中國石化產業的工業化水平從規模上已經躋身世界前列,但大而不強、大而不優是我國石化行業的現狀。中國石化是我國石化行業數一數二的特大型國有企業,如何通過數字化轉型迎接競爭與挑戰,看中國石化信息化管理部主任、石化盈科董事長李德芳怎么說。
經過數十年的發展,中國石油化工產業的規模、產量和能力都有了大幅度的提升——化學品產量位居世界第一,煉油能力位居世界第二,2017年已達7.7億噸;同時還擁有自主開發的催化裂化、加氫裂化等6大煉油核心技術,以及千萬噸級煉油、百萬噸級乙烯和芳烴生產等5大成套技術。可以說,中國石化產業的工業化水平從規模上已經躋身世界前列。
但是,我國石化工業目前還是大而不強、大而不優,主要存在產業布局不盡合理,較為分散;煉油裝置開工率僅為72%,產能過剩;通用產品所占比例較高,高端產品自給率不足;能耗、物耗較高,安全環保壓力較大,生產成本較高等問題。
除了上述這些傳統產業本身所面臨的壓力之外,特別是新一輪的ICT革命、能源革命以及電動汽車革命,對中國石化行業發展帶來了嚴峻挑戰。電動汽車的發展引人注目,中國的電動汽車保有量正在不斷攀升,面對新能源汽車的異軍突起,傳統石化企業是否陷入了發展危機?此外,石化行業在安全和環保方面也迫切需要實現本質提升。這些變化時刻提醒著石化行業乃至整個能源產業中的廣大傳統企業,在制定未來發展規劃時必須要有超前的戰略思考。
中國石油化工集團公司(簡稱中國石化)是我國石化行業數一數二的特大型國有企業集團,在2017年“財富世界500強”企業中排名第3位。作為一家傳統企業,中國石化在轉型發展過程中同樣面對著上述挑戰,如何應對必須引起企業的高度重視和深入思考。
▌中國石化的智能制造之路
對于中國石化來說,智能制造是推動我國石化工業向高效化和綠色化方向發展,實現由大變強的必由之路。以石化行業為代表的流程行業具有以下顯著特點:存在復雜的物理化學過程;生產過程耦合性強,難以建立數學模型,難以實現數字化;原料復雜、生產工況波較動大等,在邁向智能制造的過程中面對著更多的挑戰。
以德國的“工業4.0”為代表的針對離散工業的智能制造模式不完全適用于流程工業,要實現流程工業的高效化和綠色化,必須自主創新,探索適合我國流程工業特點的智能制造模式。為此,中國石化以旗下的石化盈科為主體,聯合國內的一些高等院校以及華為、埃森哲等國內外領先ICT企業,展開自主研發,打造了石化自己的工業物聯網平臺和智能制造平臺。
中國石化在智能制造領域進行了長期的探索與實踐,其建設歷程可以分為3大階段:
? 2003~2011年, MES系統(生產執行系統)建設和推廣階段。實現自主研發的MES系統在中國石化煉化企業全覆蓋,并推廣到神華、中煤等大型企業;對于這些傳統企業生產管控水平的提高起到了很大作用,為石化工業的數字化、網絡化和智能化奠定了一定的基礎;
? 2012~2015年,智能工廠規劃與試點階段。完成智能工廠總體規劃和設計,在燕山石化、鎮海煉化、茂名石化和九江石化這4家下屬企業開展試點,打造了石化“智能工廠1.0”版,形成了相關理論、解決方案和核心軟件產品,2015年九江石化還被國家樹立為智能制造試點示范;
? 2016年至今,智能工廠升級與ProMACE石化智云建設階段。啟動“智能工廠2.0”建設,與華為開展合作,打造ProMACE 2.0,鎮海煉化和茂名石化分別于2016年和2017年被國家樹立為智能制造試點示范;除此之外,還在2016和2017年連續兩年承擔國家智能工廠標準制定,2017年石化盈科還入選了全國“第一批智能制造系統解決方案供應商推薦目錄”。
智能工廠的建設也使中國石化的數字化、網絡化和智能化水平不斷提升,有效促進了企業的轉型升級和提質增效,取得了一系列顯著成果——整個公司的勞動生產率平均提升了10%以上,對生產數據的自動采集率達到95%以上,對重點環境排放點實現了100%的實時監控與分析預警。公司下屬的鎮海煉化的乙烯裝置績效進入全球第一群組,2015~2017年連續3年利潤超過百億;茂名石化2016年勞動生產率比2013年提升近一倍,2017年效益也首次突破百億元;九江石化2015年起扭虧為盈,2017年盈利超16億,在同規模企業中效益名列前茅。
在建設“智能工廠1.0”、特別是隨后向“智能工廠2.0”提升的過程中,ProMACE智能工廠解決方案的應用為中國石化各個方面都帶來了重要的改變:
?生產操作協同聯動。率先在煉化企業建成了工業4G無線網,實現了智能巡檢和內外操協同,提高了現場處置效率,操作平穩率提高5.3%,操作合格率從90.7%提升至99%;
?基于大數據的報警和預警。利用催化裝置的歷史數據分析和挖掘裝置的報警規律,形成知識庫并建立預警模型,將關鍵報警提前了1~2分鐘預警,為操作人員及時采取措施、規避生產風險爭取了寶貴時間;
?計劃調度協同優化。綜合利用機理建模技術與優化算法,通過計劃、調度和操作的協同優化,實現了生產全過程效益最大化,試點企業年綜合增效10億元以上;
