隨著經濟和科學技術的發展,人們開始對電子產品的要求越來越高,這些電子產品必須滿足多功能,小型化,高密度,高性能,高品質的要求。因此,對于SMT行業來說,高焊接質量是電子產品的壽命。
然而,在實際制造中,通常會發生焊接缺陷,特別是在回流階段。事實上,這一階段所見的焊接問題并非完全由回流焊技術引起,因為SMT焊接質量與PCB焊盤的可制造性,模板設計,元件和PCB焊盤可焊性,制造設備狀態,焊料質量密切相關每個工作人員的粘貼和技術參數以及每個工人的操作技能。 SMT的制造程序如下圖1所示。
此問題的每個環節都可能出現問題程序,影響SMT的焊接質量。在本文中,將討論和分析可能影響SMT焊接質量的元素,以避免在實際制造中出現類似問題。
BOM準備
作為SMT中最重要的復合材料之一,BOM的質量和性能與回流焊接的質量直接相關。具體而言,必須考慮以下幾個方面:
a。元件包裝必須滿足貼片機的自動安裝要求。
b。元件圖必須滿足自動SMT的要求,因為它必須具有高尺寸精度的標準形狀。
c。元件的可焊接端和PCB焊盤焊接質量應滿足回流焊接的要求,元件和焊盤的可焊端不會受到污染或氧化。如果元件和PCB焊盤的可焊端遭受氧化,污染或潮濕,則可能會發生一些焊接缺陷,如潤濕不良,偽焊接,焊珠或腔體。對于濕度傳感器和PCB管理尤其如此。真空包裝后,濕度傳感器必須存放在干燥箱中,下次制造前必須將其烘烤。
PCB墊的可制造性設計
SMT的水平在于PCB設計質量,是影響表面貼裝質量的第一要素。根據惠普的統計數據,70%至80%的制造缺陷源于PCB設計問題,包括基板材料選擇,元件布局,焊盤和導熱墊設計,焊接掩模設計,元件封裝類型,裝配方法,傳輸邊界,定位,光學定位點,EMC(電磁兼容性)等
對于具有正確焊盤設計的PCB,即使在表面安裝過程中發生一點歪斜,也可以在熔錫焊錫表面張力的影響,稱為自動定位或自校正效應。但是,如果PCB焊盤設計不正確,即使安裝位置非常準確,仍會出現焊接缺陷,例如元件位置偏移和墓碑形狀。因此,在SMT焊盤設計方面必須仔細考慮以下幾個方面。
?焊盤的對稱性。為了避免回流焊接后的位置偏移和墓碑問題,對于0805或更低的芯片元件,兩端的焊盤應保持對稱的焊盤尺寸和吸熱和散熱能力,以保持熔化表面張力的平衡焊錫。如果一端在大銅箔上,則建議在大銅箔上連接焊盤使用單線連接。
?焊盤之間的間距。為了確保元件端部或引腳與焊盤之間的合適搭接尺寸,當焊盤之間的間隙過大或過小時,往往會導致焊接缺陷。
?剩余尺寸焊盤必須確保在元件端部或引腳與焊盤之間的搭接接合后焊接點的彎月形狀。
?焊盤寬度應基本兼容與組件末端或引腳的組合。
?不得在通孔上放置通孔過孔。否則在回流焊接過程中,錫熔化可能會沿著通孔過孔流走,產生偽焊接和錫不足。它可能會流到電路板的另一側而導致短路。
焊膏印刷
焊膏印刷技術主要旨在解決與焊膏印刷量(填充量和焊膏轉移量)不相容的問題。根據專業統計數據,正確設計PCB后,60%的PCB用于返工是由于焊膏印刷不良造成的。在焊膏印刷中,必須記住三個重要的“S”:焊膏,模板和刮刀。如果選擇正確,可以獲得優異的印刷效果。
