一、概念
PAC(可編程自動化控制器)的概念是由ARC咨詢集團的高級研究員Craig Resnick提出的,在談到創造這個新名詞的意義時,他認為,“PLC在市場相當活躍,而且發展良好,具很強的生命力。然而,PLC也正在許多方面不斷改變,不斷增加其魅力。自動化供應商正不斷致力于PLC的開發,以迎合市場與用戶需求。功能的增強促使新一代系統浮出水面。PAC基于開放的工業標準、具多領域功能、通用的開放平臺以及高性能。ARC創造了這個詞,以幫助用戶定義應用需要,幫助制造商在談到其產品時能更清晰?!?/p>
PAC的概念定義為:控制引擎的集中,涵蓋PLC用戶的多種需要,以及制造業廠商對信息的需求。PAC包括PLC的主要功能和擴大的控制能力,以及PC-based控制中基于對象的、開放數據格式和網絡連接等功能。
它是將最佳的PLC,DCS和PC技術融合在一個統一的、多功能的單元上,并用于滿足現代工業應用中愈來愈多的復雜要求。
實施一個現代化的工業應用會引出一系列問題,有時甚至是艱巨的復雜要求。比如,眾所周知,典型的控制系統必須接收傳感器和激勵發出的信號,但對于許多現代應用,這僅僅是一個開始。先進的控制功能、網絡連通性、設備的互操作性及企業數據整合都是工業應用中所越來越強調的。
這些現代化的要求大大超出了傳統基于離散邏輯的可編程邏輯控制器(PLC)對I/O信號的控制。大多數PLC使用梯形邏輯編程,它起源于用來描述控制系統內布局和連接的離散物理繼電器及定時器的接線圖。
對于這一模式的偏離或需要擴展的應用,梯形邏輯編程有些力不從心。例如,數學上的復雜應用,如PID回路控制應用于溫度控制包括浮點算法等。為了執行這些計算, PLC往往須增加獨立和單獨編程的硬件卡。
使用PLC來滿足應用中的網絡連通、設備互操作、企業數據整合等要求時可能會遇到問題。這些類型的任務往往更適合PC來處理。
為了在PLC的應用中提供這些功能,需要在獨立PC中運行更多的處理器、網關或轉換器、“中間件”軟件,且企業系統中的特殊軟件必須經常與系統進行整合。
另一方面,一臺用于工業環境下的PC能提供大量的現代應用功能,尤其是那些需要聯網和數據通訊功能的。如同將PLC擴容至完成PC的任務,但是,工業用PC需要執行類似PLC的任務如機器或過程控制,同樣需要擴展。
例如,一臺PC所使用的操作系統大多并不是高性能、確定性工業應用的最佳選擇。附加I/O擴展卡或特殊擴展可能需要融入PC的操作系統中以提供高性能、確定性或類確定性操作。
二、基本要求
1多域功能(邏輯、運動、驅動和過程)——這個概念支持多種I/O類型。邏輯、運動和其他功能的集成是不斷增長的復雜控制方法的要求。
2單一的多學科開發平臺——單一的開發環境必須能支持各種I/O和控制方案。
3用于設計貫穿多個機器或處理單元的應用程序的軟件工具——這個軟件工具必須能適應分布式操作。
4一組de facto網絡和語言標準——這個技術必須利用高投入技術。
5開放式、模塊化體系結構——設計和技術標準與規范必須是在實現中開放的、模塊化的和可結合的。
進入PAC
隨著現代工業應用需求范圍擴大,自動化生產商已經做出積極回應,一項融合PLC類似確定性機器的工業控制設備或擁有靈活配置的過程控制,使企業能基于PC系統進行優勢整合的設備誕生。這個設備即被定義為可編程自動化控制器,或者叫PAC。
來自ARC咨詢公司的工業分析家Craig Resnick在2002年首創了“PAC”的定義。ARC創造這一新名詞基于2個原因:幫助自動化硬件用戶更好地確定他們的應用需求;給予自動化硬件商一個更明確的概念用于幫助他們闡述產品功能。
合并PLC和PC技術用于工業控制的想法之前已出現過,但是只有通過如前述的“添加”的方法來實現,其中附加的中間件、處理器與一個或多個PLC協同工作。一個PAC,擁有先進的功能,需要納入設計中。
例如,執行功能包括計數、閉鎖、PID回路控制、數據采集及傳輸,一個典型的PLC控制系統需要更多的、價格較昂貴的過程硬件。一個PAC則內置了以上所有功能。
PAC的矚目之處在于模塊化的設計和架構,同樣使用開放式的架構提供擴展性和設備及商用系統的互聯性。特別的是,PAC冠以高效處理及I/O掃描的特點,并以多種方式使其能夠融入企業的商用系統。根據ARC,可編程自動化控制器必須符合下列要求:
1.在多領域中的單一平臺上操作包括邏輯、運動、驅動和過程控制
2.采用一個單一的開發平臺,使用通用的標簽和一個單一的數據庫用于不同門類的任務開發
3.無縫集成控制器硬件和軟件
4.使用軟件工具進行編程能設計控制程序以支持跨越多個機器或設備的“流程”
5.在開放、模塊化的架構中進行操作反映了工業應用中從設備布局到過程中的單元操作