?日效益分析優化。采用深度學習算法實現了生產的智能排產和動態優化,企業由月效益分析轉變為日效益分析;
?數字化物資倉庫。試點企業應用物聯網技術實現庫存物資實時盤點和智能配送,提高了物資管理效率,年減少庫存占用資金5000余萬元;
?全自動立體倉庫。鎮海煉化采用國產技術建成國內石化行業首個超大型、全自動且無人操作的聚丙烯立體倉庫,實現固體產品包裝和倉庫作業的自動化管理以及無人裝車發貨;
?三維數字化工廠。基于工程設計數字化交付成果建成三維數字化工廠,實現人員培訓、設備吊裝模擬、工程量估算、設備故障定位和應急演練等應用;
?設備健康和可靠性管理。利用大數據分析技術對設備運行狀態進行評估以及智能診斷,實現設備預知性維修,減少了非計劃停工;
?能源全過程管理。實現能源的供、產、轉、輸、耗全流程管理,支撐了能源管理中心建設;
?能流在線優化。建成了全廠蒸汽動力產、輸的優化模型,優化了鍋爐、汽輪機和換熱器等設備的操作,促進了節能減排和降本增效,企業年節約能源成本700萬元以上;
?應急指揮協同一體化。實現了報警、接警和處警的應急聯動和快速響應,依據爆炸、泄漏和火災等模型計算事件擴散影響范圍,指導現場救援;
?環保在線管控。通過“環保地圖”實現污染物排放(COD、氨氮、二氧化硫、VOCs)的實時監控、異常報警和信息推送。
▌打造“不一樣”的智能工廠
在“智能工廠1.0”建成以后,為什么中國石化還要繼續打造ProMACE石化智云?中國石化智能工廠試點建設起步于2012年,當時采用的還是傳統的信息系統架構。隨著2016年“智能工廠2.0”的啟動、新技術的發展以及業務需求的變化,我們建設系統的思路、途徑、方法、技術都需要進行調整。
按照《中國制造2025》國家戰略的要求,面向數字化、網絡化、智能化現代工廠的目標,我們提出“平臺+數據+服務”的建設模式,致力于打造一個“不一樣”的智能工廠,并與華為在2016年聯合推出了ProMACE石化智云。
這既是中國石化智能制造自身建設的需要,也是支撐整個流程工業,為整個行業提供服務的要求。同時,ProMACE石化智云將以智能工廠為核心,以智能物流、智能服務為紐帶,與智慧園區、智慧城市融為一體,形成傳統行業與信息技術深度融合的新模式、新業態,引領產業發展方向。
作為中國石化未來智能制造發展的主要支撐平臺,ProMACE主要具有如下5項核心要素:
?第一,安全可控的工業物聯網:通過全面感知與互聯互通形成泛在的工業物聯網環境,實現物料、產品、設備、環境和人員的感知、識別和控制;
?第二,開放智能的流程工業云平臺(工業PaaS):云平臺是智能制造的工業操作系統,提供集中集成、實時計算、智能分析、物聯網接入以及二/三維可視化5項核心能力;
?第三,融入最佳實踐的工業App:面向流程工業,提供融入了生產管控、安全、環保、設備和能源等最佳實踐的工業級核心應用;
?第四,基于行業經驗的專家服務:通過行業內的院士、設計大師、設備專家和工藝專家等,為客戶提供設備遠程診斷、煉化工藝指導和安全環保咨詢等特色服務;
?第五,標準與安全體系:ProMACE運行的保障。
可以說,ProMACE石化智云是物理信息系統(CPS)在石化行業智能工廠的具體實現, 也是流程工業CPS的具體實現,承載了我們對于物理工廠的模型化描述。站在流程工業的角度,主要有3個維度:一是對工廠資產的描述,通過工廠模型、三維模型等進行刻畫;二是對過程的描述,通過機理模型進行刻畫;三是各類數據匯聚形成大數據模型,隨著數據更新獲得自學習能力。利用ProMACE中的模型和數據,結合優化與控制,實現了計算進程與物理進程的交互,打造了流程工業的CPS。支撐了生產管控、供應鏈管理和資產全生命周期管理3條業務主線,并形成了新一代生產運營模式。
-
數字化
+關注
關注
8文章
8710瀏覽量
61730 -
工業物聯網
+關注
關注
25文章
2375瀏覽量
64116 -
智能制造
+關注
關注
48文章
5551瀏覽量
76319
原文標題:案例| 中國石化打造“不一樣”的智能工廠
文章出處:【微信號:mfg2025,微信公眾號:智能制造】歡迎添加關注!文章轉載請注明出處。
發布評論請先 登錄
相關推薦
DAC5682Z輸出不同頻率幅度不一樣,這是正常的嗎?
ADS1299各通道的噪聲偏置不一樣是哪里的問題?
空載時輸出波形如圖2所示,發現相位相反,幅度不一樣,為什么?
為什么不同的片子同相端的電壓不一樣?
TINA-TI仿真,為什么VF1和VG1的波形不一樣?
OPA817跟opa818一樣的封裝,為什么兩者的熱阻不一樣呢?
用iar debug進去的程序和用STVP燒錄的程序不一樣,為什么?
智能傳感器有什么不一樣
Khadas攜新品亮相,定義不一樣的“mini”
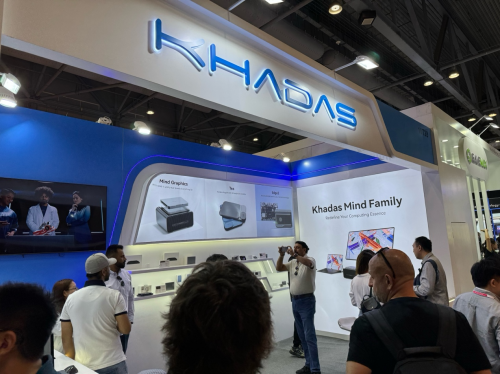
評論