Abstract: This application note explains 4-20mA current loops and intelligent transmitters and explains their need for high-resolution low-power DACs.
An optimum power-supply chip is not the only critical choice to be made in designing a mixed 3V/5V microprocessor-controlled system. Because more and more systems require low-power components capable of low-voltage startup, state-of-the-art A/D and D/A converters with near-ideal specifications, including 3V/5V operation, are also welcome.
Today's popular industrial-control applications, such as programmable-logic controllers, factory process control, computer numeric control (CNC), and intelligent transmitters, all demand low-power semiconductors. Consistent with this trend is the use of 4mA-to-20mA current loops, which have become a well-established part of the analog communications between the host computer and smart transmitters in a factory environment. This article describes intelligent transmitters and explains their need for high-resolution low-power D/A converters.
At the end of the transmission line, a precise termination resistor converts the loop current to an accurate voltage. This resistor (typically 50Ω to 750Ω) establishes the current-loop receiver's input impedance. A high signal-source impedance minimizes voltage fluctuations across the termination resistor caused by variations in line resistance, but it also picks up more EMI and other industrial interference. Large-valued bypass capacitors reduce EMI pickup by helping to lower the signal-source impedance. To summarize, current loops offer four major advantages:
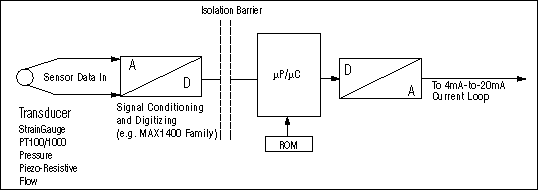
Figure 1. The inclusion of μP/μC intelligence makes this circuit a "smart" 4mA-to-20mA transmitter.
The ADC in a single-channel transmitter often includes compensation circuitry, and the ADC in a multichannel system often includes one or more op amps and multiplexers. Sophisticated ADC/DAC combinations can compensate the sensor for offset, offset temperature coefficient, full-span output, full-span output temperature coefficient, and nonlinearity. A new line of intelligent 0.1%-accurate signal conditioners from Maxim were designed for these applications.
The first products in this four-member family (MAX1450 and MAX1457) are available now. Future members include the MAX1458, a signal conditioner equipped for internal calibration and the temperature compensation of piezoresistive sensors (via electronic trim using an on-board EEPROM). Another future product optimized for the same purpose (MAX1460) is a highly integrated, signal-processor-based, digitally compensated signal conditioner.
If the sensor must reside in an explosive atmosphere, safety measures require not only an isolation barrier that prevents ground loops but operation that is "intrinsically safe" as well; this is a rule that limits the level of transmitter energy below that capable of generating an electrical discharge. The isolation barrier for such a system typically resides on the power-supply side. For smart transmitter systems that are not intrinsically safe, the isolation barrier can be placed between the microcontroller (μC) and the conditioned and digitized sensor data. Data can be transferred across this barrier by general-purpose optocouplers such as the 6N136, the 4N26, or the IL300.
The transducer voltage must be digitized with precision by an A/D converter, preferably one with high resolution and an on-board calibration capability that removes system- and component-drift errors before the signal reaches a controlling processor. The processor then reads the data, processes it, and transmits it through a low-power high-resolution D/A converter to the 4mA-to-20mA current loop.
The next step up is an even smarter circuit called an intelligent transmitter (Figure 2). An intelligent transmitter combines a transducer signal and memory for storing transmitter information with the two-way communication skills of a microcomputer. With an additional A/D converter, the system can produce data on the current loop's condition that enables adjustment and calibration by the μC.
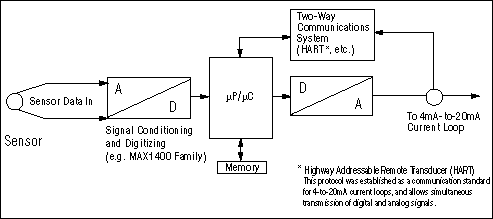
Figure 2. The association of μP/μC intelligence with the sensor produces an "intelligent" 4mA-to-20mA transmitter.
