控制系統的第一代產生于1930年到1940年,主要代表是以基地式儀表為代表的機械控制技術。第二代產生于1950年,主要是電氣控制技術為主的繼電器控制技術和調節器為代表的模擬控制技術。目前所稱的控制系統是第三代控制系統,誕生于二十世紀七十年代,主要技術代表是用于流程工業的集散控制系統(DCS)和用于離散工業的可編程控制器(PLC)。 PLC和DCS是第三代控制系統的代表,在冶金、電力、石油、化工、輕工等工業過程控制中應用的很多,PLC和DCS功能相似,但其實使用領域有很大的差別,PLC使用在如繞線機、包裝機等,而DCS則使用在航天、大型工業控制,最近幾年DCS和PLC公司都轉向共同稱之為“混合型控制系”的領域,嘗試著把DCS系統的強大功能、復雜性和PLC系統的靈活、開放性以及低價位結合起來。為此,DCS公司減少了其系統所占用的空間,而PLC公司則開始集成其組件以制造更完善的系統。
可編程控制器(Programmable Controller)是計算機家族中的一員,是為工業控制應用而設計制造的。早期的可編程控制器稱作可編程邏輯控制器(Programmable Logic Controller),簡稱PLC,它主要用來代替繼電器實現邏輯控制。隨著技術的發展,這種裝置的功能已經大大超過了邏輯控制的范圍,因此,今天這種裝置稱作可編程控制器,簡稱PC。但是為了避免與個人計算機(Personal Computer)的簡稱混淆,所以將可編程控制器簡稱PLC,plc自1966年出現,美國,日本,德國的可編程控制器質量優良,功能強大。
PLC是一種專門為在工業環境下應用而設計的數字運算操作的電子裝置。它采用可以編制程序的存儲器,用來在其內部存儲執行邏輯運算、順序運算、計時、計數和算術運算等操作的指令,并能通過數字式或模擬式的輸入和輸出,控制各種類型的機械或生產過程。PLC已經廣泛應用于鋼鐵、石油、化工、電力、建材、機械制造、汽車、輕紡、交通運輸、環保及文化娛樂等各個行業,它具有高可靠性、抗干擾能力強、功能強大、靈活,易學易用、體積小,重量輕,價格便宜的特點。
PLC技術發展呈現新的動向:產品規模向大、小兩個方向發展 大:I/O點數達14336點、32位為微處理器、多CPU并行工作、大容量存儲器、掃描速度高速化。 ?。河烧w結構向小型模塊化結構發展,增加了配置的靈活性,降低了成本。 2:PLC在閉環過程控制中應用日益廣泛 3:不斷加強通訊功能 4:。新器件和模塊不斷推出 高檔的PLC除了主要采用CPU以提高處理速度外,還有帶處理器的EPROM或RAM的智能I/O模塊、高速計數模塊、遠程I/O模塊等專用化模塊。 5:編程工具豐富多樣,功能不斷提高,編程語言趨向標準化 有各種簡單或復雜的編程器及編程軟件,采用梯形圖、功能圖、語句表等編程語言,亦有高檔的PLC指令系統 6:發展容錯技術 采用熱備用或并行工作、多數表決的工作方式。 7:追求軟硬件的標準化。
