加減速控制是CNC 系統的關鍵技術之一,也是實現數控系統高實時性的瓶頸。在CNC裝置中,為了保證機床在啟動或停止時不產生沖擊、失步、超程或振蕩,必須對進給電機的脈沖頻率或電壓進行加減速控制。即在機床加速啟動時,保證加在電機上的脈沖頻率或電壓逐漸增加;而當機床減速停止時。保證加在電機上的脈沖頻率或電壓逐漸減小。好的加減速控制算法除了應保證數控機床運動平穩,在啟停和程序段間速度有變化時不產生失步、超程、沖擊和振蕩外;還應當具有算法簡單、系統加減速處理時間短、實時性強的特點。此外,很好的柔性(通用性)也是必要的,以便適應不同配置的機床,特別是在高速加工中,這顯得尤為重要。
1 加減速控制方法
1.1 直線加減速控制方法
直線加減速控制方法是加減速控制方法中最為簡單的一種,也是最常用的一種。數控系統每插補一次,都要進行穩定速度、瞬時速度和加減速處理。整個過程共有加速、勻速、減速三個階段。
1.2 S 曲線加減速控制方法
直線加減速啟動和加減速結束時存在加速度突變,產生沖擊,因而不適合用于高檔的數控系統。一些先進的CNC 系統采用S 形加減速,通過對啟動階段即高速階段的加速度衰減,來保證電機性能的充分發揮和減小啟動沖擊。正常情況下S 曲線加減速的運行過程可分為7段:加加速段、勻加速段、減加速段、勻速段、加減速段、勻減速段、減減速段。
1.3 四次曲線加減速控制方法
是一種四次位移曲線,三次速度曲線的加減速控制方法。非常實用于高檔的數控系統上,具有算法簡單,柔性好的優點,是一種值得推廣的加減速模式。
2 四次位移曲線加減速系統總體結構與組成
2.1 系統硬件結構
本數控系統采用通用PC 機和單片機構成的主從式二級控制總體結構,系統硬件組成如圖1 所示,上位機采用通用PC 機,完成系統參數的設置、加工數據的實時計算和仿真等任務,而下位單片機系統完成不同方向的進給驅動控制,并從外部機器上獲取加工狀態的反饋信息,上、下位機間以中斷方式進行串行通信。
圖1 硬件系統結構框圖
下位機系統能根據主機命令,獨立完成全部數控功能,基于單片機技術設計的速度位置控制單元,用于同時對三軸((x, Y, z 向)電機進行多功能的控制。速度位置控制單元采用Winbond78E58 作為主控芯片。整個電路主要由開關量輸入控制電路、脈沖控制電路及通訊電路等組成。脈沖控制電路由三個定時/計數器8254 來實現對三個驅動電機的位置及速度控制。當前加工軌跡段運行完畢后可向主機申請中斷,78E58 也可通過查詢中斷的方式獲得當前運行狀態。開關量輸入電路可檢測限位開關、對刀儀等狀態,并向78E58 申請中斷。
2.2 系統軟件結構
根據數控機床的功能控制要求,并結合圖1 硬件總體結構,本數控系統的系統軟件,由PC 系統控制軟件和驅動接口卡軟件兩大部分組成,它們之間相互獨立,如圖2 所示。其中PC 機上的系統控制軟件采用面向對象的編程技術((OOP)、由高級編程語言Visual C++編制而成,各個功能模塊被獨立地封裝在不同的對象中,系統具有良好的擴充性和可移植性。驅動卡上的軟件部分由匯編語言編制而成。
PC 系統控制軟件負責整個系統的綜合管理、人機交互和數據處理等工作。具體由以下幾部分組成:人機接口部分、數據處理軟件部分、工作模式控制軟件部分、通信部分、診斷部分和聯機幫助系統軟件部分,各個部分各自包含一些獨立的功能模塊。其中,人機接口部分用于管理機床參數、提供NC 程序全屏幕編輯窗口并且可以在加工過程中動態顯示機床加工狀態,以實現用戶與系統之間的信息交互。數據處理軟件部分用于對NC 程序進行語法檢查和譯碼,間隙補償、加減速控制和插補運算等強實時功能。工作模式控制軟件部分提供各種常見的工作模式控制,協調控制機床實時運動,并實現動態圖形仿真功能。通信軟件部分用于實現PC 機和接口卡之間的雙向串行數據通信,保證數據通訊暢通。診斷軟件部分可以在系統工作過程中隨時發現系統故障、并指示故障類型,以實現在線診斷功能,保證系統正常運行。聯機幫助系統提供聯機幫助功能。