New low-power low-voltage D/A converters from Maxim meet both requirements for a digitally adjustable 4mA-to-20mA current loop: a 3V/5V supply-voltage capability, and internal amplifiers able to control the gate voltage of an external MOSFET. The only drawback in this configuration is the need to drive an external n-channel MOSFET, which requires a much higher supply voltage. If not provided on-board, this voltage must be realized with an external power-boost circuit.
Fortunately, most industrial-control applications provide both high and low voltages for support of 3V/5V programmable-logic control as well as the sensors (piezoelectric, pressure, temperature, and flow) that demand voltages as high as 36V (24V typical). As component suppliers adapt to the industry's need for lower power, the use of common-threshold MOSFETs (controllable by a single +5V power supply) is spreading rapidly.
You can create a reliable, digitally adjustable 4mA-to-20mA current loop by combining an op amp and a MOSFET with one of the D/A converters in Table 1. Most of these D/A converters have Schmitt-trigger inputs, which enable a direct interface to the optocouplers in an isolated system.
Table 1. D/A Converters for 4mA-20mA Current Loops
*In addition to the packages listed, all parts are available in DIPs.
The 13-bit low-power voltage-output D/A converters shown in Figure 3 include precision output amplifiers that can drive an external MOSFET directly. You can also bypass this internal amplifier with an external op amp. SPI?, QSPI?, and Microwire? compatibility simplifies the converters' data interface, making them suitable for use with most of the processors and controllers found in industrial-control applications.
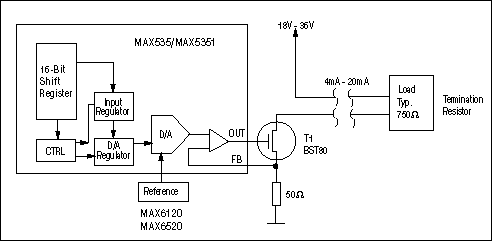
Figure 3. This simple, digitally adjustable 4mA-to-20mA current loop is suitable for transmission over moderate distances.
During long-distance signal transmission, the converters' force and sense pins (OUT and FB) compensate instantly for error voltages at the receiver. These connections to the internal, user-programmable output amplifier also let you configure a simplified current loop (Figure 4).
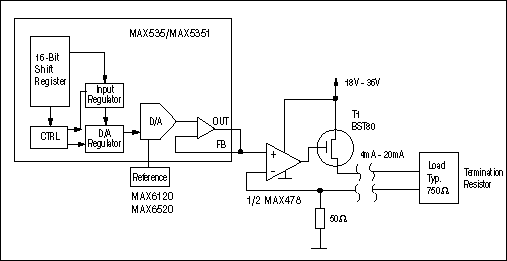
Figure 4. Adding a high-voltage op amp to the Figure 3 circuit provides vigorous gate drive to the MOSFET, enabling longer-distance current-loop transmissions.
An external MOSFET (Table 2) drives the loop with a current determined by the 50Ω resistor:
With outputs of 1.200V typical, the MAX6120/MAX6520 references are well suited for these applications. Accuracy is 100ppm/°C (30ppm typical) for the MAX6120 and 50ppm/°C (25ppm typical) for the higher-precision MAX6520. The small packages in Figures 3 and 4 (μMAX for the MAX535/MAX5351 and SOT23 for the MAX6120/MAX6520) support space-critical applications. Some industrial-control current loops have 60Ω sense resistors that allow maximum loop currents of only 20mA. This is not quite enough, because most loops must be capable of delivering a 10% over-range (i.e., 20mA + 2mA = 22mA in this case). Setting the reference voltage slightly higher (to 1.44V) solves this problem.
Table 2. N-Channel MOSFETS for 4mA-to-20mA Current Loops
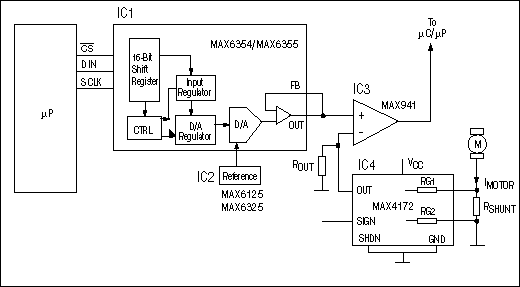
Figure 5. On sensing excessive current in the motor, this digitally controlled current monitor alerts the μP.
