SMT模板概述
SMT模板是一種薄片材料(金屬),切割成電路焊盤圖案該材料。最常見的材料是黃銅和不銹鋼。
在表面貼裝組件中,SMT模板是精確和可重復焊膏沉積的門戶。當焊膏通過模板孔印刷時,它會形成沉積物,將元件固定在適當的位置,并在回流時將它們固定在基板上,通常是PCB。模板設計 - 其成分和厚度,孔的大小和形狀 - 最終決定了沉積物的尺寸,形狀和位置,這對于確保高產量的裝配過程至關重要。
smt激光模板
焊膏模板的演變和歷史
焊膏的基本理解模板技術及與之相關的術語:
SMT模板有兩個主要功能。第一是確保在襯底上精確放置諸如焊膏,焊劑或密封劑的材料。第二是確保形成適當大小和形狀的沉積物。
SMT模板技術發展為化學蝕刻,激光切割和電鑄箔,因為印刷要求決定了性能增強。
最初,有厚膜屏幕;然而,穿過孔口開口的金屬絲網阻礙了漿料轉移。因此,提供化學蝕刻的模板以獲得更好的開放區域,并且適用于鉛間距低至0.8 mm的SMT器件。
化學蝕刻梯形孔,以及電解拋光和鍍鎳的后處理,有助于平滑孔徑側壁,改善粘貼轉移。化學蝕刻孔的一個工藝問題是小孔的蝕刻速率與大孔的蝕刻速率之間的差異。帶蝕刻有助于解決這個問題,但是對于小孔徑有限制。
現在要克服這個問題,使用激光模板并在90年代中期引入它們,恰好及時滿足0.65毫米的印刷要求。間距SMT器件。
小激光束光斑尺寸切割小孔和大孔,精度相同。啟用電拋光和鍍鎳的后處理有助于平滑孔徑側壁。
早期的激光切割速度很慢,因此混合模板很受歡迎,其中大孔徑經過化學蝕刻,小孔徑被激光切割。橡膠刮刀片與屏幕配合良好,但從較大的孔徑中舀出漿料,減少了漿料的轉移量。
因此,為了解決這個問題,使用了金屬刮刀刀片,并且變得非常受歡迎。
參考這種含糊劑 - 還介紹了頭部輸送系統。這些系統使用壓力將漿料推入孔中,而擦拭器刮片有助于將漿料容納在頭部并在穿過孔后擦拭干凈。
焊膏模板模板技術的設計指南由縱橫比確定,定義為孔徑寬度(W)除以模板厚度(T)大于1.5。
在這個比例的幫助下,可以進行良好的粘貼轉移。
如果孔徑的長度(寬度至少比寬度大5倍),寬高比是一個很好的指導。
但是再次引入BGA和QFN的縱橫比有一定的局限性。所以引入了新的設計指南,稱為面積比,定義為孔徑開口面積除以孔壁面積。孔的壁試圖將膏保持在孔中,而孔開口下的墊試圖將膏拉開。
模板技術
焊膏Stencil Technologies
基本上,業內正在使用五種SMT模板技術:激光切割,電鑄,化學蝕刻塑料和混合。 Hybrid是化學蝕刻和激光切割的組合。化學蝕刻對于階梯模板和混合模板非常有用。
SMT模板的化學蝕刻工藝
使用兩個正像通過化學銑削從兩側蝕刻金屬掩模和柔性金屬掩模模板。在此過程中,蝕刻不僅在所需的垂直方向上進行,而且在橫向上進行。這稱為底切,開口比期望的大,導致額外的焊料沉積。因為從兩側進行50/50蝕刻,所以在中心幾乎形成一個逐漸變細到略微沙漏形狀的直壁。由于電蝕模板壁可能不平滑,電拋光是一種微蝕刻工藝,是一種實現的方法。光滑的墻。在孔中實現更光滑側壁的另一種方法是鍍鎳。拋光或光滑的表面有利于漿料的釋放,但可能導致漿料越過模板表面而不是在刮板前面滾動。通過選擇性地拋光孔壁而不拋光模板表面可以避免這個問題。鍍鎳進一步改善了平滑度和印刷性能。但是,它確實減少了光圈開度并需要進行藝術品調整。
化學蝕刻模板
< strong>激光切割工藝
激光切割是一種減法工藝。 Gerber數據被翻譯成激光理解的CNC類型語言。通過僅移動激光頭,移動僅固定模板的工作臺或每個工具的組合來切割光圈。激光束進入孔徑邊界內并橫穿到周邊,在那里它完全切出金屬孔,一次一個孔。切割的平滑度取決于許多參數,包括切割速度,束斑尺寸,激光功率和光束聚焦。典型的束斑尺寸約為1.25密耳。激光可以在很寬的尺寸和形狀要求下切割非常精確的孔徑尺寸。與化學蝕刻一樣,激光切割孔徑尺寸必須根據所采用的后處理處理進行調整,因為在此過程中會發生孔徑尺寸變化。