圖2 系統軟件的組成圖
接口卡軟件接收計算機發送的加工信息,驅動電機完成刀具幾何位置及運動速度的控制,并且反饋加工信息。PC 機和接口卡之間通過RS-232C 接口,按照自行定義的通信協議,以中斷機制實現具體功能的數據傳輸。整個系統已通過與驅動器和電機的聯機調試,取得了符合要求的控制效果。該系統的運行過程分為以下幾步:
2.2.1 開啟計算機,運行本系統控制軟件,檢測下位機的連接狀態是否正常,如異常會出現提示對話框。軟件啟動時,計算機上首先顯示啟動畫面,隨后便可進入系統控制界面。
2.2.2 設定或復位相關的系統參數后,可進行輔助加工工作:手動控制、回機械零點、對刀、碰邊對中((1/2 功能)及各方向置零、溫機等。
2.2.3 讀入加工代碼文件,前臺還原顯示加工路徑文件描述的圖形,可檢查加工的工件是否超過出了工作臺面的范圍,后臺解釋該文件,提取出數控命令和數控數據,將其存儲在約定的數據結構中,以供后續加工重復使用。
2.2.4 選擇不同加工方式:自動、模擬、選段。加工時,系統實時跟蹤加工過程及顯示加工進程中相關信息。另外在不關閉控制軟件的情況下,用戶可在計算機上操作其它軟件,不會影響系統的正常運行。
2.2.5 加工過程中,可執行急停和暫停命令。在暫停狀態下,可用手動控制任意移動主軸頭位置,不會影響繼續加工。在加工結束或急停后,自動將主軸頭Z 方向提升到安全高度。
2.3 工作過程
本系統共使用了三種加減速控制方法,分別是直線加減速、四次曲線加減速、S 曲線加減速。可以任意選擇一種加減速方式來進行實際加工,同時可根據實際情況,調整相應的參數使加工效果更趨于理想。
3 四次位移曲線加減速系統的實驗及結果分析
為了驗證微線段軌跡加工的實際效果,設計了三種插補器,一種是傳統的直線插補器,一種是具有微線段終點控制算法的直線插補器,最后一種是具有微線段插補終點控制算法的四次曲線插補器。對最具代表性的圓弧進行了實際加工,由于篇幅所限,圓弧的代碼段不顯示了,讀者需要請與作者聯系。
圖3 是經過傳統直線插補器插補后的理論曲線和實際加工曲線,由于速度變換頻繁,加工過程不穩定,從圖中可以看到在實際加工曲線中有微小的鋸齒型誤差存在。加工時間為2.960s。
圖3 采用傳統直線插補器的加工實例
圖4 是經過具有微線段終點控制算法的直線插補器插補后的理論曲線和實際加工曲線,從圖上可以看出理論曲線和實際加工曲線的差別已經很小,同時基本保持一個較高的速度在運行,在很短的線段內甚至可以達到最高速度,運行時間是1.704s。與上面的方法相比較,效率有很大的提高。
圖4 基于微線段終點控制算法的直線插補器加工實例
圖5 是經過具有微線段插補終點控制算法的四次曲線插補器插補出來的,實際加工曲線和理論加工曲線已經很逼近,同時速度基本上保持以較大值運行。運行時間是1.820s,雖然加工時間比基于微線段插補終點算法的直線插補器稍微慢一些,但它的柔性和平穩性卻是最好的。
圖5 四次曲線插補器加工實例
4 學術價值和創新點
由以上實驗數據結果表明,四次位移曲線加減速系統在加減速、定位、微線段插補終點控制等方面都取得了良好的效果。與傳統的數控系統相比,性能得到很大的改善。好的加減速算法要求進給過程中速度變化盡可能平穩,即要求系統加減速具有高度的柔性,同時程序復雜度要較小。傳統的直線加減速在進給過程中存在柔性沖擊,而S 曲線加減速程序分為很多段,變化復雜,實現起來有比較大的困難。而四次曲線加減速具有算法簡單,柔性好的優點,是一種值得推廣的加減速模式。
-
單片機
+關注
關注
6035文章
44553瀏覽量
634755 -
CAN
+關注
關注
57文章
2744瀏覽量
463633 -
數控系統
+關注
關注
5文章
260瀏覽量
24236
發布評論請先 登錄
相關推薦
解析四次位移曲線的CNC數控系統的研究
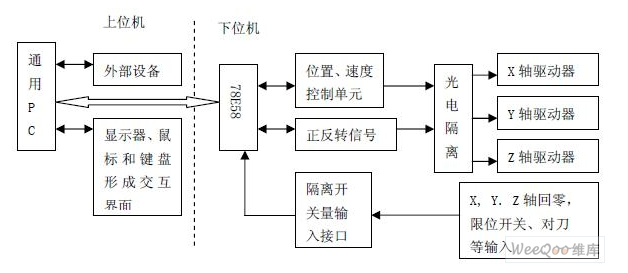
評論