引線成形的主要目的是一方面保證器件引線能夠焊接到pcba相對應的焊盤上;另一方面主要解決應力釋放問題,pcba組件焊接完成并調試通過后,將進行振動和高低溫沖擊等環境應力試驗,在這種環境應力條件下,將對器件本體和pcba焊點強度形成一定的考驗,通過對集成電路引線成形,將對環境應力試驗過程中形成的一部分應力加以消除,消除應力主要體現在成形元器件引線根部和焊接點之間的所有引線或導線上,以保證兩個制約點間的引線或導線具有自由伸縮的余地,防止由于機械振動或溫度變化對元器件和焊點產生有害的應力,對提高產品可靠性起到關鍵的作用,因此集成電路引線成形越來越受到產品生產部門的重視。
除特殊情況外,集成電路引線有三種出線方式,分別為頂部出線方式、中部出線方式及底部出線方式,但無論哪種出線方式,其成形機理不會有太大的差別,只是在工藝控制上有所不同。根據實際使用經驗及按照標準的有關要求,下面佩特科技小編就來講解分析一下集成電路引線成形的幾個關鍵技術參數:
1、肩寬(A)
即引線根部到第一個彎曲點的距離,如圖1所示,成形過程中器件兩邊肩寬應基本保持一致,引線不得在器件本體根部彎曲,器件本體到引線彎曲點間平直部分距離A,其最小尺寸為2倍引線直徑或0.5mm,在這種條件下,還應綜合考慮相對應pcba焊盤的尺寸,進而根據實際需求進行適當調整。
2、焊接面長度(B)
即引線切割點到第二個引線彎曲點的距離,如圖1所示,為了保證焊接的可靠性,對于圓形引線而言,應保證引線搭接在焊盤上的長度最小為3.5倍的引線直徑,最大為5.5倍的引線直徑,但不應小于1.25mm;對于扁平引線而言,應保證引線搭接在焊盤上的長度最小為3倍引線寬度,最大為5倍引線寬度,引線切腳后的端面離焊盤邊緣至少為0.25mm,扁平引線寬度小于0.5mm時,其搭接長度不小于1.25mm;
3、站高(D)
即成形后元器件本體與安裝面間的距離,如圖1所示。其間距最小為0.5mm,最大距離為1mm。在元器件引線成形過程中,提供一定尺寸的站高是非常必要的,其主要原因也是考慮到應力釋放的問題,避免元器件本體與pcba表面間形成硬接觸后而造成應力無釋放空間,進而損傷器件。另一方面,在三防和灌封過程中,三防漆及灌封膠能夠有效浸入芯片本體底部,固化后將有效提高芯片對pcba的附著強度,增強抗振效果。
4、引線彎曲半徑(R)
如圖1所示,為了保證集成電路引線成形后,其引線焊接面具有良好的共面度(不大于0.1mm),由于成形過程中,器件引線存在反彈,不同材料和不同引線厚度(直徑)的反彈系數存在一定的差別,因此引線成形過程中應控制好引線彎曲半徑,確保成形后引線焊接面共面度良好,翹曲不超過0.25mm,IPC610D中規定了當引線厚度小于0.8mm時,最小引線彎曲半徑為引線厚度的1倍;當引線厚度(或直徑)大于0.8mm時,最小引線彎曲半徑為引線厚度的1.5倍~2.0倍。實際成形過程中一方面借鑒上述經驗值,另一方面通過理論計算進行確定,需確定的主要參數為成形模具的圓角半徑和引線的內側圓角半徑,其計算方法如下:
計算方法公式
其中:
R—引線彎曲內側圓角半徑
r—成形模具圓角半徑
σs—材料屈服極限,MPa
E—材料彈性模數
t—引線厚度(或引線直徑),mm
5、引線成形的共面性
共面性是最低落腳平面與最高引腳之間的垂直距離。共面性是集成電路引線成形的一個重要參數之一,如果器件的共面性不好,超過規定的允許范圍,將造成器件本體受力不均,影響產品整機可靠性,JEDEC規定了器件引線成形共面性為0.1016mm。引起共面性不良的主要因素有以下幾個方面:首先是成形模具的檔條設計不合理,共面性較差,需要在設計上進行適當調整;另一方面也與操作人員的操作穩定性以及在周轉過程中引起器件引線翹曲都有很大關系。成型后的集成電路引線共面性的評估通常情況下通過外觀進行定性判定,其方法是將成形后的集成電路放到平面度良好的平面上,用10倍放大鏡側面觀察各引腳在平面上的位置情況,有條件的單位可購置輪廓儀或光學引腳掃描儀進行定量測量。
6、引腳歪斜
引腳歪斜是指相對于封裝的中心線測量,其成形的引腳從其理論位置的偏移。通常情況下可通過外觀進行定性判斷,其主要方法是將成形后的集成電路放置于待焊接的pcba加工焊盤上,觀察引腳與pcba焊盤的相對位置,應保證最大側面偏移不得超過引線寬度的25%。這是最低要求,另一方面可通過輪廓投射儀和光學引腳掃描系統進行精確測量,其引腳歪斜應小于0.038mm。引腳歪斜的原因可能與許多因素有關,包括成形、引腳切割、成形和引腳結構本身。
-
PCBA
+關注
關注
23文章
1530瀏覽量
51653 -
華強pcb線路板打樣
+關注
關注
5文章
14629瀏覽量
43094
發布評論請先 登錄
相關推薦
什么是專用集成電路 通信專用集成電路有哪些類型
專用集成電路和通用集成電路的區別在哪 專用集成電路 通用集成電路有哪些類型
專用集成電路設計流程是什么 專用集成電路的特點有哪些
專用集成電路技術有哪些特點 專用集成電路技術有哪些類型
專用集成電路技術是什么意思 專用集成電路技術應用有哪些
專用集成電路技術有哪些特點
簡述專用集成電路設計的基本要求有哪些
專用集成電路 通用集成電路有哪些
專用集成電路技術應用有哪些
專用集成電路技術是什么意思 專用集成電路技術有哪些
專用集成電路是什么電路 專用集成電路和通用有哪些不同
CMOS工藝技術的概念、發展歷程、優點以及應用場景介紹
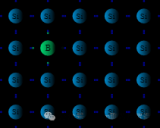
評論