1.引言
如今,隨著信息化應用的發展,將無線通信技術、智能采集技術和自動控制技術綜合應用于現代企業信息化管理,已成為一種趨勢。
企業也迫切需要將各種有利于提高生產效率的信息因素收集匯總,用于分析與管理,而設備的消耗電能與運行時間正是十分重要的一種生產信息。本文所設計的電表采集器是生產采集系統的核心部件,通過電表上的通訊接口,實時地讀取表中的數據,并通過無線網絡將數據傳送到服務器中。這使得企業能夠及時準確地了解生產運行情況,在避免手工抄表中不及時和易出錯情況的同時,也為合理利用資源及有效維護設備提供了豐富的數據支持。
2.采集系統的結構
近年來,電表的數字化程度越來越高,大多提供標準的通信總線結構,便于設計人員編程實現對電表數據的讀取。在生產采集系統中,分散于廠區各個配電間的電表采集器與多個電表通過通訊接口相連,構成點對多點的主從網絡,定時采集各表的電度值與電流值;在將整理后數據通過WIFI網絡上傳至WEB服務器的數據庫中存儲;終端客戶可通過網絡訪問和查詢服務器中的各個設備運行情況。
3.采集器的硬件設計
電表采集器以嵌入式Cortex-M3微控制器為核心,使用MAX485芯片與PZ162L型電表進行RS485總線形式通信,獲取電表內部寄存器的數據;使用SD2405芯片獲取系統時鐘,以判斷發送的時間;使用WIFI232模塊連接WIFI網絡,將組幀數據傳送至服務器。電表采集器的硬件設計如圖1所示。
3.1 主要部件的選擇
電表采集器使用TI公司生產的32位Cortex-M3內核微控制器LM3S8962,存儲方式為哈佛結構,其獨立的指令總線和數據總線使得該芯片可以同時進行讀寫指令和數據的操作。
該芯片工作頻率可達50MHz,有256K的FlashRAM,3個UART串口和一個I2C總線接口。通用I/O口功能設計為:MAX485接UART0,即Rx端接PA0口,Tx端接PA1口,控制口接PF0口;WIFI模塊接UART1,即Rx端接PD2口,Tx端接PD3口,其電源控制口接PF1口;SD2405接I2C總線接口,即SDA端接PB2口,SCL端接PB3口;異常指示燈連PF2口;電度測試按鍵連PE0口,電流測試按鍵接PE1口。
WIFI模塊采用第三方提供的串口與WIFI數據包的雙向透明轉發模塊,型號為U S R -WIFI232-X,采集器將數據組幀以串行方式送至WIFI模塊,WIFI模塊則以網絡終端形式再將數據轉送至服務器。
系統時鐘芯片SD2405是一種內置晶振、充電電池、具有標準IIC接口的實時時鐘芯片,可通過5位地址尋址來讀寫片內32字節寄存器的數據(包括時間寄存器、報警寄存器、控制寄存器、通用SRAM寄存器)。
3.2 采集器與電表通信的實現
廠區使用的P Z 1 6 2 L型數字電表集成了RS485通信協議,因此設計增加了MAX485芯片來完成LM3S8962的RS485通信。微控制器采用UART0串口與MAX485傳輸數據,通信模式為8位數據位,1位停止位,無校驗位,波特率為9600.而采集端的電表波特率也為9600,而表的A、B端與MAX485的A、B端相連,并共用地線。設計中使用通用接口PF0作為MAX485的控制口,置高電平時向總線發數據,置低電平時從總線接收數據。另外,由于每個采集器要采集多個電表,在對電表配置時,需保證使每個表的編號唯一,以免因目標沖突引起采集錯誤。
3.3 WIFI模塊的供電控制
在電表采集器中,WIFI模塊耗電量和發熱量都較大,且實際每天僅需一次連接無線網絡,故在硬件設計中加入了WIFI模塊的供電控制電路。該電路使用ST111電壓控制轉換芯片,可將電路電壓穩定在WIFI模塊所需的3.3V上,而芯片的控制端則與通用接口PF1相連。