IC4 is a high-side current-sense amplifier whose current-source output (OUT) delivers a current equal to 1/1000 of the monitored current flowing through its RG1/RG2 terminals. The OUT current develops a voltage in ROUT proportional to the motor current, and a comparator (IC3) compares this motor-current signal with a threshold voltage set by the DAC. The trip threshold represented by the DAC output can be programmed via the user interface, transmitted from another system, or stored in an external memory. As another alternative, an external A/D converter can make this threshold dependent on other conditions or parameters.
The 10-bit serial-input DAC's variable-gain output stage can be configured for various applications similar to the unipolar case shown in Figure 5. To accommodate bipolar signals, the output stage's accessible inverting input lets you form inverting or noninverting amplifiers with gain.
After processing by the μP, digital data is fed to the DAC via a 3-wire interface either as single 16-bit words or as two 8-bit words (3 control bits and 10+3 data bits). The DAC's double-buffered input stage enables it to load new data without disturbing "old" data residing in the DAC register. The DAC's output-voltage swing is determined by the output gain and the external reference voltage. A gain of two and the 2.5V, 50ppm/°C MAX6125, for example, produces an output swing of 0V to 5V. For better precision and lower noise, choose the MAX6325, which features an output noise of 1.5μVp-p and a temperature coefficient of 1ppm/°C to 2.5ppm/°C.
Thus, the comparator output remains high until motor current exceeds the DAC-output threshold; then it delivers a low-to-high transition to the μP. Most of the motor current is diverted by a shunt resistor, resulting in the following expression for the motor-current signal at the comparator's inverting input:
RSHUNT is the current-sense resistor,
ROUT is the voltage-setting resistor,
IMOTOR is the full-scale sensed motor current, and
RG = RG1 = RG2 is the gain-setting resistor.
Products now in development by Maxim include 13-bit DACs with internal references and 14-bit DACs with greater precision. Also in development are products representing the conditioning and digitizing function between transducer and microcontroller. For example, a new 16-bit oversampling A/D converter (MAX1400, from Maxim's new family of lower-power 16-bit Δ-σ converters) is designed to meet the industry need for digitizing transducer data.
____________________
1The resistance temperature detector (RTD) is a resistive temperature sensor whose variation with temperature is almost linear in a range, including 273°K (0°C). PT100, for example, is a member of an RTD family manufactured with platinum. PT indicates a positive temperature coefficient, and the number indicates the nominal value in ohms at room temperature. The 100Ω RTD value is the most common, but others are available.
An optimum power-supply chip is not the only critical choice to be made in designing a mixed 3V/5V microprocessor-controlled system. Because more and more systems require low-power components capable of low-voltage startup, state-of-the-art A/D and D/A converters with near-ideal specifications, including 3V/5V operation, are also welcome.
Today's popular industrial-control applications, such as programmable-logic controllers, factory process control, computer numeric control (CNC), and intelligent transmitters, all demand low-power semiconductors. Consistent with this trend is the use of 4mA-to-20mA current loops, which have become a well-established part of the analog communications between the host computer and smart transmitters in a factory environment. This article describes intelligent transmitters and explains their need for high-resolution low-power D/A converters.
