UTCForget food and guns, the first 3D-printed jet engines have arrived By Jenni RyallAustralia
One day there are 3D-printed Oreos, the next there are 3D-printed jet engines. The world of 3D printing has taken off, with the latest development straight out of Australia.
Researchers at Monash University in Melbourne with help from the CSIRO and Deakin University have printed not one, but two metal jet engines.
The proof-of-concept prototype in partnership with the Monash‘s commercial arm, Amaero Engineering, has already piqued the interest of international aerospace companies, such as Airbus, Raytheon and Boeing.
The use of 3D printing in the aerospace industry can help with reducing the length of time spent on a project, creating a lighter engine while reducing operational and production costs, according to a white paper by Smarttech. The use of a printed model can reduce waste by up to 90%, leading not only to a reduction of cost, but also a reduction in the environmental impact from manufacturing.
Researchers were provided an old auxiliary powered gas turbine engine by French aerospace supplier Safran that could be pulled apart and copied using a 3D printer. The process, known as additive manufacturing, allows the powder form of metals to be melted and then fused together into objects using a laser.
“It was our chance to prove what we could do,” Professor Xinhua Wu, the director of the Monash Centre for Additive Manufacturing, said in a statement. “We took the engine to pieces and scanned the components. Then we printed two copies.”
This technology allows for simpler production techniques — such as printing two components at once — and designs to be tweaked more easily and parts to be printed as needed.
The jet engine.
Image: MCAM
The researchers are currently doing cost analysis to discover the parts worthwhile to 3D print, compared with parts that should remain manufactured in the traditional way. Testing is also underway to see what parts of the prototype would be feasible to produce on a larger scale for aerospace companies. Already, Amaero has been commissioned to make hundreds of prototype fuel injectors for testing.
Ben Batagol, business development manager for Amaero Engineering, said: “It was a challenge for the team and pushed the technology to new heights of success –- no one has printed an entire engine commercially yet.”
3D printing in the aerospace industry has been around for decades, but emerging technology that allows the melting of metal powders is opening up the door to the possibilities for widespread use and exciting developments in the field.
BONUS: What Is 3D Printing and How Does It Work?
Have something to add to this story? Share it in the comments.
自動翻譯僅供參考
忘掉食物和武器,第一款3D打印噴氣發動機已經來臨 2015年2月26日2時08分35秒UTCForget食品和槍支,第一款3D打印噴氣發動機有arrivedJenniBy珍妮RyallAustralia2015-02-26 2時08分35秒UTC
有一天,有3D打印奧利奧,下有3D打印噴氣發動機。 3D打印的世界已經起飛,與最新發展直出澳大利亞。
研究人員在墨爾本莫納什大學與來自CSIRO和迪肯大學的幫助印有不是一個,而是兩個金屬噴氣發動機。
概念驗證的原型與蒙納士的商業機構,Amaero工程的合作伙伴關系,已經引起了國際航空航天公司,如空中客車公司,雷聲公司和波音公司的利益。
3D打印在航空航天工業中的使用有助于減少在項目上花費的時間,創造更輕的引擎,同時降低操作和生產成本,根據StaskTeal技術的白皮書。使用印刷模型可以減少多達90%的浪費,這不僅降低了成本,而且減少了制造業對環境的影響。
研究人員由法國航空航天供應商賽峰集團可能被拉開,并使用3D打印機復制提供了一個古老的輔助動力的燃氣渦輪發動機。的過程中,被稱為添加劑制造,允許金屬的粉末形式可以熔融,然后熔合在一起成為使用激光的對象。
“這是我們的機會來證明我們可以做什么,”新華武教授,莫納什中心添加劑制造的主任,在聲明中說。 “我們采取了發動機件和掃描組件。然后,我們打印一式兩份。“
此技術允許更簡單的生產工藝 - 諸如打印兩個組件在一次 - 和設計能夠更容易地調整和根據需要被印刷的部分。
莫納什
噴氣發動機。
研究人員目前正在做成本分析來發現值得三維打印的部分,部件應在傳統的方式保持。制造比較。測試也正在進行中,看看有什么原型的部分會產生對航空航天公司規模較大可行的。目前,Amaero已委托進行數百原型的燃料噴射器進行測試。
本Batagol,為Amaero工程業務發展經理,說:“這是為球隊的挑戰,并推動該技術的新高峰 - 沒有人打印的整個發動機市場上還沒有。”
3D打印在航空航天工業已經存在了幾十年,但新興的技術,讓金屬粉末熔化的開放之門的可能性在該領域的廣泛使用和令人振奮的發展。
獎金:什么是3D打印,它是如何工作的?
有什么要補充的這個故事?
-
3D打印
+關注
關注
26文章
3547瀏覽量
109028
發布評論請先 登錄
相關推薦
虹科免拆案例 | 2014款保時捷卡宴車發動機偶爾無法起動
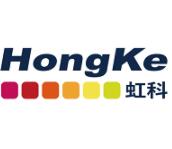
直噴發動機和電噴發動機的區別
2017款奔馳E300L車行駛中發動機偶爾無法加速
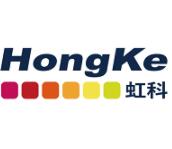
虹科免拆診斷 | 2010款凱迪拉克SRX車發動機無法起動
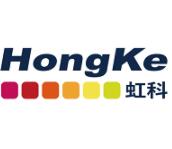
基于隱形飛機噴氣式發動機雙S彎噴管的纖維纏繞工藝
1994款凱迪拉克fleetwood車發動機無法起動
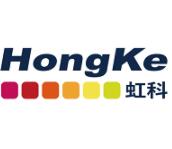
發動機故障燈亮是什么原因 發動機故障燈閃爍是什么問題
飛機發動機盤點:飛機發動機類型有哪幾種
汽車發動機:六沖程發動機工作原理
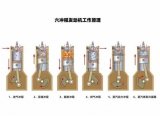
評論