?焊膏質量
作為必要的材料回流焊,焊膏是一種由合金粉末和助焊劑(松香,稀釋劑,穩定劑等)均勻混合的膏狀焊料,其中合金粉末是焊點成分的關鍵要素。助焊劑是消除表面氧化,提高潤濕性和確保焊膏質量的關鍵材料。在質量方面,一般來說,80%至90%的焊膏屬于金屬合金,而就其體積而言占50%。焊膏質量保險主要來自兩個方面:存儲和應用。焊膏通常儲存在0到10°C之間,或根據制造商的要求儲存。對于其應用,SMT車間的溫度必須為25°C±3°C,濕度必須為50%±10%。此外,其回收時間必須為4小時或更長,并且在施加之前必須進行充分攪拌,以使其粘度具有優異的可印刷性和脫模變形。應用后必須正確放置焊膏蓋,并且焊膏必須在兩小時內完成回流焊接。
?模板設計
模板的關鍵功能在于PCB焊盤上均勻的焊膏涂層。模板印刷技術必不可少,其質量直接影響錫膏印刷的質量。到目前為止,制造模板有三種方法:化學腐蝕,激光切割和電鍍。在完全考慮并適當處理以下方面之前,不會確保模板設計。
a。鋼板厚度。為了保證焊膏量和焊接質量,模板表面必須光滑均勻,鋼板厚度的選擇應由引腳間距最小的元件決定。鋼板厚度與最小螺距,組分值之間的關系可歸納于下表1中。
b。光圈設計。孔是梯形截面孔,其開口為喇叭口。他們的墻壁光滑,沒有毛刺。寬厚比=孔徑寬度/模板厚度(適用于Fine-Pitch QFP,IC);面積比=孔徑/孔壁面積的基面積(0201,BGA,CSP部件)。
c。防焊球加工。在0603或以上CHIP元件的模板孔上實施的防焊球加工可有效避免回流焊后產生焊球。對于墊子太大的部件,建議應用網格劃分來阻止過多的錫產生。
d。 MARK 。模板B側應至少生成3個MARK點,模板應與PCB上的MARK兼容。應該有一對具有最長對角線距離的MARK點,以提高打印精度。
e。印刷方向。印刷方向也是關鍵控制點。在打印方向確定的過程中,彼此之間具有良好空間的組件不應太靠近軌道。否則,橋接連接可能是由于錫太多造成的。
?刮板
鏟運機,在某種程度上,根據不同硬度的材料和形狀,對印刷質量產生影響。通常,使用鍍鎳的鋼刮刀,通常使用60°的刮刀。如果有通孔元件,建議使用45°的刮刀,以便增加通孔元件上的錫量。
?印刷參數
印刷參數主要包括刮刀速度,刮刀壓力,模板下降速度,模板清潔模式和頻率。刮刀與模板的角度和焊膏的粘度之間確實存在限制性關系,因此在正確控制這些參數之前,不能確保焊膏的印刷質量。一般而言,低速刮刀導致相對高的印刷質量,并且可能形成模糊的焊膏形狀。此外,極低的速度甚至會降低制造效率。相反,高速刮刀可能導致網孔中焊膏填充不足。刮刀壓力太大可能導致錫不足并增加刮刀和模板之間的磨損,而極低的壓力導致焊膏印刷不完整。因此,通常滾動焊膏應盡可能地提高速度。此外,應調整刮刀壓力以獲得高印刷質量。極高的下降速度可能會導致焊膏冰柱或不良形成,而低速會影響制造效率。不合適的模板清潔模式和頻率將導致模板清潔不完整,連續錫電沉積或模板孔中的錫不足往往會導致狹窄空間的產品。
