現,但它們在不同環境中會以某種方式激活,最終影響整個系統的運行。
為了發現芯片出現的各種問題,業界多種使用異常檢測的方法,如零件平均測試法(PAT)。
PAT的測試流程如下:
首先,對晶圓進行電氣測試;
其次,把硬件和PAT算法組合,檢測出違反特定測試規范的異常或故障芯片;
最后,將異常芯片去除。
*PAT中極限和異常值的圖形表示 來源:Automotive Electronics Council
隨著跟多高端芯片用于汽車,迫切需要高級的異常檢測算法;
異常檢測技術必須符合輔助駕駛和自動駕駛技術的發展趨勢;
英偉達和其它沒有異常檢測經驗的IC制造商正在蜂擁進入汽車市場,這意味著他們需要提高芯片面臨的一系列問題。
汽車芯片的發展趨勢
*隨機缺陷 來源: KLA-Tencor
既然如此,為什么不在這些芯片離開晶圓廠之前就檢測出這些缺陷呢?
晶圓廠測試
根據加州大學伯克利分校的統計,月產5萬片晶圓的晶圓廠需要以下設備:
50臺掃描儀/步進器和晶圓軌道;
10個高電流離子注入器和8個中等電流離子注入器;
40臺蝕刻機;
30個CVD工具。
晶圓廠一般采用自動化技術分步處理晶圓。一個先進工藝的晶圓制造過程可能有多達600-1000個步驟,甚至更多,相比之下,成熟工藝的步驟更少。
先進工藝中,半導體設備必須處理更小且更加精確的特征,隨著工藝尺寸的縮減,缺陷也變得越來越難查找。
在汽車領域,芯片制造商必須在其器件的制造工藝中實施更加嚴苛的控制措施,并實施持續的缺陷改進計劃。
“你必須有一個管理良好的工廠,一個強大的質量體系和貫徹高質量的理念,才能夠獲得制造汽車產品所需的認證。在汽車行業里,質量控制始于工藝設計和工廠規劃,并一直延伸到實際生產芯片。”聯電副總裁溫文婷表示。
晶圓廠中,人們使用檢測系統定位晶圓缺陷。一般來講,芯片制造商不會檢查每一片晶圓,因為那樣不僅耗時長而且成本高,抽樣檢測某些晶圓或者部分芯片是最好的辦法。
對于消費級芯片來說,過程簡單。“當我們開發一項技術時,我們進行認證,通常來講,抽樣的樣本數量總是有限的。”溫文婷表示。
但汽車級芯片要求就不同了。“你必須測試大量的樣本才能得出故障率,這個過程的成本非常高。”溫文婷說。
所有問題和挑戰都是需要大量時間和資金去解決。如果芯片在經過檢測后符合規范,就可以把晶圓從晶圓廠分發到封測廠。
同時,壓力就轉給封測廠了。為了幫助測試,KLA-Tencor設計了一種技術方案來解決晶圓廠的問題。這一技術被稱為在線零件平均測試(I-PAT),它利用PAT的概念。但是,與在測試部門進行的PAT及其變體不同,I-PAT在晶圓廠中執行。
I-PAT不一定會與傳統的第三方異常檢測供應商競爭。它的目標是提供更多的測試數據,補充既有的測試組合。通常來講,這個過程仍然需要執行傳統的異常檢測。
KLA-Tencor的技術涉及硬件和數據分析軟件包。簡言之,先將檢驗數據輸入到計算機建模程序中,然后分解數據,并查看晶圓圖上的硅片,最后在晶圓廠的多個檢查步驟中查找異常缺陷。
舉例來說,這個技術將顯示具有五層的芯片晶圓圖,包括源區、柵極、觸點層、金屬層1和金屬層2。
假設金屬層1上可能會有800個缺陷。計算機從晶圓上隨機選擇10個芯片,然后,使用各種I-PAT算法,系統最終確定這10個芯片中有9個存在潛在的可靠性缺陷。
KLA-Tencor高級營銷總監David Price說。 “通過不斷重復,可以看到缺陷的統計性質如何幫助你找到有可能包含可靠性缺陷的芯片。”
I-PAT可用于挑選有問題的芯片。 另外,這些數據可以與其他異常檢測方法結合使用,以改進測試通過或不通過的決策。Price說:“通過在晶圓廠中實施I-PAT技術,能夠減少傳統PAT方法的不足。”
晶圓廠到測試廠之路
晶圓從晶圓廠轉移到測試廠后,進行晶圓分類、最終測試,有時也會進行系統級測試。
檢查和測試會產生巨大的數據量。但是,在大量數據面前,如何知道器件是否仍存在潛在的可靠性缺陷或其他問題呢?