6.采用事實上的標準網絡接口,語言和協議,使數據交換成為網絡化的多供應商系統的一部分
7.提供高效的處理和I/O掃描
PAC的優點
PAC控制解決方案,如PACSystems可實現工廠和OEM廠商都需要的優點:
(1)提高生產率和操作效率:一個通用輕便控制引擎和綜合工程開發平臺允許快速地開發、實施和遷移;且由于它的開放性和靈活性,確保了控制、操作、企業級業務系統的無縫集成,優化了工廠流程。
(2)降低操作成本:使用通用、標準架構和網絡,降低了操作成本,讓工程師們能為一個體現成本效益、使用現貨供應的平臺選擇不同系統部件,而不是專有產品和技術;只要求用戶在一個統一平臺和開發環境上培訓,而不是幾種;且為用戶提供了一個無縫遷移路徑,保護在I/O和應用開發方面的投資。
(3)使用戶對其控制系統擁有更多控制力:使用戶擁有更多靈活性來選擇適合每種特殊應用的硬件和編程語言,以他們自己的時間表來規劃升級,并且可在任何地方設計、制造產品。
的弱勢:
雖然PLC業界已經注意到了這一趨勢,并通過將PC技術應用于PLC產品,直接提供OPC Server、WEB Server及IEEE標準通訊接口等,以提供更高的應用靈活性。但是受限于傳統PLC專屬式的設計,其互操作性和靈活性限制(即使是對于同一品牌的PLC來說,也是這樣),并不能完全滿足用戶的要求:
1傳統的PLC均不能提供主動的事件通知,系統的集中監視管理有賴于服務器主機的主動定時查詢;
2因為在實時信息上的欠缺,要實現跨PLC的事件處理比較困難,且速度延遲,效果不佳;
3無法提供本地直接處理的預約控制,預約控制完全有賴于服務器主機的集中處理,所以系統當機時,立刻停擺;
4系統的建構由于采用了不同供應商的多種平臺,為整合各種不同的專用總線,系統之銜接有賴于第三方提供的OPC Server或Gateway,故其實施并不是一件輕松和容易的事情;
5系統升級將必須付出重新設計的成本和時間,其不可預見成本太高。
6梯形圖程序的設計是基于個案進行,每一專案均無法完全復制應用,無法實現標準化,從而工程設計費用無法降低;
7現行自動化系統的數據容量太小,在適應新的應用需求時顯得力不從心;
8無法實現實時同步遠程的數據傳輸,與PDA、手機的連接比較困難;
9需要通過PC或第三方設備來實現基于WEB的遠程數據發布。
RTU和PAC
遠程終端設備(RTU)類似控制器設備,安裝在遠程位置以收集傳感器和其他數據。流行了幾十年后,RTU通常被用來作為監控和數據采集( SCADA系統)網絡,RTU向SCADA發送數據。RTU從SCADA主控接收信息而操控遠程位置上的現場設備上。
RTU主要在遙遠的地理區域部署,以監測,采集和控制遠程分散設備,如管道、井、起重機、或電信設施等。傳統的PLC在這些類型的應用中不具備天然的通訊功能。另外, PLC一般不提供承受惡劣的野外環境條件,也沒有多數RTU應用中所需的靈活I/O配置。
總的說來,RTU更強調其通訊功能的開發,適用于嚴酷環境,擁有靈活的I/O配置。
然而,傳統的RTU通信能力通常是過時的,因為它們是在私營無線電或租用專線通訊網時期發展起來的。如今開放的,基于IP的有線和無線本地和廣域的網絡則更加靈活,而且價格更便宜。由于這一原因,改造現有的RTU或執行新的應用程序時,使用過時的RTU技術在商業或技術上是沒有太大意義的。
相反地,PAC能提供卓越的通信能力,通用I / O選項,寬溫和振動規格,并使用當今領先的通信標準。這些特點使得PAC適合替代傳統戶外RTU,尤其是舊網絡,專有網絡等由于維修費用增加或過時廢棄的網絡。
數據采集
數據采集系統(DAQ)基于PC設備,提供快速的信號采集、基本信號調試、數據保存功能和有限的聯網能力。多數DAQ系統是基于PC,在物理環境或遠程位置上的使用有一定限制。大多數DAQ系統更喜歡呆在實驗室里而非戶外的環境。
PAC提供通用且靈活的信號偵測、調試及多線路。其擁有強大的處理器和大量的內存,獲得的原始數據可以在傳送至數據庫用于其他應用之前進行累加、校對或其他處理(例如,將原始數據轉換成工程單位)。
另外,數據可以保存在本地。由于PAC不是PC ,故不像PC需要較高的成本,它可以在現場應用中隨意部署。所以PAC是個不錯的選擇。
各種工業自動化供應商現在提供PAC或類似PAC產品。在某些情況下,這些產品更像PLC,而在其他情況下則更象是工業用PC 。如前所述,PAC與這些設備集成,從而使側重PLC或PC功能的設備可能會并不適用于你的應用需求。
在評估PAC或類似PAC自動化控制器時,只需考慮這一經驗方法:為了滿足您的要求,你是否需要添加附加的處理器,網絡接口或中間件使得控制器擁有PLC或PC類似的特點?
