隨著5G網絡的快速發展,5G天線模塊的需求越來越多,為滿足其特殊性能,部分天線模塊設計厚度已達到11.5mm以上;針對此類超厚板,在層壓、鉆孔、線路及CNC等工序均面臨較大的技術瓶頸。本文從疊層設計優化入手,采用兩次分壓子部件并提前做好線路及表面處理,然后總壓鉆孔,再采用二次內定位成型等技術,有效實現了11.5mm超厚板的批量加工,滿足了客戶特種需求。
5G網絡作為第五代移動通信技術, 其最高理論傳輸速度可達每秒數10Gb,這比目前4G網絡的傳輸速度快數百倍; 由于其高速率、低時延、低功耗的特點,未來將滲透到物聯網及各行各業,與工業設施、醫療儀器、交通工具等深度融合,有效滿足工業、醫療、交通等垂直行業的多樣化業務需求。同時隨著5G網絡時代的快速來臨,其核心部件 5G天線模塊的需求也越來越多,為滿足其特殊性能,部分天線模塊設計厚度已達到11.5mm以上;針對此類超厚板,在層壓、鉆孔、電鍍、線路及CNC等工序均面臨較大的技術瓶頸。本文從疊層設計優化入手,采用兩次分壓子部件并提前做好線路及表面處理,然后總壓鉆孔、再采用二次內定位成型等技術,有效實現了11.5mm超厚板的批量加工,滿足了客戶特種需求。
超厚5G天線模塊加工工藝分析
該產品的關鍵技術難點涉及5大塊,包括:(1)超厚板盲埋孔+背鉆+樹脂塞孔技術;(2)超厚板層壓技術;(3)超厚板二鉆精度控制技術;(4)超厚板表面處理工藝;(5)超厚板外形加工技術。
針對這些難題,需要對產品結構優化以滿足可制造性。客戶設計線路為6層,使用4張高頻材料對壓,成品板厚為11.44mm,考慮到天線模塊的設計指標,各層介質厚度無法降低。
客戶原設計金屬化通孔+背鉆,考慮到11.5mm超厚板壓合后在沉銅/電鍍/線路/蝕刻/阻焊等工序的困難度,經分析網絡連接后,建議客戶將原L36+L13背鉆取消,更改為L13+L46盲孔互連,結構優化后兩次分壓厚度為6.7mm+4.3mm,其電鍍難度大大降低,且盲孔設計比背鉆更利于高頻信號傳輸,如下圖1所示。考慮到總壓后阻焊及表面處理制作困難,特將流程優化到分壓后制作完成,即總壓后無需再做阻焊及表面處理。
經上述工藝優化后,11.5mm天線模塊加工基本有了可制造性。
圖1 優化為兩次盲孔分壓再總壓結構
產品制程設計
超厚板兩次盲孔分壓
對兩次盲孔分壓流程設計如下:
①盲孔L1/L3+背鉆+樹脂塞孔(使用X公司高速板材與高速PP,子部件板厚6.7mm)
流程:內層L10+L23制作→ L1/L3分壓 →鉆孔→等離子→ 沉銅→一銅
背鉆→樹脂塞孔→內線酸蝕→內層蝕檢
②盲孔L4/L6制作+樹脂塞孔(使用X公司高速板材與高速PP,子部件板厚4.3mm)
流程:內層L5/6常規流程制作→L4/L6分壓 →鉆孔→等離子→沉銅→一銅
→樹脂塞孔→內線酸蝕→內層蝕檢
考慮到總壓后整體板厚達到11. 5 mm左右,在此厚度下制作阻焊及表面處理非常困難,為此特將流程優化到分壓后/總壓前制作完成,即總壓后無需再做阻焊及表面處理。
此外層壓的板邊還要設計兩組鉚合定位孔,便于后續壓板可進行精確對位,如下圖2所示。