每天在需要傳送數據前,微控制器將PF1口置1,啟動ST111芯片使WIFI模塊上電,而在傳送數據結束后,將PF1口置清0,使WIFI模塊斷電。這種工作方式可以減少采集器的能耗與發熱,延長無線模塊的使用壽命。其供電控制電路如圖2所示。
4.采集器的軟件設計
電表采集器的整體設計方案是先檢測電表的編號與個數,并在指定時間點發送控制字獲取每個表的相應信息,再將得到的數據組成數據幀發送給服務器,其軟件設計流程圖如圖3所示。
設計流程中,初始化部分是對LM3S8962的GPIO引腳進行初始化,如UART初始化,設定指定引腳的功能、通訊模式、波特率,還有I2C的初始化。此外還包括時鐘的初始化,以及維護時的屏幕和按鍵的初始化。
鑒于工廠中各電表不一定能按順序排列,需要采集器檢測總線上實際的電表數量和編號,才能準確的發送查詢命令,因此加入了電表信息檢測部分。該設計部分使采集器的通用性增強,具備了一定的自動化功能。由于檢測電表信息僅執行一次,如要新增電表,需重啟采集器,就能檢測到新添加的電表的數據了。
發送時間的判斷主要通過讀取SD2405的系統時間,與設定時間相比較,判定是否要為WIFI模塊供電。未到發送時間,則每分鐘檢測一次各個電表的電流,當電表電流大于設定閾值時認為設備正在運行,對應時間計數器自增1,該計數器即為設備實際運行的分鐘數;到達發送時間,則為WIFI模塊上電,從總線獲取各電表的電度值并組幀發送,將時間計數器值作為設備運行時間并組幀發送,再將計數器清0,并將WIFI模塊斷電。在實際設計中,發送信息設置為每天一次,因此采集的數據為某生產線的每日電度值和運行時間。
5.采集器的運行測試
根據廠方的實際要求,在廠區車間共安裝了3個無線電表采集器,采集各生產線對應的18個電表。所設計的采集器能夠自動檢測總線上的電表的編號及個數,且讀取電表的數據與電表顯示值一致,發送給服務器的數據幀也完整無誤,服務器后臺的數據庫能記錄到各個電表的電能和機器運行時間。圖4為服務器接收到數據后處理生成的設備生產運行界面。
6.結論
綜上所述,本文設計的無線電表采集器能夠準確檢測電表當前的電能和電流等信息,并經過數據處理后,上傳至服務器,可得到企業所需的生產電力成本和設備運行時間,以利于企業快捷有效的統計成本,準確把握機器運行狀況,并能對生產做出合理調整。此外,采集器充分利用了廠區覆蓋的WIFI網絡傳送數據,還具有布點靈活、節省成本的特點。
-
微控制器
+關注
關注
48文章
7565瀏覽量
151577 -
芯片
+關注
關注
456文章
50910瀏覽量
424504 -
采集器
+關注
關注
0文章
194瀏覽量
18221
發布評論請先 登錄
相關推薦
恩智浦LPC1800 ARM Cortex-M3微控制器怎么樣?
STM32 的核心Cortex-M3 處理器是什么
STM32的核心Cortex-M3處理器是什么
STM32的核心Cortex-M3處理器的標準化是什么意思
恩智浦ARM Cortex-M3 USB微控制器LPC134
愛特梅爾推出全新SAM3S16 Cortex-M3微控制器
基于ARM Cortex-M3的MODBUS協議實現及其應用
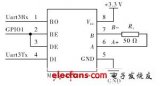
AN-1159: 基于Cortex-M3的精密模擬微控制器(ADuCxxx系列)上的I2C兼容接口
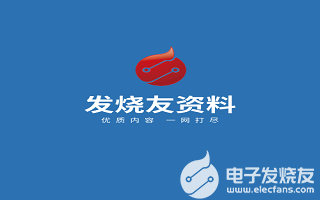
STM32 的核心Cortex-M3 處理器
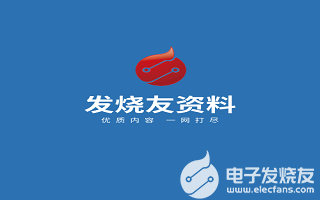
基于Arm Cortex-M3內核的32位微控制器APM32E103xCxE數據手冊
MM32L3xxo產品手冊:32位基于ARM Cortex-M3核心的微控制器
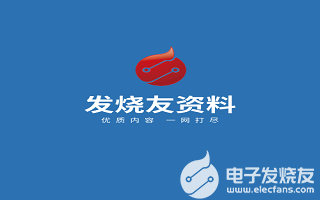
評論