如果是,查看一下控制器是否更符合如前所述的PAC特點?
對于任何產品,一些廠商可能從業已久。許多供應商最近引入了新PAC或PAC類似產品,有幾個候選公司,包括OPTO 22,在PAC進入主流的前幾年就已經用出色的銷售業績證明了其強大功能。
在1990年,在PAC概念誕生前的11年,Opto 22引進了PAC雛形—以電腦為形式的硬件設備—mistic控制器。現在Opto 22 SNAP PAC系統以mistic為基礎,其他PAC設備應用包括半導體處理、原料加工、水和水處理、管道監測等。
總之,PAC提供了一個擁有先進控制功能的緊湊型控制器,網絡連接,設備互操作,以及企業數據集成功能,都能在PLC或基于PC的控制器中找到。有了這些功能,PAC在現代工業應用中已經成為滿足各種工業需求不可獲缺的部分。
PAC蓄勢待發
仔細看看如何使PAC適用于現代工業應用
如下圖所示的單一的PAC正在多域內進行操作以監測管理生產線,包括化學工藝、測試臺、物流等。為了完成以上任務,PAC必須同時管理模擬值如溫度、壓力;數字量閥門的開/關狀態,開關及儀表;庫存跟蹤和測試設備中的串行數據等。
PAC與OLE交換數據用于過程控制服務器(OPC)、操作界面及SQL(結構式查詢語言)數據庫等。且PAC能同時處理這些任務,無需附加任何處理器、網關或中間件等。
PAC、操作員、工作臺、測試設備、生產線、過程傳感器、激勵及條形碼識別等一起連接在遍布設備區的標準10/100 Mbps以太網上。在一些實例中,一些無內置以太網連接功能的設備如溫度傳感器等是通過一個中繼以太網激活I/O單元從而連接在I/O模塊上,再依次與PAC通訊。
使用以太網,使PAC與遠程I/O模塊通訊,對模擬、數字和串口信號進行讀、寫操作。以太網同時把PAC和OPC服務器連接起來,故PAC也可以和類似升降機、臨時工作臺等移動設備通訊。
PAC能控制、監測,并與各種設備和系統交換數據,源于PAC與它們使用相同標準的網絡技術和協議,包括有線和無線以太網、IP網絡傳輸、OPC及SQL等。
在另一種控制情況中,需要應用到基于的應用層的協議如Modbus、SNMP(簡單的網絡管理協議)及通過調制解調器的PPP(點對點協議)。而PAC能夠滿足這些不同的通訊要求。
在一些工廠實例中,PAC與企業SQL數據庫交換制造、生產及清單數據。這樣依次與幾個關鍵商務系統交換數據,包括企業資源計劃(ERP)系統、總體設備效率(OEE)系統及供應鏈管理(SCM)系統等。因為從工廠車間來的數據不斷由PAC更新,所以整個商務系統的信息是實時、有價值的。
-
傳感器
+關注
關注
2550文章
51038瀏覽量
753086 -
控制器
+關注
關注
112文章
16333瀏覽量
177813 -
自動化
+關注
關注
29文章
5563瀏覽量
79240
發布評論請先 登錄
相關推薦
可編程序控制器(plc)有哪些應用
可編程控制器(PLC)
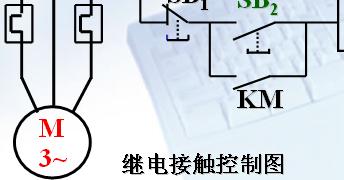
新興的可編程自動控制器PAC特征與應用
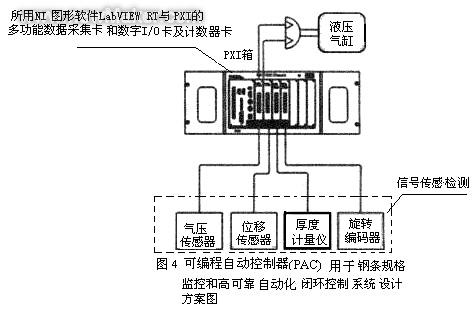
新興的可編程自動控制器PAC
PAC--先進的可編程自動化控制器
可編程自動控制器的發展研究
基于PAC的電機控制器快速控制原型研究
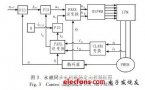
德州儀器可編程邏輯和自動化控制器(PLC/PAC)解決方案
可編程控制器(PLC)和自動化技術怎么學習
使用NI可編程自動化控制器在LabVIEW應用中與工業網絡設備的通信設計
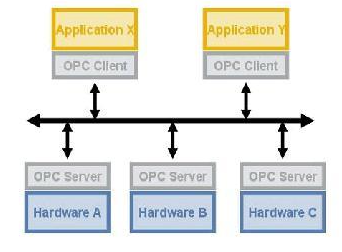
評論