我最近是真的看到了AVL所探討的捷豹的模組實(shí)物。這種全部靠粘膠組合的方式,也是存在一定的局限性的。因此以部分粘膠和部分加力的模式可能是未來軟包模組的發(fā)展方向。
1)全部靠膠的方式
確實(shí)在新的模組設(shè)計(jì)中,電芯模組支架、散熱片取消了,設(shè)計(jì)了新的散熱方式,這樣4個(gè)電芯成為一個(gè)小組,然后再通過中間的泡棉進(jìn)行分割成一個(gè)單元,內(nèi)部采取涂膠的方式進(jìn)行連接形成一個(gè)整體。
這種改進(jìn),主要的變化,如下圖所示對(duì)比:
每個(gè)模組降低了150g的重量
每個(gè)電芯減少了0.4mm的厚度空間
支架方面的成本減少了
在這個(gè)設(shè)計(jì)里面,粘接膠和發(fā)泡的結(jié)構(gòu)填充膠就占據(jù)了很重要的地位,需要把這個(gè)模組內(nèi)部的部分形成一體,防止電芯相對(duì)運(yùn)動(dòng)。這里采取的絕緣措施會(huì)有一定的差異。具體的模組工藝和并聯(lián)的部分,由于實(shí)際的區(qū)隔處理,可能在泡棉和絕緣材料的使用上有不同。而且下方電芯的極耳的處理和固定,需要發(fā)泡的材料膠進(jìn)行處理,類似采取局部滴膠的辦法。
2)分塊模式進(jìn)行組合
現(xiàn)代在它的兼容的BEV/PHEV里面提出了的結(jié)構(gòu)
這個(gè)電池系統(tǒng)的結(jié)構(gòu)分三層,以小模塊、大模組和系統(tǒng)所組成,小模塊的系統(tǒng)結(jié)構(gòu)為每個(gè)軟包電芯提供足夠的表面壓力,并保持電池小模塊之間的精密檢出,防止整個(gè)生命周期內(nèi)的變形應(yīng)力傳遞。這里包括4*4*3,一共48顆電芯構(gòu)成的半包。
小模塊內(nèi)裝有四個(gè)軟包電芯,包含
4顆軟包電芯
維持電池之間的內(nèi)部壓力泡棉
用于間接冷卻袋式電池的鋁冷卻板
所有組件按順序堆疊并組裝成一個(gè)子模塊,用長螺栓將四個(gè)電池組裝成一個(gè)完整的模塊。此時(shí),通過計(jì)算泡棉的壓縮量來設(shè)計(jì)電芯初始的表面壓力
當(dāng)不同厚度的電芯存在在Pack里面的時(shí)候,電池模組的側(cè)板和容納電芯的電池注塑盒體為均一化部件,主要調(diào)整不同厚度的泡棉。在實(shí)際的力學(xué)仿真過程中,模組的側(cè)板和整個(gè)半包的側(cè)板是比較重要的檢查點(diǎn)。這里涉及到,端板、鋁側(cè)板、支撐板等結(jié)構(gòu)件。
小結(jié):這兩種基本的結(jié)構(gòu)設(shè)計(jì)大概是短期內(nèi)量產(chǎn)的兩邊出極耳的主要設(shè)計(jì)形式,后者往前的持續(xù)性空間要更大一些
-
AVL
+關(guān)注
關(guān)注
0文章
14瀏覽量
10097 -
電芯
+關(guān)注
關(guān)注
14文章
751瀏覽量
26160 -
電池系統(tǒng)
+關(guān)注
關(guān)注
9文章
396瀏覽量
30153
原文標(biāo)題:兩種軟包模組設(shè)計(jì)
文章出處:【微信號(hào):QCDZSJ,微信公眾號(hào):汽車電子設(shè)計(jì)】歡迎添加關(guān)注!文章轉(zhuǎn)載請注明出處。
發(fā)布評(píng)論請先 登錄
相關(guān)推薦
日志篇:模組日志總體介紹

Linux應(yīng)用層控制外設(shè)的兩種不同的方式
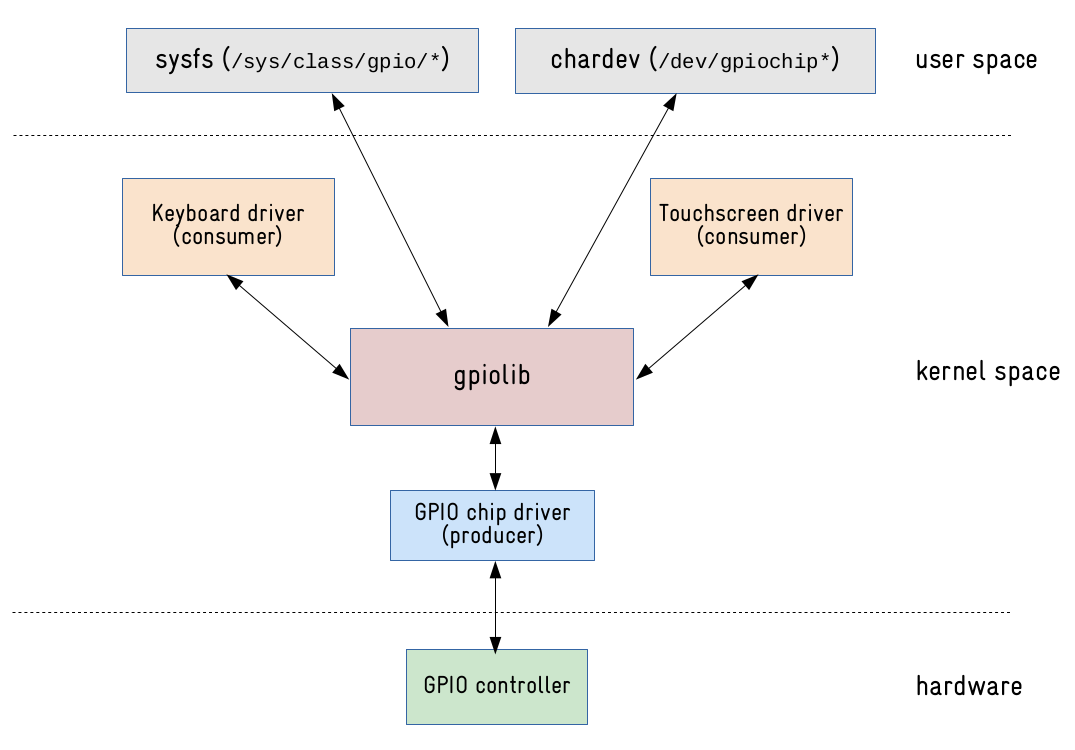
評(píng)論