摘要:根據工信部、發改委、科技部聯合印發《汽車產業中長期發展規劃》的要求,到2025年,新能源汽車占汽車產銷量20%以上,動力電池系統比能量達到350瓦時/公斤。
在當前電池材料技術體系下,軟包憑借外包裝材料的輕量化,是最有希望達到國家動力電池能力密度要求的產品體系之一,軟包動力電池是提高能量密度的優選道路。
軟包動力電池又稱為“聚合物電池”,聚合物鋰離子電池外包裝采用鋁塑包裝膜。本文將對軟包裝膜的技術難點、國內外技術現狀進行整理與分析,為我國軟包裝膜產業的發展提供參考。
鋁塑復合膜(簡稱“鋁塑膜”)軟包裝鋰電池封裝的關鍵材料之一,起到保護內部電芯材料的作用,由外層尼龍層、粘合劑、中間層鋁箔、粘合劑、內層熱封層等五層組成,每層功能要求都比較高,是目前工人的鋰電池材料領域技術難度較高的環節,也是我國動力電池領域實現國產化的關鍵材料。
軟包裝膜生產存在較高的技術壁壘
由于在阻隔性、冷沖壓性、耐穿刺性、化學穩定性和絕緣性方面有嚴格要求,鋁塑膜的生產技術壁壘很高,其技術難度超過正極、負極、隔膜、電解液,被稱為鋰電行業三大技術難題之一。
1.對軟包裝材料的生產技術具有較高的要求
聚合物鋰離子電池要求軟包裝材料具有較高的阻隔性,為普通鋁塑復合材料1000倍以上,普通的復合技術和復合材料難以實現該級別的阻隔性。
一般需要采用4-7層結構的復合材料和極厚的鋁箔,且生產過程中的對軟包裝材料的生產技術要求較高,需要綜合應用各種復合技術,對同一個材料同時采取擠復法、連續擠復法、干復法、三合一擠出發、流涎復合法或熱復法、多層共擠法。
2.復合內層熱封材料的選擇難度較高
聚合物鋰離子電池采用的有機電解液由多種酯組成,在存在水分的情況下,電解質會發生水解,產生酸性極強的物質。而多數熱封性材料與酯類有機物具有可溶脹性,尋找兼具足夠強的耐酸性能且不與電解液發生反應的低熔點熱封性材料難度較高。
3.包裝材料的設計復雜程度較高
軟包裝材料的設計,要滿足熱封合性較好、熱封性材料不與電鍍液起反應、具有權高的阻水阻氧性能、具有高的柔韌性和機械強度以及具有良好的耐電解液浸泡能力。
同時,又要兼顧軟包材料對聚合物鋰離子電池的影響程度和實現軟包裝材料的生產;此外,還需要根據聚合物鋰離子電池的發展提前開發所需要的軟包裝材料。
聚合物鋰離子電池對軟包裝材料的一般要求
(資料來源:軟包裝)
4.軟包裝材料質量判定周期偏長
判定軟包裝材料是否合格的試驗周期偏長。包裝領域測試儀的最小精度低于聚合物鋰離子電池所要求的阻氧、阻水性能,因此無法實現對所開發的軟包材料的定量測試。
目前一般采用實際包裝電池的最后判定法,即根據軟包材料對電池的影響速率及影響程度和電池的檢驗特性進行判斷,軟包裝材料的質量判定周期一般超過三個月。
核心技術仍未實現自主化,高端市場被日韓企業壟斷
現階段鋁塑膜的核心技術掌握在日本企業手中,同時,全球約90%的市場份額被大日本印刷株式會社、日本昭和電工、日本凸版因數株式會社和韓國栗村化學占據,其中,前兩者占據了全球市場的70%。
目前,從日本進口的鋁塑膜在國內的市場份額超過90%,我國自主研發生產的鋁塑膜市場競爭力較弱。
近年來,國產鋁塑膜在設備、技術工業、材料等方面都在持續更新和完善,產品一致性、質量和耐電解液性能都取得了較大發展。
憑借本土化生產,國內鋁塑膜價格優勢明顯,比國外產品低20%-30%,已經成功進入低端消費類市場,并逐漸向中高端市場滲透。但在儲能領域及新能源汽車領域,鋁塑膜技術和產品依舊處于被日本企業壟斷的狀態。
這一現狀的實質是國內產品關鍵技術與國外先進水平存在著較大的差距。現階段,國內鋁塑膜廠家僅有部分指標可以與大日本印刷的規格持平,但沖深性能不過關的短板較為明顯,國外的沖深在8-12mm,國內的僅為5mm左右。
此外,國內產品還存在耐電解液性能不過關的缺點。除了技術,設備、原材料、生產工藝等也阻礙著國內鋁塑膜技術的發展,國內鋁塑膜難以進入動力電池領域與高端消費類應用領域。
結語
由于在阻隔性、冷沖壓性、耐穿刺性、化學穩定性和絕緣性方面有嚴格要求,鋁塑膜的生產技術壁壘很高。
現階段鋁塑膜的核心技術掌握在日本企業手中。盡管近年來,國產鋁塑膜在設備、技術工藝、材料等方面都在持續更新和完善,產品一致性、質量和耐電解液性能都取得了較大發展,但在儲能領域及新能源汽車領域,市場依舊處于被日本企業壟斷的狀態。
-
鋰離子電池
+關注
關注
85文章
3243瀏覽量
77791 -
動力電池
+關注
關注
113文章
4540瀏覽量
77750 -
核心技術
+關注
關注
4文章
625瀏覽量
19629
原文標題:被日韓壟斷的鋁塑膜技術,在國內發展怎么樣了?