但是,目前市場上的用戶并不認為混合控制系統是一種革命性的新產品,也沒有將它們看成一個完全不同的產品。而且,目前的國內市場上,既存在如上所述的混合控制系統,也有可通過裝備回路控制板實現較多過程控制功能的PLC。但是,混合控制系統的概念切合了生產實際,是控制系統的發展趨勢。從理論上講,當代的DCS與PLC都是混合控制系統,但是作為一種產品,混合控制系統無疑為用戶提供了一種新的選擇。
隨著無線技術進一步為公眾所接收,其應用的范圍也在日益擴大,尤其在工業過程領域,無線技術對習慣于有線技術的工業過程領域所帶來的沖擊是巨大的。到目前為止,大多數的無線項目用于開環回路的監測,應該說,現今的無線技術是對有線技術強有力的補充。由于無線技術的應用,解決了有線技術由于投資成本及環境限制未能實現的功能,提升了過程控制精度,為工廠管理帶來極大效益。應該認識到,過程控制的無線化是一場靜悄悄的革命,是一個逐步滲透的過程,隨著人們認知程度的提高,以及無線技術更為可靠、連續、兼容的操作方式將給整個工業界以使用的信心,越來越多的無線設備將用于工廠。然而,安全有效的工廠操作總是放在第一位的,就目前來說控制功能的應用仍然是通過有線電纜來完成的。
DCS是分布式控制系統的英文縮寫(Distributed Control System),在國內自控行業又稱之為集散控制系統。即所謂的分布式控制系統,或在有些資料中稱之為集散系統,是相對于集中式控制系統而言的一種新型計算機控制系統,它是在集中式控制系統的基礎上發展、演變而來的。它是一個由過程控制級和過程監控級組成的以通信網絡為紐帶的多級計算機系統,綜合了計算機,通信、顯示和控制等4C技術,其基本思想是分散控制、集中操作、分級管理、配置靈活以及組態方便。
首先,DCS的骨架-系統網絡,它是DCS的基礎和核心。由于網絡對于DCS整個系統的實時性、可靠性和擴充性,起著決定性的作用,因此各廠家都在這方面進行了精心的設計。對于DCS的系統網絡來說,它必須滿足實時性的要求,即在確定的時間限度內完成信息的傳送。這里所說的“確定”的時間限度,是指在無論何種情況下,信息傳送都能在這個時間限度內完成,而這個時間限度則是根據被控制過程的實時性要求確定的。