隨著汽車工業的快速發展,手動變速器已經更多地在朝自動變速器轉變。這些變速器制造主要涉及的核心工藝有:軸及齒輪、殼體等關鍵部件的生產,總成裝配、試驗檢測等。
齒輪與軸類零件
1. 齒輪加工工藝流程
根據不同結構要求,齒輪零件加工主要工藝流程采用的是鍛造制坯→正火→精車加工→插齒→倒尖角→滾齒→剃齒→(焊接)→熱處理→磨加工→對嚙修整。熱后齒部一般不再加工,除了主減從齒或顧客要求磨齒的零件。
2. 軸類工藝流程
輸入軸:鍛造制坯→正火→精車加工→搓齒→鉆孔→插齒→倒尖角→滾齒→剃齒→熱處理→磨加工→對嚙修整。
輸出軸:鍛造制坯→正火→精車加工→搓齒滾齒→剃齒→熱處理→磨加工→對嚙修整。
3. 具體工藝流程
(1)鍛造制坯
熱模鍛是汽車齒輪件廣泛使用的毛坯鍛造工藝。以前較廣泛采用的是熱鍛和冷擠壓的毛坯,近年來,楔橫軋技術在軸類加工上得到了大量推廣。這項技術特別適合為比較復雜的階梯軸類制坯,它不僅精度較高、后序加工余量小而且生產效率高。
(2)正火
這一工藝的目的是獲得適合后序齒輪切削加工的硬度和為最終熱處理做組織準備,以有效地減少熱處理變形。一般的正火由于受人員、設備和環境的影響比較大,使得工件冷卻速度和冷卻的均勻性難以控制,造成硬度散差大,金相組織不均勻,直接影響機加工和最終熱處理。
(3)精車加工
為了滿足高精度齒輪加工的定位要求,齒坯的精車加工全部采用數控車床。齒輪先進行內孔和定位端面的加工,然后另一端面及外徑加工同步完成。既保證了內孔與定位端面的垂直度要求,又保證了大批量齒坯生產的尺寸離散小。從而提高了齒坯精度,確保了后序齒輪的加工質量。
4.軸類零件加工的定位基準和裝夾主要方式:
(1)以工件的中心孔定位
在軸的加工中,零件各外圓表面、端面的同軸度,端面對旋轉軸線的垂直度是其相互位置精度的主要項目,這些表面的設計基準一般都是軸的中心線,若用兩中心孔定位,符合基準重合的原則。
(2)以外圓和中心孔作為定位基準(一夾一頂)
用兩中心孔定位雖然定心精度高,但剛性差,尤其是加工較重的工件時不夠穩固,切削用量也不能太大。粗加工時,為了提高零件的剛度,可采用軸的外圓表面和一中心孔作為定位基準來加工。這種定位方法能承受較大的切削力矩,是軸類零件最常見的一種定位方法。
(3)以兩外圓表面作為定位基準
在加工空心軸的內孔時,(例如:機床上莫氏錐度的內孔加工),不能采用中心孔作為定位基準,可用軸的兩外圓表面作為定位基準。當工件是機床主軸時,常以兩支撐軸頸(裝配基準)為定位基準,可保證錐孔相對支撐軸頸的同軸度要求,消除基準不重合而引起的誤差。
殼體類零件1. 工藝流程
一般工藝流程是銑結合面→加工工藝孔和連接孔→粗鏜軸承孔→精鏜軸承孔和定位銷孔→清洗→泄漏試驗檢測。
2. 控制方法
(1)夾具方面
變速器殼體的加工工序以采用“立式加工中心加工。10#工序+立式式加工中心加工 20#工序+臥式加工中心加工 30#工序”為例,需要三套加工中心夾具,避免工件的夾緊變形,還要考慮刀具干涉、操作靈活、多件一夾、快速切換等因素。
▲ 加工中心殼體夾具
(2)刀具方面
在汽車零部件制造成本中,刀具成本占總成本的3%~5%。模塊式結構的復合刀具具有精度較高,刀柄可重復使用,庫存量少等特點,被廣泛采用,它可以大幅度縮短加工時間,提高勞動效率。因此,在精度要求不高、標準刀具能夠達到比較好的加工效果時盡量采用標準刀具,降低庫存,提高互換性。同時,對于大批量生產的零件,精度要求又高的零件采用先進的非標復合刀具更能提高加工精度和生產效率。
-
變速器
+關注
關注
5文章
317瀏覽量
34324 -
齒輪
+關注
關注
3文章
266瀏覽量
25111
原文標題:【匯總】IPTV增值服務動態大搜羅(3月16日-3月22日)
文章出處:【微信號:iptvott,微信公眾號:流媒體網】歡迎添加關注!文章轉載請注明出處。
發布評論請先 登錄
相關推薦
自動變速器動力傳遞路線分析(十二)—81-40LE系列自動變速器(圖
汽車變速器,汽車變速器是什么意思
汽車變速器工作原理是什么?
變速器裝配生產線及其工藝規程概述
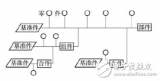
汽車電子控制自動變速器相關知識詳述
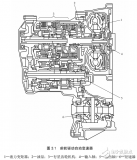
變速器的功能是什么
汽車變速器殼體軸齒輪的工藝流程詳細說明
一文詳解行星齒輪變速器
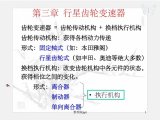
評論