圖2 板邊兩組鉚合定位孔設計
總壓前還要進行沉邊處理,沉邊后用8mm長度鉚釘即可滿足鉚合要求。
①L1/3板厚6.7mm,從頂層長邊沉邊深度3.2mm, 余厚3.5 mm。
②L4/6板厚4.3mm,從底層長邊沉邊深度2.3mm,余厚2.0mm。
完成總壓后進行切片分析,可見切片層間偏移在4.0mil以內,符合客戶要求,效果如下圖3所示。
圖3 總壓后對位切片圖
超厚板二鉆精度控制
客戶對定位精度有特殊要求,孔中心位置偏差要求按±0.05mm控制。因此需要預鉆小孔,使內層盲孔制作時先預鉆小孔,以減少總壓鉆通孔的阻力,降低斷刀風險。同時采用板邊菲林孔定位測量漲縮,為鉆孔文件提供精確的尺寸漲縮信息。最后在鉆孔加工過程中,要使用刃長12mm直徑1.65mm新鉆刀,一步下鉆方式,一次鉆透NPTH安裝孔,防止分步鉆孔造成精度偏差,效果如下圖4所示。
圖4 二鉆后隔離環無明顯偏移
超厚板外形加工及熱沖擊效果
由于成品板過厚,需要采用正反控深銑的方式加工,外形設計頂層、底層兩組文件,從正、反兩面各控深6mm做外形加工。此外定位方式以板內1.65mm-NPTH孔做內定位,防止外形偏移。完成加工后檢測外形,設計尺寸為32.5mm*32.5mm*11.4mm,實際檢驗尺寸偏差≤0.10mm,板邊光滑平整,符合品質要求,如下圖5、圖6所示。
圖5 外形后邊緣質量 圖6 外形尺寸測量
對成品進行耐熱性測試,在熱沖擊條件288℃/10S/3次條件下,未出現分層爆板現象。
圖7 熱沖擊無爆板分層(熱沖擊條件288℃/10S/3次)
總結
本文提供了一種11.5mm超厚板的生產加工方法,并通過工藝改進,有效解決了業界常見的技術難題:
1、超厚板層壓技術:常規水平線加工板厚上限在7.0mm左右,本次通過結構優化,將通孔+背鉆優化為兩次盲孔分壓,有效滿足了超厚板的層壓、電鍍及蝕刻要求。
2、超厚板表面處理工藝:通過流程優化,將阻焊及表面處理優先在盲孔子部件時制作完成,大大降低了表面處理的工藝難度。
3、超厚板二鉆技術:將分步下鉆改為預鉆小孔+一次下鉆11.5mm通孔、確保孔位精度控制。
4、超厚板成型技術:采用內定位+正、反控深銑,保證外形公差在±0.10mm以內。
作者:石學兵 唐宏華 樊廷慧 陳春
本文首發于《印制電路信息》 2018年11月 第26卷 總第316期
-
5G
+關注
關注
1354文章
48466瀏覽量
564518
發布評論請先 登錄
相關推薦
愛立信5G增強技術測試再獲佳績
華為5g技術介紹 華為5g技術的優勢
最常見的三種RFID標簽天線制作工藝介紹
嵌入式設備中的4G/5G模塊管理
請問mx880 5G數據終端可以設置優先5G網絡嗎?
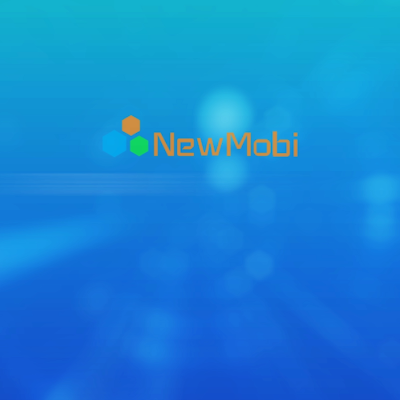
MPI 5G手機天線新材料的應用及焊接制造
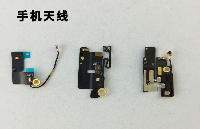
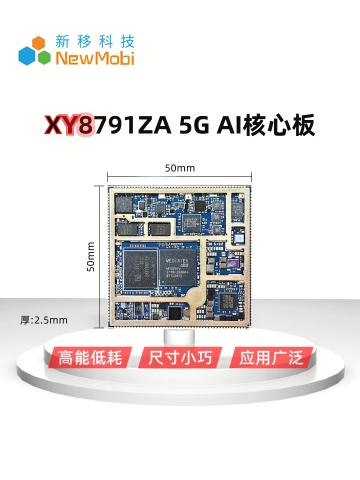
評論