Basic Requirements for 4mA-20mA Transducers
For transmitting low-amplitude low-frequency signals over several hundred yards in a noisy industrial-control environment, current is preferred over voltage, because the current at any instant is constant over the entire length of the cable. Voltage transmission is not recommended, because the voltage at any point depends on line resistance and capacitance, which change with the cable's length. Current transmission also allows a single 2-wire cable to carry power and signals at the same time.At the end of the transmission line, a precise termination resistor converts the loop current to an accurate voltage. This resistor (typically 50Ω to 750Ω) establishes the current-loop receiver's input impedance. A high signal-source impedance minimizes voltage fluctuations across the termination resistor caused by variations in line resistance, but it also picks up more EMI and other industrial interference. Large-valued bypass capacitors reduce EMI pickup by helping to lower the signal-source impedance. To summarize, current loops offer four major advantages:
- Long-distance transmission without amplitude loss
- Detection of offline sensors, broken transmission lines, and other failures
- Inexpensive 2-wire cables
- Lower EMI sensitivity
Digitally Controlled 4mA-to-20mA Current Loops
Smart transmitters incorporate a processor or a controller that linearizes the sensor data and communicates it to the host system. As shown in Figure 1, these systems employ five general building blocks: an A/D converter, a microcontroller (μC), some RAM, a D/A converter with an optional integrated amplifier, and a sensor or a transducer (thermocouple, strain gauge, PT100 RTD1, etc.).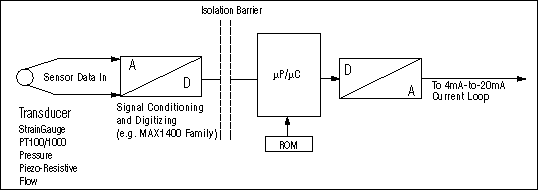
Figure 1. The inclusion of μP/μC intelligence makes this circuit a "smart" 4mA-to-20mA transmitter.
The ADC in a single-channel transmitter often includes compensation circuitry, and the ADC in a multichannel system often includes one or more op amps and multiplexers. Sophisticated ADC/DAC combinations can compensate the sensor for offset, offset temperature coefficient, full-span output, full-span output temperature coefficient, and nonlinearity. A new line of intelligent 0.1%-accurate signal conditioners from Maxim were designed for these applications.
The first products in this four-member family (MAX1450 and MAX1457) are available now. Future members include the MAX1458, a signal conditioner equipped for internal calibration and the temperature compensation of piezoresistive sensors (via electronic trim using an on-board EEPROM). Another future product optimized for the same purpose (MAX1460) is a highly integrated, signal-processor-based, digitally compensated signal conditioner.
If the sensor must reside in an explosive atmosphere, safety measures require not only an isolation barrier that prevents ground loops but operation that is "intrinsically safe" as well; this is a rule that limits the level of transmitter energy below that capable of generating an electrical discharge. The isolation barrier for such a system typically resides on the power-supply side. For smart transmitter systems that are not intrinsically safe, the isolation barrier can be placed between the microcontroller (μC) and the conditioned and digitized sensor data. Data can be transferred across this barrier by general-purpose optocouplers such as the 6N136, the 4N26, or the IL300.
The transducer voltage must be digitized with precision by an A/D converter, preferably one with high resolution and an on-board calibration capability that removes system- and component-drift errors before the signal reaches a controlling processor. The processor then reads the data, processes it, and transmits it through a low-power high-resolution D/A converter to the 4mA-to-20mA current loop.
The next step up is an even smarter circuit called an intelligent transmitter (Figure 2). An intelligent transmitter combines a transducer signal and memory for storing transmitter information with the two-way communication skills of a microcomputer. With an additional A/D converter, the system can produce data on the current loop's condition that enables adjustment and calibration by the μC.
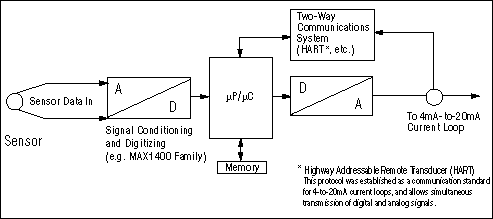
Figure 2. The association of μP/μC intelligence with the sensor produces an "intelligent" 4mA-to-20mA transmitter.
New low-power low-voltage D/A converters from Maxim meet both requirements for a digitally adjustable 4mA-to-20mA current loop: a 3V/5V supply-voltage capability, and internal amplifiers able to control the gate voltage of an external MOSFET. The only drawback in this configuration is the need to drive an external n-channel MOSFET, which requires a much higher supply voltage. If not provided on-board, this voltage must be realized with an external power-boost circuit.
Fortunately, most industrial-control applications provide both high and low voltages for support of 3V/5V programmable-logic control as well as the sensors (piezoelectric, pressure, temperature, and flow) that demand voltages as high as 36V (24V typical). As component suppliers adapt to the industry's need for lower power, the use of common-threshold MOSFETs (controllable by a single +5V power supply) is spreading rapidly.
