「在 2000 年時,汽車的科技化水平和消費電子有 6 年左右的差距,但現在兩者在新技術應用上幾乎是同步的。」上周極客公園受邀前往德國英戈爾施塔特的奧迪總部參觀,奧迪工程師為我們分析了汽車科技化的現狀。
在自動駕駛、車聯網等技術的牽引下,汽車行業對于新科技的接納程度遠超從前,目前幾乎所有汽車廠商都將「科技化」列為重要的發展方向。
這樣的趨勢從每年年初的 CES 展會也能看出來——CES 原本只是針對消費電子產品的展會,但是最近幾屆明顯感覺到已經變成了汽車廠商「秀肌肉」的場所。
汽車與科技相交的十字路口,一直也是極客公園關注的領域。過去一段時間我們跟蹤報道了自動駕駛的技術演進,也介紹過各種不同的汽車科技。
這一次前往英戈爾施塔特,極客公園和奧迪的質保部門進行了深入交流,我們試圖了解在全面擁抱科技的背后,汽車工業本身正在發生怎樣的變革。
比消費電子更苛刻的部件要求
「如今的汽車里有 100 個互聯的控制單元,8000 個活躍的半導體,超過 80% 的汽車創新是由微電子技術實現的。」奧迪質保部門半導體專家 Stefan Simon 說道。
自動化駕駛、電氣化動力系統和車聯網都依賴于半導體技術的發展, 從這個角度來說,汽車和消費電子的「創新源泉」是相同的。但在具體的應用上,兩者是有著很大的區別。
舉例來說,在消費電子領域 OLED 顯示技術已經被廣泛使用,最新的 iPhone X 配備的便是 OLED 屏幕。在汽車領域,OLED 的應用主要集中在車燈等部件中。
OLED 車燈的優勢在于光的均勻度更高,而且對于空間要求更低——它不會投射任何明顯的陰影,也不需要反射器、導光器或類似的光學部件。因此在三維布局上,OLED 車燈可以給設計者帶來更多的「創作自由」。
新 A8 的 OLED 車燈模塊
實際應用中的挑戰在于,汽車對于 OLED 壽命的要求遠比消費電子產品更加嚴苛,甚至要在十五年以上的使用時間里避免老化問題出現,直接搬用現有產業鏈技術顯然是行不通的。
因為比較看中車燈的設計,奧迪常被大家戲稱為「燈廠」。奧迪在 OLED 技術上布局已久,幾個月前發布的新奧迪 A8 用上了貫穿式的 OLED 尾燈,看起來非常「亮眼」且散發著「科技感」。
在具體的落地上奧迪經歷了一場「重造」,奧迪的做法是先對現有技術進行評估,再根據自身的需求和供應商進行聯合開發,制定車規標準。在引進生產之前,奧迪半導體實驗室的工程師會進行多階段驗證,解決老化、褪色等現有產業鏈的薄弱問題。
自動駕駛中復雜的零部件也面臨著同樣的挑戰。奧迪新 A8 是首款擁有 L3 級別自動駕駛能力的量產汽車,在 60 公里/小時的緩行公路上奧迪 AI 可以完全接管方向盤。除了雷達、攝像頭和超聲波傳感器之外,奧迪還是第一家在量產車中引入激光掃描儀的汽車廠商。
新 A8 所使用的激光掃描儀
自 2014 年以來,奧迪半導體實驗室的工程師就已經開始在為新 A8 的激光掃描儀做準備,與供應商一起定義了具體規格和要求。作為激光掃描儀中的核心部件——激光二極管,奧迪為了滿足它車規部件精確度和耐久性的要求,切入到「源頭」對二極管的制造過程進行了優化,并在落地前進行了復雜的路試檢驗。
各種新技術的應用,給汽車的研發和質保部門帶來了不小的挑戰——不但需要對新技術立刻做出反應(技術評估),還要針對車載平臺苛刻的工作環境,更長的使用壽命進行優化(技術改進)。跨課題和跨部門的專業人員需要覆蓋整個產品周期,保證新技術盡早納入到整車的研發進程中。
電氣化引發的「新工作」
和消費電子領域發生的變革一樣,汽車的電氣化也在逐步提高。一方面,汽車的驅動方式向電動過渡,另一方面汽車所產生的數據計算量也在呈指數級的提高,隨之而來的是一些新的難題。
就拿噪音為例,普通燃油汽車的噪音更容易被內燃機的聲音所淹沒,但對于電動汽車來說,空調的噪音、電子控制部件的噪音甚至是屏幕風扇的噪音,在一個相對安靜的內反而會被「放大」。定位、分析這些噪音源給汽車的可靠性檢測工作帶來了挑戰。
奧迪的聲學專家需要與技術開發部門協同工作,利用現代儀器(高靈敏度麥克風、人造頭模擬人耳)將噪音可視化,再進一步衰減、消除或抑制這些噪音。「電動奧迪必須聽起來和配備內燃發動機的奧迪一樣高品質。」奧迪整車聲學品質專家 Andreas Wolf 說。
