第一眼看到斯柯達全新明銳,給我印象最深的莫過于其外開式的全景天窗以及掀背式的尾箱蓋設計。這款車在大眾全新MQB平臺基礎上開發設計而來,在外觀上融合了捷克波西米亞以及德意志嚴謹的設計風格,并且在車輛安全方面與時俱進地融入了許多科技元素如MCB多次碰撞制動系統、CBC彎道控制系統等。接下來我們將從制造層面探秘不一樣的新明銳。
● 全新MQB平臺介紹
MQB屬于大眾汽車未來模塊化平臺之一,用于開發小型至中型轎車,覆蓋大眾、奧迪、斯柯達和西亞特等多個品牌。該平臺的發動機采用橫向前置布局,在此基礎上可調整輪距、軸距和懸掛,開發出不同車型。不同車型可共線生產,從而大幅提高了生產靈活性并縮減了成本。
大眾第一款使用MQB平臺技術打造的車型是奧迪A3,在中國投產的第一個MQB平臺車型是高爾夫7。高爾夫7于一汽-大眾佛山工廠投產,也是佛山工廠投產的首款車型。而大眾目前橫置平臺的所有小型、緊湊和中型車,諸如POLO、新甲殼蟲、捷達、帕薩特等,新一代型號均將以MQB平臺作為基礎。
模塊化設計令前后懸、前后輪距等都可以調整,令軸距更長,MQB平臺全新明銳的長寬高分別達到了4659/1814/1460mm,軸距達到了2686mm。正是平臺帶來的靈活性才奠定了新明銳優秀的空間表現。
● 新明銳寧波工廠參觀
由于涉及到新車型保密的原因,本次工廠參觀只是走馬觀花,廠區內不允許拍照,以下所用圖片均由廠家官方提供,望讀者見諒!接下來就斯柯達寧波工廠沖壓、焊裝、涂裝以及總裝車間的兩點做相關介紹。
沖壓車間亮點:自動化高速壓機、多層鍍層材料零件全方位檢驗以及高強度一體成型零件。車間用到的沖壓模局均由歐洲頂尖模具廠商提供,生產過程中熱成型技術采用德國布特勒BTR公司的產品。沖壓線有兩條,分別為8100噸以及6900噸。
自動化高速壓機的特點是縮短了壓機之間的距離與零件的傳遞時間,從而提高了生產效率,整線最高無故障沖次可達15次/分鐘,模具更換自動換,整套模具的更換僅需4分鐘,可實現零件小批量、多品種的柔性化生產,目前流水線上有4臺KUKA機器人協同工作;另外,鋼板采用的是雙面鍍鋅技術,能夠提高鋼板的耐腐蝕性。
焊裝車間亮點:車頂背包帶、側圍落水槽出均采用激光焊接工藝、UIR自適應焊接技術應用、世界先進壓鉚工藝以及高精度擰緊槍運用。焊裝車間生產節拍51s,共有焊裝機器人530臺,整車大約7455個焊點,車間自動化率達到86%。
一般激光焊都用于車頂、側圍,寧波工廠車身車間運用激光焊接的部位除了這兩個外還包括側圍落水槽等共160個等效焊點位置,業內屬于領先,能夠提高整車噪音隔離的效果;UIR技術能夠自動調整焊接時間和電流,實現對板材間隙、表面質量、材料變化等擾動因素的自動補償;高精度擰緊槍則可以把擰緊力精確到0.01Nm,并對每一棵擰緊的螺栓擰緊力數據存入數據庫,可對不合格螺絲扭矩進行追溯以及分析。
涂裝車間亮點:車身翻轉技術、底部PVC防石擊保護膜噴涂、車身內部空腔注蠟工藝。涂裝車間還采用了內部稱作2010工藝的生產方式替代了傳統工藝,簡單來講就是將水性漆替代溶劑型漆,并且取消了中涂工藝,和傳統工藝相比較該工藝能夠大幅降低30%的能耗。
車身翻轉技術相比較傳統鏈條式技術能夠減少槽體的長度和寬度,并且去離子對用量和廢水排放量能夠降低30%左右,車身翻轉運動會造成良好的湍流效應,可提高脫脂和磷化的質量,有效杜絕電泳死角的產生,保證車身每個立柱和角落都得到均勻的電泳涂層,確保車身12年防腐;車身空腔注蠟是對車身空腔注射防腐蠟,使車身的內腔內表面形成致密的保護蠟層,新明銳每輛車身注蠟約2kg左右,行業處于領先水平。
總裝車間亮點:高精度擰緊槍及數據上傳系統、高強度雨淋試驗以及煙霧試驗。其中高精度擰緊槍和焊裝車間的裝配類似,總裝共裝配186把高精度擰緊槍用于車輛重要螺栓的擰緊,使用RFID代替條碼槍掃描,高精度槍數據能夠保存至服務器15年。
高強度雨淋試驗雨淋參數為2-8bar,高于行業內一般水平(2bar),壓力逐級增加,長達70min動態強化雨淋,保證整車在360°內均可雨淋覆蓋,模擬極端惡劣環境,確保整車密封性長期有效;煙霧試驗營造車內外產生環境壓力差,將車外煙霧吸入車內,可直觀發現煙霧進入車內的位置,為后續改進提供指導。
總結:官方給我們介紹全新明銳整體的設計風格符合精準以及永恒的主題。大概意思是只有在設計以及制造上到達絕對的精準,車輛才會“0”事故地永恒流傳下去。從斯柯達寧波工廠的探秘中我們可以發現,工廠無論是制造設備、管理培訓以及人員操作上都達到了近乎“嚴苛”的要求,這對消費者來說是值得信賴的。
-
大眾
+關注
關注
1文章
783瀏覽量
34033 -
斯柯達
+關注
關注
2文章
38瀏覽量
3897
發布評論請先 登錄
相關推薦
2025寧波國際照明展覽會
名單公布!【書籍評測活動NO.50】親歷芯片產線,輕松圖解芯片制造,揭秘芯片工廠的秘密
智慧燈桿與寧波共建5G智慧城市!
