鍍鋅生產過程中的帶鋼振動直接影響鋅層厚度及均勻性,既降低產品質量,又導致鋅液過度消耗,增加生產成本。無論是通過尋找振源從根本上消除振動,還是通過電磁鐵等進行主動減振,都離不開振動的檢測。為了保護帶鋼表面,不能采用任何接觸式振動檢測手段。目前比較常用的檢測方案包括渦流探頭和光學探頭兩類,前者為了達到所需要的量程,必須采用大直徑的探頭,系統造價頗高;后者在多截面測量時又存在多探頭數據的同步問題。
探索切實可行的光學檢測方案具有重要的現實意義和應用價值。本文介紹的方案以激光三角法測距原理為基礎,通過RS485總線廣播同步觸發信號,實現了多截面振動的同步測量。
1 多截面振動檢測系統總體方案
1.1 帶鋼整體振動檢測方案
圖1所示為鍍鋅生產線簡圖,要檢測帶鋼的整體振動情況,必須檢測多個截面的振動情況,具體取決于帶鋼振動的模式,以及允許布置探頭的位置。圖2所示為通過3個截面對帶鋼振動進行檢測的系統方案,圖中3段帶鋼表示的是同一條帶鋼上的3個部分。每個截面上通過激光器均勻的投射出5個等間的光斑,每個攝像頭的視野必須覆蓋它所對應的5個光斑,通過攝像機鏡頭后,這5個光斑在感光器件上成像,如果鋼帶振動,像的位置就會相應變化,每個光斑像的位移與帶鋼振動的對應關系可以通過三角法簡單確定。圖3所示為垂直于帶鋼且通過5個光斑的某個水平截面的光路圖。
圖1 鍍鋅生產線簡介
圖2 多截面帶鋼振動檢測示意圖
圖3 通過成像實現振動檢測的原理
這里以中心光斑為例,假設其與鏡頭的距離為a,鏡頭與感光器件的距離為b,感光器件的法線與帶鋼成45°夾角,當帶鋼在中心光斑處產生位移e時,其在平行于感光元件的方向的投影為e.cos45°,在感光元件上產生的位移為:
e'=(ecos α)b/a
當α=45°時,
e'=0.707eb/a (1)
由式(1)可見,采用較大的α值,對于相同的e可以得到更大的e'值,但是各個光斑成像差異變大,且攝像機不容易聚焦,通常取α=45°。
對上式簡單變換即可得到
e=(1.414a/b)e' (2)
通過式(2)即可根據光斑像的位置變化計算對應光斑處的帶鋼振動。
對千其他4個光斑,可以做相同的分析,但各個光斑的a值和α不同,當a較大時,各個光斑對應的α近似相同,5個光斑處的帶鋼振動均可近似采用上述同一個公式計算。
同樣道理,可以得到每個測量截面處的帶鋼振動情況,但如果各個界面分別獨立測量,則無法據此分析帶鋼的整體振動,因此必須采用各截面同步采集方案。
1.2 視頻采集模塊設計
為了有效檢測帶鋼振動,視頻采集模塊必須滿足時間分辨率和空間分辨率要求。所謂時間分辨率要求即攝像頭的幀速率與帶鋼振動頻率相比必須滿足采樣定理,通常帶鋼振動頻率僅3~5 Hz,因此采用幀速率為10幀/秒以上的攝像頭均可滿足要求;所謂空間分辨率要求即感光器件上相鄰像素間距所對應的帶鋼振動位移是否滿足檢測需求,這與a、b、α均相關。實際系統中,往往采用可調焦距攝像頭,通過選擇合適的焦距,讓感光元件在寬度上覆蓋整個帶鋼寬度,當然可以捕獲5個光斑的影像。假設帶鋼寬度為1 100mm,5個光斑等間隔分布在寬度為1000 mm的范圍內,感光元件每行有效像素為720,考慮到兩端留有一定余量,假設5個光斑對應的有效像素數量為700,即感光元件上的相鄰光斑像間隔為140像素,那么相鄰兩個像素對應的帶鋼振動位移可以通過計算得到,其值約為1mm,即該系統的空間分辨率為1mm.可見分辨率不高,但由于帶鋼振動幅度較大,通常可達10mm以上,因此對于分析振動規律,還是能夠滿足要求的。
實驗所采用的攝像頭感光元件為130萬像素的OV9650數字圖像傳感器,其最高分辨率可達1280x1024,其中有十位的數據接口用于數據傳輸,還有標準的SCCB接口用于實現對攝像頭中寄存器的初始化。
視頻采集模塊的總體結構如圖4所示。ARM平臺通過RS485接口接收同步廣播信號,啟動并獲取OV9650攝像頭的數字輸出,最后通過TCP/ IP協議上傳到主控計算機。