因此,衡量系統網絡性能的指標并不是網絡的速率,即通常所說的每秒比特數(bps),而是系統網絡的實時性,即能在多長的時間內確保所需信息的傳輸完成。系統網絡還必須非??煽?,無論在任何情況下,網絡通信都不能中斷,因此多數廠家的DCS均采用雙總線、環形或雙重星形的網絡拓撲結構。為了滿足系統擴充性的要求,系統網絡上可接入的最大節點數量應比實際使用的節點數量大若干倍。這樣,一方面可以隨時增加新的節點,另一方面也可以使系統網絡運行于較輕的通信負荷狀態,以確保系統的實時性和可靠性。在系統實際運行過程中,各個節點的上網和下網是隨時可能發生的,特別是操作員站,這樣,網絡重構會經常進行,而這種操作絕對不能影響系統的正常運行,因此,系統網絡應該具有很強在線網絡重構功能。
其次,這是一種完全對現場I/O處理并實現直接數字控制(DDC)功能的網絡節點。一般一套DCS中要設置現場I/O控制站,用以分擔整個系統的I/O和控制功能。這樣既可以避免由于一個站點失效造成整個系統的失效,提高系統可靠性,也可以使各站點分擔數據采集和控制功能,有利于提高整個系統的性能。DCS的操作員站是處理一切與運行操作有關的人機界面(HMI-Human Machine Interface或operator interface)功能的網絡節點。
工程師站是對DCS進行離線的配置、組態工作和在線的系統監督、控制、維護的網絡節點,其主要功能是提供對DCS進行組態,配置工作的工具軟件(即組態軟件),并在DCS在線運行時實時地監視DCS網絡上各個節點的運行情況,使系統工程師可以通過工程師站及時調整系統配置及一些系統參數的設定,使DCS隨時處在最佳的工作狀態之下。與集中式控制系統不同,所有的DCS都要求有系統組態功能,可以說,沒有系統組態功能的系統就不能稱其為DCS。
DCS自1975年問世以來,已經經歷了二十多年的發展歷程。在這二十多年中,DCS雖然在系統的體系結構上沒有發生重大改變,但是經過不斷的發展和完善,其功能和性能都得到了巨大的提高??偟膩碚f,DCS正在向著更加開放,更加標準化,更加產品化的方向發展。
作為生產過程自動化領域的計算機控制系統,傳統的DCS僅僅是一個狹義的概念。如果以為DCS只是生產過程的自動化系統,那就會引出錯誤的結論,因為現在的計算機控制系統的含義已被大大擴展了,它不僅包括過去DCS中所包含的各種內容,還向下深入到了現場的每臺測量設備、執行機構,向上發展到了生產管理,企業經營的方方面面。傳統意義上的DCS現在僅僅是指生產過程控制這一部分的自動化,而工控自動化系統的概念,則應定位到企業全面解決方案,即total solution 的層次。只有從這個角度上提出問題并解決問題,才能使計算機自動化真正起到其應有的作用。