這也為什么汽車廠商希望他們的供應商在測試過程中執行傳統異常檢測。
PAT是最基本的邊界檢測形式,可以檢測出一個超出不合格閾值的芯片。測試閾值可以設置為靜態(SPAT)或動態(DPAT)模式。
在SPAT中,測試閾值是基于該批次的數量決定的;在DPAT中,則會在每次晶圓測試時計算閾值。
在SPAT和DPAT中,都會執行一個算法,最終得出測試通過或失敗的結果。
但是,這些算法可能在某些情況下會失敗。有的器件的特征可能和其它器件明顯不同,但是它也在合理范圍內。有的器件可能是遠離正態分布的極端異常。
雖然異常檢測專家已經加入了一些程序來解決這些問題。但是,多年來,這些芯片變得越來越復雜,因此需要更先進的異常檢測技術。
據新智駕了解,有一些基于幾何分布、多變量和其它復雜異常檢測算法可以和DPAT和SPAT結合一起使用。,例如通過它的幾何分布鄰近度來查看芯片質量。
GPAT有一個復雜版本,稱為GDBN。GDBN基于一種理念:缺陷總是趨向于集中出現在晶圓的某些特定位置上。簡單來講,缺陷較多的區域可能會找出一些不合格芯片。
還有一種被稱為最差殘差(NNR)技術。“最差殘差技術是在每個芯片的每一次測試中檢查所有值,它不僅考慮整體晶圓,還考慮臨近芯片的情況。”Optimal+ Schuldenfrei說。
通常,上述方法都可以結合使用。
未來趨勢
展望未來,ADAS和自動駕駛將進一步推動檢測技術的需求。隨著汽車的自動化程度越來越高,芯片缺陷檢測也將變得越來越重要。
此外,機器學習和人工智能的運算能力與功能也日益強大,我們相信,它們也會更多地參與到異常檢測中來。
最后,把所有的數據集成在一起也許是最大的挑戰。想象一下,從芯片獲取數據,并將其與多個不同公司的電路板數據關聯起來,需要共享數據才能實現更好的異常檢測。
-
半導體
+關注
關注
335文章
28302瀏覽量
229729 -
晶圓
+關注
關注
52文章
5076瀏覽量
128974 -
人工智能
+關注
關注
1803文章
48406瀏覽量
244625 -
自動駕駛
+關注
關注
788文章
14115瀏覽量
168721
原文標題:汽車芯片零缺陷有多難?這幾家公司正在掀起芯片質量檢測大戰
文章出處:【微信號:WW_CGQJS,微信公眾號:傳感器技術】歡迎添加關注!文章轉載請注明出處。
發布評論請先 登錄
相關推薦
蔡司軟件 | ZEISS INSPECT Optical 3D在汽車行業的應用
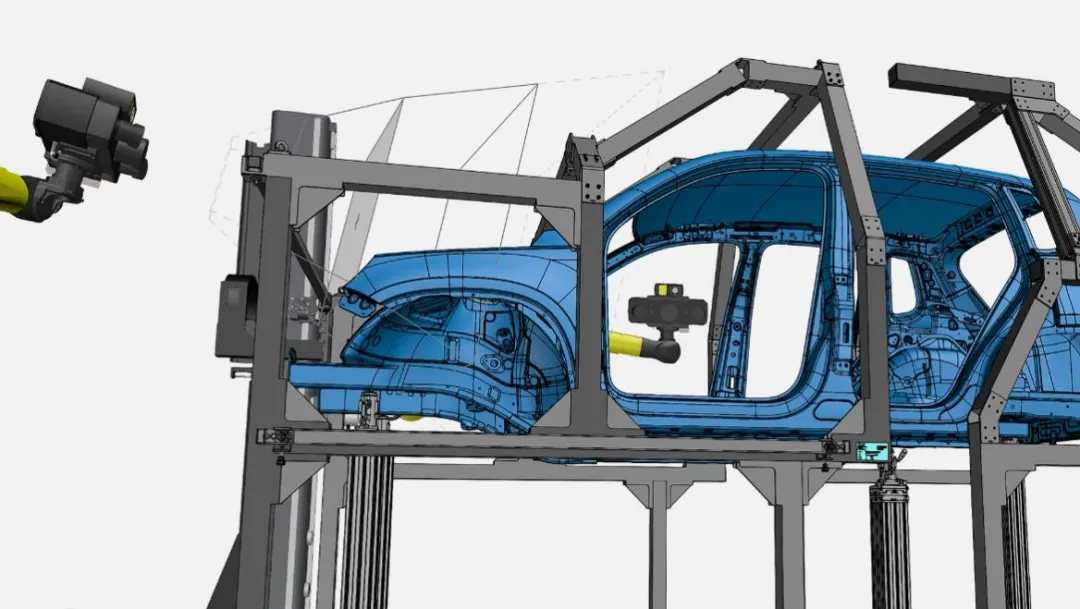
云服務在智能汽車行業的機遇與挑戰
汽車行業AI視覺檢測(下):創新驅動品質提升
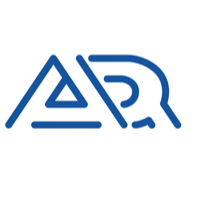
德州儀器攜手經緯恒潤推動汽車行業智能化轉型
汽車行業AI視覺檢測(上):創新驅動品質提升
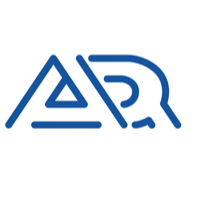
符合AEC-Q200的汽車行業專用保險絲
智能制造在汽車行業的應用
干簧傳感技術如何引領汽車行業的未來變革?
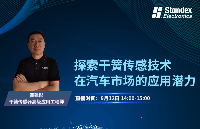
為什么加速數據處理對各行各業的AI創新都至關重要
Modbus轉Profibus網關在汽車行業的應用
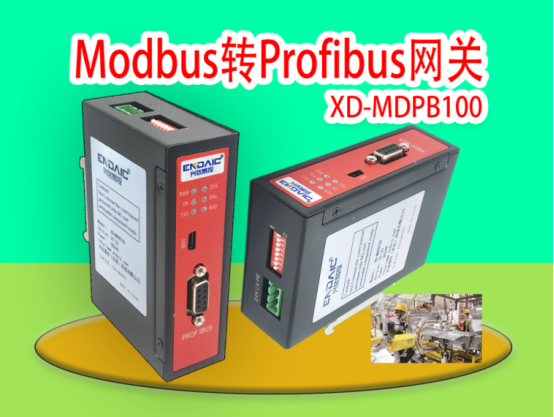
評論