隨著科學技術水平不斷的提高,磨削加工已廣泛應用于金屬及其他材料的粗、精加工,是非常重要的切削加工方式。目前,磨削加工已經成為現代機械制造領域中實現精密與超精密加工最有效、應用最廣泛的基本工藝技術,為人們提供高精度、高質量、高度自動化的技術裝備的開發和研制。
精密磨削中超硬磨料砂輪
精密磨削技術
磨削是指用磨料或磨具去除材料的加工工藝方法,一般來講,按照砂輪線速度的高低可將其進行分類,把砂輪速度低于45 m/s的磨削稱為普通磨削,把砂輪速度高于45 m/s的磨削稱為高速磨削,把砂輪速度高于150m/s的磨削稱為超高速磨削。
按磨削效率將磨削分為普通磨削、高效磨削(高速磨削、超高速磨削、緩進給磨削、高效深切磨削、砂帶磨削、快速短行程磨削和高速重負荷磨削)。
磨削加工能達到的磨削精度在生產發展的不同時期有不同的精度范圍,當前,按磨削精度將磨削分為普通磨削(加工精度>1μm、表面粗糙度R a0.16~1.25μm)、精密磨削(加工精度1~0.5μm、表面粗糙度R a0.04~1.25μm)、超精密磨削(加工精度≤0.01μm、表面粗糙度R a≤0.01μm)。
精密加工是指在一定發展時期中,加工精度和表面質量達到較高程度的加工工藝,當前是指被加工零件的加工精度為l~0.1μm,表面粗糙度值Ra0.2~0.01μm的加工技術。
精密磨削是目前對鋼鐵等黑色金屬和半導體等脆硬材料進行精密加工的主要方法之一,在現代化的機械和電子設備制造技術中占有十分重要的地位。
精密磨削一般使用金剛石和立方氮化硼等高硬度磨料砂輪,主要靠對砂輪的精細修整,使用金剛石修整工具以極小而又均勻的微進給(10~15mm /min)。獲得眾多的等高微刃,加工表面磨削痕跡微細,最后采用無火花光磨。
由于微切削、滑移和摩擦等綜合作用,達到低表面粗糙度值和高精度要求。高精密磨削的切屑很薄,砂輪磨粒承受很高的應力,磨粒表面受高溫、高壓作用,一般使用金剛石和立方氮化硼等高硬度磨料砂輪磨削。
精密與超精密磨削的機理與普通磨削有一些不同之處:
1)超微量切除。應用較小的修整導程和修整深度精細修整砂輪,使磨粒細微破碎而產生微刃。一顆磨粒變成多顆磨粒,相當于砂輪粒度變細,微刃的微切削作用就形成了低粗糙度。
2)微刃的等高切削作用。微刃是砂輪精細修整而成的,分布在砂輪表層同一深度上的微刃數量多,等高性好,從而加工表面的殘留高度極小。
3)單顆粒磨削加工過程。磨粒是一顆具有彈性支承和大負前角切削刃的彈性體,單顆磨粒磨削時在與工件接觸過程中,開始是彈性區,繼而是塑性區、切削區、塑性區,最后是彈性區,這與切屑形成形狀相符合。
4)連續磨削加工過程。工件連續轉動,砂輪持續切入,開始磨削系統整個部分都產生彈性變形,磨削切入量(磨削深度)和實際工件尺寸的減少量之間產生差值即彈性讓刀量。此后,磨削切入量逐漸變得與實際工件尺寸減少量相等,磨削系統處于穩定狀態。最后,磨削切入量到達給定值,但磨削系統彈性變形逐漸恢復為無切深磨削狀態。
精密磨削技術的歷史與發展
磨削加工是利用磨料去除材料的加工方法,也是人類最早使用的生產技藝方法。
18 世紀中期世界上第一臺外圓磨床問世,由石英石、石榴石等天然磨料敲鑿成為磨具,用天然磨料和粘土燒結成砂輪,隨后又研制出平面磨床。
20 世紀40 年代末,人造金剛石出現;1957 年立方氮化硼研制成功;隨著磨削技術的發展,特別是超硬磨料人造金剛石砂輪與立方氮化硼砂輪的應用,磨削加工應用范圍日益增大,磨削加工精度及加工效率也不斷提高。
磨削技術得到快速發展,磨床在加工機床中也占有相當大比例。據1997 年歐洲機床展覽會(EMO)調查數據表明,25% 企業認為磨削是他們應用最主要加工技術,車削只占23% ,鉆削占22% ,其它占8% ;而磨床在企業中占機床比例高達42% ,車床占23% ,銑床占22% ,鉆床占14% 。