走進上汽大眾寧波工廠:機器人激光焊接,讓制造更高效、更環保
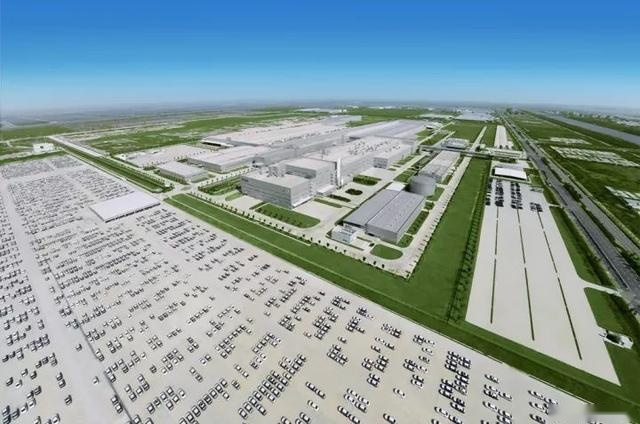
中芯寧波嚴正聲明!絕不諒解
2024寧波國際照明展展位即將售罄,欲購從速!
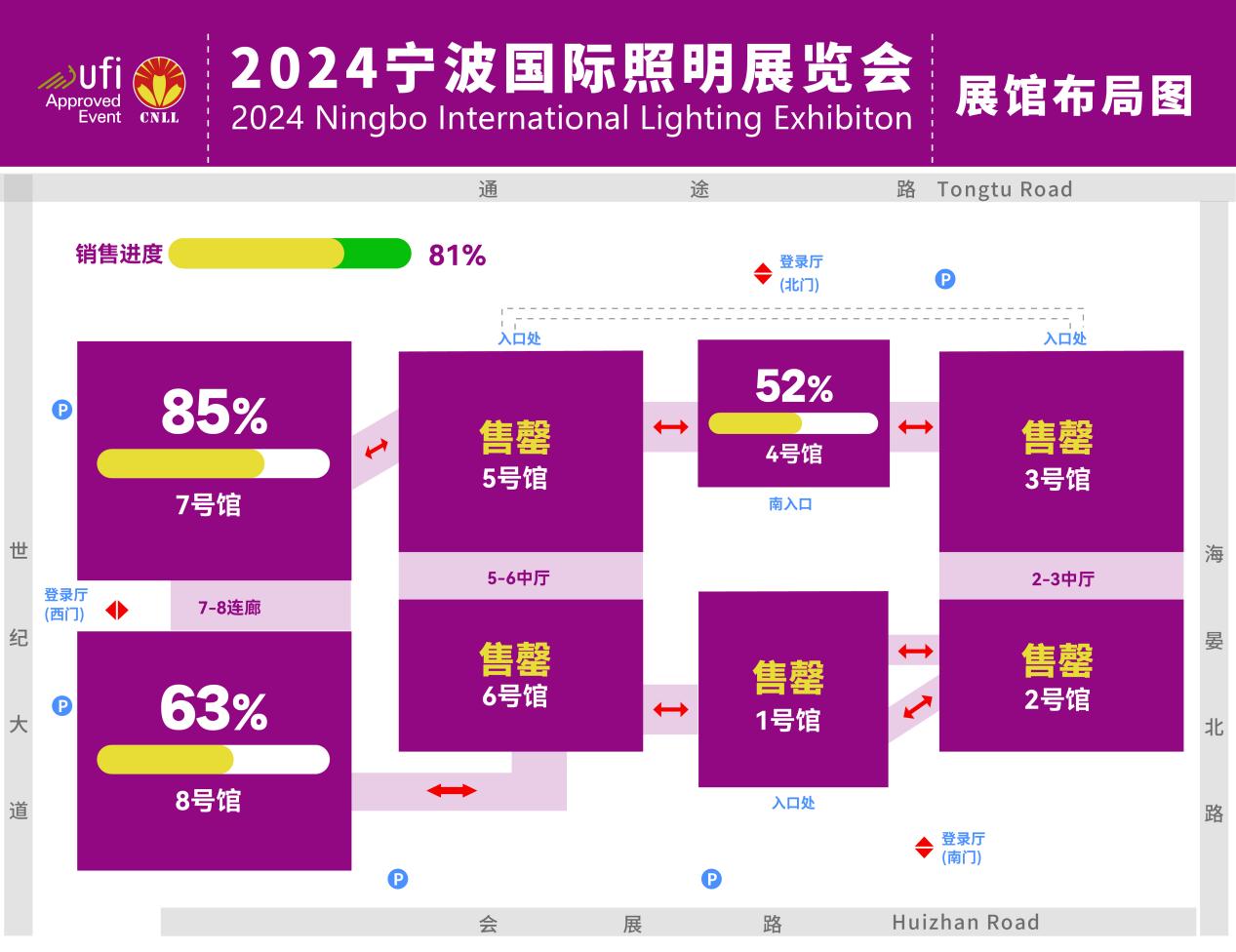
評論