文章出處:【微信號:gh_639cc27d0014,微信公眾號:芯片晶圓切割保護膜】歡迎添加關注!文章轉載請注明出處。
發布評論請先 登錄
相關推薦
智己汽車B輪融資94億元,加速核心技術研發
原生鴻蒙系統正式發布,余承東宣布不依賴國外核心技術
國產8位MCU為什么能被國內的電子工程師大量應用?
兼容7A100T和PG2L100H雙芯核心板,米爾FPGA平臺
芯旺微電子再次入選國家級專精特新“小巨人”企業
摩爾線程與國內EDA企業合作加速GPU芯片設計
又一家人工智能企業成功IPO,核心技術涉及感知、理解、執行
【大語言模型:原理與工程實踐】核心技術綜述
安達發|APS生產排程軟件6大核心技術
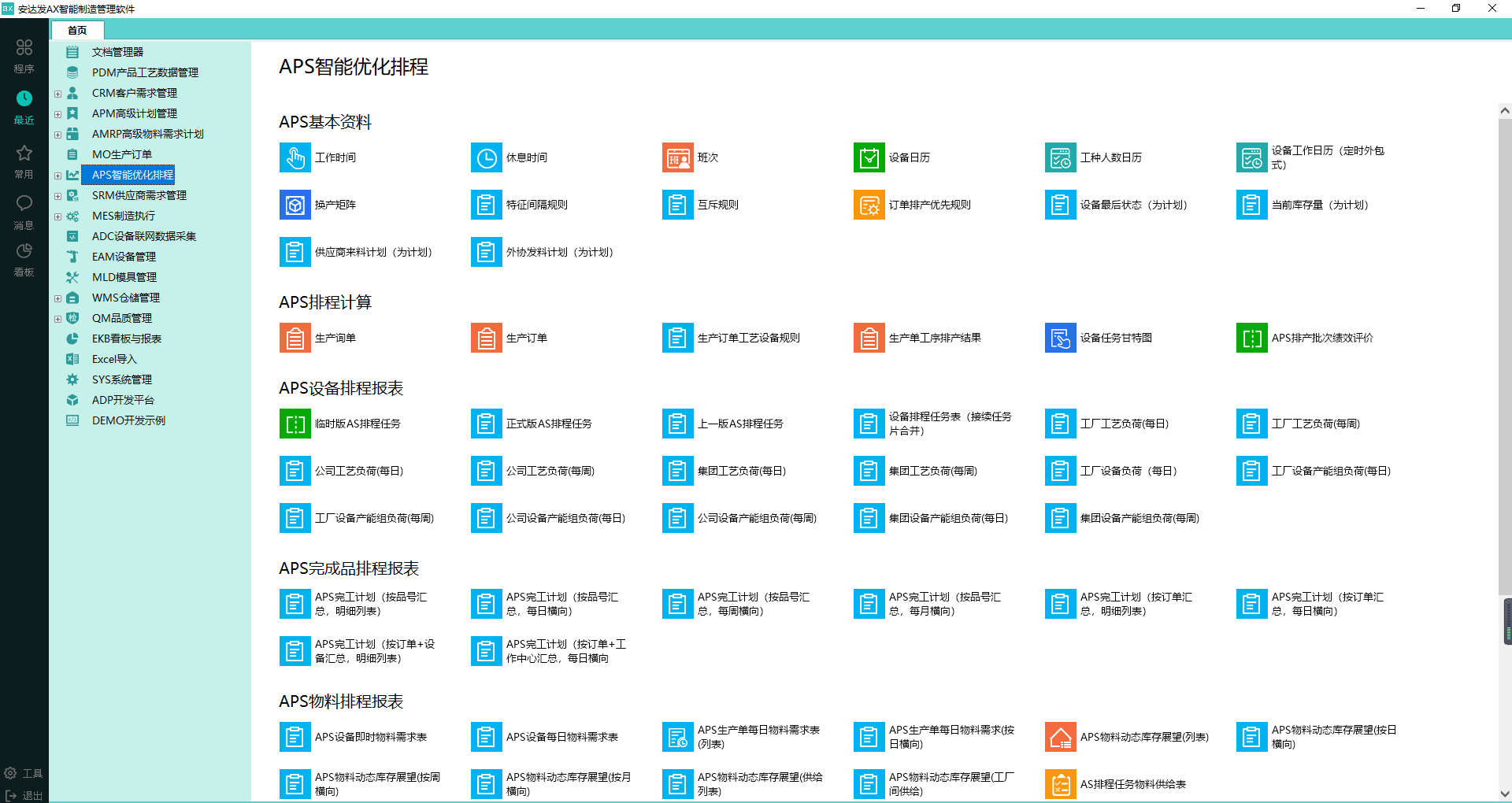
評論