我國從1949~2007 年,開發生產通用磨床有1800 多種,專用磨床有幾百種,磨床擁有量占金屬切削機床總擁有量15% 左右。可見,磨削技術及磨床在機械制造業中占有極其重要位置。
近年來,國外對精密和超精密磨削技術的開發研究獲得了不少成果,主要體現在ELID鏡面磨削新工藝的研究和加工硅片以及非球面零件的應用上。
日本國家理化學研究所的大森整教授于1987年研制成功了在線修整砂輪的ELID鏡面磨削新工藝。
ELID鏡面磨削技術是利用在線電解修整作用連續修整砂輪來獲得恒定的出刃高度和良好的容屑空間,同時,在砂輪表面逐漸形成一層鈍化膜,當砂輪表面的磨粒磨損后,鈍化膜被工件表面磨屑刮擦去除,電解過程繼續進行,對砂輪表面進行修整,加工表面粗糙度Ra達到0.02~0.01μm,表面光澤如鏡。
美國在應用ELID磨削技術加工電子計算機半導體微處理器方面已取得突破性進展,在國防、航空航天及核工業等領域的應用研究也在進行,PeiZJ等人對自旋轉磨削法精密磨削硅片的加工過程以及加工參數、砂輪粒度、冷卻液供給等加工條件對磨削力、硅片面型精度、表面磨削紋路、表面粗糙度的影響進行了系統的試驗研究。
德國是最早研究ELID磨削技術的幾個國家之一。在1991年就有德國的機床廠家進行了系列ELID專用機床的設計。此外,英、法等國對ELID磨削技術也進行了深入的研究。
我國對精密磨削的研究尚處于初級階段,主要集中在高校。哈爾濱工業大學以袁哲俊教授為首的ELID課題組研制成功了ELID磨削專用的脈沖電源、磨削液和砂輪,在國產機床上開發出平面、外圓和內圓ELID磨削裝置,實現了多種難加工材料的精密鏡面磨削。目前正積極推廣普及該技術,實現其產品化。東華大學機械學院的研究者利用固結磨粒低頻振動(頻率f為0.5~20Hz、振幅為0.5~3mm)壓力進給的精整加工,研究了適宜的經濟加工條件及有關參數,并驗證了經過磨削加工后的陶瓷工件,再經過超精加工可以進一步降低其表面粗糙度,可降低2~4個等級。清華大學在集成電路超精密加工設備、磁盤加工及超精密砂帶磨削和研拋、金剛石微粉砂輪超精密磨削等方面進行了深入研究,并有相應產品問世。
ELID磨削技術
ELID磨削技術是應用電化學反應的非傳統材料去除技術來解決金屬基超硬磨料砂輪的修整問題的超精密鏡面加工技術,以其效率高、精度高、表面質量好、加工裝置簡單及適應性廣等特點,已較廣泛用于電子、機械、光學、儀表、汽車等領域。
ELID磨削的基本原理
ELID(Electrolytic In-process Dressing)磨削是在磨削過程中,利用非線性電解修整作用使金屬結合劑超硬磨料砂輪表層氧化層的連續修整用與鈍化膜抑制電解的作用達到動態平衡。從而獲得穩定厚度的氧化層,使砂輪磨粒獲得恒定的出刃高度和良好的容屑空間,實現穩定、可控、最佳的磨削過程,它適用于硬脆材料進行超精密鏡面磨削。
ELID磨削的必備裝置主要有磨床、電源、電解裝置、電解液和砂輪五個要素。
其工作原理是:金屬結合劑超硬磨料砂輪的轉軸與電刷的接觸而接通電源正極作為陽極,銅電極(工具電極)與電源負極相接作為陰極。砂輪與負極之間存在100~500μm的間隙(間距可調),利用噴嘴噴出具有電解功能的磨削液使之充滿間隙。在高電壓(60~120v)和高脈沖頻率電源的作用下,使磨削液電解產生陽極溶解效應,將砂輪表層的金屬基體電解去除,與此同時,在砂輪表面會產生一層絕緣的鈍化膜能有效抑制金屬基體的過度電解,以減少砂輪基體的過分電解損耗。因為氧化膜極易磨損,從而容易使新的磨粒露出鋒利的棱角以達到修銳效果。整個加工過程中電解作用與鈍化膜的抑制作用達到動態平衡,保證了磨粒的恒定的突出量,使砂輪在加工過程中始終保持有磨粒突出的最佳磨削狀態。該技術將砂輪的在線修整與磨削過程結合在一起,從而實現對工件的連續超精密鏡面磨削。