電解拋光的激光切割模板絕對具有比非孔徑更光滑的內孔壁 - 電拋光激光切割模板。因此,前者在給定面積比下會釋放比后者更高的糊劑百分比。
一些激光切割機是自制系統,一些是老式激光器,有些是精細切割的激光機。電拋光和鍍鎳也可用于進一步平滑表面壁并改善焊膏釋放。
激光模板
模板印刷工藝可分為三類:光圈填充工藝,漿料轉移工藝和沉積漿料的位置。所有這三個過程在實現所需結果方面起著至關重要的作用 - 將精確體積的漿料(磚)沉積到基板上的正確位置。
印刷焊膏的第一步是填充模板孔用膏。這是使用金屬刮刀來實現的。有幾個因素可能有助于光圈填充過程。孔徑相對于刮刀刀片的方向對填充過程有影響。
孔徑方向與刀片行程方向相同的孔徑不能填充以及以短軸方向定向的孔徑到刀片行程。刮刀速度也會影響孔徑填充。必須減小刮刀速度以填充孔徑,使長軸平行于刮刀行程。
刮刀刀刃會影響焊膏填充模板孔的程度。經驗法則是在最小的刮刀壓力下進行打印,同時仍保持模板表面上焊膏的清潔擦拭。如果刮刀壓力太高,刮刀和模板都可能被損壞。過多的刮刀壓力也會導致模板表面下的漿料涂抹。
如果壓力太低,可能會發生兩種情況中的一種。在小孔徑的刮板側留下粘貼將保持粘貼,防止其釋放到PCB墊,導致焊料不足。在刮刀側的擋板上留下的大孔將通過孔向下拉,導致多余的焊料。
適當的刮刀壓力是實現漿料清潔擦拭的最小壓力。最小壓力是葉片類型的函數。最近的一項研究表明,一個刮刀*的最小刮刀壓力約為聚四氟乙烯/鍍鎳刀片用于無鉛焊膏的40%。測試證實,無鉛焊膏通常比錫/鉛膏需要大約25%的刮刀壓力。
模板技術的技術說明
在了解模板技術的技術方面之前,有必要了解與焊膏印刷相關的性能問題。
有三個主要的性能問題,它們如下:
孔徑尺寸(孔徑的寬度和長度)和模板箔厚度決定了應用于印刷電路板(PCB)的焊膏的潛在體積
焊膏從模板孔壁釋放的能力。
在印刷周期中穿過模板,焊膏填充模板孔。然后,在電路板/模板分離循環期間,焊膏會釋放到電路板上的焊盤中。理想情況下,在打印過程中填充孔徑的100%漿料從孔壁釋放并附著到板上的焊盤上,形成完整的焊料磚。
模板技術狀態
在表面貼裝組件中,模板是精確,可重復焊膏沉積的途徑。
當焊膏通過模板孔印刷時,會形成沉積物,將元件固定到位,并在回流時將它們固定到基板上。
模板設計 - 其成分和厚度,孔徑的大小和形狀 - 最終決定了沉積物的大小,形狀和位置,這對于確保高產量的裝配過程至關重要。 br>今天,各種各樣的材料和制造技術使QualiEco Circuits Ltd.能夠設計模板,以滿足細間距技術,小型化元件和密集封裝板的裝配挑戰。
Stencil技術現在提供全系列的m成像材料。
模板設計師已經深入了解孔徑尺寸和形狀如何影響沉積。新技術將印刷平臺和模板的功能擴展到各種應用,如粘合劑沉積和晶圓凸點。
方面和面積比的重要性設計模板孔徑:
膏體從內孔壁釋放的能力主要取決于三個主要因素:?模板設計的面積比/縱橫比
孔徑側壁幾何形狀
孔壁光滑度
第一個因素是孔徑設計相關而另外兩個因素與模板技術相關的因素。
面積比是孔徑開口下方的面積除以內部孔壁的面積;面積比= [(LXW)/(2(L + W)T)]。 br>歷史上,縱橫比是孔徑的寬度除以模板的厚度;寬高比= W/T.可接受的膏體釋放的普遍接受的設計準則是[面積比率大于] 0.66和縱橫比[大于] 1.5。縱橫比實際上是面積比的一維簡化。當長度(L)遠大于寬度(W)時,面積比與縱橫比相同。
當模板與基板分離時,焊膏釋放遇到競爭過程。 br>這再次產生懷疑,它會轉移到基板上的焊盤還是會粘到側面孔壁上?