當然不可忽視的還有電氣儀表的發展,不論過程系統如何發展,功能如何強大,過程儀表的作用不能被忽視,儀表是在工業生產過程中,對工藝參數進行檢測、顯示、記錄或者控制的基礎。隨著工業的發展,對儀表控制系統提出了更高的要求,電動儀表逐步向數字化、智能化方向發展,計算機系統向網絡化、開放化發展,新一代的儀表主要特點是智能化和數字化。
工廠的生產好壞很大程度上依賴于過程儀表的狀況,這些儀表除了流量、液位、壓力及溫度等參數的傳感器和變送器,還包括分析儀及控制閥。用于過程技術的堡盟傳感器和測量設備極其精密和穩定,完全能夠滿足應用要求。尤其是在極端環境條件下,它們也能進行準確的測量。良好的產品質量不僅延長了使用壽命,而且降低了維護周期,提高了過程生產的安全性和效率。
現在,自動化控制系統正在向第四代控制系統發展,第四代控制系統有兩個趨勢,一是系統的開放性,一是流程工業控制和離散控制的融合,體現在DCS和PLC功能的融合。目前,PC-BASED控制系統、嵌入式控制系統、現場總線控制系統都希望能成為第四代控制系統的主流系統,但是,由于這些系統都有各自的缺點,因此,大家普遍認為第四代控制系統還是會由以目前第三代控制系統的特點,加上開放和融合性的特點組成的柔性控制系統。第四代控制系統的發展依然是在摸索中,自動化專業的靴子必將擔當起這個責任。
-
plc
+關注
關注
5010文章
13274瀏覽量
463073 -
可編程控制器
+關注
關注
6文章
536瀏覽量
38846 -
DCS
+關注
關注
20文章
609瀏覽量
50049
發布評論請先 登錄
相關推薦
[原創]2010中國現代工業質量控制技術高峰論壇(7月,上海,免費)
現代工業電機驅動如何實現短路保護
現代工業制造中的精密測量技術簡單介紹
中國制造2025”與英國“現代工業戰略”的區別
英國“現代工業戰略”與《中國制造2025》異同分析
工控機在現代工業中的關鍵作用
高頻點焊電源技術在現代工業制造中的應用探索與實踐
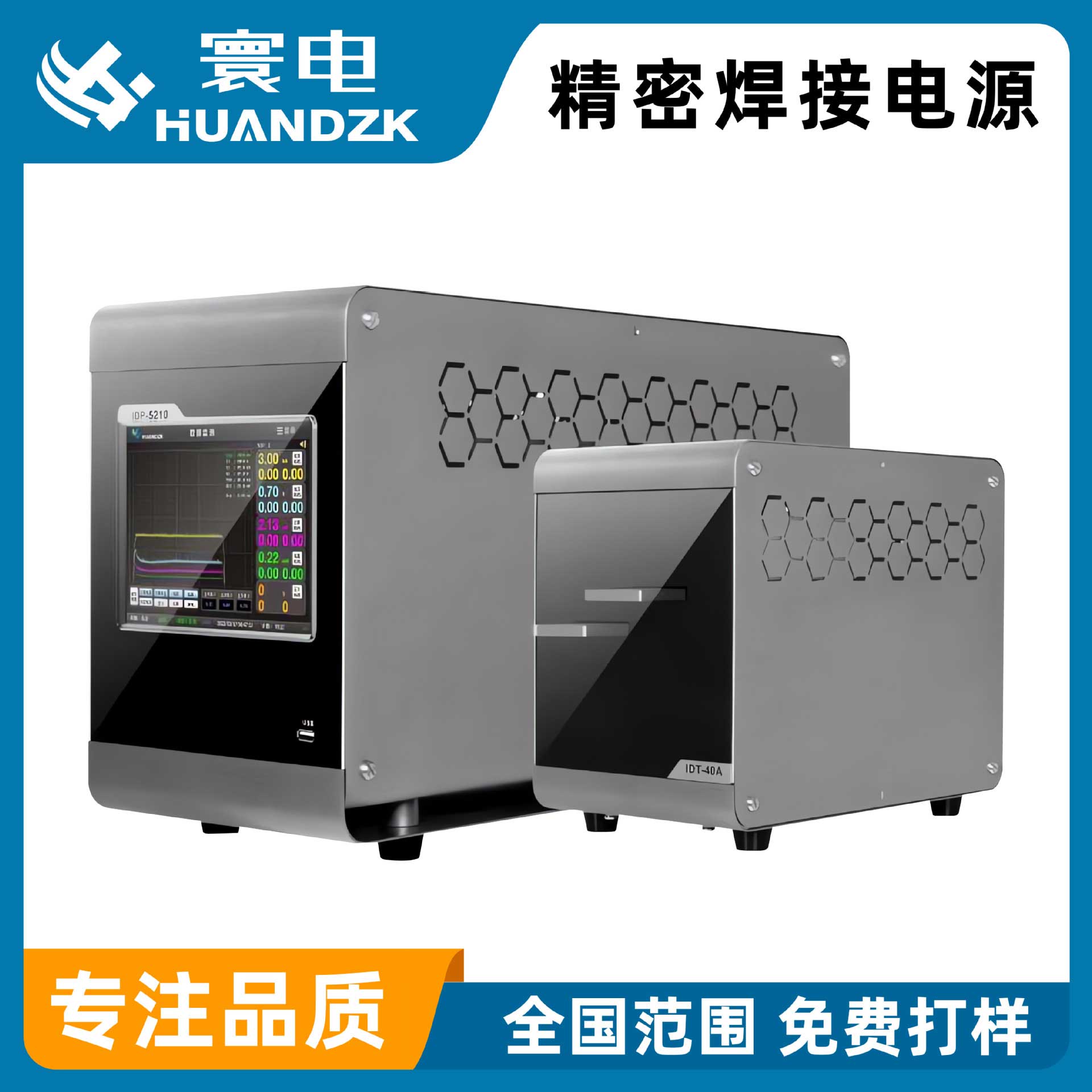
脈沖型電阻焊電源技術及其在現代工業焊接中的應用探索
高能點焊電源技術在現代工業制造中的應用與研究進展
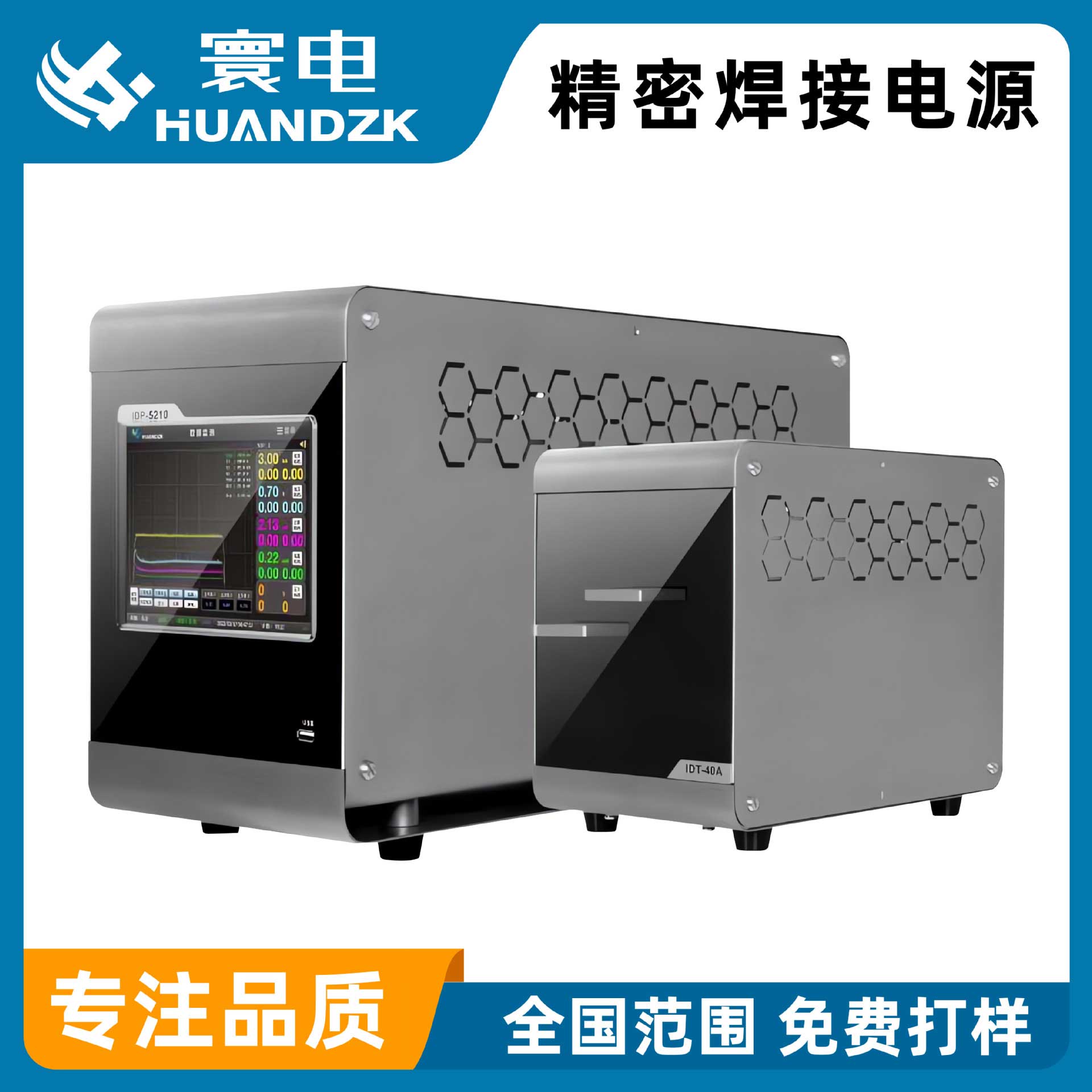
評論