ELID超精密磨削的過程可分為四個階段,具體歸納如下圖。
如下圖ELID鏡面磨削基本原理圖(a)所示,在砂輪修正前,砂輪由磨粒和金屬結合劑組成,磨粒均勻分布。在進行磨削加工前,需單獨對砂輪進行電解修整工作(圖b),在砂輪表面電離溶解一層金屬結合劑,以一定厚度的鈍化膜取而代之。一方面能有效減小砂輪的形狀誤差,另一方面能預先生成具有一定彈性的鈍化膜,防止開始磨削時砂輪切入是造成工件的硬質劃傷。
在磨削開始后,由于氧化膜極易磨損,固定在氧化膜中的磨粒路出鋒利的棱角,其可以視為無數大小型刀具對工件表面進行微切削作用。砂輪在通過與工件的接觸區域后,由于工件材料的刮擦作用,磨粒磨損鈍化,出刃高度降低,磨削效果變弱。由于鈍化膜變薄,導電性恢復,當砂輪轉到工具電極位置時,在電解液的作用下,砂輪表面形成新的氧化膜,使磨料出刃高度增加(如圖c)。當氧化膜達到磨損前的厚度時,電阻足夠大而起到絕緣作用,使電解作用終止。
由此可知,由于這種非線性電解作用的結果,使得修整過程對磨削過程有一定的自適應能力,砂輪在每個旋轉周期內都保持以相同厚度的氧化層和相同出刃高度的磨粒進行磨削,即砂輪表層氧化膜的電解生成與磨損達到動態平衡,最終使得砂輪表面結合劑基體不斷被電解,新的磨料不斷地露出,以保證金屬基砂輪在磨削過程中的銳利性。
這種磨削方法即不會由于表層磨料的磨損和脫落而失去切削能力造成切屑堵塞現象,又不會造成砂輪的過快消耗,能充分發揮超硬磨料的磨削能力,非常有利于對硬脆材料實現高精度、高效率的超精密鏡面磨削。
精密磨削存在的問題以及發展前景
精密和超精密磨削技術在各方面均取得迅速發展,已成為先進制造技術的關鍵技術之一.在今后的研究中應著重關注以下幾個問題:
1)超精密磨削的基本理論和工藝研究,著重研究多顆粒磨削機理、磨削表面生成及影響因素等;
2)開發高精度、高性能、高自動化的加工機械及測試裝置的移動導向機構及軸承;
3)目前ELID鏡面磨削技術存在的問題是向高速回轉的砂輪供電非常困難,通常采用接觸式電刷供電設備,該設備復雜昂貴,影響了ELID鏡面磨削技術的推廣應用;
4)開發適于超精密加工并能獲得超高精度,超高表面質量的新型材料,如超微粉燒結金屬、新高分子材料等。
磨削技術發展很快,在機械加工中起著非常重要的作用。目前,磨削技術的發展趨勢是:發展超硬磨料磨具,研究精密及超精密磨削、高速高效磨削機理并開發其新的磨削加工技術,研制高精度、高剛性的自動化磨床。
隨著機械產品精度、可靠性和壽命的要求不斷提高,高硬度、高強度、高耐磨性、高功能性的新型材料的應用增多,磨削加工技術在磨削機理、磨料磨具開發、精密超精密磨削、高速超高速磨削、磨削自動化和智能化、磨削工藝過程監控與檢測技術、磨削加工軟件技術等方面發展迅速,在機械加工中起著至關重要的作用。因此,我們應深入研究國外先進磨削技術,系統地開展和推廣各種先進與實用的磨削技術,積極推進我機械制造工藝技術的進步。
上海康匯研發生產的U-How?容積式旋轉活塞流量計,屬于精密加工計量器件,經過北京市計量檢測科學研究院檢測認證,精度達到1.0級。為確保流量計轉子達到50萬轉次以上和腔體容積的穩定性,腔體及轉子等主要部件,均用精密磨削工藝加工,保證部件尺寸精度達到1μm以上。
U-How?康匯燃油流量計
U-How?康匯流量計是上海康匯實業發展有限公司,根據旋轉活塞式工作原理自主研發生產的,具有測量流速低、量程寬、精度高、結構簡單、工作安全可靠等特點的高精度流量傳感器。