解決方案是,當焊盤面積大于三分之二時在內孔壁的區域內,膏體可能達到80%或更好的膏體釋放。
縱橫比和面積比是設計模板孔徑時的重要考慮因素。例如,一個20密耳間距的四方扁平封裝(QFP),孔徑設計為10密耳×60密耳,采用5密耳模板,長寬比為2.0,面積比為0.86。所以在這里你可以看長寬比大于1.5,面積比也大于0.66。因此,采用優質激光模板的設計可以獲得良好的印刷性能。
然而,考慮采用20密耳微球柵陣列(microBGA),10密耳孔徑,5密耳 - 厚模板。因為孔徑是圓形的或者是具有圓角的正方形,所以面積比是決定因素。在這種情況下,面積比為0.5,遠低于推薦值0.66。可以通過減小模板厚度或增加孔徑來改變孔徑設計,或者可以選擇模板技術,以在該面積比下提供更好的焊膏釋放。
對于方孔,面積比= S/4T,其中S是正方形的一側。對于圓形孔徑,面積比= D/4T,其中D是圓的直徑。
焊膏模板的設計規則和功能
SMT模板孔徑的大小和形狀決定了體積,沉積在基材上的材料的均勻性和清晰度。因此,嚴格控制孔徑質量對于成功的模板設計至關重要,特別是對于必須精確沉積少量材料的精細和超細間距應用。
面積比(面積比)等測量孔徑開口除以孔壁的表面積)和縱橫比(孔徑寬度除以模板厚度)可用于確定合適的孔徑尺寸。一般規則是,對于可接受的膏體釋放,面積比應大于0.66,縱橫比大于1.5。在設計符合這些規則的孔徑時,有必要根據其自身優點考慮每種模板制造技術。例如,化學蝕刻工藝降低到1.5縱橫比以下是具有挑戰性的,而激光切割時,可以生成與模板厚度成1:1縱橫比的孔。
印刷過程中,當模板與基板分離時,競爭的表面張力決定了焊膏是否會轉移到已經印刷過的焊盤上或者仍然粘附在模板孔壁上。
當焊盤區域如果孔壁面積大于孔徑壁面積的66%,則實現有效膏體轉移的可能性增加。當比率降低到66%以下時,漿料轉移效率降低,印刷質量變得不穩定。
孔壁的光潔度會對這些水平產生影響。在制造過程中經過電解拋光和/或電鍍的激光切割孔可提高漿料轉移效率。
最終孔徑尺寸。這決定了將在PCB模板上印刷的焊膏量。三個尺寸(在矩形孔上),孔的長度,寬度和壁高決定了印刷在板上的焊料磚的體積。高度或SMT模板厚度將對模板的性能和隨后的產品缺陷率產生顯著影響。正確的規格將最大限度地減少產品缺陷和返工。最終孔徑尺寸還將考慮所需的任何減少量。還將更詳細地討論減少。
模板是否遵守某些物理定律,以保證焊膏成功地從模板轉移到PCB。在印刷期間,漿料粘附到PCB上的焊盤和模板的孔壁上。對墊的粘附力必須大于對模板的粘附力,以確保良好的轉移。因此可以推斷出可印刷性將取決于模板壁面積與開口面積的比率。這當然忽略了其他微小的影響,如壁面粗糙度和拔模角度。
模板尺寸精度和印刷位置精度。模板尺寸精度取決于傳送的CAD數據的質量,用于制造模板的方法和技術,以及使用條件(即模板在高于正常溫度下不使用)。印刷位置精度將由所使用的對齊方法確定。
模板設計指南
模板設計的注意事項:
孔徑尺寸與焊盤尺寸,孔徑形狀,模板厚度,粘合劑印刷,SMT模板制造方法,模板厚度,孔徑設計等
光圈尺寸與焊盤尺寸有關
建議將更細的間距光圈開口略小于著陸焊盤尺寸。
主要用于:
改善間隙尺寸著陸墊和模板的下側。
防止在細間距組件上橋接。