You can create a reliable, digitally adjustable 4mA-to-20mA current loop by combining an op amp and a MOSFET with one of the D/A converters in Table 1. Most of these D/A converters have Schmitt-trigger inputs, which enable a direct interface to the optocouplers in an isolated system.
Table 1. D/A Converters for 4mA-20mA Current Loops
|
|
|
|
|
|
|
|
|
|
|
MAX5354 |
|
|
|
|
|
|
|
|
|
|
MAX5355 |
|
|
|
|
|
|
|
|
|
|
MAX5251 |
|
|
|
|
|
|
|
|
|
|
MAX5352 |
|
|
|
|
|
|
|
|
|
|
MAX5353 |
|
|
|
|
|
|
|
|
|
|
MAX531 |
|
|
|
|
|
|
|
|
|
|
MAX5156 |
|
|
|
|
|
|
|
|
|
|
MAX5157 |
|
|
|
|
|
|
|
|
|
|
MAX5253 |
|
|
|
|
|
|
|
|
|
|
MAX535 |
|
|
|
|
|
|
|
|
|
|
MAX5351 |
|
|
|
|
|
|
|
|
|
|
MAX5152 |
|
|
|
|
|
|
|
|
|
|
MAX5153 |
|
|
|
|
|
|
|
|
|
|
*In addition to the packages listed, all parts are available in DIPs.
The 13-bit low-power voltage-output D/A converters shown in Figure 3 include precision output amplifiers that can drive an external MOSFET directly. You can also bypass this internal amplifier with an external op amp. SPI?, QSPI?, and Microwire? compatibility simplifies the converters' data interface, making them suitable for use with most of the processors and controllers found in industrial-control applications.
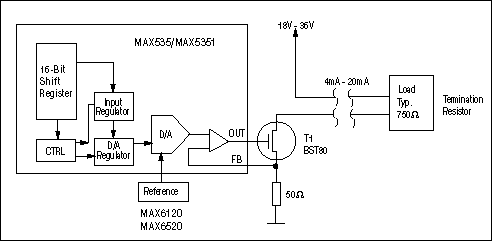
Figure 3. This simple, digitally adjustable 4mA-to-20mA current loop is suitable for transmission over moderate distances.
During long-distance signal transmission, the converters' force and sense pins (OUT and FB) compensate instantly for error voltages at the receiver. These connections to the internal, user-programmable output amplifier also let you configure a simplified current loop (Figure 4).
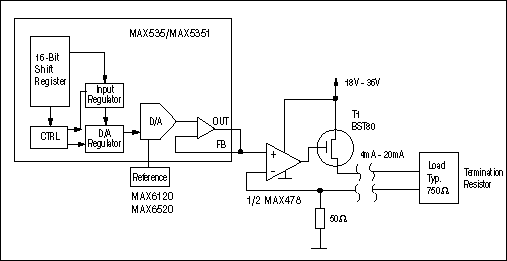
Figure 4. Adding a high-voltage op amp to the Figure 3 circuit provides vigorous gate drive to the MOSFET, enabling longer-distance current-loop transmissions.
An external MOSFET (Table 2) drives the loop with a current determined by the 50Ω resistor:
IOUT = (VREF/RSENSE)(DIN/2N)The DAC's resolution is N and the decimal equivalent of its input code is DIN, which represents the sensor's digitized output after processing by the microcomputer. Resolution for the serial, 3V/5V MAX535/MAX5351 converters is 13 bits, yielding a full-scale range of 2N = 213 = 8192. For a 1.2V reference, 50Ω current-sense resistor, and full-scale DAC output of DIN = 8192, the output current is IOUT = VREF/RSENSE = 1.2V/50Ω = 24mA.
With outputs of 1.200V typical, the MAX6120/MAX6520 references are well suited for these applications. Accuracy is 100ppm/°C (30ppm typical) for the MAX6120 and 50ppm/°C (25ppm typical) for the higher-precision MAX6520. The small packages in Figures 3 and 4 (μMAX for the MAX535/MAX5351 and SOT23 for the MAX6120/MAX6520) support space-critical applications. Some industrial-control current loops have 60Ω sense resistors that allow maximum loop currents of only 20mA. This is not quite enough, because most loops must be capable of delivering a 10% over-range (i.e., 20mA + 2mA = 22mA in this case). Setting the reference voltage slightly higher (to 1.44V) solves this problem.