圖4 視頻采集模塊總體結構
2 多通道視頻采集同步方案
多個視頻采集模塊的同步采集依賴RS485同步廣播實現,同步廣播的發出者是一個獨立的單片機定時模塊,稱為同步器,其同步報文的播發間隔可以根據需要設定,但不能超過攝像頭的最高幀速率。
2.1 同步器的結構原理
同步器的結構如圖5所示。該模塊由單片機、設定按鈕、狀態及播發間隔顯示以及RS485發送接口等組成。其中設定按鈕用于根據需要改變播發間隔,顯示部分用于顯示工作狀態并配合實現參數設定。這里采用PS485接口的目的之一是便于實現廣播式通信,二是各個采樣模塊距離達數十米,且工業現場往往存在電磁干擾,如果采用RS232難以保證可靠通信。其次,沒有采用直接中斷式同步的原因是希望通過RS485播發采樣序列號,以實現更大時間跨度的同步。事實上,本系統中的網絡拓步結構是以同步器為主節點、其他所有采集模塊為從節點的主從式總線結構。
圖5 同步器的結構原理簡圖
同步器啟動后,AT89C2051單片機通過內部定時器確定時間間隔,然后定時向RS485總線播發采集同步信號,每個采集器必然同時收到同步信號,并通過完全相同的程序啟動采集,同步信號內部含有采樣序號,ARM平臺獲取采樣數據并上傳時,數據包中將包含這個采樣序號,這樣可以避免由于以太網傳輸延遲而導致的各個采集模塊數據錯誤匹配問題。
2.2 視頻同步采集系統總體結構
整個同步采集系統的總體結構如圖6所示。運行過程中,同步器按照既定的間隔定時播發含有序列號的同步消息,通知采集模塊進行視頻采集,然后連同序列號打包后通過集線器發送到主控計算機,由主控計算機進行后續的位移判別、計算等工作,最終給出整體振動情況。
圖6 視頻同步采集系統總體結構
3 同步精度分析
1)以太網傳輸延遲問題本文介紹的系統采用RS485總線定時播發含有序列號的報文來實現多采集模塊的同步。序列號的生成規則采用簡單的0~255循環方式,如果攝像頭的采集速率為25幀/秒,那么再次播發相同序列號的時間間隔超過10 s.則只要以太網的傳輸延遲不超過10s,在主控計算機端處理采樣數據時就不會出現匹配錯誤。
2)采集啟動延遲問題各個采集模塊是同一個方案的多個拷貝,結構、程序完全相同,因此對RS485同步報文的響應處理延遲也應該是相同,唯一可能造成采樣啟動時間誤差的因素就是以太網傳輸過程的管理,實驗證明這種時間誤差在10ms量級,這相對于200~300 ms的帶鋼振動周期來講是可以忽略的。
4 結束語
分析研究了通過視頻采集實現帶鋼振動檢測的原理與方法,探討了空間、時間分辨率確定原則;采用自制同步器,通過BS485總線定時播發同步報文,實現了多個視頻采集模塊的同步采樣;在同步報文中添加序列號,避免了因以太網傳輸延遲的不確定性而可能造成的各個采集模塊之間的數據包匹配錯誤問題;為鍍鋅生產線的帶鋼振動整體檢測提供了一種可行的方案。
-
激光
+關注
關注
19文章
3249瀏覽量
64736 -
視頻
+關注
關注
6文章
1956瀏覽量
73071 -
廣播
+關注
關注
1文章
307瀏覽量
23100
發布評論請先 登錄
相關推薦
5V的RS232/RS485多協議收發器
5V RS232 / RS485多協議收發器參考設計
采用LTC1387的5V RS232 / RS485多協議收發器的參考設計說明
工控機一個RS485接口如何采集多個傳感器信號?
如何對RS485進行調試呢
什么是RS485轉LoRaWAN的數據采集器?
分布式控制系統的主從式RS485多機通信
RS485接口電路原理圖
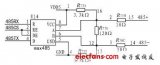
運用AD9371實現多通道寬帶同步采集系統
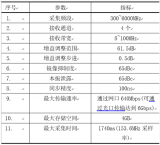
評論