工作原理
旋轉活塞式流量計,是屬于容積式流量計,它基于活塞與計量室一直保持的相切密封狀態。并有一個固定的偏心距計量元件活塞,在壓差的作用下,對活塞產生轉動力矩,使活塞做偏心旋轉運動,活塞的轉數正比于流體的流量,通過記數機構記錄出活塞轉數,即可測得流體總流量。
旋轉活塞式流量計進出口由隔板隔開。當被測流體從進口進入計量室,這時進出口形成壓差,迫使活塞逆時針旋轉如圖a所示。流體連續流入,迫使活塞轉動如圖b所示,形成二個半月牙腔體,在壓差作用下迫使活塞轉動如圖c,V2流體從出口排出,使活塞轉動如圖d所示,在壓差作用下轉動,活塞每轉一周迸出的流體等于V1+V2的和。
工作原理圖
流量計爆炸圖:
產品參數
1、機械部分:
型號 |
PDFM 4D |
PDFM 8D |
PDFM 8Db |
液壓連接器 |
M14 x1.5 |
M14 x1.5 |
M16/22 x1.5 |
最大工作壓力 (MPa) |
2.5 | 2.5 | 2.5 |
測量范圍 (l/h) |
1~ 80 |
20~ 200 |
80~ 320 |
精度 (﹪) | ±1 | ±1 | ±1 |
重復率 (﹪) | ±0.2 | ±0.2 | ±0.2 |
測量室體積 (ml) |
5 | 12.44 | 12.44 |
內置濾網尺寸 (mm) |
0.125 | 0.15 | 0.15 |
工作溫度 (℃) |
﹣20 ~80 |
﹣20 ~80 |
﹣20 ~80 |
存儲溫度 (℃) |
﹣40 ~100 |
﹣40 ~100 |
﹣40 ~100 |
2、電子部分:
型號尺寸 | KHDQ |
工作電壓 (V) | 9~40 |
輸出接口 | RS485/RS232 |
數據線 | 2×0.75 |
工作溫度 (℃) | ﹣20~80 |
存儲溫度 (℃) | ﹣40~100 |
測量介質:
可測量輕質和中質油料,如:汽油、柴油、煤油、石腦油、潤滑油
產品資質
1. 發明專利:ZL201020504169.8流量傳感器
2. 國家汽車質量監督檢驗中心車輛檢測報告
3. 交通部委托北京計量院精度檢測報告
油耗監控解決方案
應用對象
1.發動機:
火車、汽車、工程車、拖拉機、發電機組及內河或近海航行的船舶中測量各類動力機器的燃油消耗量,及各種較重液體的裝卸計量和管道過液計量。
2.燃燒器:
車載鍋爐、移動鍋爐等設備的燃油消耗計量。
數據采集方式
通過采集流量計脈沖數據的方式,以RS485/RS232對接設備單位的系統集成
解決方案
實施案例
某大型石油集團:
吊管機、移動電站、多功能車、彎管機、空壓機等
某大型采油廠:
鍋爐車、清蠟車、超導車、水泥車、吊車等;
港口:
龍門吊、堆高機、正面吊、裝載機等
其它:
輪胎胎壓油耗測試;駕駛員駕駛技術比武;發動機性能標定
空壓機
鍋爐車
-
自動化
+關注
關注
29文章
5562瀏覽量
79240 -
機械制造
+關注
關注
1文章
105瀏覽量
15092
原文標題:高端制造的精密磨削技術
文章出處:【微信號:WW_CGQJS,微信公眾號:傳感器技術】歡迎添加關注!文章轉載請注明出處。
發布評論請先 登錄
相關推薦
什么電阻才屬于精密電阻?精密電阻技術的歷史演進
RTOS發展歷史
INA軸承影響磨削變質層的因素
嵌入式系統的發展歷史
如何延長磨削電主軸的壽命?深圳廠家教你
磨削電主軸保養方法 深圳廠家告訴你
磨削溫度場的計算機仿真技術的應用研究

功率放大器超聲橢圓無心磨削技術研究中的應用
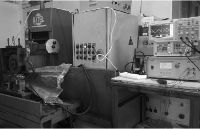
評論