?設備精度
在印刷高密度,小空間的產品時,印刷精度和重復印刷精度會影響焊膏印刷的穩定性。
?PCB支持
PCB支持是焊膏印刷的重要調整內容。如果PCB缺乏有效的支撐或具有不合適的支撐,高厚度的焊膏或不均勻的焊膏。 PCB支撐應平整且均勻,以保證模板和PCB之間的緊密性。
元件安裝
質量元件安裝取決于三個要素:正確選擇元件,精確放置和合適的安裝壓力。正確選擇組件是指組件必須與BOM的要求兼容。精確放置意味著安裝坐標必須正確,安裝器的精度必須確保安裝穩定性和正確的元件安裝在焊盤上。同時,必須注意安裝角度以確保部件的方向正確性。合適的安裝壓力是指按壓部件的厚度,它不應該太小也不能太大。安裝壓力可以通過設置PCB厚度,元件封裝厚度,噴嘴的安裝器壓力和安裝器Z軸的調整來確定。
回流焊接
焊點的焊接質量在于正確設定回流焊溫度曲線。良好的回流焊接曲線要求PCB上的所有安裝組件都必須獲得優異的焊接和焊接點,同時具有出色的外觀和高質量。如果溫度上升過快,一方面,元件和PCB會受到熱量的影響,以至于元件容易損壞,PCB會發生變形。另一方面,焊膏中的溶劑揮發得太快,金屬復合物會像鍍錫球一樣濺出。峰值溫度通常設定為高于焊膏的熔點30℃至40℃。如果溫度過高且回流時間過長,則會損壞耐熱元件或元件塑料。相反,由于焊膏的不完全熔化,將形成可靠的焊點。為了加強焊接質量并阻止元件氧化,可以應用氮氣再焊接。回流曲線通常根據以下方面設定:
a。可根據焊膏推薦的溫度曲線進行設定。焊膏的成分決定了其活化溫度和熔點。
b。根據耐熱元件和有價值元件的熱性能參數,對于某些特殊元件,必須考慮最高的焊接溫度。
c。應根據PCB基板材料,尺寸,厚度和重量進行設置。
d。應根據回流爐結構和溫度區長度進行設置,不同的回流焊爐應采用不同的設置。
有很多元素影響SMT焊接質量,包括元件可焊性,PCB質量,PCB焊盤設計,焊膏質量,PCB制造質量,SMT制造設備情況,SMT各環節技術參數和各工人操作技能。在這些元件中,元件的質量,PCB和焊膏以及PCB設計是回流焊接質量保證的基礎,因為這些元件引導的焊接缺陷很難或不可能通過技術解決方案來解決。因此,提高焊接質量的優勢在于良好的材料質量控制和出色的PCB焊盤設計。此外,焊膏印刷,安裝和回流焊接過程中每個環節的技術參數必須通過實施完善的制造技術程序進行管理和優化。
-
PCB設計
+關注
關注
394文章
4683瀏覽量
85548 -
PCB打樣
+關注
關注
17文章
2968瀏覽量
21696 -
華強PCB
+關注
關注
8文章
1831瀏覽量
27749 -
華強pcb線路板打樣
+關注
關注
5文章
14629瀏覽量
43035
發布評論請先 登錄
相關推薦
CPCI設計與制造:提高可制造性的關鍵要素
PCB可制造性設計審核的內容
關于PCB設計時需考慮哪些可制造性問題
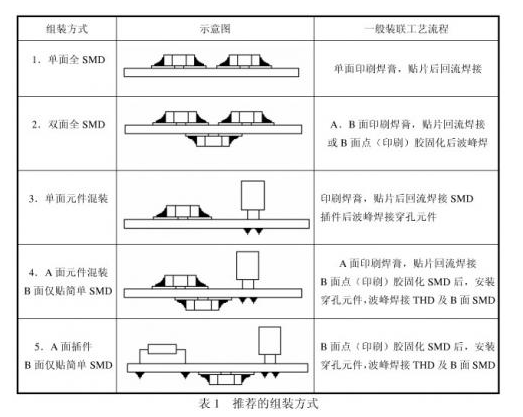
評論