Add Thermal Monitoring to Reduce Data Center Energy Consumption
Abstract: Precise and adaptable thermal management is imperative for efficiently managing the energy consumption of data centers and other temperature-sensitive environments. This article details how 1-Wire? technology enables double-digit reductions in the power consumption of climate-controlled environments.
Today's Challenge: Reduce Power Consumption in Data Centers
The EPA estimates that data centers accounted for 1.5% (61 billion kWh) of total U.S. electricity consumption in 2006.1 Astonishingly, IT equipment was responsible for only half of this electricity consumption; power and cooling infrastructure accounted for the other half. Yet to date, most efforts to reduce the power consumption of data centers have addressed only the first half of the problem: the energy efficiency of the chips and components in IT equipment.To effectively minimize overall data center energy consumption, it is imperative that the energy consumed by the cooling infrastructure be reduced as well. By implementing an intelligent cooling infrastructure, organizations will be able to accommodate higher power densities without building additional data centers. Additionally, they will reduce their electricity bill while minimizing their carbon footprint.
Conventional Cooling Infrastructures Waste Substantial Energy
The ambient temperature in a data center or other thermally controlled environment is not constant throughout the space. Temperature varies significantly across both the vertical and horizontal planes depending on proximity to active or inactive equipment, as well as airflow. Moreover, the cooling zones of computer room air conditioners (CRACs) frequently overlap, resulting in cooling redundancy. Simply stated, data centers waste substantial power by cooling areas that are already cool, because they lack intelligent thermal-monitoring capabilities.The ability to identify specific areas where ambient temperature needs to be reduced is the key to reducing data center power consumption. However desirable this goal, it has not been simple to implement. The complexity of wiring and interfacing multiple temperature sensors is compounded by the difficulty of managing a vast array of temperature-measurement nodes. Consequently, multipoint temperature monitoring is particularly problematic.
Efficient Multipoint Temperature Measurement
Multiple temperature-measurement nodes, combined with appropriate temperature data processing, enable an optimized environmental temperature-control system that saves power and reduces cost. To implement such a system without adding any complex wiring overhead, designers can draw on various technologies—for example, a network of wireless sensors based on Zigbee? or other wireless standards, or a hardwired approach using a simple serial interface such as Maxim's 1-Wire technology. A 1-Wire system can route all sensor readings over a single wire, possibly an unused wire pair in a CAT5 network cable that is already part of the server farm infrastructure.Wireless solutions would be easy to install, since few new wires would be needed (just a tap into the local power supply to power the module). However, today's per-module cost for each sensor could be $10 (U.S.) or more, thus adding thousands to tens of thousands of dollars to the data center overhead. Alternately, a hardwired system using a simple 1-Wire serial interface can run off parasitically derived power (less than 1mA per node) and keep costs per node to just a couple of dollars.
The 1-Wire interface can thus solve the wiring complexity challenge of large, multipoint temperature-sensing arrays (Figure 1).2 Using 1-Wire technology, sensors are multidropped throughout an enclosure or space from a single, low-cost twisted pair like that available in CAT5 cables. Temperature data from individual sensors, or a group of sensors, is communicated digitally to a host processor through the 1-Wire protocol.
Figure 1. Energy management in a server farm can be improved by adding a network of 1-Wire digital temperature sensors, such as the DS28EA00, to monitor multiple locations for more efficient, controlled cooling.
Location-Aware Temperature Sensors
Monitoring many temperatures in a data center is challenging. How will the measurement of a given sensor be associated with its physical location? Any solution that requires manual configuration is time-consuming, expensive, and prone to error. Chain-mode operation, a new feature offered on some 1-Wire temperature sensors, solves this problem (Figure 2).All 1-Wire temperature sensors are factory programmed with a unique and unalterable 64-bit ID value that can be electronically read from the 1-Wire master device. Unique among Maxim's 1-Wire-based thermal sensors, the DS28EA00 has two additional pins to implement a sequence-detect function (i.e., chain mode). Using the DS28EA00's chain mode function, the 1-Wire master reads and associates the sensors' registration numbers according to each device's physical location in a multidrop-configured connection. If the sequence-detect function is not needed, these two pins can be used as general-purpose inputs or outputs.