對此,奧迪還研發了一種「一勞永逸」的方法,一種名為 NVH 的測量工具,它通過視覺化的分析將主觀的噪聲轉換為客觀特征,通過記錄觸發條件來找到出現異常部分。NVH 工具可以幫助全球各地的奧迪員工記錄任何水平的震顫和噪聲,搜集到的數據可以用于分析、評估或與其他汽車數據作對比。未來,NVH 分析軟件幾秒鐘內就能記錄一個噪音并檢測其發生源。
電氣化帶來的另一個直接挑戰就是數據量的大幅提高。舉例來說,奧迪 A3 擁有超過 15 種輔助系統,每 8 小時會產生 3GB 數據;A7/A8 則擁有超過 40 種輔助系統,每 8 小時會產生 50GB 數據。暴增的數據量不但提高了生產制造環節的難度,也增加了路試檢驗的復雜性。
圖中的平板為 CarPad 系統
在路試檢驗期間,奧迪全球 17 個站點約有 600 輛試生產車輛在實際道路狀況下行駛了 50,000~100,000 公里的路試檢驗。有些汽車在 2~3 年內行駛了 200,000 公里。所有汽車都配備了特殊測量電纜和數據記錄器,以便隨后跟蹤專家提出的任何問題。
路試車輛的數據記錄器裝在后備箱內
過去在進行可靠性測試時,需要手工填寫部分清單,現在奧迪的質量專家使用 CarPad 應用程序(平板形態)就可以完成信息錄入,并匯總到奧迪質保數據庫中進行統一分析。在現場,奧迪工程師用 CarPad 向我們展示了新 A8 自動泊車的路試檢驗,駕駛員可以從平臺列表中選擇需要驗證的功能,路試后可以對泊車的各個關鍵關節進行記錄和打分。
「質保前置」壓縮迭代時間
「數字化趨勢、可持續性和城市化正在改變消費者對汽車質量的理解,并影響著我們質保部門的工作——質保工作正在從單純的組件分析轉向整體系統視角。在此過程中,我們將會越來越多地借助虛擬和數字方法。」奧迪質保部負責人 Werner Zimmermann 說道。
新造車企業或者說電動汽車正在努力擺脫著傳統汽車的「迭代束縛」,而奧迪也正在通過更多的數字化分析、檢測工具來加速壓縮汽車的「迭代周期」。
例如聚焦離子束(FIB)可以在復雜的材料組合情況下,通過極小的切割窗口獲得高分辨率的橫截面圖像,完成材料的精確分析;數字化的精測樣架能夠在不接觸材料的情況下完成車體測量——整個車身模型的構建時間從 48 小時減少到僅僅 4 小時。
「數字化精測樣架的使用,使得我們可以提前將專業的知識投入到產品構建過程中,甚至可以早至生產開始的兩年半之前。」奧迪精測樣架及測量部門負責人 Marcus Hoffmann 在介紹質保工作時說道。
完整的汽車研發周期可能需要 3~4 年,而很多新技術的迭代時間則要短的多,甚至以月為計量單位。如何提高兩個時間的匹配程度,從更加宏觀的角度去擺脫「迭代束縛」規劃一項新技術,是汽車廠商在科技化之路上一定要解決的問題。
一方面自身提高研發、質保效率,通過將質保環節「前置」來避免因流程后期更改帶來的額外成本;另外加強和產業鏈的配合度,深度參與到技術的定義中,提前識別并解決因跨領域所產生的薄弱點,這是在數字化時代奧迪帶來的「參考答案」。
-
奧迪
+關注
關注
4文章
528瀏覽量
33734 -
自動駕駛
+關注
關注
784文章
13786瀏覽量
166404
發布評論請先 登錄
相關推薦
蔚來在澳勝訴奧迪商標案
上汽奧迪A5L Sportback明年初推出
奧迪股份如何通過升級至SAP S/4HANA實現財務與后勤的高效整合?
奧迪威榮獲“持續15年高新技術企業”卓越成就獎
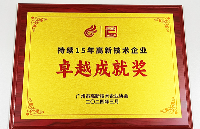
啟明信息奧迪一汽CC項目熱線啟動
奧迪借助Microsoft Intune簡化終端管理平臺
消息稱下一代奧迪A5將首搭華為智駕方案
今日看點丨消息稱下一代奧迪 A5將首次搭載華為智駕方案;思科全球裁員6300人
禾賽科技獲得奧迪新車型激光雷達量產項目定點
奧迪攜手微軟Azure OpenAI,計劃為200萬輛汽車引入ChatGPT
上汽與奧迪正式簽署合作協議,聯合開發智能數字平臺
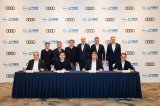
大眾全新奧迪E31.2電子架構介紹
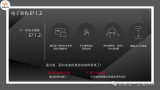
評論