Table 2. N-Channel MOSFETS for 4mA-to-20mA Current Loops
|
|
|
|
|
ND2410L/B |
|
|
|
|
ND2020L/E |
|
|
|
|
BF245B |
|
|
|
|
BS107 |
|
|
|
|
Monitoring Peak Currents through a Motor Block
Another application common to industrial environments is the digital control of synchronous/asynchronous motors and servomotors. The circuit in Figure 5 detects excessive current in the motor block (i.e., motor current in excess of an adjustable threshold), and either displays the value or feeds it back for use by a controller or an embedded processor in regulating the current loop. For maximum flexibility, the system should let you set this threshold at any time and to any level within the allowed range.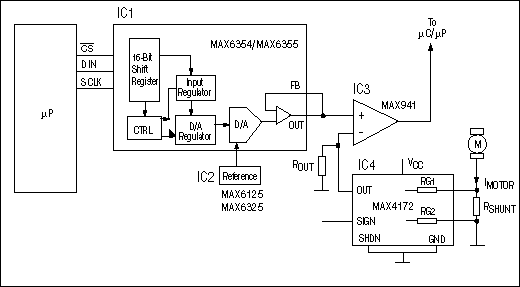
Figure 5. On sensing excessive current in the motor, this digitally controlled current monitor alerts the μP.
IC4 is a high-side current-sense amplifier whose current-source output (OUT) delivers a current equal to 1/1000 of the monitored current flowing through its RG1/RG2 terminals. The OUT current develops a voltage in ROUT proportional to the motor current, and a comparator (IC3) compares this motor-current signal with a threshold voltage set by the DAC. The trip threshold represented by the DAC output can be programmed via the user interface, transmitted from another system, or stored in an external memory. As another alternative, an external A/D converter can make this threshold dependent on other conditions or parameters.
The 10-bit serial-input DAC's variable-gain output stage can be configured for various applications similar to the unipolar case shown in Figure 5. To accommodate bipolar signals, the output stage's accessible inverting input lets you form inverting or noninverting amplifiers with gain.
After processing by the μP, digital data is fed to the DAC via a 3-wire interface either as single 16-bit words or as two 8-bit words (3 control bits and 10+3 data bits). The DAC's double-buffered input stage enables it to load new data without disturbing "old" data residing in the DAC register. The DAC's output-voltage swing is determined by the output gain and the external reference voltage. A gain of two and the 2.5V, 50ppm/°C MAX6125, for example, produces an output swing of 0V to 5V. For better precision and lower noise, choose the MAX6325, which features an output noise of 1.5μVp-p and a temperature coefficient of 1ppm/°C to 2.5ppm/°C.
Thus, the comparator output remains high until motor current exceeds the DAC-output threshold; then it delivers a low-to-high transition to the μP. Most of the motor current is diverted by a shunt resistor, resulting in the following expression for the motor-current signal at the comparator's inverting input:
VOUT = (RSHUNT*ROUT*IMOTOR)/RG, whereVOUT is the MAX4172 output voltage,
RSHUNT is the current-sense resistor,
ROUT is the voltage-setting resistor,
IMOTOR is the full-scale sensed motor current, and
RG = RG1 = RG2 is the gain-setting resistor.
Products now in development by Maxim include 13-bit DACs with internal references and 14-bit DACs with greater precision. Also in development are products representing the conditioning and digitizing function between transducer and microcontroller. For example, a new 16-bit oversampling A/D converter (MAX1400, from Maxim's new family of lower-power 16-bit Δ-σ converters) is designed to meet the industry need for digitizing transducer data.
____________________
1The resistance temperature detector (RTD) is a resistive temperature sensor whose variation with temperature is almost linear in a range, including 273°K (0°C). PT100, for example, is a member of an RTD family manufactured with platinum. PT indicates a positive temperature coefficient, and the number indicates the nominal value in ohms at room temperature. The 100Ω RTD value is the most common, but others are available.
MICROWIRE is a trademark of National Semiconductor Corp.
QSPI is a trademark of Motorola, Inc.
SPI is a trademark of Motorola, Inc.
評論