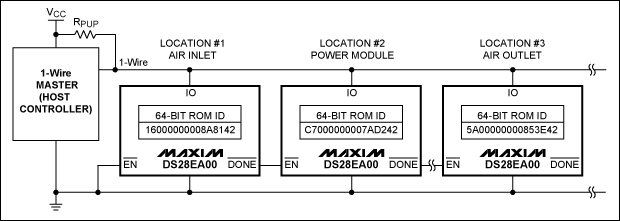
Figure 2. The DS28EA00 employs the chain-mode function in a typical 1-Wire network.
The chain-mode function, therefore, gives the host controller a computer-controlled and fully automated method to determine the sequential ordering of the unique ID for each device in a multidrop temperature-sensor configuration. This sequential ID information directly correlates to the physical construction of the multidrop temperature array and, therefore, the physical location of each sensor in the enclosure.3 This correlation between the DS28EA00's 64-bit ID and physical location in the enclosure enables the application to use its environmental control algorithm to measure temperature in a storage tower at different heights and/or location.
Using Parasitic Power
Powering an array of temperature sensors can add complexity and cost to a distributed temperature-sensing application. Fortunately, 1-Wire temperature sensors can operate from parasitic power supplied by the single data line. This parasitic mode of operation is, in fact, a fundamental feature of 1-Wire products.At the IC level, individual 1-Wire devices, or sensors, have internal circuits to capture and store electronic charge from the 1-Wire data waveforms. Whenever the 1-Wire line is in a logic 0 state (i.e., transmitting a data value of 0), sensors derive their operating power from this captured charge. Note that the actual temperature-measurement and digitization process requires more power than can be stored by this internal parasitic power circuit. Thus, when operating in a parasitic power mode, the 1-Wire line must remain at the logic 1 state during a temperature-conversion cycle. There is an alternative to parasitic-power mode that would remove this restriction: provide an external power source by tapping into a power supply near where the sensor is positioned. (The DS28EA00, for example, has a VCC pin that can optionally be used to supply power to the IC.)
Accurate and Dependable Measurements
A fundamental requirement for an accurate environmental temperature-control system is precise temperature measurement. For environments like a data center, temperature-measurement accuracy typically needs to be ±1°C or better. Exceeding this basic performance requirement, 1-Wire temperature sensors like the DS28EA00 provide ±0.5°C measurement accuracy.The DS28EA00 also includes thermostatic-type functions with user-programmable temperature-measurement alarms which can be polled electronically. Additionally, the device's general-purpose I/O pins can be used to turn on and off visual or audible indicators, such as LEDs or buzzers, for notification of out-of-range temperature conditions (Figure 3).
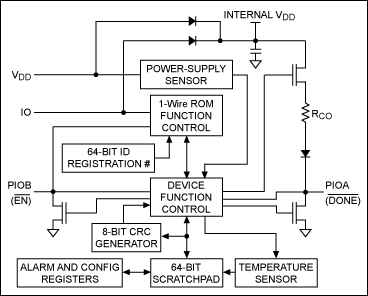
Figure 3. Able to run from either parasitically derived power or from an external supply, the DS28EA00 combines a temperature sensor, Chain-Mode detection, GPIO, alarm capabilities, and the 1-Wire interface in an 8-pin micro-small-outline package (μSOP).
In a typical server farm, each rack of multiple servers might incorporate several temperature sensors. These sensors, along with sensors from other racks in the farm, would send their temperature readings back to the host system that monitors the server farm. That host system would then control overall system cooling. Meanwhile, using its internal alarm capabilities, each 1-Wire sensor could locally control indicators, alarms, and/or temperature subsystems to enable localized cooling.
Multipoint Temperature Monitoring Reduces Cooling Energy by 30%
One such system implementation by a leading manufacturer of large-scale server systems leverages the DS28EA00. In an initial implementation, the company reported a 30% reduction in cooling energy in their data center. They are now saving over two million kWh/year, which equates to a reduction of over 1300 tons/year of CO2 in the atmosphere.Summary
Cooling infrastructure accounts for half of the electricity used by data centers. Consequently, intelligent thermal monitoring is critical for effectively minimizing data center power consumption.1-Wire temperature sensors like the DS28EA00 provide a cost-effective solution for implementing the advanced thermal monitoring needed in twenty-first century applications such as energy-efficient data centers. Data shows that more efficient monitoring of many temperature sensors provides better management of the entire system and significantly reduces overall power consumption.
評論