推薦的焊盤和孔徑尺寸:
模板墊和孔徑尺寸
必須從每一側均等地采用孔徑寬度減小,以使孔徑在墊片上居中。 (圖1)孔徑長度可以通過相似的尺寸減小,以減少焊球的可能性。?模板墊
孔徑可以移到焊盤的外邊緣,以減少“下”的可能性芯片“焊球。 (圖2)。
孔徑形狀:
模板孔徑
模板厚度:
模板或“箔”厚度是模板設計的重要組成部分。焊盤尺寸,孔徑開口和箔厚度之間存在的關系會影響PCB上的最佳焊膏沉積。雖然孔的尺寸可以適當地適用于墊,但是太薄或太厚的模板仍然可能導致焊膏的沉積不是最佳。
這種關系也稱為“方面”。方面是將力從孔中拉到墊上或者使膏保持在孔內的力的差異。這些力可以量化并表示為稱為縱橫比的度量。簡單來說,為了使漿料充分沉積在焊盤上,焊膏表面張力必須強于焊膏到孔壁的表面張力。
采用了一套廣泛的規則來幫助我們設計模板具有適當的寬高比,具體取決于訂購的模板類型。重要的是,電路板上的最小孔徑用于此計算。
模板型間距
例如:
激光切割模板16密耳引線元件(8密耳孔寬)的最大箔厚度應為6密耳* [6 x 1.2 = 8]
模板應始終具有0.2或更大的焊膏拉伸張力:
smt stencil
焊膏模板
模板框架:(也稱為“膠合”或安裝模板)
框架模板是最強的形式目前市場上的激光切割模板,專為大批量絲網印刷而設計。
主要特點和優勢:
平滑的獨特工藝Aperture Walls
非常干凈的激光切割孔徑
卓越的打印性能
適用于大批量模板印刷
獨特的工藝創造永久性不可拆卸的不褪色基準
蝕刻和激光切割模板是制作模板的減法工藝。化學蝕刻工藝是最古老和最廣泛使用的方法,而激光切割是一個相對較新的方法。
要獲得良好的印刷效果,您需要結合使用正確的方法和材料:
粘貼材料 - 粘度,金屬含量,最大粉末尺寸和最低通量活性可能
工具 - 打印機,模板和刮刀刀片 - 工藝 - 良好的套準,清潔掃描
-
pcb
+關注
關注
4319文章
23080瀏覽量
397522 -
PCB板
+關注
關注
27文章
1447瀏覽量
51610 -
華強pcb線路板打樣
+關注
關注
5文章
14629瀏覽量
43035
發布評論請先 登錄
相關推薦
選擇SMT加工廠時需要注意的幾個關鍵點
尋找優質smt貼片加工廠需要遵循的原則
何選擇合適的SMT貼片錫膏?
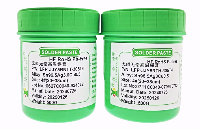
如何選擇合適的SMT貼片錫膏?
SMT貼片廠選擇錫膏的方法有哪些?
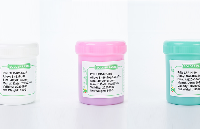
在smt貼片加工廠中選擇性波峰焊存在的作用和意義
SMT貼片加工廠使用哪些關鍵設備?
SMT貼片加工發生短路的原因及解決方法
全流程掌控:為何選擇同家廠商做PCB與SMT
SMT貼片加工時錫膏如何選擇?
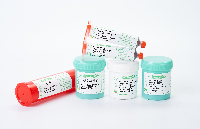
SMT加工廠用選擇性波峰焊有什么優點嗎?
SMT貼片加工必備:全面解析錫膏種類與特性
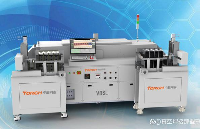
Samtec - 通過優化焊膏模板開孔來擴大連接器的選擇范圍
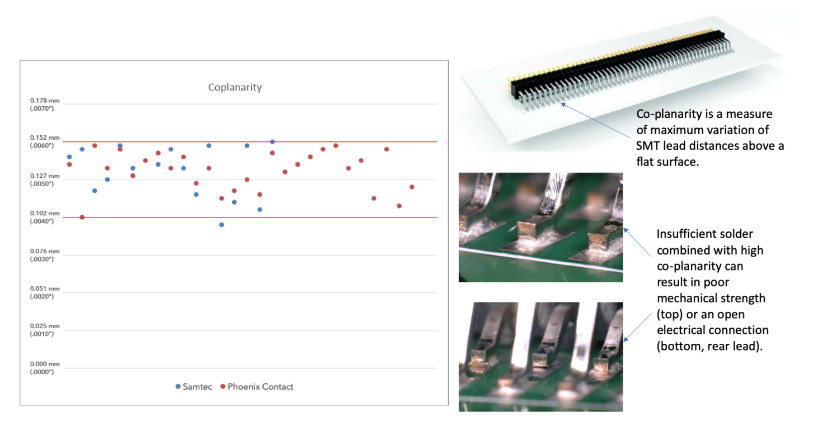
評論